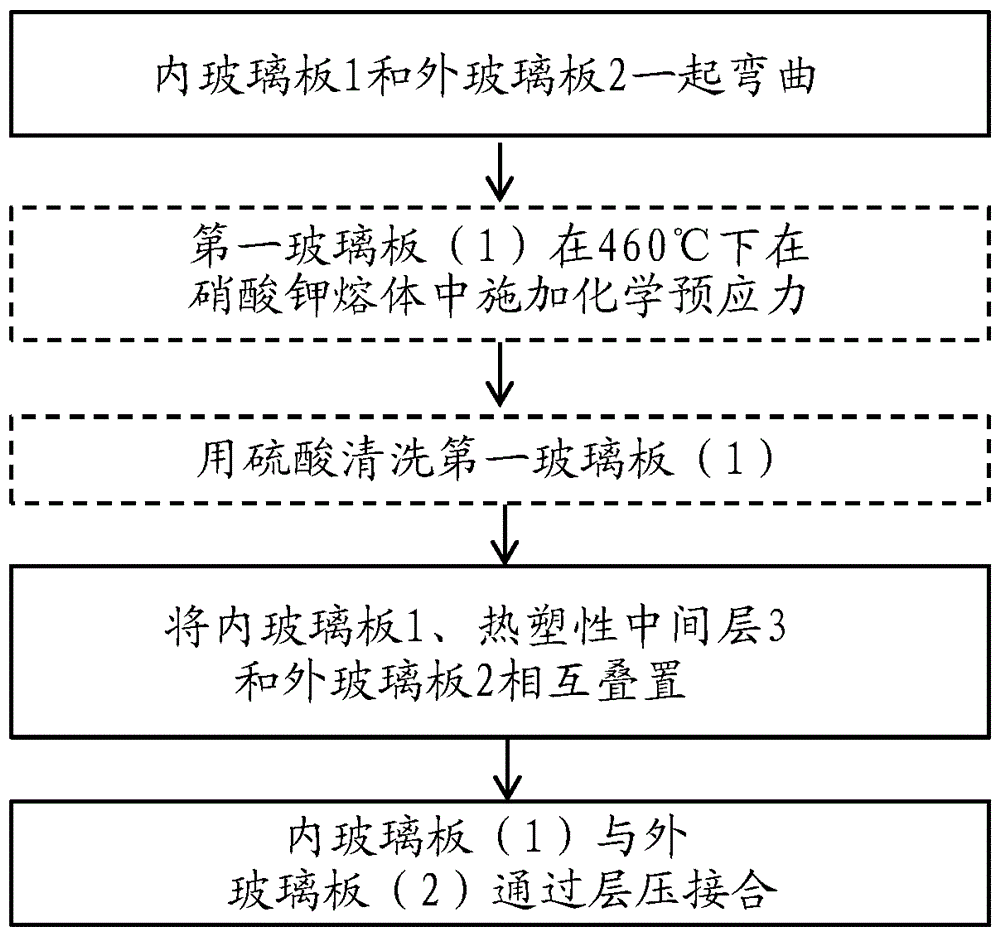
复合玻璃是熟知的作为在汽车领域中的窗玻璃。它们通常由两块具有2毫米至3毫米的厚度的玻璃用玻璃板制成,该玻璃板借助于热塑性中间层彼此接合。这种复合玻璃特别地用作为挡风玻璃和顶玻璃,但是也越来越多地作为侧玻璃和后玻璃。汽车工业目前试图减少机动车的重量,这与减少的燃料消耗有关。窗玻璃的重量的降低,其可以特别地通过减小的玻璃板厚度而获得,可以为此做出显著的贡献。这种薄的玻璃板特别地具有低于2毫米的厚度。尽管该减小的玻璃板厚度,然而必须满足对于该玻璃板的稳定性和抗破裂性的要求。目前接受的观点是,为了确保足够的稳定性和抗破裂性,该复合玻璃的两个玻璃板必须不低于一定的最小厚度。例如US2013/0295357A1公开了用于机动车的具有薄内玻璃板的复合玻璃。该复合玻璃由具有1.5毫米至3.0毫米,例如1.6毫米的厚度的外玻璃板,和具有0.5毫米至1.5毫米,例如0.7毫米的厚度的施加化学预应力(chemischvorgespannt)的内玻璃板组成。明显地认为具有更薄的内玻璃板的复合玻璃不足够稳定的以符合在汽车领域中的安全要求。本发明的目的是提供具有进一步减小厚度并因此进一步减轻重量的复合玻璃,其然而具有足够的稳定性和抗破裂性以能用于汽车领域中。本发明的目的根据本发明通过根据权利要求1的复合玻璃得到完成。优选的实施方案由从属权利要求进行显示。根据本发明的复合玻璃优选是用于机动车的复合玻璃(机动车复合玻璃)。该复合玻璃在开口中,特别地机动车的窗口中,用于使内室与外部环境分隔开。根据本发明的复合玻璃(或者复合玻璃板)至少包括内玻璃板、外玻璃板和热塑性中间层,该热塑性中间层使内玻璃板与外玻璃板接合。内玻璃板和外玻璃板优选由玻璃制成。在本发明的范围中,“内玻璃板"指该复合玻璃板面对内室(机动车内室)的玻璃板。“外玻璃板"指面对外部环境的玻璃板。外玻璃板优选具有1.0毫米至1.8毫米的厚度。该内玻璃板优选具有0.1毫米至0.4毫米的厚度。在本发明的范围中,“内玻璃板"指该复合玻璃板面对内室(机动车内室)的玻璃板。“外玻璃板”指面对外部环境的玻璃板。已经发现具有根据本发明的外玻璃板和内玻璃板的厚度的复合玻璃令人惊讶地具有高的稳定性和抗破裂性,特别是抗划痕性和抗石头冲击性。该内玻璃板因此可以具有比目前通常设想的显著地更低的厚度。复合玻璃的稳定性和抗破裂性产生自该外玻璃板的厚度的根据本发明的选择和外和内玻璃板关于厚度的显著不对称性。令人惊讶地,根据本发明的复合玻璃满足在汽车领域中的高安全要求。这些要求典型地通过标准化破裂、冲击和划痕试验(如根据ECER43的落球试验)进行验证。该内玻璃板的厚度优选为该外玻璃板的厚度的最多25%,特别优选最多20%。这种显著的不对称对于该玻璃板的强度是特别有利的。根据本发明的复合玻璃特别优选是机动车辆的挡风玻璃。在一个优选实施方案中,该内玻璃板是预弯曲玻璃板,即,在层压以形成复合玻璃之前已经受热弯曲工艺的玻璃板。诚然,该内玻璃板原则上也可以是非预弯曲玻璃板,其由于它的低厚度而在层压的时候适应于外玻璃板的形状。然而,有利的是,特别地在所谓的在多个空间方向中的“三维弯曲”的情况下,使用预弯曲内玻璃板,这是因为期望的形状这时可以在低的光学畸变时而得到。因为该弯曲工艺在该玻璃结构中留下特征标记,本领域的技术人员可以通过肉眼检查区别预弯曲和非预弯曲的玻璃板。根据本发明,该较厚的外玻璃板是预弯曲的。该外玻璃板和内玻璃板优选进行全等预弯曲,换言之它们具有相同的预弯曲。该内玻璃板可以例如具有0.1毫米、0.2毫米、0.3毫米或者0.4毫米的厚度。该外玻璃板可以例如具有1.0毫米、1.1毫米、1.2毫米、1.3毫米、1.4毫米、1.5毫米、1.6毫米、1.7毫米或者1.8毫米的厚度。在一个特别有利的实施方案中,内玻璃板具有0.2毫米至0.4毫米,优选0.2毫米至0.3毫米,特别优选大约0.3毫米的厚度。因此,关于该具有高稳定性和抗破裂性的复合玻璃的较低重量方面,获得特别好的结果。在一个特别有利的实施方案中,该外玻璃板具有1.4毫米至1.8毫米,优选1.5毫米至1.7毫米,特别优选约1.6毫米的厚度。这是特别有利的,一方面,关于该复合玻璃的低重量,另一方面具有足够大的厚度以确保在外玻璃板和内玻璃板之间的足够的厚度不对称,其进而产生高稳定性。在本发明的一个有利的实施方案中,该外玻璃板是未施加预应力的玻璃板。该外玻璃板可以暴露于应力如石头冲击。如果石头,特别地小的锐石,撞击玻璃用玻璃板,它可以刺入它的表面。在施加预应力的玻璃板的情况下,该石头因此可以刺入在该玻璃板内部中的拉伸应力区域,这引起玻璃板的震裂。未施加预应力的外玻璃板在内部中具有宽的压缩应力区域和更低的拉伸应力并且因此是对锐利物体的冲击较少敏感的。因此,未施加预应力的外玻璃板总体上在机动车乘客的安全方面是非常有利的。在本发明的一个优选实施方案中,该外玻璃板包含钠钙玻璃或者硼硅酸盐玻璃,特别地钠钙玻璃。钠钙玻璃可经济地得到并且已经被证实它对于在汽车领域中的应用的价值。在本发明的一个有利的实施方案中,该内玻璃板是施加化学预应力的玻璃板。借助于预应力,该内玻璃板可以被提供有特殊的破裂稳定性和抗划痕性。对于非常薄的玻璃用玻璃板,如根据本发明旨在作为内玻璃板,施加化学预应力是比施加热预应力更好地适合的。由于施加热预应力基于在表面区域和中心区之间的温差,施加热预应力要求该玻璃用玻璃板的最小厚度的前提。适当的应力可以典型地使用可商业获得的施加热预应力的系统在最低约2.5毫米的玻璃厚度得到。使用更低的玻璃厚度,通常不能获得对于预应力通常要求的值(参看例如ECE规则43)。在施加化学预应力期间,在该表面区域中该玻璃的化学组成通过离子交换进行改变,其中通过扩散使离子交换限制在表面区域。施加化学预应力因此尤其适用于薄的玻璃板。施加化学预应力还通常被称为化学淬火、化学硬化或者化学加强。第一玻璃板的稳定性可以通过应力的适当值和局部分布而得到改善,该应力通过在施加化学预应力期间掺入离子而产生。施加化学预应力的内玻璃板优选具有高于100MPa,优选高于250MPa,特别优选高于350MPa的表面压缩应力。该玻璃板的压缩应力深度特别为它的厚度的至少十分之一,优选它的厚度的至少六分之一,例如约该内玻璃板的厚度的五分之一。这在一方面关于该玻璃板的抗破裂性和另一方面关于较少时间的(zeitintensiv)施加预应力工艺是有利的。在本发明的范围中,术语“压缩应力深度”表示从该玻璃板的表面开始测量的深度,直至该深度处玻璃板处于高于0MPa的量的压缩应力。如果该内玻璃板具有例如0.3毫米的厚度,该内玻璃板的压缩应力深度优选高于30微米,特别优选高于50微米,最特别优选100微米至150微米。该内玻璃板原则上可以具有本领域的技术人员已知的任何化学组成。该内玻璃板可以例如包含钠钙玻璃或者硼硅酸盐玻璃或者用这些玻璃制成。优选地,该内玻璃板应该适合于施加化学预应力,特别地,为此目的,具有适当的碱金属元素,优选钠的含量。该内玻璃板可以例如包含40重量%-90重量%的氧化硅(SiO2)、0.5重量%-10重量%的氧化铝(Al2O3)、1重量%-20重量%的氧化钠(Na2O)、0.1重量%-15重量%的氧化钾(K2O)、0重量%-10重量%的氧化镁(MgO)、0重量%-10重量%的氧化钙(CaO)和0重量%-15重量%的氧化硼(B2O3)。该内玻璃板此外可以包含其它组分和杂质。然而已经令人惊讶地发现,该内玻璃板的某些化学组成特别地适合于经受化学预应力。这表现在该扩散过程的高速度,其引起该施加预应力工艺的有利地低的时间花费,和产生大的预应力深度(压缩应力深度),这产生稳定的并且抗裂的玻璃。在本发明的范围中这些组成是优选的。在一个优选实施方案中,该内玻璃板包含铝硅酸盐玻璃。该内玻璃板优选包含50重量%-85重量%的氧化硅(SiO2),3重量%-10重量%的氧化铝(Al2O3),8重量%-18重量%的氧化钠(Na2O),5重量%-15重量%的氧化钾(K2O),4重量%-14重量%的氧化镁(MgO),0重量%-10重量%的氧化钙(CaO)和0重量%-15重量%的氧化硼(B2O3)。该内玻璃板此外可以包含其它组分和杂质。内玻璃板特别优选包含至少55重量%-72重量%(最特别优选57重量%-65重量%)氧化硅(SiO2),5重量%-10重量%(最特别优选7重量%-9重量%)氧化铝(Al2O3),10重量%-15重量%(最特别优选12重量%-14重量%)氧化钠(Na2O),7重量%-12重量%(最特别优选8.5重量%-10.5重量%)氧化钾(K2O)和6重量%-11重量%(最特别优选7.5重量%-9.5重量%)氧化镁(MgO)。除施加化学预应力能力之外,这些优选的玻璃组合物具有另一种令人惊奇的优点。这种玻璃板适于与传统的钠钙玻璃的玻璃板(也称为“标准玻璃”)一起全等地弯曲。相似的热性质是其原因,使得两种类型玻璃在相同的温度范围(即约450℃至700℃)中是可弯曲的。如本领域的技术人员充分已知的是,全等弯曲玻璃板,由于它们的最佳匹配的形状,是特别地适合于接合以形成复合玻璃。具有优选的化学组成的玻璃板因此是特别适合用于具有外玻璃板(具有不同的组成,其特别地由钠钙玻璃制成)的复合玻璃中。然而,该内玻璃板或者可以也是未施加预应力的玻璃板。特别地,使用非常薄的玻璃用玻璃板,通过施加化学预应力可以获得的应力值并因此该稳定效果越来越降低。如果该内玻璃板不是施加预应力的,在一个优选实施方案中,它包含硼硅酸盐玻璃。已经发现由此可以获得这种特别显著的稳定性和抗破裂性。热塑性中间层包含至少一个热塑性薄膜并且在有利的实施方案中由单个热塑性薄膜形成。这在该复合玻璃的简单结构和低总厚度方面是有利的。该热塑性中间层或者该热塑性薄膜优选至少包含聚乙烯醇缩丁醛(PVB)、乙烯乙酸乙烯酯(EVA)、聚氨酯(PU)或者它们的混合物或者共聚物或者衍生物,这已经证实它们对于复合玻璃的价值。该热塑性中间层的厚度优选是0.2毫米至1.0毫米。例如,可以使用具有0.76毫米的标准厚度的热塑性薄膜。在一个特别优选的实施方案中,该复合玻璃不具有其它玻璃板或者聚合物层,因此由仅仅该外玻璃板、该内玻璃板和该热塑性中间层组成。该外玻璃板、该内玻璃板和该热塑性中间层可以是透亮的和无色的,但是还可以是着色的或者有色的。在一个优选实施方案中,穿过该复合玻璃的总透射率为高于70%,特别地当该复合玻璃是挡风玻璃时。该术语“总透射率”指由ECE-R43,Annex3,§9.1建立的测试汽车窗户的光透过率的方法。该复合玻璃优选作为对于汽车玻璃的惯例在一个或者在多个空间方向中进行弯曲,其中具有在约10厘米至约40m范围中的典型曲率半径。该复合玻璃然而可以也是平面的,例如,当它被提供作为用于公共汽车、火车或者拖拉机的玻璃板时。根据本发明的复合玻璃可以具有功能性涂层,例如,IR反射或者吸收涂层,UV反射或者吸收涂层,着色涂层,低辐射性涂层,可加热涂层,具有天线功能的涂层,粘附碎片的(splitterbindend)涂层,或者用于屏蔽电磁辐射的涂层。功能性涂层优选被布置在外玻璃板上。较厚的外玻璃板,其此外优选由普通玻璃制成,可以以技术上比非常薄的内玻璃板更简单的方式和更经济地进行涂覆,例如通过物理气相沉积(如溅射)。特别地,涂覆和施加化学预应力可以进行结合,但从技术观点看具有很大难度。在施加预应力之前施用的涂层妨碍在施加化学预应力期间的离子扩散工艺。由于该典型地高温,在施加化学预应力之后涂覆改变了在该玻璃板中的应力分布。该功能性涂层优选被布置在外玻璃板的面对该热塑性中间层的表面上,在那里它被保护不受腐蚀和损害。该复合玻璃还可以被提供有附加功能,这一点上,除该功能性涂层之外或者代替该功能性涂层,该中间层具有功能性夹杂物(Einlagerung),例如,具有IR吸收、UV吸收、着色或者声学的性质的夹杂物。该夹杂物是例如有机或者无机离子、化合物、附聚体、分子、晶体、颜料或者染料。本发明进一步地通过用于制备根据本发明的复合玻璃的方法而完成,其中:(a)将所述内玻璃板、所述热塑性中间层和所述外玻璃板以该顺序以平面方式相互叠置,和(b)将所述内玻璃板和所述外玻璃板通过层压彼此接合。如果该复合玻璃要进行弯曲,对至少该外玻璃板在层压之前经受弯曲工艺。在本发明的一个实施方案中,对该内玻璃板不进行预弯曲。由于它的非常低的厚度,该内玻璃板具有膜一样的柔韧性并因此适合于该预弯曲外玻璃板而不必须本身进行预弯曲。该复合玻璃的制备因此得到简化。在一个替换的实施方案中,该内玻璃板也经受弯曲工艺。这是有利的特别地在多个空间方向中具有急弯曲(所谓的“三维弯曲”)。该外玻璃板和该内玻璃板可以分别地进行弯曲。优选地,该外玻璃板和该内玻璃板是联合地全等弯曲(即,同时地并且通过相同的工具),因为由此该玻璃板的形状在该随后的层压时最佳地彼此相配。用于玻璃弯曲工艺的典型温度例如是500℃至700℃。在一个优选实施方案中,该内玻璃板被提供有施加化学预应力。任选地,在弯曲之后,该内玻璃板进行缓慢地冷却。过于快速冷却在该玻璃板中产生热应力,其可以在随后的化学淬火期间引起形变。该冷却速率优选为0.05℃/秒至0.5℃/秒直至冷却至温度400℃,特别优选0.1-0.3℃/秒。借助于这种缓慢冷却,可以防止在该玻璃中的热应力,其特别地引起光学缺陷以及对随后的施加化学预应力的负面影响。此后,它可以进一步地进行冷却甚至以较高的冷却速率,因为低于400℃,产生热应力的风险是低的。该施加化学预应力优选在300℃至600℃,特别优选400℃至500℃的温度下进行。该内玻璃板用盐熔体进行处理,例如,浸于该盐熔体中。在该处理期间,特别地,该玻璃的钠离子被更大的离子,特别地更大的碱金属离子交换,产生期望的表面压缩应力。该盐熔体优选是钾盐,特别优选硝酸钾(KNO3)或者硫酸钾(KSO4),最特别优选硝酸钾(KNO3)的熔体。该离子交换通过该碱金属离子的扩散进行测定。该表面压缩应力的期望值和压缩应力深度因此可以进行调节,特别地通过该施加预应力工艺的温度和持续时间进行。用于该持续时间的通常时间为2小时至48小时。在使用盐熔体处理之后,使该玻璃板冷却至室温。然后,对该玻璃板进行清洁,优选使用硫酸(H2SO4)进行清洁。该热塑性中间层优选作为薄膜进行提供。通过层压制备复合玻璃使用本身由本领域的技术人员已知的传统方法例如高压釜方法、真空袋方法、真空环法、压延方法、真空层压机、或者其组合来进行。外玻璃板和内玻璃板的接合通常在热量、真空和/或压力的作用下进行。本发明进一步地包括根据本发明的复合玻璃在机动车,优选机动车辆,特别优选载人车辆中的用途,特别是作为挡风玻璃、侧玻璃、后玻璃或者顶玻璃。在下文中,本发明参考附图和示例性实施方案进行详细说明。附图是示意表示并不是真实比例。该附图决不限制本发明的范围。附图描绘了:图1根据本发明的复合玻璃的一个实施方案的剖面图,和图2根据本发明的方法的一个实施方案的流程图。图1描绘了根据本发明的复合玻璃,其用内玻璃板1和外玻璃板2制成,它们经由热塑性中间层3彼此接合。中间层3由单个薄膜形成,该薄膜由PVB制成,具有0.76毫米的厚度。该复合玻璃设计作为机动车辆的挡风玻璃。该复合玻璃按照用于机动车辆挡风玻璃的惯例是在三个维度上进行弯曲。这表示该玻璃板在多个空间方向中,特别地在水平和垂直方向中具有曲率。然而,为了简化起见,该复合玻璃在该附图中示意地被描绘为平面的。用于根据本发明的复合玻璃(实施例)的内玻璃板1和外玻璃板2的厚度、玻璃材料和预应力概括在表1中。根据本发明的复合玻璃的稳定性通过标准测试进行评估,结果与具有传统厚度的复合玻璃(对比例,参看表1)进行比较。表1实施例对比例内玻璃板1厚度0.3毫米1.6毫米材料铝硅酸盐玻璃(60.7重量%SiO2;7.7重量%Al2O3,13.1重量%Na2O,9.6重量%K2O,8.4重量%MgO)钠钙玻璃预应力施加化学预应力未施加预应力外玻璃板2厚度1.6毫米2.1毫米材料钠钙玻璃钠钙玻璃施加预应力未施加预应力未施加预应力抗石头(锐石)冲击的稳定性具有菱形截面尖的抛射体从不断提高的高度落在根据本发明的复合玻璃(实施例)上,以模拟锐石的冲击。测量该复合玻璃破裂时的高度。在从1400毫米的高度在外玻璃板2上的冲击,观察到玻璃破裂。根据本发明的具有非常低的玻璃厚度的复合玻璃令人惊讶地具有比传统的对比例(从1100毫米的高度的冲击引起玻璃破裂)更高的耐石头冲击性。根据ECER43的落球测试该测试在30cm×30cm试样上进行实施。在第一测试中,具有227g重量的钢球从8.5m的高度落在外玻璃板2上。这种测试模拟石头从外部在复合玻璃上的冲击。当该球被该复合玻璃阻止并且不贯穿它时并且当在背离该冲击的一侧上释放的碎片的量低于特定的量(依赖厚度)时,该测试被认为通过。使用适用于挡风玻璃的玻璃组合的对比例正如所料地通过该测试。然而,具有低的玻璃厚度的根据实施例的本发明复合玻璃也令人惊讶地通常该测试。甚至在该球的冲击后,由内玻璃板1释放出更少的碎片,这必须被评价为对于机动车乘客的安全性是有利的。在第二测试中,具有2260g重量的钢球从4m的高度落在内玻璃板1上。这种测试模拟机动车乘客的头部在复合玻璃上的冲击。当该球被该复合玻璃阻止并且在该破裂后的5s内不贯穿它时,该测试被认为通过。该具有高玻璃厚度的对比例正如所料地通过该测试。然而,具有低的玻璃厚度的根据实施例的本发明复合玻璃也通常该测试。根据本发明的复合玻璃由于非常低的玻璃厚度而具有非常低的重量。然而,如该测试证明,该复合玻璃的特征为高抗破裂性和抗石头冲击性。该复合玻璃特别地满足对于在汽车领域中的复合玻璃的高安全要求,使得例如它可以用作为挡风玻璃。它特别地可以使用极其薄的内玻璃板用于机动车玻璃。这种结果是本领域的技术人员意料之外的并且令人惊奇的。或者,内玻璃板1可以,例如,还用未施加预应力的硼硅酸盐玻璃制成。据证实,甚至使用这种玻璃组合(外玻璃板1.6毫米,未施加预应力的钠钙玻璃;中间层0.76毫米PVB;内玻璃板0.3毫米未施加预应力的硼硅酸盐玻璃),可以获得非常好的关于稳定性和抗破裂性方面的结果。图2描绘了根据本发明的用于制备根据本发明的复合玻璃的方法的一个实施方案的流程图。内玻璃板1和外玻璃板2以平面的开始状态进行提供。使内玻璃板1和外玻璃板2一起经受弯曲工艺并且全等地弯曲为它们的最终的三维形状。任选地,内玻璃板1在弯曲之后施加化学预应力。为此,内玻璃板1在弯曲之后缓慢地进行冷却以避免热应力。适当的冷却速率是例如0.1℃/秒。内玻璃板1随后在460℃的温度下使用硝酸钾熔体进行处理数小时的时间段,例如4小时,并由此施加化学预应力。该处理引起经由该玻璃的表面钠离子用更大的钾离子的扩散驱动交换。由此产生表面压缩应力。内玻璃板1随后进行冷却和然后用硫酸洗涤以除去硝酸钾的残留物。随后,热塑性中间层3被布置在内玻璃板1和外玻璃板2之间。由内玻璃板1、中间层3和外玻璃板2组成的堆叠体以传统方法通过层压,例如通过真空袋方法进行接合。附图标记列表:(1)内玻璃板(2)外玻璃板(3)中间层。当前第1页1 2 3