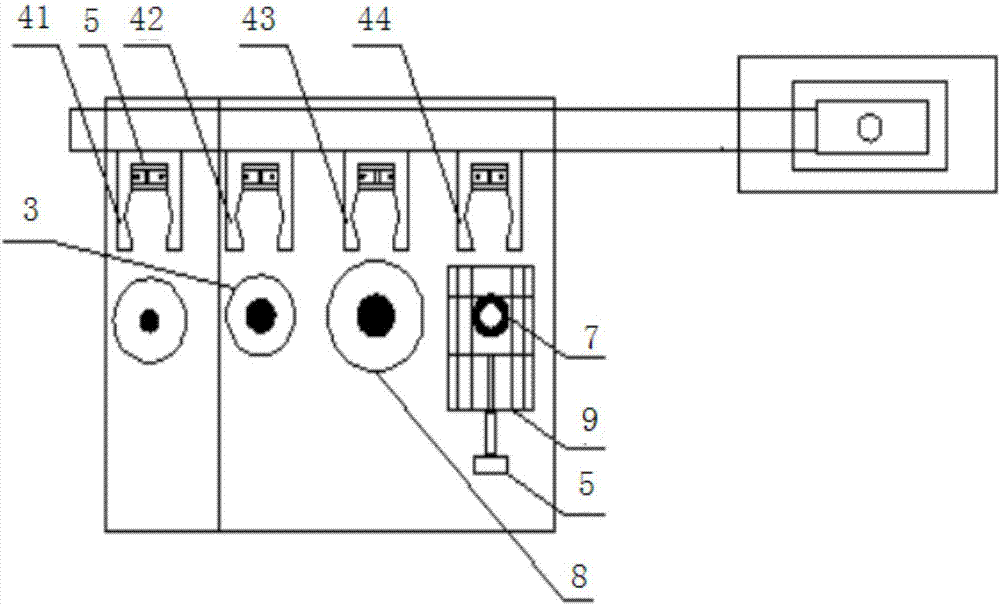
本发明涉及一种轴承生产的机械设备,特别是一种多工位自动冲压装置。
背景技术:
:我国现有各类冲床近百万台,主要分布在机械、电子、轻工、仪表等行业,大多数企业还是沿用传统的工艺生产方式,条料冲压,人工送料,明显存在以下问题:1、缺少辅机,手工送料,断指事故严重;2、材料浪费大,生产效率低,劳动强度高;3、废品率高,产品质量不好,为了解决上述问题,少数企业根据自身产品的特点,开发了一些机械装置,但是这些装置不是太简单,送料精度不高,效率低,就是返用性差,可靠性低,只能用于某种产品的生产,而国外一些发达国家推出的诸如冲床加工中心等自动化程度较高的冲压加工系统则存在系统非常复杂,价格昂贵的问题,不适合中国的国情。cn202411278涉及自动冲压生产机械手,该机械手包括底座、连在底座一端的伺服电机ⅰ、与伺服电机ⅰ输出轴连接的滚珠螺杆及通过连接座与滚珠螺杆连接的垂直支撑板,垂直支撑板的顶端连有移动平台ⅰ,移动平台ⅰ上连有可相对其滑动的移动平台ⅱ,移动平台ⅰ的一侧固定有伺服电机ⅱ,伺服电机ⅱ的输出轴连接有齿轮ⅰ,移动平台ⅱ的一侧固定连有与齿轮ⅰ相啮合的齿条ⅰ,移动平台ⅱ一侧连有可相对其的移动平台ⅲ,移动平台ⅱ上连有伺服电机ⅲ,伺服电机ⅲ的输出轴连接有齿轮ⅱ,移动平台ⅲ靠移动平台ⅱ一侧边固定连有与齿轮ⅱ相啮合的齿条ⅱ,移动平台ⅲ上分别连接有向外延伸且并排设置的上料抓取装置、抓取旋转装置及下料抓取装置。cn202123165开了一种自动冲压机械手,包括至少一台机械手主机、至少一中转台及机械手辅助工作站,主机上设有机械手与冲床上的机械手辅助工作站配合,机械手将多台冲床串联机进行自动生产;中转台设在主机与冲床之间以及相邻的冲床之间;机械手上设有可水平、垂直移动的机械手臂,用于吸取产品与工件。本实用新型通过采用自动化的机械手主机、机械手辅助工作站,以及做为工件传送机构的机械手和吸取产品的手臂相互配合完成整个送料、定位、冲压、取料的动作,完全实现冲压自动化生产。本实用新型适合多种类似规格的产品自动冲压生产,具有运行精度高、生产效率高、加工成本低、对工件规格可调的特点,可节省大量的劳动力,实现自动冲压生产。cn104525783b公开了一种自动冲压打底系统,包括压力机,压力机的两侧面为敞口设置,压力机的一侧设有翻转输送机构,翻转输送机构的外侧设有烘烤炉,压力机的另一侧设有出料输送机构,压力机内设有共轴模内机械手,从烘烤炉出来的开口向下的产品移至翻转输送机构上,由翻转输送机构输送并翻转使产品开口向上,最终将开口向上的产品输送至压力机的一侧,由共轴模内机械手抓取产品移到压力机内产品模具上,由压力机对产品进行冲压打底,冲压打底后的产品由共轴模内机械手抓取并移送至出料输送机构,由出料输送机构将产品输送至成品区。本发明自动冲压打底系统具有效率高、质量好以及能自动输送、翻转、夹取和放置的优点。现有技术中轴承生产的机械手仅能单独工位工作,机械化程度低,不但影响生产效率,也增加了工人的劳动强度。技术实现要素:本发明目的在于解决现有技术中存在的上述技术问题,提供一种多工位自动冲压装置。本发明所述的一种多工位自动冲压装置,主要通过以下步骤实现:(1)耐磨切底凹模,成型凹模的激光熔覆处理按重量份,将镍粉100份,碳化钨1-5份,苯基高流速琼脂糖微球0.01-0.1份,铁酸铋靶0.01-0.1份,纳米四氧二铁酸钴0.05-0.5份,混合均匀,得到耐磨合金粉末,在切底凹模和成型凹模表面均匀铺设0.5-2mm,使用固体脉冲激光加工机进行激光熔覆处理,得到耐磨成型凹模6和耐磨切底凹模8;(2)一种多工位自动冲压装置一种多工位自动冲压装置,包括,成型冲头1,夹子4,上墩头2,下墩头3,液压油缸5,切底冲头6,耐磨切底凹模7,耐磨成型凹模8,自动脱料装置9,所述上墩头2在下墩头3的正上方,成型冲头1在耐磨成型凹模8的正上方,切底冲头6在耐磨切底凹模7的正上方,下墩头3,耐磨切底凹模7,耐磨成型凹模8位于同一中心线均匀分布,上墩头2,成型冲头1,切底冲头6位于同一中心线均匀分布,夹子4共4个,为夹子41,42,43,44,位于同一中心线并均匀分布,自动脱料装置9,切底冲头6,耐磨切底凹模7位于同一中心线上。加工轴承的冲压工艺过程为,夹41把第四个料段夹起,夹子42把第三个料饼夹起,夹子44把第一个产品夹起,而机械手臂同时动作,机械手臂又沿着x方向移动特定距离,四个夹子又同时放料,完成各自的任务实现多工位同时工作,并传信号给冲床进行第二次冲压,把第二个料段冲压成料饼,把第一个料饼冲压成型,当冲压消失回到上死点时,放料位又感应列第三个料段,机械手臂又沿着y轴方向移动至放料位,同时pcl控制柜又通过电子阀移动夹子41,把第三个料段夹起,夹子42把第二个料饼夹起,夹子23把第一个成型料夹起,机械手臂又沿着x轴方向移动特定距离,夹子41把第三个料段放到下墩头3工位,夹子42把第二个料饼放到耐磨成型凹模8工位,夹子43把第一个成型料块放到耐磨切低凹模7工位,机械手臂又马上回到待机状态,这时自动脱料装置通过推进进入切低凹模上方,并传信号给冲床进行第三次冲压,把第三个料段压成料饼,把第二个料饼冲压成型,把第一个成型料切底冲穿;由于切底冲头6切底的同时会因为毛刺把产品带出凹槽,自动脱料装置上把产品从冲头上脱下,当冲床滑块回到料模上方时,自动脱料装置自动返回,放料位又感应到第四个料段,机械手臂又沿着y轴方向移动到放料位,同时pcl控制柜又通过电子阀推动夹子4,使机械手臂从待机状态沿着y轴方向移动至放料位pcl控制柜通过电子阀推动动作使夹子41,夹子42,夹子43,夹子44同时合紧把料段夹起沿着x轴方向移动特定距离,把料段送往下一个工位,放开夹子4马上回到待机状态,并传送信号给冲床进行冲压,当冲压消失回到上死点,放料位感应到有料时,机械手臂又重复以上动作不断地把上一个工位的料段传递给下一个工位,不断地自动循环,达到多工位同时冲压,自动夹料,送料,放料的目的,当放料位没有来料时pcl控制柜通过延时时间,机械手臂于自动往下一个工位递送,把每个工位的料段全部做完,并回到待机状态,等待来料。所述激光熔覆处理为在耐磨切底凹模7和耐磨成型凹模8表面用激光熔覆一层高性能合金复合材料,所述固体脉冲激光加工机进行激光熔覆的工艺为本领域现有工艺,本发明不做限制。所述特定距离为200-400mm。所述镍粉,碳化钨,苯基高流速琼脂糖微球,铁酸铋靶,纳米四氧二铁酸钴均为市售产品。所述自动机械手,pcl控制柜为市售产品。所述自动脱料装置(10),为常山亚瑞轴承有限公司公司研制产品。附图1为实施例1的设备结构示意图。附图2为实施例1的设备结构的俯视图。附图1,2说明一种多工位自动冲压装置,包括,成型冲头1,夹子4,上墩头2,下墩头3,液压油缸5,切底冲头6,耐磨切底凹模7,耐磨成型凹模8,自动脱料装置9,所述上墩头2在下墩头3的正上方,成型冲头1在耐磨成型凹模8的正上方,切底冲头6在耐磨切底凹模7的正上方,下墩头3,耐磨切底凹模7,耐磨成型凹模8位于同一中心线均匀分布,上墩头2,成型冲头1,切底冲头6位于同一中心线均匀分布,夹子4共4个,为夹子41,42,43,44,位于同一中心线并均匀分布,自动脱料装置9与切底冲头6,耐磨切底凹模7位于同一中心线上。与现有技术相比,本发明的一种自动脱料装置,具有以下有益效果:1.激光熔覆处理,在金属表面生成了提高了含纳米四氧二铁酸钴的镍基复合材料熔覆层,提高了耐磨成型凹模6和耐磨切底凹模8的表面耐磨损性能,延长了耐磨成型凹模6和耐磨切底凹模8的使用寿命,挤压寿命由7200次提高到12100次。2.四个夹子同时放料,完成各自的任务实现多工位同时工作,节省时间,提高进度,生产效率较非自动化工艺提高30%以上。具体实施方式以下实例仅仅是进一步说明本发明,并不是限制本发明保护的范围。实施例1:(1)耐磨切底凹模,成型凹模的激光熔覆处理按重量份,将镍粉100份,碳化钨2份,苯基高流速琼脂糖微球0.03份,铁酸铋靶0.02份,纳米四氧二铁酸钴0.09份,混合均匀,得到耐磨合金粉末,在切底凹模和成型凹模表面均匀铺设1mm,使用固体脉冲激光加工机进行激光熔覆处理,得到耐磨成型凹模6和耐磨切底凹模8;(2)一种多工位自动冲压装置一种多工位自动冲压装置,包括,成型冲头1,夹子4,上墩头2,下墩头3,液压油缸5,切底冲头6,耐磨切底凹模7,耐磨成型凹模8,自动脱料装置9,所述上墩头2在下墩头3的正上方,成型冲头1在耐磨成型凹模8的正上方,切底冲头6在耐磨切底凹模7的正上方,下墩头3,耐磨切底凹模7,耐磨成型凹模8位于同一中心线均匀分布,上墩头2,成型冲头1,切底冲头6位于同一中心线均匀分布,夹子4共4个,为夹子41,42,43,44,位于同一中心线并均匀分布,自动脱料装置(10)与切底冲头(6),耐磨切底凹模(7)位于同一中心线上,产品编号为a-1。所述一段距离为240mm。实施例2:一种多工位自动冲压装置,主要通过以下步骤实现:(1)耐磨切底凹模,成型凹模的激光熔覆处理按重量份,将镍粉100份,碳化钨1份,苯基高流速琼脂糖微球0.01份,铁酸铋靶0.01份,纳米四氧二铁酸钴0.05份,混合均匀,得到耐磨合金粉末,在切底凹模和成型凹模表面均匀铺设0.5mm,使用固体脉冲激光加工机进行激光熔覆处理,得到耐磨成型凹模6和耐磨切底凹模8;(2)一种多工位自动冲压装置一种多工位自动冲压装置,包括,成型冲头1,夹子4,上墩头2,下墩头3,液压油缸5,切底冲头6,耐磨切底凹模7,耐磨成型凹模8,自动脱料装置9,所述上墩头2在下墩头3的正上方,成型冲头1在耐磨成型凹模8的正上方,切底冲头6在耐磨切底凹模7的正上方,下墩头3,耐磨切底凹模7,耐磨成型凹模8位于同一中心线均匀分布,上墩头2,成型冲头1,切底冲头6位于同一中心线均匀分布,夹子4共4个,为夹子41,42,43,44,位于同一中心线并均匀分布,自动脱料装置(10)与切底冲头(6),耐磨切底凹模(7)位于同一中心线上,产品编号为a-2。所述一段距离为200mm。实施例3(1)耐磨切底凹模,成型凹模的激光熔覆处理按重量份,将镍粉100份,碳化钨5份,苯基高流速琼脂糖微球0.1份,铁酸铋靶0.1份,纳米四氧二铁酸钴0.5份,混合均匀,得到耐磨合金粉末,在切底凹模和成型凹模表面均匀铺设2mm,使用固体脉冲激光加工机进行激光熔覆处理,得到耐磨成型凹模6和耐磨切底凹模8;(2)一种多工位自动冲压装置一种多工位自动冲压装置,包括,成型冲头1,夹子4,上墩头2,下墩头3,液压油缸5,切底冲头6,耐磨切底凹模7,耐磨成型凹模8,自动脱料装置9,所述上墩头2在下墩头3的正上方,成型冲头1在耐磨成型凹模8的正上方,切底冲头6在耐磨切底凹模7的正上方,下墩头3,耐磨切底凹模7,耐磨成型凹模8位于同一中心线均匀分布,上墩头2,成型冲头1,切底冲头6位于同一中心线均匀分布,夹子4共4个,为夹子41,42,43,44,位于同一中心线并均匀分布,自动脱料装置(10)与切底冲头(6),耐磨切底凹模(7)位于同一中心线上,产品编号为a-3。所述一段距离为400mm。对比例1不加入碳化钨,其它同实施例1。产品编号为a-4。对比例2不加入苯基高流速琼脂糖微球,其它同实施例1。产品编号为a-5。对比例3不加入纳米四氧二铁酸钴,其它同实施例1。产品编号为为a-6。对比例4不加入铁酸铋靶,其它同实施例1,产品编号为a-7。对比例5不进行耐磨切底凹模的激光熔覆处理,其它同实施例1,泵产品编号为a-8。表1:不同工艺做出的自动脱料装置凹模挤压寿命以及提高生产效率的比较编号挤压寿命次提高生产效率%a-11131046a-21117042a-31210047a-4896034a-5990037a-61073039a-7720032以上仅为本发明的具体实施例,但本发明的技术特征并不局限于此。当前第1页12