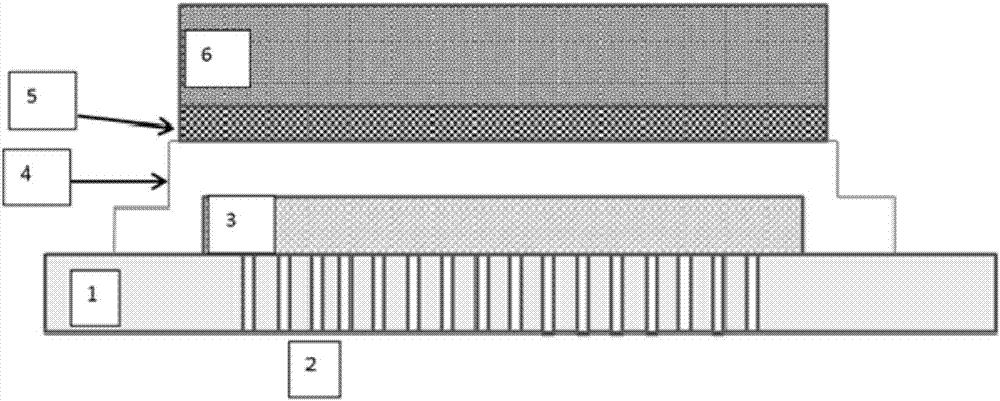
本发明涉及一种用于形成金属支撑的固体氧化物燃料电池的电解质的方法,特别涉及一种改善电解质密度的方法。还描述了燃料电池,燃料电池堆和用途。
背景技术:
:固体氧化物燃料电池(sofc)是用于通过燃料气体(通常为氢气基)的电化学氧化以产生电能的电化学装置。所述装置是基于陶瓷的,并且使用氧离子导电金属氧化物衍生的陶瓷作为其电解质。作为本领域已知的陶瓷氧离子导体(最典型地为掺杂氧化锆或掺杂氧化铈)仅在超过500℃的温度(对于氧化铈基电解质)或600℃(对于氧化锆基陶瓷)时显示与技术上相关的离子电导率,所有sofc都必须在高温下运行。电解质是电池的重要部分,并且在sofc中具有四个主要功能:·以可移动的氧离子的形式允许阴极(正极空气电极)和阳极(负极燃料电极)之间的电流通过。·以电子的形式阻止电极之间的电流通过,这将导致电池内部的短路。·防止燃料和空气的混合,这意味着电解质需要至少为理论密度的95%没有相互连通孔隙,因此电解质层是不透气的,并且基本上没有缺陷。·一些电池,例如申请人在gb2,368,450中定义的电池,通过粘附在电极周围的金属基底(名义上为阳极)来提供气密边缘密封,以防止燃料侧的反应物和氧化剂侧的反应物在电池电化学附近混合。传统上,sofc是全陶瓷器件,其中电解质或电极之一为电池提供结构支撑。这种方法具有众所周知的缺点,总结如下,其阻止了sofc技术的广泛商业化。氧化锆基电解质材料的相对低的离子电导率意味着电解质支撑的sofc电池(esc)需要在高温(通常为850-1000℃)下操作,以便实现实际有用的功率输出,作为电解质需要相对较厚(>100μm)和阻碍,因此具有足够的机械强度。堆和系统组件的材料将承受在这样高的温度下的连续运行,由于成本高昂而面临挑战。更新的发展是阳极支撑的电池(asc),其中电池的结构部分是具有<20μm厚度的电解质膜的阳极(通常为镍电解质材料金属陶瓷复合材料)。asc的较薄的电解质允许在650-800℃的范围内的更低的操作温度。如果在工作温度下由于燃料损失而使得阳极中的镍氧化成氧化镍,则asc主要的问题是它们的灾难性故障的趋势(例如,可能发生在由于系统的技术故障而导致不可控停机事件的情况下)。如果发生这种情况,镍再氧化后的体积膨胀会产生应力导致整个电池破裂。由于许多sofc阴极材料相对于电解质的具有相对高的热膨胀系数,以及在电解质焙烧温度下保持足够的孔隙度的挑战,阴极支撑的电池非常难以制造。此外,以不易受来自热循环和机械振动的应力损害的方式将陶瓷燃料电池密封成堆叠是非常困难的。避免上述问题的sofc电池的设计是cerespower公开的金属支撑的sofc设计(gb2,368,450)。这种sofc电池使用在其中心区域形成的部分多孔的铁素体不锈钢箔作为其结构支撑,以允许燃料进入阳极。主要活动的电池层(阳极,电解质和阴极)通常作为厚膜全部沉积在基层的顶部。cerespowersofc电池还允许在低于通常温度的情况下操作。这些可以在450-650℃的范围内,并且通常工作温度在500-620℃的范围内(因此,cerespower电池被认为是“低温固体氧化物燃料电池”,与在超过650℃的温度下操作的、通常超过700℃的传统的固体氧化物燃料电池相反)。这通过使用主要是氧化铈基的陶瓷材料例如cgo10(ce0.9gd0.1o1.95)作为氧离子导电电解质来实现,其具有比氧化锆基材料本质上更高的氧离子导电性。稳定氧化锆的薄膜沉积在电解质中,以防止由于氧化铈基电解质的混合的离子-电子传导性而导致的电池内部短路,如gb2,456,445中所公开的。由于氧化锆层如此薄,所以其对氧离子传输的阻碍足够低,使得低温操作仍然是可能的。金属支撑的sofc的制造中的主要挑战是使用适合于批量制造的具有成本效益的方法来生产致密的,基本上无缺陷的掺杂氧化铈电解质层。如果要生产真正强大而有效的电池,需要解决的主要问题是:·在不会导致金属基层过度氧化的温度下,将电解质层烧结至>95%的理论密度(为使用cerespower设计的铁素体不锈钢基材,通常<1100℃)。·在非收缩金属支撑上烧结电解质层。这意味着烧结收缩被限制在一个维度上,烧结期间的收缩限制的问题是相对于无约束各向同性的烧结来抑制致密化。·开发避免陶瓷层中包含或引起缺陷的沉积方法。已知掺杂氧化铈比通常用于sofc电解质中的氧化锆更容易烧结至全致密,这有利于制造金属支撑的电池。然而,与氧化锆不同,在升高的温度下暴露于还原气氛时,当ce4+离子部分还原为ce3+离子时,二氧化铈可以被还原。已知这会导致材料的晶格的膨胀,这最终导致陶瓷电解质中的应力的发展,其高到足以导致电解质通过破裂而失效。这种氧化铈基电解质的特性排除了使用还原气氛以使电解质在非常高的温度下烧结而所述的钢不被氧化,正如已经报道的用于生产具有氧化锆基电解质的金属支撑的sofc一样。此外,为了便于低成本批量生产,并且避免阳极中的镍与不锈钢载体之间的相互作用的问题,非常需要在空气中烧结电解质。已知通过低量级加入某些金属氧化物,特别是氧化钴,氧化铜和氧化锂,可以显着增强掺杂氧化铈的致密化。陶瓷粉末压块的生坯密度可以通过向压实体施加高压来增强,以尽可能紧密地压实粉末。压制后的粉末压块的典型生坯密度在理论密度35-60%的范围内,这取决于粉末的形态和表面积。本发明旨在克服或改善上述问题的至少一些方面。从而可以提供一种致密的,气密的,并且可以使用低成本批量生产的在铁素体不锈钢载体上的电解质的生产方法。技术实现要素:因此,在本发明的第一方面,提供了一种用于形成用于金属支撑的固体氧化物燃料电池的电解质的方法,所述方法包括以下步骤a-d中的一个或多个:a.将掺杂氧化铈粉末可选地与烧结助剂和溶剂组合以形成浆料;b.将浆料施加到阳极层;c.干燥形成生的电解质;和d.焙烧生的电解液以形成烧结电解质;其中,步骤b中的所述浆料包括掺杂氧化铈的粉末,其具有选自双峰粒度分布,bet表面积在15-40m2/g范围内,球形形态,或它们组合的物理性质。通常所述方法包括步骤a和b以及可选的步骤c或d中的一个,通常是步骤a至d中的任何两个或三个或多个的组合或所有步骤a至d将用于提供致密的,气密掺杂氧化铈的电解质。此外,存在于步骤b的浆料中的掺杂氧化铈粉末通常具有多于一种,选自双峰粒度分布,bet表面积在20-40m2/g范围内,和球形形态的物理性质,通常这三种物理性质都存在以提供最佳的致密化电解质。更具体地说,可以制备密度大于95%的理论密度的电解质,例如在95-100%,通常95.1,97或98-100%密度的范围内,可以使用本发明的方法实现。这降低了孔隙率,因而降低了气体渗透性,因此电解质是气密的。此外,达到如此高百分比的理论密度的电解质密度确保了电解质仅具有非常低的微观孔隙率,因此在烧结期间不容易开裂(因此失效)。掺杂氧化铈的生的电解质通常由具有高氧传导性的掺杂氧化铈形成,例如掺杂钆的氧化铈(例如ce0.9gd0.1o1.95(cgo10))或掺杂钐的氧化铈(如ce0.9sm0.1o1.95)。通常,由cgo(钆掺杂氧化铈)形成掺杂氧化铈的生的电解质。在许多情况下,掺杂氧化铈首先是粉末的形式,使得初始工艺步骤可以是提供掺杂氧化铈粉末。通常粉末将具有双峰粒度分布,一个峰在约0.45μm处,一个峰在约1.6μm处。掺杂氧化铈粉末通常将具有限定的表面积,以确保形成生的电解质层的良好烧结。通常,掺杂氧化铈粉末的bet表面积的范围为15-40m2/g,更经常为20-35m2/g,更经常为24-28m2/g。通常情况下,即使使用研磨,粉末的bet表面积也将在该范围内。用于烧结生的电解质层的热力驱动力主要由可用的表面积驱动,因为减小表面积降低了系统的能量状态。因此,具有较高比表面积的粉末将在任何给定温度下更容易烧结。然而,具有高比表面积的粉末倾向于具有显著的纳米级孔隙率,因此填充较差,导致低的生坯密度。在陶瓷加工中,所述生坯密度是指在烧结之前用作陶瓷前驱体的粉末压块的密度。通常表示为相同质量的无孔隙率的陶瓷材料的理论密度的百分比。具有低生坯密度的生的粉末压块将收缩更多以达到全密度。由于在部分烧结的陶瓷中产生的高应力收缩可能引起问题,一旦收缩,可能会导致破裂失效。因此,在使用具有高bet比表面积的粉末和因此可烧结性之间达到平衡,并且实现了高的生坯密度,这是使收缩率最小化并避免开裂所必需的。选择粉末的bet表面积的范围使得其足够高以允许粉末有足够的烧结性,但是又足够低以使在尺寸太小(单个表面积太高)的颗粒之间出现的间隙最小化,以确保可以获得至少50%理论密度的生的电解质的密度。当生坯密度为至少50%的理论密度时,更容易实现最终烧结电解质的密度大于95%的理论密度,确保提供气密,坚固的电解质。使用bet表面积超出规定范围的掺杂氧化铈粉末可能导致烧结层的致密化不充分或破裂。在许多情况下,粉末将通过使用诸如碳酸铵的碱将硝酸铈溶液与掺杂剂的硝酸盐共沉淀来制备掺杂氧化铈的前驱体。然后将这种前驱体(通常掺杂铈的碱式碳酸盐)分离,干燥并煅烧以通过将碱式碳酸盐热分解成无定形氧化物,随后结晶而形成所需的掺杂氧化铈粉末。当掺杂氧化铈为cgo时,结晶将形成单相立方萤石晶体。这种方法是有利的,因为通常需要使用具有大致球形形状和很少不规则形状的颗粒的粉末。虽然经常使用共沉淀法,但是可以使用产生具有大致球形形态颗粒的任何方法都可以使用。或者,可以在制造之后对粉末进行加工以改变颗粒形状,从而制造球形颗粒。具有球形形态的颗粒的一个优点是改进颗粒的填充,这又有助于在本发明的方法中在低的(通过陶瓷加工标准)烧结温度下提供高密度电解质。通过该方法制造的粉末具有大致球形的形态,因此常常采用这种掺杂氧化铈粉末制备的方法。如本文所用,术语“大致球形”旨在描述整体形态。如本领域技术人员将理解的,颗粒是球形的,在正常公差之内并且不明显地从该形状变形。此外,几乎所有的颗粒将是“大致球形”,使得例如在90-100%的范围内是球形的,通常95-100%或98-100%的本体颗粒将具有“大致球形”的形态。浆料通常包括烧结助剂,通常这将包含过渡金属氧化物(tmo)粉末(最常见的是co3o4或cuo),因为这些tmo提供了优异的烧结增强。烧结助剂可以以总阳离子的0.5-5mol%范围内的水平存在,更通常在0.75-3mol%的范围内,更通常在1-2mol%范围内。这个水平平衡了增强致密化的需要,而不改变材料的电性能。在本发明的方法中,烧结助剂通常是粉末形式并与掺杂氧化铈混合。在这种情况下,通常它的粒径与cgo的尺寸相当或更小。这确保tmo能够与cgo均匀混合,从而在烧结时形成单相。然而,烧结助剂也可以通过在掺杂氧化铈制造过程中掺入掺杂氧化铈粉末与掺杂氧化铈粉末相结合,掺杂氧化铈制造过程是通过使烧结助剂的硝酸盐与硝酸铈和掺杂剂的硝酸盐共同沉淀。或者,烧结助剂可以加入到掺杂氧化铈中,通过将掺杂氧化铈与烧结助剂的硝酸盐溶液加入非水溶剂如乙醇中,然后干燥和热分解以从烧结助剂中将硝酸盐分解。由于在分解过程中排放有毒的氮氧化物,这个过程不是优选的,但是可以用于效益超过氮氧化物排放问题的情况。将烧结助剂与掺杂氧化铈组合的另一种可能的方法是将掺杂氧化铈粉末与烧结助剂的硝酸盐水溶液混合,然后使用合适的碱例如碳酸钠沉淀烧结助剂的氢氧化物或碳酸盐。然后将粉末洗涤,干燥并煅烧以将烧结助剂的碳酸盐或氢氧化物分解成其氧化物。在所有情况下,意图是将烧结助剂与掺杂氧化铈均匀混合,使得以均匀的方式增强烧结。在一些情况下,所述方法将进一步包括从油墨形成掺杂氧化铈生的电解质的附加步骤。通常,油墨将是可印刷丝网的油墨,然而,本领域技术人员将会理解,油墨可以使用各种各样的方法来应用,包括加压喷射应用或流动应用。这通常是通过将掺杂氧化铈粉末与烧结助剂的混合(尽管烧结助剂可能不存在),和随后浆料的形成。可选地,为了增加溶剂的分散,也将存在分散剂。分散剂通常以相对于cgo重量的5-15%的范围存在。浆料中使用的溶剂可以选自适用于制备具有无机颜料的丝网印刷油墨的各种溶剂,但通常是挥发性低的溶剂(因此油墨在沉积前不会干燥),聚合物所需的良好相容性和有限极性赋予油墨必需的流变性。合适的溶剂包括但不限于texanol(2,2,4-三甲基-1,3-戊二醇单异丁酸酯),萜品醇,丁基卡必醇,水及它们的组合物。其中,由于水与颗粒表面上的羟基之间氢键的形成,难以分散金属氧化物粉末,所以水是最不优选的,导致颗粒聚集。浆料可以具有双峰粒度分布,具有在约0.15μm处的峰,通常在0.1-0.4μm或0.15-0.35μm的范围内;和在约1.0μm的峰,通常在0.5-1.5μm或0.75-1.25μm的范围内(使用分散在texanol中的马尔文粒度分析仪(malvernmastersizer)粉末测量)。通常会有一个主峰,通常这将是在约0.3μm的峰,其中存在主峰,次要的峰通常是在约1.0μm的峰。双峰粒度分布,增强了生的电解质的烧结,以提供致密,无裂纹的电解质层。不受理论束缚,我们认为,与单峰粒度分布相比,双峰粒度分布更容易实现,因为存在较大颗粒的群体有助于颗粒的沉积,因此有助于生的电解质层填充和强度。在一些实例中,通过研磨浆料将提供双峰粒度分布。通常这是通过磨碎粉碎。研磨浆料的其它优点包括降低掺杂氧化铈粉末的粒度以及降低存在的任何烧结助剂的粒度。研磨过程还具有使存在的任何烧结助剂与掺杂氧化铈粉末均匀分散的益处。如果存在,则烧结助剂通常会在粒径减小到亚微米级,例如在0.1-0.9μm,通常为0.3-0.6μm的范围内。因此,本发明的方法可以包括研磨浆料的附加步骤,可选地产生双峰粒度分布。合适的研磨方法包括但不限于球磨,振动研磨,碾磨及它们的组合。这些都涉及将非常硬的陶瓷球添加到浆料中,并施加机械能,使得球磨子彼此连续碰撞,当粉末被夹在碰撞球之间时被粉碎。在球磨子存在的情况下,在研磨完成之后可以进行从浆料中除去球磨子的步骤。可选地,有机聚合物可以经常在研磨之后加入到浆料中,以将其转化成可丝网印刷的油墨。通常使用的有机聚合物包括粘合剂(通常在1-5wt%范围内),分散剂(如果不在研磨阶段加入),表面活性剂(通常在0.05-5wt%范围内)以及它们的组合,表面活性剂在制造和印刷期间帮助油墨平整打印和释放气泡。粘合剂具有改变油墨流变性的双重作用,以提高其触变性质,这对于有效的印刷是重要的,并且当印刷层干燥时将颗粒结合在一起,防止开裂并给予干燥的生的粉末一些压缩强度。合适的粘合剂包括但不限于聚乙烯醇缩丁醛(pvb)和乙基纤维素。合适的分散剂和表面活性剂通常是专有添加剂,由byk-chemie,basf,tego或schwegmann等公司提供。油墨形成通常需要溶解添加剂。尽管可以使用其他方法,但是这可以通过使用合适的高剪切分散混合方法,例如高速分散器(hsd)。可以使用三辊研磨机进一步均化油墨。油墨的形成使掺杂氧化铈更容易地沉积到阳极层上。通常情况是,在电解质/浆料沉积之前,阳极层已被施加到金属基底上。金属可以是金属支撑的sofc中通常使用的任何金属基底,然而,对于本发明,金属基底通常包括由gb2,368,450中描述的非穿孔区域包围的穿孔区域,其公开内容,特别是关于对于这种类型的金属支撑的sofc的基本构造,通过引用并入本文。在这些设计中,阳极定位在穿孔区域的上方,该构型提供气体通过穿孔(通常是激光钻孔)区域进入阳极。通常,金属基底将是不锈钢基底,通常铁素体不锈钢如铁素体不锈钢具有与最常用的掺杂氧化铈gdc相似的热膨胀系数;从而在加热/冷却循环期间减小半电池内的应力。通常通过将油墨沉积到阳极层上而形成生的电解质层。通常这是通过将墨水丝网印刷到阳极层上。通常,丝网印刷电解质层将覆盖阳极层并与阳极层的边缘重叠,使得电解质层覆盖未被阳极层覆盖的部分或全部金属基底。阳极层通常也通过将阳极材料配制成油墨而形成,并且通常还通过丝网印刷沉积。可选地,在电解质沉积之前,将阳极层烧结以形成多孔陶瓷复合材料(阳极)。然而,本发明不排除在生的阳极上的沉积生的电解质,并且共烧结两层,这样阳极层是生的阳极层,并且生的阳极层和生的电解质在单次烧制步骤中烧结。从制造成本的观点来看,共烧结可能是有利的,尽管通常使用顺序烧结,由于共烧结可以使得形成高质量的电解质变得困难。在一些情况下,生的电解质包括多层电解质,其通过在阳极层上的层中施加掺杂的氧化铈电解质,并在施加每层之间进行干燥。这提供了形成较厚的电解质,而不会由于在阳极层上施加单个“厚”层而引起结构控制的损失。通常电解质层的范围为1-20μm。在许多实例中,存在将任何溶剂和有机物质从生的电解质中除去的步骤,通常这种去除步骤将在干燥以形成生的电解质之后,并且将包括蒸发溶剂。这通常存在于油墨或浆料的沉积步骤中。这通常处于100-250℃或150-200℃的温度范围内,并且经常在5-20分钟的时间段内,之后溶剂将被去除。在使用该方法的这个方面,设置粘合剂具有额外的益处。通常,烘箱将用于提供热量。这个步骤可以另外地或替代地包括加热生的电解质直到有机物分解的步骤。本领域技术人员将理解如何实现这一点,然而,加热通常将在250-500℃或300-400℃的温度范围内,保持在该温度范围内(在大致恒定的温度或在范围内变化),直到发生分解。这通常将在10-60分钟的时间段内,有机物质将被燃烧/升华,从而从生的电解液中除去。通常,烘箱或炉将用于供应热量。有机物质,包覆了存在的掺杂氧化铈颗粒,以及烧结助剂颗粒,通常包括粘合剂,分散剂聚合物和表面活性剂聚合物。分解有机物质(“烧掉”)并因此将其从墨水中除去仅留下掺杂氧化铈和任何存在的烧结助剂使得电解质变得更致密。这是因为在不存在其它材料的情况下,可以使加压的掺杂氧化铈颗粒彼此更紧密。可以存在压制步骤,其中加压生的电解质以增加生坯层的密度,从而提高烧制的电解质的密度。这个步骤可以包括在50-500mpa,通常为100-400mpa,更经常为250-350mpa的范围内施加压力。具有所要求的一种或多种物理性质的沉积的生的电解质的初始密度可以在约20-40%的范围内。如果使用,压制将需要一段时间,以确保(如果尚未通过简单地提供适当形态的颗粒,粒度分布和/或表面积来获得)生的电解质的密度范围为50-60%理论密度(例如,在50-55%范围内)。本领域技术人员将能够为施加的压力选择适当的时间段,然而,压力通常将在0-5分钟范围内施加一段时间。仅当沉积的生的电解质的初始密度不在理论密度的30-60%的范围内时才考虑压制,因为已经如果在焙烧生的电解质之前发现没有达到这些密度,则电解质通常不会足够密实,使其气密且坚固耐开裂。为了获得气密的,坚固的系统,如上所述,期望焙烧后的密度大于95%的理论密度。通常,使用冷等静压,单轴囊式压迫或其组合施加压力。这些方法在生的电解质的表面上施加均匀的压力,确保达到均匀的密度。压制方法提供了一种高度压实的生坯层。通常,焙烧步骤将经常在空气气氛下在炉中发生。在某些情况下,在800-1000℃的温度范围内,在5-20℃/分钟范围内的升温速率下,已经发现有利于形成电解质。通常,速率至少为5℃/min。通常这种加热速率将在900-1100℃的温度范围内使用,更常见的是950-1050℃,更常见的是990-1030℃。通常,总加热时间将在20-120分钟,通常30-90分钟,更经常35-60分钟或35-40分钟的范围内。已经发现,在800-1000℃的温度范围内,温度升高的速率为5-20℃/分钟,可以为在金属基层(特别是钢基层)上发生电解质层烧结时内部的竞争过程的提供优点,。理想的方法是当陶瓷致密化时,将挥发性烧结助剂阳离子移动到陶瓷内的晶界,在那里它们加速烧结。然而,有一系列竞争,不良的过程发生。其中之一是通过蒸发进入炉气氛或通过扩散进入阳极,在高温下完全损失了挥发性烧结助剂物质。另一个不希望的过程是电解质层被从钢蒸发的挥发性过渡金属氧化物(特别是铬氧化物)污染。如其他地方所公开的(gb2,400,486),已知铬离子可抑制掺杂氧化铈如cgo的烧结。如果允许电解质在温度>800℃但低于其将完全致密化(通常>980℃)的温度下花费太长时间,则烧结助剂将趋于蒸发,并且铬污染物的水平将变化致使电解质将不会完全致密化。为了实现这种快速加热,连续带式炉通常用于电解质烧结,也可以使用间歇式炉,只要在>800℃下可以充分快速加热,而不会在烧结停留间隙内导致温度过度扩散。这将使生的电解质烧结成致密的不透气陶瓷,通常密度至少为理论密度的95%。如本领域技术人员将理解的,不透气电解质层的生产通常导致在电解质内存在残留的非连接孔隙,因此难以提供电解质其密度可以接近理论值的100%,通常仅在理论上的50-85%的范围内。本文所述的方法,特别是所选择的颗粒性质(粒度分布,表面积和/或形态),解决了提供极低孔隙率问题而导致高密度的电解质,产生了气密电解质层,其与本领域中已知的那些相比,不太可能破裂。此外,该方法可以包括将物质施加到金属支撑部分的至少部分,其中在电解质焙烧之前既没有施加阳极也没有施加电极材料,以至少保持部分金属支撑在电解质和/或阳极的烧结期间平坦。该物质可以是使炉子的条件为坚固并耐用的任何物质,并且具有足够大的质量以防止金属支撑变形。该物质通常是氧化铝,因为它在炉子条件下是惰性的,尽管任何惰性陶瓷或者涂覆的金属部件都可以工作。通常,该物质将被放置在金属支撑上,在生的电解质的周长的大部分(如果不是全部),使得金属支撑在烧结之后保持平坦。例如,该物质可以覆盖生的电解质的周长的30-100%,或者必要时可以是50-95%,通常70-90%或90-99%。如本领域技术人员将理解的,覆盖度取决于金属支撑的性质以及在阳极/电解质的烧结期间将其放置在其上的应力程度。在一些情况下,可能需要完整的圆周覆盖,在一些情况下,仅部分地覆盖。已经证明使用该物质可以允许在金属支撑的sofc上重复沉积大的高质量的电解质层,较大的层是可能的,因为在金属支撑上烧结电解质层不是完全约束的烧结,由于金属支撑在烧结温度下的塑性变形。这倾向于导致陶瓷层中的烧结应力被金属支撑的变形所缓和。正是由于这个原因,在烧结期间将钉状物施加到金属支撑以保持其平坦是有利的,否则由于金属支架塑性变形,从电解质施加到金属支撑的烧结应力可能足以引起基层的大的曲率。因此,该方法可以包括将物质施加到金属支撑部分的至少部分的附加步骤,其中在电解质焙烧之前既没有施加阳极也没有施加电极材料,至少保持部分金属支撑在电解质和/或阳极的烧结期间平坦。在本发明的第二方面,提供了一种用于形成燃料电池的方法,包括使用本发明第一方面的方法在金属支撑的阳极层上形成电解质,并将阴极材料应用到电解质。在本发明的第三方面,提供了通过依据本发明的第一方面的方法获得的电解质。在本发明的第四方面,进一步提供了一种包括依据本发明第三方面的电解质的燃料电池,在本发明的第五方面中,一种燃料电池堆包括至少两种依据本发明的第四方面的燃料电池。此外,在本发明的第六方面中,提供了根据本发明的第四或第五方面的燃料电池或燃料电池堆在产生电能中的用途。因此,可以说,本发明提供了一种用于形成金属支撑的固体氧化物燃料电池的电解质的方法,所述方法可选地包括以下一种或多种:a.将掺杂氧化铈粉末与烧结助剂和溶剂混合以形成浆料,掺杂氧化铈粉末(通常为钆掺杂氧化铈粉末)通常具有bet比表面积为15-40m2/g和/或大致球形的形状,烧结助剂通常为tmo烧结助剂,可选地为颗粒尺寸在1-10μm的范围内;b.可选地研磨浆料以可选地产生掺杂氧化铈粉末的双峰粒度分布;c.可选地通过可选地将一种或多种分散剂,粘合剂和表面活性剂添加到浆料中形成油墨,通常为可丝网印刷油墨;d.可选地将阳极层施加到金属基层上,金属基层可选地包括被非穿孔区域包围的穿孔区域,并且独立地可选地是钢基层;e.任选地焙烧阳极层;f.将浆料施加到阳极层,可选地在多层中施加;g.干燥形成生的电解质;h.可选地从生的电解质中除去任何溶剂和有机物质,可选地通过溶剂的蒸发,可选地在100-250℃的温度范围内,可选地通过加热将有机物质分解,可选地在250-500℃的温度范围内和可选地在5-20分钟范围内的时间段内;i.可选地压制生的电解质以增加生的电解质的密度,可选地通过施加50-500mpa的压力,可选地使用冷等静压,单轴囊式压迫或它们的组合施加压力;j.可选地在应用物质到金属载体的部分的至少部分上,其既没有施加阳极也没有施加电极材料,以保持至少部分金属支撑在电解质和/或阳极的烧结期间平坦;和k.焙烧生的电解质以形成烧结的电解质,可选地在800-1000℃的温度范围内以5-20℃/分钟的范围内的升温速率,可选地总加热时间在20-120分钟的范围内。除非另有说明,所描述的每个整数可以与本领域技术人员将理解的任何其它整数组合使用。此外,虽然本发明的所有方面优选地“包括”与该方面有关的描述的特征,但是具体设想的是它们可以由权利要求中概述的那些特征“组成”或“基本上组成”。此外,除非本文特别定义,否则所有术语均旨在被给予其在本领域中通常理解的含义。此外,在本发明的讨论中,除非另有说明,否则对参数的允许范围的上限或下限的替代值的公开,将被解释为暗示的陈述,即所述参数的在更小和更大的替代值之间的每个中间值,本身也被公开为参数的可能值。另外,除非另有说明,本申请中出现的所有数值应理解为被术语“约”所修饰。附图说明为了更容易理解本发明,将参照附图和下文具体实施例进一步描述本发明。图1是gb2,368,450中公开的燃料电池的类型的示意图;图2是图1所示的燃料电池的sem图像,如gb2,368,450中所公开的;图3是依据本发明制造的半电池;图4是在焙烧之前的图3的半电池,其包括在焙烧期间防止电池变形的物质。图5是用于本发明的具有球形形态的cgo粉末的sem图像;图6是具有非球形形态的cgo粉末的sem图像;图7是由bet表面积小于20m2/g的cgo粉末形成的烧结电解质的sem图像;图8是由bet表面积在20-40m2/g范围内的cgo粉末形成的烧结电解质的sem图像;图9是显示使用在空气中加热速率为10℃/min的推压式膨胀计测量的未掺杂(即不含过渡金属添加剂)粉末的烧结密度的图。烧结密度值是从室温到1100℃的斜坡上的瞬时值;图10是说明用于本发明的双峰粒度分布的曲线图;图11是说明用于本发明的双峰粒度分布与近似单峰粒度分布之间的比较的曲线图;和图12是包含不太明确的粒度分布的颗粒的电解质层的sem图像,如图b所示。具体实施方式图1和图2的现有技术的燃料电池包括铁素体不锈钢衬底(1),通过在基层(2)的中心区域使用激光钻取数千个孔制成部分多孔的。多孔基层由覆盖基层多孔区域的阳极层(3)覆盖。在阳极层上沉积cgo电解质层(4),其将阳极重叠在钢的未钻孔区域上,从而在阳极边缘周围形成密封。阴极具有薄的活性层(5),其中发生氧的还原,以及较厚的集电器层(6),以允许电流从堆中的电池收集。图2另外示出了非常薄的稳定氧化锆层(7)和更薄的掺杂氧化铈层(8),其阻挡电子传导性并分别形成阳极和电解质之间的界面。图3显示出了依据该专利中公开的方法制造的半电池。可以看出,在gb2,368,450公开的结构中,其中金属基层通过激光钻孔制成多孔的阳极区域(1),钢基层不可渗透的外部区域(2)和与这两者重叠的密集的cgo电解质(3),并且在阳极的边缘周围形成气密密封。当将现有技术的燃料电池与其中电解质层包含具有选自双峰粒度分布的物理性质的掺杂氧化铈粉末的燃料电池进行比较时,bet表面积在20-40m2/g范围内,球形形态或它们的组合,观察到改善的密度。图4显示出了在烧结之前施加陶瓷钉扎物质的部件,以防止由于烧结应力引起的变形。实施例可以通过将半电池放置在氦气检漏仪上来提供本发明的燃料电池是气密的证据。如果电解质的气体渗透性低于规定的阈值,则烧结层中的微观缺陷的数量和尺寸是可接受的,并且已经实现了气密层。已经发现电解质需要>95%密度以确保气体渗透性低于操作阈值。图5显示了用于本发明方法的cgo粉末。所得粉末的bet表面积在20-40m2/g的范围内。通过使用碱如碳酸铵从铈和钆的硝酸盐溶液中共沉淀前驱体制备粉末。然后将铈钆的碱式碳酸盐前驱体分离,干燥并煅烧,通过将碱式碳酸盐热分解成无定形氧化物,形成所需的cgo粉末,然后结晶形成所需的单相立方萤石晶体结构。从图5可以看出,所生产的粉末具有近似球形的形态,几乎不规则形状的颗粒。其他形态可用,如图6所示,其具有明显的非球形形态并且在使用中显示差的填充功能。这种不良填充导致电解质层的烧结密度小于95%,我们发现需要确保气体渗透性低于操作阈值。图7显示出了由bet表面积小于20m2/g的颗粒的烧结而产生的小于95%密度的烧结电解质。可以看出,烧结不良,不能获得不透气层。将其与图8的烧结电解质进行比较,其密度大于95%,并且不存在诸如裂纹的宏观缺陷。图9显示了bet表面积和密度之间的关系。然后形成图5的粉末的浆料,并使用球磨在200wh/kg浆料的比能量下研磨粉末。所得粉末具有如图10所示的双峰粒子分布。已经发现,双峰分布中较大的颗粒分配辅助生的电解质层的填充和强度。当双峰分布不如图10所示,例如,如图11所示,其中具有更多单峰分布的测试(图中的下部曲线)导致如图12所示的烧结破裂。上述结果总结在下表1中,这些结果清楚地显示了在生产不透气,无裂纹的电解质层时控制表面积,粒度分布和形态的重要性。表1电解质参数烧结电解质不破裂烧结电解质致密度>95%bet比表面积<20m2/g是否bet比表面积>40m2/g否是单峰psd否是双峰psd是是球形形态是是非球形形态否否已经证明本文所述的方法允许在金属支撑的sofc上重复沉积高质量的电解质层,其表面积高达108cm2。较大的层是可能的,因为在烧结温度下由于金属支撑的塑性变形而使烧结钢支撑上的电解质层不完全约束烧结。这倾向于导致陶瓷层中的烧结应力被钢的变形所缓和。应当理解,本发明的方法和装置能够以各种方式实现,其中只有少数已经在上述中示出和描述。当前第1页12