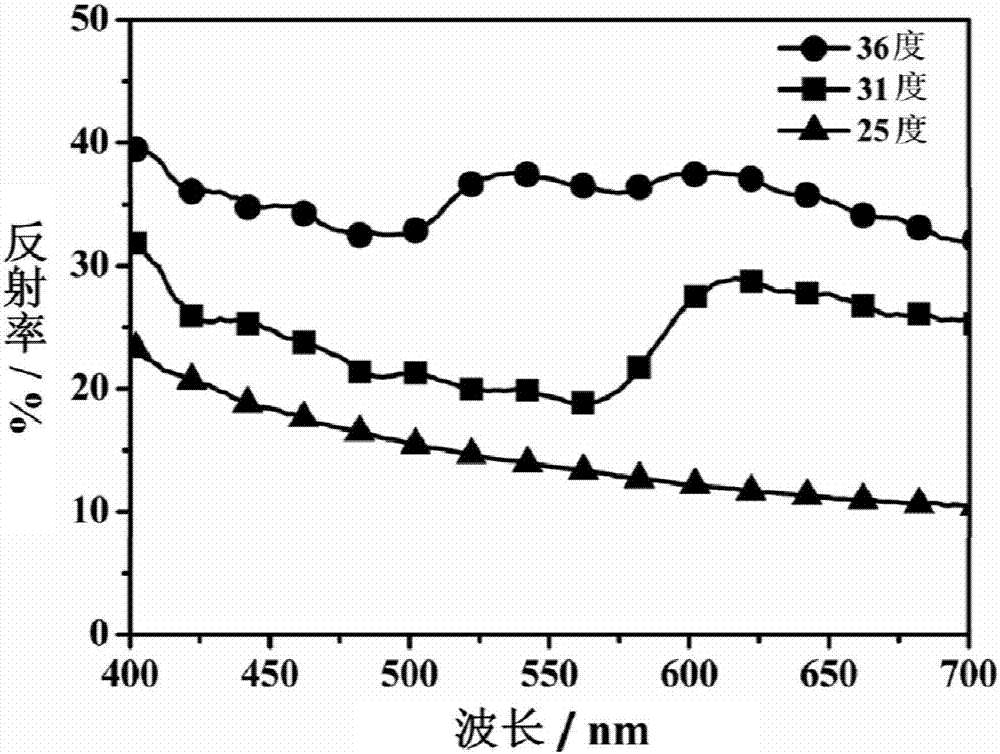
本发明属于功能性液晶材料制备和应用
技术领域:
,尤其涉及一种热致变色薄膜及其制备方法。
背景技术:
:不论是军工还是在日常生活中,热致变色材料都扮演者重要的角色。在军事领域中,现代战场中的变色术之一就是利用可逆变色材料,使被保护的目标表面的颜色随着背景的颜色不同而变色、与所处背景混成一体,从而达到视觉隐身的目的。例如,如果在军队营房的表面覆盖一层热致变色薄膜材料,冬天时就可以显示出周围沙土的颜色、春天时可以呈现周围植物的嫩绿色、夏天时显示出周围植物葱绿和鲜花的颜色、秋天则显示周围树木的枯黄色。在日常生活中,热致变色材料可作为建筑玻璃的贴膜,这种薄膜无需任何能量驱动,气温较低时薄膜呈透明状态,不影响室内采集光线和热量;而气温较高时呈强烈光散射状态,屏蔽掉太阳光辐射能,同时避免室内人员的眼睛受强烈阳光的刺激,这样可以最大限度地达到建筑节能的目的;可以用于室内玻璃、隔断、墙体、灯罩、壁画、假花等,使其随室内温度变化而变色,营造出一个梦幻般的环境;可以作为蔬菜、水果及各种乳制品的适宜保存温度指示器,还可以作为指示冷热的智能型材料,做成指示冷热用的变色茶杯、婴儿用的汤勺、奶瓶等。目前,热致变色材料的研究热点主要集中在如下几类材料上:(1)无机热致变色材料,主要包括一些金属和金属氯化物、金属氧化物和多种金属氧化物的多晶体、钒酸盐、铬酸盐、钨酸盐等。这些无机变色材料主要优点是具有良好的耐温性、耐久性、耐光照及混合加工性,但其示温变色精度较低,同时其变色机理是利用物质固有的性质,无法自主选择所希望的变色温度和颜色,使其实际应用受到一定的限制。(2)有机热致变色材料,根据其化合物的命名,可分为:三芳甲烷苯酞类、荧烷类、三苯甲烷类、席夫碱类、螺环类等。这些有机变色材料的主要优点是变色温度可选性较大、变色区间窄、颜色组合自由等,但是其耐久性,耐光照性较差,在温度较高时容易发生分解而失去温敏特性。(3)液晶热致变色材料,主要为胆甾相液晶材料,胆甾相液晶材料虽然可以实现多层次可逆变色,但是其耐久性和成膜性较差,在很大程度上限制了其实际应用。技术实现要素:为了解决现有的热致变色材料的变色温度和变化颜色不能任意设定等缺点,本发明提供了一种变色温度可调,变化颜色多样、可调的热致变色膜及其制备方法。本发明提供的热致变色膜,由多层温敏变色材料组成,每层温敏变色材料包括高分子网络骨架、液晶分子和染料;所述高分子网络骨架中聚合物分散液晶网络结构与聚合物稳定液晶网络结构共存,具体结构包括含有网孔的高分子基体,以及所述网孔内部的垂直排列的高分子网络;所述液晶分子分散在所述高分子网络骨架内部,具有近晶相~胆甾相的转变,且不同温敏变色材料层中的液晶分子的相变温度不同;所述高分子网络骨架和所述液晶分子之间分散有染料,且不同温敏变色材料层内的染料对不同波段的可见光具有吸收。上述热致变色膜,制备每层温敏变色材料的原料中液晶材料、可聚合单体、染料的配比为:液晶材料:10.0~90.0重量份;可聚合单体:10.0~80.0重量份;染料:0.01~20.0重量份。作为上述技术方案的一个较好的选择,所述可聚合单体包括液晶性可聚合单体和非液晶性可聚合单体。作为上述技术方案的一个较好的选择,每层温敏变色材料中高分子网络骨架由可聚合单体通过分步聚合而成。所述的分步聚合以及下文提及的紫外光分步聚合指的是将体系内的可聚合单体通过可控的方式实现聚合,其包括紫外光引发的预聚和紫外光及电场共同作用下的加电聚合,所述预聚是使得体系内10%~90%的非液晶性可聚合单体和0.1%~90%的液晶性可聚合单体实现聚合,从而形成具有一定粘度的基底和具有网孔的初步的高分子基体,之后再通过紫外光和电场的共同作用下使网孔内聚合形成具有明显垂直取向的高分子网络。依据用途(如刚性和柔性以及产品特性的要求),可以控制预聚的聚合度来实现对于分步聚合的控制。控制的方式可以选择延长或者缩短紫外光照的时间,如选择预聚的光照时间在10-600s之内,为了得到具有不同预聚程度的产品,可以选择的预聚紫外光照时间可以是10-30s,30-60s,60-120s,100-200s,200-400s,400-600s不等。控制预聚的紫外光照时间可以得到非液晶性可聚合单体聚合程度(单体反应比例)为10-20%,20-30%,30-50%,50-60%,60-70%,70-90%以及液晶性可聚合单体聚合程度(单体反应比例)为0.1-10%,10-20%,20-40%,40-60%,60-70%,70-90%的预聚产物。在本发明的实施例内使用了控制紫外光照时间的方式来控制分步聚合,但是本领域技术人员应当知晓,其他可以控制聚合进度的方法也可以应用于本发明的实施。作为上述技术方案的一个较好的选择,所述每层温敏变色材料中高分子基体的网孔尺寸大小为1μm~100μm。所述基体的网孔孔径可以根据需要进行控制,作为基础常识在控制了孔径后,依照本发明方法制备得到的垂直取向的高分子网络也会进行改变。对于所述的网孔大小,可以选择不同的范围值,如1-10,10-20,20-40,40-60,60-80,80-100微米不等,受制于网孔直径,相应的垂直取向的高分子网络尺寸也会相应变为更小的尺寸。作为上述技术方案的一个较好的选择,所述液晶材料为具有SmA~N*相转变的液晶材料,且层与层之间的液晶材料相变温度相差0.2℃以上。作为上述技术方案的一个较好的选择,所述液晶材料包括近晶相液晶材料和向列相液晶材料。作为上述技术方案的一个较好的选择,所述液晶材料中掺杂有手性化合物。所述液晶材料中的液晶单体包括但不仅限于下面分子中的一种或几种:其中,M、N各自独立是含有1~16个碳原子的烷基,或含1~16个碳原子的烷氧基,或含1~16碳个原子的硅氧烷基,或氰基,或卤素,或异硫氰基,或硝基;A、B各自独立为芳香族环(如1,4-苯环、2-5-嘧啶环、1,2,6-萘环),或脂肪族环(如反-1,4-环己基);A、B可含有0~4个侧基,所述侧基为卤素、氰基或甲基;x,y分别为0~4的整数;Z为酯基,或炔基,或亚甲基,或直接相连,或氮氮双键,或醚键。所述的向列相液晶材料还可选择市场在售液晶材料,如永生华清液晶材料有限公司的SLC-1717、SLC-7011、TEB30A等,德国默克液晶材料公司的E7、E44、E48、ZLI-1275等,但不仅限于这些材料。所述的手性化合物包括但不仅限于下面分子中的一种或几种,如胆甾醇壬酸酯、CB15、C15、S811、R811、S1011、R1011等.作为上述技术方案的一个较好的选择,所述在每一层内的染料对不同波段的可见光具有吸收。作为上述技术方案的一个较好的选择,所述聚合单体为紫外光可聚合单体,包括非液晶性紫外光可聚合单体和液晶性紫外光可聚合单体。其中非液晶性紫外光可聚合单体可选择但不仅限于下面中的一种或几种,如不饱和聚酯、环氧丙烯酸酯、聚氨酯丙烯酸酯、聚酯丙烯酸酯、环氧丙烯酸酯、多烯硫醇体系、聚醚丙烯酸酯、水性丙烯酸酯、乙烯基醚类等。液晶性紫外光可聚合单体亦可选择但不限于下面分子中的一种或几种,如:其中,m、n为4~8的整数,x、y为1或2,E、Q各自独立为丙烯酸酯基,或环氧基团,或聚氨酯丙烯酸酯基,或巯基。列举如下分子供参考,但并不仅限于这些材料:上述光引发剂可选择二苯甲酮、安息香双甲醚(UV651)、氯代硫杂蒽酮(ITX)、2,4-二乙基硫杂蒽酮(DETX)、异丙基硫杂蒽酮(ITX)、2-羟基-2,2-甲基-1-苯基丙酮(UV1173)等,但不仅限于这些材料。所使用间隔粒子的粒径为5um~300um。作为上述技术方案的一个较好的选择,多层温敏变色材料结构可通过多层涂膜的方式形成或将多层温敏变色薄膜叠加形成。本发明还提供前述热致变色膜的制备方法,若采用多层涂膜的方式制备,包括:(1)液晶材料LC1与可聚合单体、引发剂、染料R1共混,得到混合均一的涂料T1;(2)利用涂布设备将T1在导电薄膜上涂布均匀,并通过控制涂布速度等条件控制涂层的厚度,形成涂层L1;(3)在惰性气体保护的条件下利用紫外光照射涂层L1,使涂层L1中的可聚合单体(包括非液晶性可聚合单体和的液晶性可聚合单体)发生不完全聚合反应,得到预聚层Y1;(4)将液晶材料LC2、可聚合单体、染料R2、引发剂混合以得到均匀的涂料T2;利用涂布设备将T2在预聚层Y1上涂布均匀,形成涂层L2;随后在惰性气体保护的条件下利用紫外光照射涂层L2,使涂层L2中的可聚合单体(包括非液晶性可聚合单体和液晶性可聚合单体)发生不完全聚合反应,得到预聚层Y2;(5)重复上述步骤,直至得到预聚层Yn,n为自然数;(6)将另一块导电薄膜铺在预聚层Yn上,通过导电薄膜施加电场,同时继续对薄膜进行紫外光照射,使薄膜内部剩余的可聚合单体聚合完全,得到热致变色薄膜。上述制备方法中,不同涂层的染料Rn是不同的,分别对不同波段的可见光具有吸收。步骤(1)和(4)中,液晶分子、可聚合单体、引发剂和染料的配比为:10~90重量份的液晶材料,10~80重量份的可聚合单体,0.1~5重量份的引发剂和0.01~20重量份的染料。本发明还提供前述热致变色膜的另一种制备方法,若通过将多层温敏变色薄膜叠加的方式制备,包括:(1)将液晶材料LC1、可聚合单体、染料R1、引发剂混合以得到均匀的混合物,;(2)将步骤(1)所得混合物转移至两片导电薄膜之间;(3)通过对薄膜进行紫外光照射,使体系中的可聚合单体(包括非液晶性可聚合单体和的液晶性可聚合单体)发生不完全聚合反应;(4)对上述导电薄膜施加电场,并继续对薄膜进行紫外光照射,使剩余的可聚合单体聚合,得到温敏变色薄膜F1;(5)将液晶材料LC2、可聚合单体、染料R2、引发剂混合以得到均匀的混合物,将其转移至两片导电薄膜之间,通过对薄膜进行紫外光照射,使体系中的可聚合单体(包括非液晶性可聚合单体和的液晶性可聚合单体)发生不完全聚合反应,然后对导电薄膜施加电场,并继续对薄膜进行紫外光照射,使剩余的可聚合单体聚合,得到温敏变色薄膜F2;(6)重复上述步骤,直至得到温敏变色薄膜Fn,n为自然数;(7)将上述n层温敏变色薄膜进行叠加,得到热致变色薄膜。上述制备方法中,不同涂层的染料Rn是不同的,分别对不同波段的可见光具有吸收。步骤(1)和(5)中,液晶分子、可聚合单体、引发剂和染料的配比为:10~90重量份的液晶材料,10~80重量份的可聚合单体,0.1~5重量份的引发剂和0.01~20重量份的染料。本发明通过分步聚合的方法,将多层掺杂不同染料的温敏材料进行叠加,所制备的热致变色薄膜在不同的温度下可呈现不同的颜色,具有变色温度可调,变化颜色多样等优点。附图说明图1是实施例1中所制备的薄膜分别在25℃、31℃和36℃下的反射光谱;图2是实施例2中所制备的薄膜分别在25℃、31℃和36℃下的反射光谱;图3是实施例3中所制备的薄膜分别在25℃、31℃和36℃下的反射光谱。具体实施方式下面为本发明的实施例,其仅用做对本发明的解释而并非限制。下述实施例内,初次聚合程度可以通过其他方法来进行控制,聚合程度的差异会导致产品的性能不同,从而可以制备出不同用途的产品。在如下的实施例内,选择了两种具有近晶相(SmA)到胆甾相(N*)转变的液晶材料,记为LC1和LC2,相转变温度分别为SmA-30℃-N*-80℃-I和SmA-35℃-N*-80℃-I,市售的各种满足前述要求的材料均可以适用于本发明,本领域技术人员也可以选用
发明内容部分所选用的化合物或其组合。凡未经指明,下面实施例均在室温25℃环境进行反应。实施例1、2、3中所用到的可聚合单体的名称及结构式如下所列:其中,HMPA(Hydroxypropylmethacrylate)结构为LMA(Laurylmethacrylate)结构为PEDGA600(Polyethyleneglycoldiacrylate)结构为Bis-EMA15(Bisphenolaethoxylatedimethacrylate)结构为C6M(2-methyl-1,4-phenylene-bis(4-((6-acryloyloxy)hexyl)oxy)benzoate)结构为所使用的引发剂651(2,2-dimethoxy-1,2-diphenylethan-1-one)结构为实施例1、2、3中所用到的可聚合单体中各组分的比例见表1。表1.实施例1、2、3中所使用的可聚合单体各组分的配比名称比例(wt%)HPMA45.6LMA30.4Bis-EMA1511.4PEGDA6007.6C6M5.0实施例1本实施例中选用了蓝色和黄色染料,均购买自余姚市荆海化工颜料有限公司,本领域的技术人员也可购买其他公司的染料或自行合成,都可以应用于本发明薄膜的制备。步骤一:混配混合物M1。M1中所选用的液晶、可聚合单体、引发剂、染料的名称和配比如表2所列。将表2中的各组分按照配比进行混配,并在室温下搅拌形成各向同性液体,混合均匀。混合物总质量为19g。表2.实施例1中混合物M1所使用的各材料的配比名称比例(wt%)液晶材料LC163.2可聚合单体35.3引发剂0.5黄色染料0.8步骤二:利用涂布设备将M1涂覆在一片镀有氧化铟锡(ITO)透明导电的塑料薄膜上(ITO导电层朝上),形成一层均匀的黄色涂层。步骤三:在氮气保护的条件下,利用365nm的紫外光对步骤二中的涂层进行辐照,紫外光强为0.5mw/cm2,光照时间为90s,形成掺杂有黄色染料的预聚层Y1。步骤四:混配混合物M2。M2中所选用的液晶、可聚合单体、引发剂、染料的名称和配比如表3所列。将表3中的各组分按照配比进行混配,并在室温下搅拌形成各向同性液体,混合均匀。混合物总质量为19g。表3.实施例1中混合物M2所使用的各材料的配比名称比例(wt%)液晶材料LC263.2可聚合单体35.3引发剂0.5蓝色染料0.8步骤五:利用涂布设备将M2涂覆在预聚层Y1上,形成一层均匀的蓝色涂层。步骤六:将另一片镀有ITO导电层的塑料薄膜(导电层向内)覆盖在步骤五的蓝色涂层上。步骤七:将此薄膜在室温下由波长为365nm的紫外光进行辐照,紫外光强为0.5mw/cm2,光照时间为90s,随后将薄膜制作上电极,施加50.0Hz,170v电压,并继续利用365nm的紫外光进行辐照,紫外光强为1.5mw/cm2,辐照时间为10min,即得到实施例1的热致变色薄膜。利用紫外可见分光光度计测试薄膜在25℃、31℃和36℃下的反射光谱,如图1所示。实施例2本实施例中选用了红色和黄色染料,均购买自余姚市荆海化工颜料有限公司,本领域的技术人员也可购买其他公司的染料或自行合成,都可以应用于本发明薄膜的制备。步骤一:混配混合物H1。H1中所选用的液晶、可聚合单体、引发剂、间隔粒子、染料的名称和配比如表4所列。将表4中的各组分按照配比进行混配,并在室温下搅拌形成各向同性液体,混合均匀。混合物总质量为19g。表4.实施例2中混合物H1所使用的各材料的配比名称比例(wt%)液晶材料LC162.7可聚合单体35.3引发剂0.5红色染料0.8间隔粒子0.5步骤二:将上述混合物H1涂覆于两片镀有氧化铟锡(ITO)透明导电膜的塑料薄膜中间,用辊压匀形成薄膜。将此薄膜在室温下由波长为365nm的紫外光进行辐照,紫外光强为0.5mw/cm2,光照时间为90s,随后将薄膜制作上电极,施加50.0Hz,170v电压,并继续利用365nm的紫外光进行辐照,紫外光强为1.5mw/cm2,辐照时间为10min,得到掺杂红色染料的温敏变色薄膜F1步骤三:混配混合物H2。H2中所选用的液晶、可聚合单体、引发剂、间隔粒子、染料的名称和配比如表5所列。将表5中的各组分按照配比进行混配,并在室温下搅拌形成各向同性液体,混合均匀。混合物总质量为19g。表5.实施例2中混合物H2所使用的各材料的配比名称比例(wt%)液晶材料LC262.7可聚合单体35.3引发剂0.5黄色染料0.8间隔粒子0.5步骤四:将上述混合物H2涂覆于两片镀有氧化铟锡(ITO)透明导电膜的塑料薄膜中间,用辊压匀形成薄膜。将此薄膜在室温下由波长为365nm的紫外光进行辐照,紫外光强为0.5mw/cm2,光照时间为90s,随后将薄膜制作上电极,施加50.0Hz,170v电压,并继续利用365nm的紫外光进行辐照,紫外光强为1.5mw/cm2,辐照时间为10min,得到掺杂黄色染料的温敏变色薄膜F2步骤五:将上述F1和F2两层温敏变色膜叠加,即可得到本发明的热致变色薄膜。利用紫外可见分光光度计测试薄膜在25℃、31℃和36℃下的反射光谱,如图2所示。实施例3本实施例中选用了红色和蓝色染料,均购买自余姚市荆海化工颜料有限公司,本领域的技术人员也可购买其他公司的染料或自行合成,都可以应用于本发明薄膜的制备。步骤一:混配混合物S1。S1中所选用的液晶、可聚合单体、引发剂、间隔粒子、染料的名称和配比如表6所列。将表6中的各组分按照配比进行混配,并在室温下搅拌形成各向同性液体,混合均匀。混合物总质量为19g。表6.实施例3中混合物S1所使用的各材料的配比名称比例(wt%)液晶材料LC162.7可聚合单体35.3引发剂0.5蓝色染料0.8间隔粒子0.5步骤二:将上述混合物S1涂覆于两片镀有氧化铟锡(ITO)透明导电膜的塑料薄膜中间,用辊压匀形成薄膜。将此薄膜在室温下由波长为365nm的紫外光进行辐照,紫外光强为0.5mw/cm2,光照时间为90s,随后将薄膜制作上电极,施加50.0Hz,170v电压,并继续利用365nm的紫外光进行辐照,紫外光强为1.5mw/cm2,辐照时间为10min,得到掺杂蓝色染料的温敏变色薄膜B1步骤三:混配混合物S2。S2中所选用的液晶、可聚合单体、引发剂、间隔粒子、染料的名称和配比如表6所列。将表6中的各组分按照配比进行混配,并在室温下搅拌形成各向同性液体,混合均匀。混合物总质量为19g。表6.实施例3中混合物S2所使用的各材料的配比名称比例(wt%)液晶材料LC262.7可聚合单体35.3引发剂0.5红色染料0.8间隔粒子0.5步骤四:将上述混合物S2涂覆于两片镀有氧化铟锡(ITO)透明导电膜的塑料薄膜中间,用辊压匀形成薄膜。将此薄膜在室温下由波长为365nm的紫外光进行辐照,紫外光强为0.5mw/cm2,光照时间为90s,随后将薄膜制作上电极,施加50.0Hz,170v电压,并继续利用365nm的紫外光进行辐照,紫外光强为1.5mw/cm2,辐照时间为10min,得到掺杂红色染料的温敏变色薄膜B2步骤五:将上述B1和B2两层温敏变色膜叠加,即可得到本发明的热致变色薄膜。利用紫外可见分光光度计测试薄膜在25℃、31℃和36℃下的反射光谱,如图3所示。最后所应说明的是,以上实施例仅用以说明本发明的技术方案而非限制。尽管参照实施例对本发明进行了详细说明,本领域的普通技术人员应该理解,对本发明的技术方案进行修改或者等同替换,都不脱离本发明技术方案的精神和范围,其均应涵盖在本发明的权利要求范围当中。当前第1页1 2 3