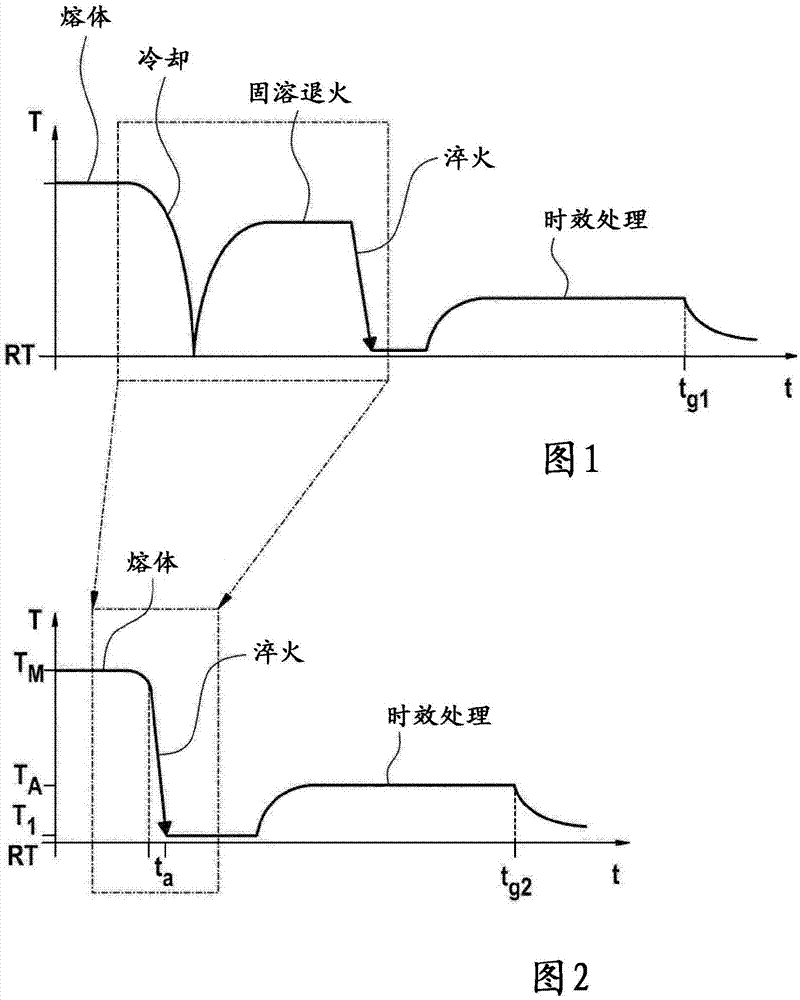
本发明涉及用于制备滑动轴承复合材料的方法,其中将轴承金属浇铸到由钢构成的带状材料上,然后使由带状材料和轴承金属构成的复合材料经历热处理。本发明还涉及滑动轴承复合材料以及由这样的滑动轴承复合材料构成的滑动元件。
背景技术:
:目前以这样的方式制备滑动轴承复合材料,在浇铸轴承金属之后使复合材料冷却至室温,然后经受包括退火步骤、淬火至室温、然后沉淀硬化(时效处理)的热处理。该方法顺序示意性示于图1中,其中将单个方法阶段的温度t相对时间t制图,并且例如描述于de496935中。rt表示室温(20℃)和tm表示熔化温度。退火步骤也被称为固溶退火,其根据din17014意指用于溶解混合晶体中的沉淀的成分的退火。例如,在奥氏体钢的情况下,使某些能够沉淀的合金元素溶于γ-混合晶体中。通过随后的充分快速冷却,获得可以硬化的过饱和的γ-混合晶体。对于在退火处理之后达到的颗粒尺寸而言,除了退火温度以外,停留时间和冷却速率也是重要的。非常缓慢的冷却,例如在炉中,导致在相对高的温度进行γ-相的转变。然而在结晶速率大时,在单位时间内形成的晶核的数量少。由此产生较粗的颗粒的前提条件。在快速冷却的情况下产生较细的组织,因为仅在较低的温度进行转变。合金添加物可能妨碍通过形成沉淀物的颗粒生长(参见e.1982ullmannsdertechnischenchemie,第22卷,第4版,第28页,verlagchemie,weinheim)。在合金中,也将固溶退火称为均匀化退火。因为几乎所有工业合金全部或大部分由混合晶体组成,所以在浇铸金属和合金的情况下经常预期或多或少地明显的结晶偏析。但是因为在合金中总是期望尽可能均匀的组织,所以致力于消除结晶偏析。这通过均匀化退火来进行。将不均匀的偏析的合金在尽可能高的温度退火如此久,直至通过扩散使晶体边缘与核之间的浓度差异平衡(参见schumannh.1989metallographie,第13版,第376页,deutscherverlagfürgrundstoffindustrie,leipzig)。“时效处理”表示保持在室温(冷时效处理)或保持在较高的温度(热时效处理),以导致从过饱和的混合晶体离析和/或沉淀。在过饱和的混合晶体耗尽时,可能出现均匀(连续)或不均匀(不连续)的沉淀。这种类型的沉淀过程例如在硬化的钢回火时具有重要作用,因为马氏体是过饱和的混合晶体并且也可以任选地沉淀出碳化物。在含有形成特别的碳化物的合金元素的钢中,这些元素的碳化物在450℃至650℃的回火温度从马氏体中沉淀并且导致二次固化(参见e.1982ullmannsdertechnischenchemie,第22卷,第4版,第34页,verlagchemie,weinheim)。一些铜合金是可硬化的。对于铜合金的硬化性,必须满足三个前提条件。对于在固体状态下的合金组分必须存在有限的溶解度,溶解度必须随着温度下降而降低,和平衡调整的惯性必须如此大,使得在高温存在的均匀的混合晶体在淬火之后保持固态(参见dki,vonkupferwerkstoffen,https://www.kupferinstitut.de/de/werkstoffe/verarbeitung/waermebehandlung.html)。由de102005063324b4已知用于制备滑动轴承复合材料,尤其是用于滑动轴承元件,如滑动轴承套的滑动轴承复合材料的通常方法。该方法提供以下方法步骤:-将铜合金浇铸到钢组成的支承层上以制备复合体,-采用以下步骤进行热机械处理:-复合体在550℃至700℃进行2至5小时的至少一次第一退火,-复合体的至少一次第一辊压,其中进行20至30%的变形程度,-在500℃至600℃进行大于1小时的至少一次第二退火。所述第一退火为均匀化退火和所述第二退火为重结晶退火。在该方法中未发生时效处理。然而,这样制备的复合材料并不满足对滑动轴承的强度的增长的要求。术语“强度”包括术语“拉伸强度”、“屈服极限”和“断裂伸长率”。技术实现要素:因此,本发明的任务在于提供滑动轴承复合材料的制备方法,所述方法可以更快地和更成本有效地进行并且同时导致具有改进的机械性质,尤其是更高的强度和更大的硬度的滑动轴承复合材料。本发明的任务还在于提供相应的滑动轴承复合材料和由此制备的滑动轴承元件。所述任务采用具有权利要求1的特征的方法得以解决。所述方法的特征在于,在浇铸轴承金属之后将复合材料淬火,然后进行时效处理过程。“然后”不仅表示“然后立即”,而且还包括在之后的时间点,例如在罩式炉中卷绕复合材料之后的时效处理,如结合图3所描述那样。在浇铸之后的热处理因此包括复合材料的淬火和时效处理过程,其也被称为时效处理。“淬火”被理解为从熔化温度快速冷却至预定温度。这样的淬火过程优选持续短于2分钟,特别优选短于1分钟。在淬火与时效处理过程之间以没有退火步骤的方式进行所述方法。通过省略退火步骤,在时间上缩短了制备方法。还节约了用于加热复合材料以进行退火步骤的能量和成本。此外还发现,通过组合浇铸、淬火过程和随后的时效处理,可以明显改进复合材料的机械性质。通过浇铸热的轴承金属熔体和通过随后淬火,使钢经受热处理,所述热处理类似用于钢硬化的热处理。轴承金属,尤其是铜合金的典型熔化温度在1000℃至1250℃,这对应于典型地用于奥氏体钢硬化的1000℃至1100℃的退火温度的范围。钢的硬化可以设定在150hbw1/5/30至250hbw1/5/30范围内。根据本发明的方法的有利之处因此在于,将浇铸与熔体的淬火过程组合用于钢的硬化。轴承金属的熔体的淬火的另外的有利之处在于,避免了结晶并且冻结了轴承金属的无序的流体结构。轴承金属中的结晶偏析因此根本不会发生,从而可以取消用于均匀化的固溶退火并且可以接着进行时效处理。冻结的无序混合晶体结构作为时效处理的起始结构的有利之处在于,例如轴承金属的硬度可以通过在宽范围内适当地选择热处理的温度和时间而有目的地进行调整。这也适用于另外的机械性质如拉伸强度(tensilestrength)和屈服极限(yieldstrength)和适用于断裂伸长率以及适用于与热导率相联系的电导率。已显示,对于时效处理过程而言,优选350℃至520℃的温度范围和优选4小时至10小时的持续时间对于有目的地调整机械性质是优选的。在此,优选将长的持续时间与低的时效处理温度组合,反之亦然。对于轴承金属,可以将硬度设定在100至200hbw1/5/30范围内和将电导率设定在20至50%iacs范围内。iacs表示国际退火铜标准。在此,将电导率表达为在纯的退火的铜中的电导率的百分比值。100%iacs对应于58·106s/m的电导率。对于拉伸强度,优选可以设定介于380mpa和500mpa之间的值,对于屈服极限,优选可以设定250至450mpa的值,和对于断裂伸长率,优选可以设定5至35%的值。优选地,时效处理过程在介于350℃和420℃之间的温度进行。在该温度范围内的时效处理一方面仅导致与铸造状态相比低的轴承金属硬度上升,其中可达到的硬度基本上等于采用常规的包括固溶退火的方法相当的硬度。但是另一方面,采用该措施相对于现有技术可以设定明显升高的轴承金属的屈服极限。因此,滑动轴承复合材料非常好地适合于重型应用,例如在重型载重汽车、建筑机械或其它重型商用机械或工作机械中,在其中将该滑动轴承复合材料用于滑动元件,例如滑动轴承套、滑动轴承瓦或滑动段。优选地,时效处理过程在介于>420℃至520℃之间的温度进行。在该温度范围内的时效处理的有利之处在于,轴承金属的硬度、拉伸强度和屈服极限相对于现有技术可以明显提高和有目的地调整。因此,滑动轴承复合材料非常好地适合用于工业领域,例如液压泵的阀板中。时效处理过程并不影响钢的已经通过淬火达到的硬度,使得仅可以选择时效处理过程的参数如温度和保持时间来调整轴承金属的性质。本方法的有利之处在于,可以制备具有非常硬的钢与不同硬度的轴承金属层组合的复合材料。优选地,将奥氏体钢用作钢,其中特别优选使用具有0.15重量%至0.40重量%的碳含量的钢。示例性钢及其组成见于下表1中。在这些钢中,通过淬火过程冻结钢的奥氏体相。优选地,浇铸由铜合金组成的轴承金属。已表明,如果将铜合金,优选可时效硬化的铜合金且尤其是铜镍合金、铜铁合金、铜铬合金或铜锆合金用作轴承金属,则可以在宽范围内调整轴承金属的机械性质。优选的铜合金的组成汇总于表2中。en表示根据欧洲标准的材料编号并且uns表示根据美国标准(astm)的材料编号。优选地,淬火过程直接在浇铸过程之后开始。由此避免了在浇铸过程之后插入正常的,即不受控制的冷却,所述不受控制的冷却的不利之处在于,轴承金属组织非常接近平衡状态,这使得在紧接浇铸之后的预定的沉淀硬化变得困难或不可能。优选地,淬火过程在浇铸过程之后15-25秒内开始。优选地,将复合材料淬火至150℃至250℃的温度t1。被动地通过任其冷却进行到室温的进一步冷却。所述冷却还可以在复合材料的卷绕状态下进行。优选地,以10k/s至30k/s的淬火速率进行淬火过程。在低于10k/s的淬火速率下,可能不保证轴承金属以过饱和的混合晶体状态存在,这使得沉淀硬化变得困难或不可能。高于30k/s的淬火速率并非必要的,因为试验显示>30k/s的淬火速率不再导致关于沉淀效果的有利之处。优选使淬火速率适应于各自的合金。优选的是,铜镍合金的淬火以15k/s至25k/s的淬火速率进行。优选的是,铜铁合金的淬火以15k/s至25k/s的淬火速率进行。优选的是,铜铬合金的淬火以10k/s至20k/s的淬火速率进行。优选的是,铜锆合金的淬火以10k/s至25k/s的淬火速率进行。对于单独的铜合金的不同的淬火速率是必要的,因为取决于合金体系,由α-混合晶体和硬质颗粒组成的两相区域在不同大小的温度范围内延伸。因此,对于具有宽的两相区域的合金体系,必须实现更高的冷却速度,以尽可能在浇铸过程中产生比具有更窄的两相区域的体系更少的沉淀。采用冷却介质,优选借助淬火流体,尤其是借助冷油进行淬火。优选地,对复合材料的背侧喷射淬火流体。通过喷射背侧,即钢侧,保证了首先使钢淬火,然后才冷却轴承金属。由此保证了在每种情况下达到期望的钢硬度,因为轴承金属的硬度总归只通过随后的时效处理过程来调整。在制备滑动轴承复合材料时,优选将钢组成的带材从卷解绕并且连续供应至单独的相继布置的处理工作站。在制备方法结束时重新卷绕制成的滑动轴承复合材料,然后将其供应至单独的时效处理工作站。然后或在之后的时间点将滑动轴承复合材料进一步加工成滑动轴承元件,例如半滑动轴承套、滑动轴承板等。在进一步加工期间,按需要施加另外的层,尤其是滑动层。优选地,将带状材料在浇铸之前预热至在900℃至1050℃范围内的温度t0。该预热的有利之处在于,轴承金属熔体在浇铸时可以以液态均匀地完全铺展在整个带材宽度上,然后进行凝固。优选地,采用热辐射器进行预热,将所述热辐射器布置在带状材料之上或之下。另外的优选的方法步骤为在浇铸之前的钢带材的压型,即钢带材的边缘的变形;在轴承金属的淬火和凝固之后铣削轴承金属表面;和去压型,尤其是去除边缘带,这在时效处理之后。滑动轴承复合材料具有由钢组成的支承层和由浇铸的铜合金组成的轴承金属层并且特征在于轴承金属层具有枝状组织结构。“枝状结构”被理解为晶体的分枝的生长形式,其具有冷杉树状结构并且其在凝固组织中的形成形式和排列高度取决于冷却条件。支承层优选具有150hbw1/5/30至250hbw1/5/30的硬度。优选地,支承层具有190至210hbw1/5/30的硬度。优选地,轴承金属层具有100hbw1/5/30至200hbw1/5/30的硬度。优选地,轴承金属层具有100至180hbw1/5/30的硬度。优选地,轴承金属层具有380mpa至500mpa,特别优选390至480mpa的拉伸强度。优选地,轴承金属层的屈服极限在250mpa至450mpa。轴承金属层的断裂伸长率优选在5%至35%。铜合金优选为铜镍合金、铜铁合金、铜铬合金或铜锆合金。镍的合金含量优选在0.5至5重量%范围内,特别优选在1至3重量%范围内。铁的合金含量优选在1.5至3重量%范围内,特别优选在1.9至2.8重量%范围内。铬的合金含量优选在0.2至1.5重量%范围内,特别优选在0.3至1.2重量%范围内。锆的合金含量优选在0.02至0.5重量%范围内,特别优选在0.3至0.5重量%范围内。磷的合金含量优选在0.01至0.3重量%范围内,锰的含量优选在0.01至0.1重量%以及锌的含量优选在0.05至0.2重量%范围内。根据本发明的滑动轴承元件具有根据本发明的滑动轴承复合材料,以及优选具有施加在轴承金属层上的滑动层。另外有利的是,滑动层由电镀层组成。电镀层为多功能材料,其突出之处尤其在于外来颗粒的良好的嵌入性,在于对滑动配偶体的适应或者磨合性质,抗腐蚀和在于在漏油情况下的良好的应急使用性质。尤其是在使用低粘度油时,电镀层是有利的,因为在此可能出现频繁的混合摩擦状态,在这种情况下适用所述性质。电镀层优选由锡铜合金、铋铜合金或由纯铋组成。在锡铜合金中,铜的含量优选为1-10重量%。在铋铜合金中,铜的优选的含量为1-20重量%。另一优选的方法为pvd法并且在此尤其是溅射。溅射层优选由铝锡合金、铝锡铜合金、铝锡镍锰合金、铝锡硅合金或铝锡硅铜合金组成。优选地,在这些合金中,锡含量为8-40重量%,铜含量为0.5-4.0重量%,硅含量为0.02-5.0重量%,镍含量为0.02-2.0重量%和锰含量为0.02-2.5重量%。根据另一实施方案,滑动层可以由塑料层组成。塑料层优选借助漆涂方法或印刷方法,例如丝网印刷或移印,通过浸渍或通过喷涂施加。待涂布的表面在此必须通过去脂,化学或物理活化和/或机械粗糙化,例如通过喷砂或抛光适当地进行预备。塑料层的基质优选由耐高温的树脂,如pai组成。此外,可以在基质中嵌入添加物,如mos2、氮化硼、石墨或ptfe。单独的或组合的添加物的含量优选介于5和50体积%之间。表3中汇总了电镀滑动层的实例。表3(以重量%计的数据)实例456锡94铋10095铜65优选的电镀滑动层具有锡基质,其中嵌入了锡铜颗粒,其由39-55重量%的铜和余量的锡组成。颗粒直径优选为0.5μm至3μm。优选将电镀层施加在中间层上,尤其是两个中间层上,其中第一中间层由ni组成并且在其上的第二中间层由镍和锡组成。第二中间层的ni含量优选为30-40重量%的ni。第一中间层优选具有1至4μm的厚度和第二中间层优选具有2至7μm的厚度。表4中汇总了溅射层的实例。表4(以重量%计的数据)实例7891011al余量余量余量余量余量sn2235251020cu0.71.20.70.50.5si2.51.5mn1.5ni0.70.7在表5中汇总了塑料滑动层的实例。表5(以体积%计的数据)实例1213141516pai7080707565mos23020bn20石墨30ptfe2515所有提及的滑动层都可以与由铜合金组成的轴承金属层组合。优选将滑动轴承元件成形为滑动轴承套、阀板或滑动段,例如滑动导向条。附图说明在下文借助附图进一步阐述示例性实施方案:图1为根据现有技术的制备方法的示意图,图2为根据本发明的方法顺序的示意图,图3为根据本发明的带材浇铸装置的示意图,图4a和b为两个滑动元件的透视图,图5为对比实施例的作为组织状态的函数的硬度的图示,图6为对比实施例的作为组织状态的函数的轴承金属强度的图示,图7为根据本发明的实施例1至3的硬度的图示,图8为根据本发明的实施例1至3的轴承金属强度的图示,图9为钢的铁-碳图,图10为轴承金属合金cuni2si的状态图,图11为铸件组织结构的显微照片,图12为根据实施例1的轴承金属层的枝状组织结构的显微照片,图13为根据实施例2的轴承金属层的另一枝状组织结构的显微照片,图14为根据实施例3的轴承金属层的另一枝状组织结构的显微照片。具体实施方式在图2中示意性示出了根据本发明的方法顺序,其中将单个方法步骤的温度t相对于时间t作图。将熔体例如以1100℃的温度tm浇铸在由钢组成的带状材料上,然后立即将复合材料淬火至约150℃至250℃的温度t1。淬火过程持续约ta=1至3min。这之后是在350℃至520℃的温度ta的时效处理。整个方法持续时间tg2因此短于根据现有技术的方法(参见图1,tg1)。通过取消整个均匀化退火(固溶退火)而产生该缩短。在例如cuni2si的情况下,根据现有技术为此需要例如750℃至800℃的目标温度的几小时的加热时间和几小时的保持时间,这之后才是淬火。在图3中示意性示出了带材浇铸装置1。钢带材卷3位于解绕工作站2中,从所述卷解绕由钢组成的带状材料6。在随后的压型工作站8中,将带状材料6的两个边缘9向上弯曲。在加热工作站10中,将带状材料6借助布置在带状材料6的上方和下方的加热元件11预热至高达t0=1050℃的温度。熔体容器13位于随后的浇铸工作站12中,在所述容器中提供轴承金属的熔体14。在浇铸工作站12中,将熔体浇铸在带状材料6上。将制备的复合材料25在淬火工作站16中借助喷射喷嘴17淬火。将喷射喷嘴17布置在带状材料6下方,从而用由冷油组成的淬火流体18喷射复合材料25的背侧26。在随后的铣削工作站20中进行轴承金属表面的粗铣削,以去除所产生的浇铸皮或者整平表面。然后将滑动轴承复合材料30在卷绕工作站4中卷起。将边缘9在卷起时用作间隔物,使得轴承金属层并不紧贴钢带材的背侧。由此防止了轴承金属和钢的粘连。只有在当重新解绕滑动轴承复合材料用于进一步加工时的之后的时间点才去除边缘9。然后将复合材料卷5送至时效处理工作站24中,在此处在罩式炉中进行最后的时效处理,以调整轴承金属的期望的机械性质。时效处理时间在350℃至520℃的温度为介于4h和10h之间。然后进一步加工如此制备的滑动轴承复合材料30。例如可以由此通过变形制备滑动轴承套。在图4a中图示了滑动轴承套42形态的滑动元件40。滑动轴承套42具有由钢组成的支承层32、滑动轴承金属层34和滑动层36。在图4b中示出的阀板44具有带根据本发明制备的轴承金属层43的钢背32的构造。在这样的应用情况下,出于负荷的原因通常放弃滑动层36。厚度d1可以为介于1.5mm和8mm之间。轴承金属厚度d2为0.5-3.0mm。对比实施例:制备由c22+cuni2si组成的滑动轴承复合材料,其中根据de102005063324b4如下进行所述制备方法:-浇铸-在t=700℃均匀化退火5h-辊压-在t=550℃重结晶退火3h-整平(具有低变形(最大5%)的辊压步骤,其用于在限定的窗口内调整钢和轴承金属的硬度)。在图5中示出了在浇铸、均匀化退火、重结晶退火和整平之后的钢和轴承金属的硬度值。滑动轴承复合材料在制备方法结束时具有138hbw1/5/30的钢硬度和100hbw1/5/30的轴承金属硬度。在图6中示出了相应的强度值。以iacs单位给出电导率。根据本发明的实施例:如果对于特定的应用情形需要钢以及轴承金属的较高的强度,即对于其中主要要求耐磨性和耐疲劳性的应用,则这采用根据本发明的方法得以实现。根据本发明的方法同样对相同的材料(钢c22和轴承金属cuni2si)进行:-将轴承金属浇铸在钢带材上,tm=1100℃,-在0.6min从1100℃淬火至300℃,即800℃,对应于22k/s的淬火速率。在浇铸之后,将钢通过快速冷却从奥氏体区域(参见图9)淬火并且硬化。以流体形式施加的轴承金属cuni2si在快速凝固之后(参见图10)由于高冷却速率作为过饱和的α-混合晶体存在,其具有低的强度和非常高的断裂伸长率值(参见图8,铸件状态)。之后不对滑动轴承复合材料进行均匀化退火,而是在380℃/8h(实施例1)、480℃/4h(实施例2)或480℃/8h(实施例3)的温度进行时效处理,即在cuni2si合金的两相区域中的时效处理(参见图10),由此在α-混合晶体中形成硅化镍,其导致轴承金属的明显的硬度升高。尽管由此稍微降低了钢的硬度,但是始终还明显高于在对比实施例的情况(参见图7)。在图8中汇总了相应的强度值。图11显示了在根据本发明的淬火过程之后的轴承金属层34的铸件状态的显微照片。组织结构因为快速凝固(淬火)而显示出非常明显的枝状结构并且作为超饱和的混合晶体存在。图12显示了在根据实施例1的时效处理之后的轴承金属层34的显微照片。图13显示了根据实施例2的轴承金属层34的显微照片。枝状晶的主干垂直于支承层32的平面延伸并且在轴承金属的基质中形成沉淀物,其导致硬度升高。图14显示了根据实施例3的轴承金属层34的显微照片。附图标记列表1带材浇铸装置2解绕工作站3钢带材卷4卷绕工作站5复合材料卷6由钢组成的带状材料8压型工作站9边缘10预热工作站11加热元件12浇铸工作站13熔体容器14轴承金属熔体15凝固的轴承金属层16淬火工作站17喷射喷嘴18淬火流体20铣削工作站24时效处理工作站25复合材料26复合材料的背侧30滑动轴承复合材料32支承层34轴承金属层36滑动层40滑动轴承元件42滑动轴承套44阀板d1钢层厚度d2轴承金属层厚度t0预热温度tm熔体的温度t1淬火之后的温度ta时效处理的温度ta淬火时间tg1根据现有技术的方法的总时间tg2根据本发明的方法的总时间当前第1页12