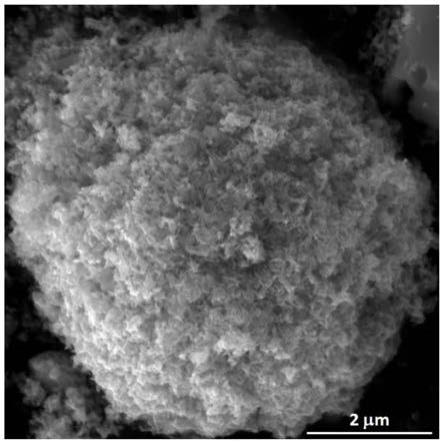
1.本发明属于钠离子电池负极材料技术领域,具体涉及双金属硒化物碳微球复合材料及其制备方法和应用。
背景技术:2.为减少能源消耗,同时满足市场需求,新能源的利用和新型储能技术的开发是目前世界能源产业发展的趋势。太阳能、风能和潮汐能等新能源,由于具有时间和空间上的不连续与不可控性,需要通过能源储存与转换器件进行加工再利用。在众多的能源储存与转换装置中,化学电源具有转换效率高、适用性强和使用便捷等优点,是目前能源技术研究的热点。锂离子电池由于其高的能量密度和功率密度被广泛应用于便携式电子设备、电动交通工具和航空航天等领域。然而,锂资源储量匮乏且分布不均,阻碍了锂离子电池的进一步开发。
3.近年来,钠离子电池由于钠资源储量丰富、价格低廉以及具有与锂离子电池相似的储能机理,得到了研究者日益广泛的关注,有望成为下一代的主流储能体系。钠离子电池的主要组成部分同锂离子电池一样,包括正负极材料、隔膜、电解液和其他配件材料,其中正负极材料特性是电池能量密度的主要决定因素。然而,钠离子较大的离子半径和摩尔质量,导致了离子扩散动力学缓慢,循环寿命有限。因此,开发出具有高容量、长循环稳定性、合适的电压平台和高安全性的正负极材料是钠离子电池商业化核心。
4.对于钠离子电池负极材料,通常包括碳材料、嵌入类、合金类以及转化类(如过渡金属氧化物、硫化物、硒化物等)负极材料。转化类负极材料由于其理论容量大,合成方法简单,已成为钠离子电池负极研究的热点之一,但是这些材料大多数表现出较差的导电性,且在脱/嵌na
+
过程中伴随较大的体积变化和金属团聚,从而影响钠离子电池的循环稳定性。金属氧化物极化较大,电导率低。金属硫化物在电化学循环过程中存在聚硫离子溶解问题,导致循环和倍率性能较差。虽然金属硒化物(m
x
se
y
)的极化相对较小,电导率相对较高,并且金属硒化物可以有效避免循环过程中金属硫化物存在的聚硫离子溶解的问题,同时硒原子还具有比硫原子直径更大、金属性更强的特点,金属硒化物较金属硫化物具有更大的层间距和更高的电导率。然而,金属硒化物在嵌脱钠过程中,存在团聚现象,其自身电子、离子传输速率差,体积膨胀还会使结构塌陷。
技术实现要素:5.本发明旨在至少解决现有技术中存在的上述技术问题之一。为此,本发明提供了一种双金属硒化物碳微球复合材料,该材料解决了硒化物在充放电过充中存在的团聚现象和体积膨胀大、导电性差的问题。
6.本发明还提供了上述双金属硒化物碳微球复合材料的制备方法。
7.本发明还提供了上述双金属硒化物碳微球复合材料的应用。
8.本发明还提供了含有上述双金属硒化物碳微球复合材料的钠离子电池。
9.本发明的第一方面提供了一种双金属硒化物碳微球复合材料,所述复合材料以碳微球为基体,所述基体的内部与表面分布有双金属硒化物纳米粒子。
10.本发明的双金属硒化物碳微球复合材料,至少具有以下有益效果:
11.本发明的双金属硒化物碳微球复合材料中,两种金属硒化物通过碳基质互相交联,均匀地结合成微米球,两种金属硒化物中,双过渡金属离子发挥金属协同效应,分散了材料的表面势能能,有利于氧化还原反应深度进行。双金属协同效果可以提高材料整体的电子和离子传输作用从而提高材料的活性和储钠性能。碳基质不仅提供了导电网络,还限制了材料的体积膨胀。
12.本发明的双金属硒化物碳微球复合材料,原料便宜、易得。具有优秀的离子、电子传输速率。兼顾了硒化锌低电压工作平台和硒化钴高容量的优点,双金属协同作用使材料获得良好的倍率性能、循环性能。材料稳定性好,储钠容量高,适合商业化应用。
13.双金属硒化物碳微球复合材料中,两种金属一个高价一个低价不是必须的。首先双金属硒化物具有更强的金属性,更低的禁带宽度,更高的电导率。因此,双金属硒化物展现出更强的化学活性以及更高的电化学活性。双金属离子分散材料中,协同效应可以诱导提高材料的表面能分散,有利于材料的氧化还原反应。
14.根据本发明的一些实施方式,所述复合材料的粒径为2μm~10μm。
15.根据本发明的一些实施方式,所述双金属硒化物包括硒化钴、硒化锌、硒化铁、硒化镍和硒化铜中的两种。
16.根据本发明的一些实施方式,所述双金属硒化物中钴的摩尔百分比为3%~7%。
17.金属钴价格昂贵,资源短缺,会成为发展的资源短板。
18.根据本发明的一些实施方式,所述双金属硒化物可以为硒化钴和硒化锌。
19.双金属硒化物为硒化钴和硒化锌时,znse、cose2均匀地结合成微米球,高价的co
4+
的引入提高了二价zn
2+
的电子、离子传输速率,发挥了双金属的协同作用,提高了材料的活性、储钠性能,同时解决了硒化物在充放电过程中存在的团聚问题和体积膨胀,提高了导电性。需要说明的是,双金属硒化物不一定需要是两种价态,是过渡金属离子即可,即可发挥双金属硒化物的协同效应。
20.本发明的第二方面提供了制备双金属硒化物碳微球复合材料的方法,包括以下步骤:
21.s1:将金属源与硒源在溶剂中分散均匀,得到溶液a;
22.s2:向所述溶液a中加入碳源与碱,搅拌均匀后得到溶液b;
23.s3:将所述溶液b置于高压反应釜中进行水热反应。
24.本发明的双金属硒化物碳微球复合材料的制备方法,无需前驱体,工艺步骤简明,反应条件不苛刻。
25.根据本发明的一些实施方式,所述金属源包括二水合醋酸锌、六水合硝酸钴、氯化铁、氯化铜、氯化镍、六水合硝酸铁、六水合硝酸镍、硝酸铜中的两种。
26.根据本发明的一些实施方式,所述金属源可以为二水合醋酸锌和六水合硝酸钴。
27.根据本发明的一些实施方式,所述溶剂包括水、甲醇或乙醇。
28.根据本发明的一些实施方式,所述硒源为硒粉。
29.根据本发明的一些实施方式,所述碳源包括葡萄糖、可溶性淀粉和一水合柠檬酸
中的至少一种。
30.根据本发明的一些实施方式,还包括在步骤s3之后,对产物进行干燥处理。
31.根据本发明的一些实施方式,所述水热反应的温度为120℃~180℃,时间为12h~30h。
32.本发明的第三方面提供了上述双金属硒化物碳微球复合材料在制备钠离子电池中的应用。
33.本发明的第四方面提供了钠离子电池,所述钠离子电池含有上述的双金属硒化物碳微球复合材料。
附图说明
34.图1是本发明双金属硒化物碳微球复合材料的扫描电镜图。
35.图2是本发明双金属硒化物碳微球复合材料的x射线衍射图。
36.图3是本发明双金属硒化物碳微球复合材料制成的钠离子电池的的倍率性能测试结果。
37.图4是本发明双金属硒化物碳微球复合材料制成的钠离子电池的循环性能。
38.图5是对比例1的单金属硒化锌碳微球复合材料的充放电长循环测试结果。
39.图6是对比例1的单金属硒化锌碳微球复合材料的微观形貌图。
40.图7是对比例2的单金属硒化钴复合碳材料的微观形貌图。
41.图8是对比例3的双金属硒化物碳微球复合材料的微观形貌图。
42.图9是对比例4的双金属硒化物碳微球复合材料的微观形貌图。
43.图10是对比例5的双金属硒化物碳微球复合材料的微观形貌图。
44.图11是对比例6的双金属硒化物碳微球复合材料的微观形貌图。
45.图12是对比例7的双金属硒化物碳微球复合材料的微观形貌图。
46.图13是对比例8的双金属硒化物碳微球复合材料的微观形貌图。
具体实施方式
47.以下是本发明的具体实施例,并结合实施例对本发明的技术方案作进一步的描述,但本发明并不限于这些实施例。
48.实施例1
49.本实施例制备了一种双金属硒化物碳微球复合材料,具体包括以下步骤:
50.(1)称取9.5mmol的二水合醋酸锌、0.5mmol的六水合硝酸钴、10mmol的硒粉,加入50ml的蒸馏水,搅拌30min使其充分溶解,溶液呈黑色;
51.(2)将1mmol葡萄糖、0.1mol氢氧化钠加入(1)中的黑色溶液,磁力搅拌2h,溶液呈褐色;
52.(3)将(2)中所述溶液置于高压反应釜中,在烘箱中加热进行水热反应,反应温度为180℃,反应时长18h;
53.(4)待反应结束后自然冷却至室温,离心收集;
54.(5)将(4)中收集的固体材料,置于60℃烘箱中,真空干燥12h,干燥完毕后,将材料研细,得到双金属硒化物碳微球复合材料。
55.其中,步骤(1)的作用是将双金属源和硒源溶解分散在溶剂中。
56.步骤(2)的作用是使硒粉与氢氧化钠发生歧化反应:
57.3se+6naoh=na2seo3+2na2se+3h2o,
58.葡萄糖为材料提供碳源。
59.步骤(3)中水热反应过程中,发生了以下反应:
60.zn(ch3coo)2+2naoh=zn(oh)2(沉淀)+2ch3coona,
61.zn(ch3coo)2+na2se=znse+2ch3coona,
62.co
4+
+2na2se=cose2+4na
+
,
63.氢氧化钠过量,过量的氢氧化钠的作用:2naoh+zn(oh)2=na2zn(oh)4,
64.na2zn(oh)4,溶于水,在后续步骤的离心洗涤中被洗去。
65.观察了本实施例制备的双金属硒化物碳微球复合材料的微观形貌,如图1所示。从图中可以看出,材料表面均匀的分布硒化锌znse、硒化钴cose2纳米球,二者和碳网络结合成了微米级的微球,且材料表面具有丰富的缺陷,给钠离子提供了穿梭通道。
66.znse和cose2通过碳基质互相交联,定向自组装成微米球。由于co
‑
se键的范德华力较大,可以产生部分团聚,从而使复合材料聚合成微米球。而均匀分布在微米球的内部和表面。
67.四价钴离子进入,发挥了双金属的协同作用以及催化效应,致使硒化钴、硒化锌纳米粒子表面催生出长程有序的碳基质,提高了材料的导电性,从而提高了离子、电子传输速率。
68.金属钴的引入,降低了复合材料的禁带宽度,金属性更强,提高了电导率,减小了转化反应所需能量。同时,双金属协同作用以及催化效应,使材料具有丰富的活性位点,更大的比表面积,有利于电解液的浸润,加快了离子的传输速率。
69.由于元素钴具有比元素锌更小的元素半径,缩小了材料的晶格间距,提高了离子、电子电导率,双金属协同效应催化效应加快了钠离子脱嵌反应,减小了材料的团聚效应。同时硒化锌、硒化钴通过碳基质交联,也限制了体积膨胀。
70.测试了本实施例制备的双金属硒化物碳微球复合材料的x射线衍射图谱,如图2所示。从图2可以看出双金属硒化物碳微球复合材料中硒化锌znse、硒化钴cose2的结晶较好。
71.实施例2
72.本实施例采用实施例1制备的双金属硒化物碳微球复合材料,制备了电池极片。具体为:
73.取70mg双金属硒化物碳微球复合材料与导电剂和粘结剂,以7:1.5:1.5的比例混合研磨,涂片。
74.待极片真空烘干后,将其冲压成电池极片。
75.实施例3
76.本实施例采用实施例2制备的电池极片,组装成钠离子电池进行电化学性能测试。
77.倍率性能如图3所示,从图3中看出,当电流密度为5a
·
g
‑1,材料的充电比容量为367.5mah
·
g
‑1,当电流密度回复到0.1a
·
g
‑1,充电比容量恢复到508.7mah
·
g
‑1(初始电流密度为0.1a
·
g
‑1时,充电比容量为503.7mah
·
g
‑1),可见本发明的钠离子电池复合负极材料具有优秀的倍率性能。说明即使在5a/g的大电流下,仍然能够获得优秀的倍率性能,说明
材料的电子、离子传输速率优秀。
78.长循环性能如图4所示,从图4可以看出,对材料进行充放电长循环测试,当电流密度为0.1a
·
g
‑1循环50圈后充电比容量为482.5mah
·
g
‑1(初始电流密度为0.1a
·
g
‑1时,充电比容量为485mah
·
g
‑1),可见本发明制备的钠离子电池复合负极材料的循环稳定性较高。
79.对比例1
80.本对比例与实施例1的区别在于本例为单金属硒化锌的制备。
81.本对比例制备了单金属硒化锌碳微球复合材料,具体包括以下步骤:
82.(1)称取10mmol的二水合醋酸锌、10mmol的硒粉,加入50ml的蒸馏水,搅拌30min使其充分溶解,溶液呈黑色;
83.(2)将1mmol葡萄糖、0.1mol氢氧化钠加入(1)中的黑色溶液,磁力搅拌2h,溶液呈褐色;
84.(3)将(2)中所述溶液置于高压反应釜中,在烘箱中加热进行水热反应,反应温度为180℃,反应时长18h;
85.(4)待反应结束后自然冷却至室温,离心收集;
86.(5)将(4)中收集的固体材料,置于60℃烘箱中,真空干燥12h,干燥完毕后,将材料研细,得到单金属硒化锌碳微球复合材料。
87.单金属硒化锌碳微球扫描电镜图如图6所示,材料呈微球状,表面纳米颗粒粒径大小分布不一,有多面体、纳米球、较大的块状结构,这不利于材料的整体氧化还原反应。
88.将材料组装成钠离子电池,对材料进行充放电长循环测试,从图5中可知,当电流密度为0.1a
·
g
‑1循环50圈后充电比容量为412.6mah
·
g
‑189.对比例2
90.本对比例与实施例1的区别在于本例是单金属硒化钴的制备。
91.(1)称取10mmol的六水合硝酸钴、10mmol的硒粉,加入50ml的蒸馏水,搅拌30min使其充分溶解,溶液呈黑色;
92.(2)将1mmol葡萄糖、0.1mol氢氧化钠加入(1)中的黑色溶液,磁力搅拌2h,溶液呈紫褐色;
93.(3)将(2)中所述溶液置于高压反应釜中,在烘箱中加热进行水热反应,反应温度为180℃,反应时长18h;
94.(4)待反应结束后自然冷却至室温,离心收集;
95.(5)将(4)中收集的固体材料,置于60℃烘箱中,真空干燥12h,干燥完毕后,将材料研细,得到单金属硒化钴碳微球复合材料。
96.单金属硒化钴复合碳材料扫描电镜图如图7所示,材料未呈球状,分布不均,硒化钴纳米团聚严重。
97.将材料组装成钠离子电池,对材料进行充放电长循环测试,从图5中可知,当电流密度为0.1a
·
g
‑1循环50圈后充电比容量为248mah
·
g
‑1,且在前10圈容量衰减较快,前10圈容量衰减了53%。
98.对比例3
99.本对比例与实施例1的区别在于水热反应时间不同。
100.(1)称取9.5mmol的二水合醋酸锌、0.5mmol的六水合硝酸钴、10mmol的硒粉,加入
50ml的蒸馏水,搅拌30min使其充分溶解,溶液呈黑色;
101.(2)将1mmol葡萄糖、0.1mol氢氧化钠加入(1)中的黑色溶液,磁力搅拌2h,溶液呈褐色;
102.(3)将(2)中所述溶液置于高压反应釜中,在烘箱中加热进行水热反应,反应温度为180℃,反应时长30h;
103.(4)待反应结束后自然冷却至室温,离心收集;
104.(5)将(4)中收集的固体材料,置于60℃烘箱中,真空干燥12h,干燥完毕后,将材料研细,得到双金属硒化物碳微球复合材料。
105.180℃水热30h的双金属硒化物碳微球复合材料电子扫描显微镜如图8所示,从图8中可以看出,复合材料仍然呈微球结构,微球由硒化钴、硒化锌的纳米颗粒均匀构成,材料的粒径较大。
106.将材料组装成钠离子电池,对材料进行充放电长循环测试,从图5中可知,当电流密度为0.1a g
‑1循环50圈后充电比容量仅为421mah
·
g
‑1。
107.对比例4
108.本对比例与实施例1的区别在于金属离子的配比不同,金属co占10%。
109.(1)称取9mmol的二水合醋酸锌、1mmol的六水合硝酸钴、10mmol的硒粉,加入50ml的蒸馏水,搅拌30min使其充分溶解,溶液呈黑色;
110.(2)将1mmol葡萄糖、0.1mol氢氧化钠加入(1)中的黑色溶液,磁力搅拌2h,溶液呈褐色;
111.(3)将(2)中所述溶液置于高压反应釜中,在烘箱中加热进行水热反应,反应温度为180℃,反应时长30h;
112.(4)待反应结束后自然冷却至室温,离心收集;
113.(5)将(4)中收集的固体材料,置于60℃烘箱中,真空干燥12h,干燥完毕后,将材料研细,得到双金属硒化物碳微球复合材料。
114.钴占摩尔比为10%时双金属硒化物碳微球复合材料电子扫描显微镜如图9所示,从图9中可以看出,复合材料仍然基本呈微球结构,微球纳米颗粒分布不均,除了细小纳米颗粒外还有较大的棒状结构构成,材料的粒径较大。
115.将材料组装成钠离子电池,对材料进行充放电长循环测试,从图5中可知,当电流密度为0.1a
·
g
‑1循环50圈后充电比容量为363.51mah
·
g
‑1。
116.对比例5
117.本对比例与实施例1的区别在于金属离子的配比不同,金属co占15%。
118.(1)称取8.5mmol的二水合醋酸锌、1.5mmol的六水合硝酸钴、10mmol的硒粉,加入50ml的蒸馏水,搅拌30min使其充分溶解,溶液呈黑色;
119.(2)将1mmol葡萄糖、0.1mol氢氧化钠加入(1)中的黑色溶液,磁力搅拌2h,溶液呈褐色;
120.(3)将(2)中所述溶液置于高压反应釜中,在烘箱中加热进行水热反应,反应温度为180℃,反应时长30h;
121.(4)待反应结束后自然冷却至室温,离心收集;
122.(5)将(4)中收集的固体材料,置于60℃烘箱中,真空干燥12h,干燥完毕后,将材料
研细,得到双金属硒化物碳微球复合材料。
123.钴占摩尔比为15%时双金属硒化物碳微球复合材料电子扫描显微镜如图10所示。
124.将材料组装成钠离子电池,对材料进行充放电长循环测试,从图5中可知,当电流密度为0.1a
·
g
‑1循环50圈后充电比容量为363.96mah
·
g
‑1。
125.对比例6
126.本对比例与实施例1的区别在于金属离子的配比不同,金属co占20%。
127.(1)称取8mmol的二水合醋酸锌、2mmol的六水合硝酸钴、10mmol的硒粉,加入50ml的蒸馏水,搅拌30min使其充分溶解,溶液呈黑色;
128.(2)将1mmol葡萄糖、0.1mol氢氧化钠加入(1)中的黑色溶液,磁力搅拌2h,溶液呈褐色;
129.(3)将(2)中所述溶液置于高压反应釜中,在烘箱中加热进行水热反应,反应温度为180℃,反应时长30h;
130.(4)待反应结束后自然冷却至室温,离心收集;
131.(5)将(4)中收集的固体材料,置于60℃烘箱中,真空干燥12h,干燥完毕后,将材料研细,得到双金属硒化物碳微球复合材料。
132.钴占摩尔比为20%时双金属硒化物碳微球复合材料电子扫描显微镜如图11所示。
133.将材料组装成钠离子电池,对材料进行充放电长循环测试,从图5中可知,当电流密度为0.1a
·
g
‑1循环50圈后充电比容量为413.01mah
·
g
‑1。
134.对比例7
135.本对比例与实施例1的区别在于金属离子的配比不同,金属co占25%。
136.(1)称取7.5mmol的二水合醋酸锌、2.5mmol的六水合硝酸钴、10mmol的硒粉,加入50ml的蒸馏水,搅拌30min使其充分溶解,溶液呈黑色;
137.(2)将1mmol葡萄糖、0.1mol氢氧化钠加入(1)中的黑色溶液,磁力搅拌2h,溶液呈褐色;
138.(3)将(2)中所述溶液置于高压反应釜中,在烘箱中加热进行水热反应,反应温度为180℃,反应时长30h;
139.(4)待反应结束后自然冷却至室温,离心收集;
140.(5)将(4)中收集的固体材料,置于60℃烘箱中,真空干燥12h,干燥完毕后,将材料研细,得到双金属硒化物碳微球复合材料。
141.钴占摩尔比为25%时双金属硒化物碳微球复合材料电子扫描显微镜如图12所示。
142.将材料组装成钠离子电池,对材料进行充放电长循环测试,从图5中可知,当电流密度为0.1a
·
g
‑1循环50圈后充电比容量为367.92mah
·
g
‑1。
143.对比例8
144.本对比例与实施例1的区别在于金属离子的配比不同,金属co占50%。
145.(1)称取5mmol的二水合醋酸锌、5mmol的六水合硝酸钴、10mmol的硒粉,加入50ml的蒸馏水,搅拌30min使其充分溶解,溶液呈黑色;
146.(2)将1mmol葡萄糖、0.1mol氢氧化钠加入(1)中的黑色溶液,磁力搅拌2h,溶液呈褐色;
147.(3)将(2)中所述溶液置于高压反应釜中,在烘箱中加热进行水热反应,反应温度
为180℃,反应时长30h;
148.(4)待反应结束后自然冷却至室温,离心收集;
149.(5)将(4)中收集的固体材料,置于60℃烘箱中,真空干燥12h,干燥完毕后,将材料研细,得到双金属硒化物碳微球复合材料。
150.钴占摩尔比为50%时双金属硒化物碳微球复合材料电子扫描显微镜如图13所示。
151.将材料组装成钠离子电池,对材料进行充放电长循环测试,从图5中可知,当电流密度为0.1a
·
g
‑1循环50圈后充电比容量为290.79mah
·
g
‑1,且在前15圈容量迅速衰减。
152.实施例1中,co在双金属硒化物中的摩尔百分比为5%时,电流密度为0.1a
·
g
‑1循环50圈后充电比容量为482.5mah
·
g
‑1,较第二圈容量衰减率为0.31%;
153.对比例1为单金属硒化锌,当电流密度为0.1a
·
g
‑1循环50圈后充电比容量为412.6mah
·
g
‑1,较第二圈容量衰减率为19.07%;
154.对比例2为单金属硒化钴,当电流密度为0.1a
·
g
‑1循环50圈后充电比容量为248mah
·
g
‑1,且在前10圈容量衰减较快,前10圈容量衰减了53%;
155.对比例3为水热时长30h的,当电流密度为0.1a
·
g
‑1循环50圈后充电比容量仅为421mah
·
g
‑1,较第二圈容量衰减率为12.68%;
156.对比例4中,co在双金属硒化物中的摩尔百分比为10%时,电流密度为0.1a
·
g
‑1循环50圈后充电比容量为363.51mah
·
g
‑1,较第二圈容量衰减率为1.18%;
157.对比例5,co在双金属硒化物中的摩尔百分比为15%时,电流密度为0.1a
·
g
‑1循环50圈后充电比容量为363.96mah
·
g
‑1,较第二圈容量衰减率为13.42%;
158.对比例6,co在双金属硒化物中的摩尔百分比为20%时,电流密度为0.1a
·
g
‑1循环50圈后充电比容量为413.01mah
·
g
‑1,较第二圈容量衰减率为34.90%;
159.对比例7,co在双金属硒化物中的摩尔百分比为25%时,电流密度为0.1a
·
g
‑1循环50圈后充电比容量为367.92mah
·
g
‑1,较第二圈容量衰减率为39.30%;
160.对比例8,co在双金属硒化物中的摩尔百分比为50%时,电流密度为0.1a
·
g
‑1循环50圈后充电比容量为290.79mah
·
g
‑1,且在前15圈容量迅速衰减40.12%。
161.上面结合实施例对本发明作了详细说明,但是本发明不限于上述实施例,在所属技术领域普通技术人员所具备的知识范围内,还可以在不脱离本发明宗旨的前提下作出各种变化。