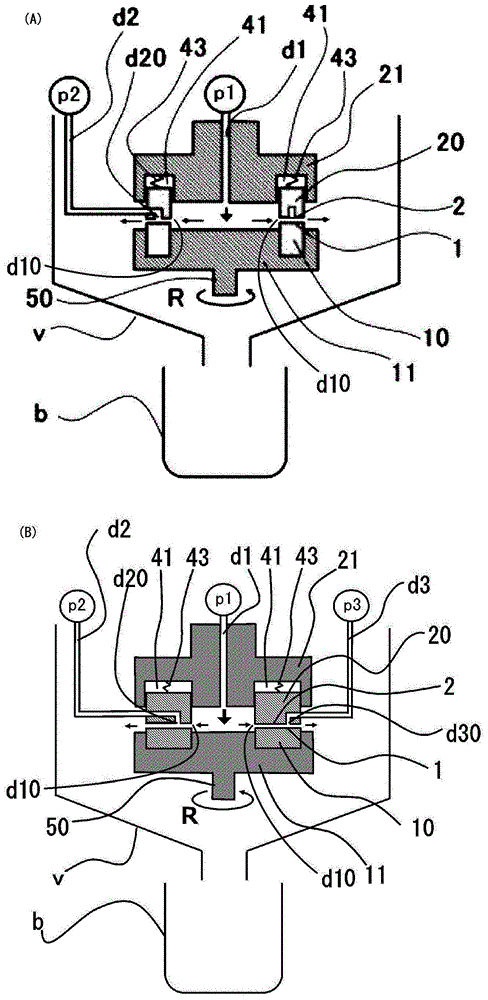
本申请是申请号为“201580068153.2”、申请日为“2015年12月15日”、发明名称为“复合酞菁微粒及其制造方法”的专利申请的分案申请。本发明涉及复合酞菁微粒及其制造方法。
背景技术:
:铜酞菁是已在颜料·半导体·感光体·记录介质·太阳能电池·液晶·催化剂等的广泛的领域中使用的材料,由于具有色相的鲜明性、高的着色力·坚牢性,因此作为青色颜料在所有的用途中使用。近年来,为了进一步发挥或者改善铜酞菁的特性,不断进行制造对于铜酞菁添加了异种金属酞菁的复合酞菁的尝试。在专利文献1中公开有由钴酞菁和铜酞菁组成的青色的颜料组合物和涂料组合物,在专利文献2中公开有含有α型钴酞菁颜料和ε型铜酞菁颜料的滤色器用颜料组合物。在这些专利文献1、专利文献2中所示的铜酞菁粒子是通过粉碎法来制造的。为了特性改善,微粒化是不可缺少的,但对于粉碎法而言,制作100nm以下、特别是50nm以下的微粒是困难的,另外,即使能够作成,制造中也需要很大的能量,强的力作用于微粒的结晶,结果结晶性差,没有获得目标的特性。因而,在对于性能的要求进一步强化的过程中,对于粉碎法而言认为存在限度。另一方面,作为消除了上述粉碎法的缺点的铜酞菁微粒的制造方法之一,已知如下的不良溶剂晶析法:通过将使铜酞菁在可将其溶解的良溶剂中溶解了的原料溶液与对于铜酞菁的溶解度比良溶剂低的不良溶剂混合,使铜酞菁微粒析出(专利文献3)。但是,在上述不良溶剂晶析法中也依然存在在有机溶剂中铜酞菁微粒进行结晶生长这样的残存课题。即,铜酞菁由于在有机溶剂中进行结晶生长,因此微粒粗大化,色特性变差。为了抑制结晶生长,考虑使用对于铜酞菁的结晶生长抑制剂。在专利文献4中,作为上述结晶生长抑制剂,教导有异种金属酞菁。但是,专利文献4中公开了的方法与上述不良溶剂晶析法不同。因此,在用不良溶剂晶析法来制造铜酞菁的情况下,关于将异种金属酞菁在怎样的工序中、以怎样的配方应用于铜酞菁来抑制结晶生长,没有任何公开。例如,关于异种金属酞菁对于铜酞菁的比率,没有任何公开。虽然如果异种金属酞菁对于铜酞菁的比率高,则抑制结晶生长,但由于异种金属酞菁的影响,色特性变差。相反,如果异种金属酞菁对于铜酞菁的比率低,则不抑制铜酞菁微粒的结晶生长,不能指望色特性的改善。对于这些课题,专利文献4没有提出任何解决对策。如在专利文献5、专利文献6中记载那样,已知在可接近·分离地相互对置配设、至少一方相对于另一方进行旋转的处理用面之间形成的薄膜流体中使流体反应的强制薄膜型的微反应器。用这样的微反应器所制作的铜酞菁微粒与用以往的配方所制造的产物相比,具有微细且均一地形成、着色力、发色力进一步提高这样的优点。另一面,奥斯特瓦尔德熟化被促进,反而倾向于在有机溶剂中粗大地生长或者引起颈缩(ネッキング),因此对于用上述微反应器制造了的微细且均一性高的铜酞菁微粒而言,存在难以发挥所期待的色特性这样的困境。实际上,就上述专利文献5或专利文献6中记载的铜酞菁微粒的可见区域中的透射·吸收光谱而言,如果从吸收光谱的观点来看,在波长600nm附近具有最高的峰,在660~700nm附近具有第2高的峰。另外,如果从透射光谱的观点来看,在400~500nm的范围显示高的透射率,虽然透射率的最大与最低成为80%以上,但从620nm至800nm,透射率再次升高。因此,就铜酞菁而言,尽管原本作为色料是希望青色至花青色的物质,但却带有红色,需要改善色特性以致呈现将红色排除了的更为鲜明的青色。另外,特别是使用微反应器制作了铜酞菁的情况下,析出反应急速地进行,因此如果如专利文献4那样只是单纯地添加了异种金属酞菁,则不能抑制析出的微粒的结晶生长,其结果未实现铜酞菁微粒的色特性改善。现有技术文献专利文献专利文献1:日本特开平10-231439号公报专利文献2:日本特开2004-252443号公报专利文献3:日本特开2012-42536号公报专利文献4:日本特开2002-155219号公报专利文献5:国际公开第2010/035861号小册子专利文献6:日本特开2012-012614号公报技术实现要素:发明要解决的课题本发明鉴于这样的实际情况,目的在于提供能够抑制结晶生长、满足所要求的特性、最适合作为颜料等色料的、纳米级、优选地100nm级以下的铜-氧钛酞菁微粒、铜-钴酞菁微粒和铜-氧钛-钴酞菁微粒等复合酞菁微粒及其制造方法。用于解决课题的手段本发明人为了解决上述课题进行了深入研究,结果发现通过以下所示的复合酞菁微粒及其制造方法能够实现上述目的,完成了本发明。本发明提供复合酞菁微粒的制造方法,其特征在于,包含:工序(1):使作为原料的、至少铜酞菁与氧钛酞菁和/或钴酞菁溶解于第1溶剂而制备溶解液;工序(2):将上述工序(1)中得到的溶解液与对于上述原料成为不良溶剂的第2溶剂混合而使复合酞菁析出;和工序(3):使有机溶剂作用于上述工序(2)中得到的复合酞菁。另外,就本发明而言,优选上述有机溶剂为芳香族化合物系溶剂或杂环式化合物系溶剂,例如,优选上述有机溶剂为选自苯乙烯、二甲苯、甲苯、苯、甲酚、枯烯、四氢呋喃、吡啶中的至少1种。通过使用对于α型铜酞菁通常诱发·促进向更为稳定的β型结晶结构等的结晶转变的芳香族化合物系溶剂或杂环式化合物系溶剂作为上述有机溶剂,令人惊奇地是,能够抑制向更为稳定的β型结晶结构等的结晶转变,另外,抑制结晶的生长可成为可能。另外,本发明能够以如下方式来实施:上述工序(1)中的上述原料的混合重量比(铜酞菁/氧钛酞菁和/或铜酞菁/钴酞菁)为1以上且不到20。另外,本发明能够通过在上述工序(1)中使氧钛酞菁和钴酞菁同时或依次溶解而实施。能够以如下方式来实施:至少上述工序(2)使用使至少2种被处理流体反应的微反应器来进行,上述被处理流体中至少1种被处理流体为上述溶解液,另一被处理流体为上述第2溶剂。具体地,能够以如下方式来实施:至少上述工序(2)使用下述的微反应器进行:将至少2种被处理流体导入可接近和分离地相互对置配设、至少一方相对于另一方相对地进行旋转的第1处理用面与第2处理用面之间,通过在第1处理用面与第2处理用面之间所赋予的导入压力,产生在使第1处理用面与第2处理用面分离的方向上发挥作用的分离力,通过上述分离力,将第1处理用面与第2处理用面之间保持为微小的间隔,且使上述至少2种被处理流体在保持为上述微小的间隔的第1处理用面与第2处理用面之间合流,在上述第1处理用面与第2处理用面之间通过,由此形成薄膜流体,在上述薄膜流体中使被处理流体之间反应;上述被处理流体中,至少1种被处理流体为上述溶解液,另一被处理流体为上述第2溶剂。另外,本发明能够以如下方式来实施:工序(2)中得到的复合酞菁与工序(3)中得到的复合酞菁为相同的晶型。即,表示在工序(3)中即使使有机溶剂作用于工序(2)中得到的复合酞菁,也不发生结晶转变。另外,本发明在上述有机溶剂中可添加表面活性剂或分散剂。另外,本发明提供复合酞菁微粒,其为至少包含铜酞菁与氧钛酞菁和/或钴酞菁的复合酞菁微粒,其特征在于,长径比为1.1以上且2.5以下,粒径为5nm以上且100nm以下。在本发明中,上述长径比是指铜-氧钛酞菁微粒等的各复合酞菁微粒中的长边与短边的比率。例如,其形状可捕捉为长方体或长方体类似体的情况下,是指3边中最长边与最短边的比率。或者,其形状可捕捉为球形或大致球形的情况的情况下,是指其最长径与最短径的比率。另外,例如,上述长径比是指由通过透射电子显微镜(tem)观察、对于100个粒子测定了长径和短径的结果的平均值求得的值。另外,在本发明中,上述粒径是指由通过透射电子显微镜(tem)观察、对于100个粒子测定了粒径的结果的平均值求得的值。能够以如下方式来实施:上述复合酞菁微粒的紫外可见区域中的吸收光谱的655~700nm中的峰顶的abs(a)与550~640nm中的峰顶的abs(b)的相对值([abs(a)]/[abs(b)])为0.8以上。在本发明中,上述abs是指基于朗伯比尔定律、在紫外可见吸收光谱测定中所算出的吸光度(abspbance),峰顶的abs是指在特定波长的范围内的abs值中最大值。发明的效果通过使用本发明的复合酞菁微粒的制造方法,能够得到最适合作为色料的、纳米级、优选地100nm级的复合酞菁微粒。特别地,通过使用本发明的制造方法,抑制在特定的溶剂中发生的结晶生长成为可能。另外,通过使用本发明的复合酞菁微粒的制造方法,耐溶剂性提高,即使在促进结晶生长的有机溶剂中,也能够抑制结晶生长,因此发挥铜酞菁微粒的本来的特性成为可能。另外,本发明的复合酞菁微粒由于具有上述长径比和粒径这样的性状,因此抑制光的散射,特别是最适合作为具有更为鲜明的青色的色料。附图说明图1的(a)为本发明的实施方式涉及的流体处理方法的实施中使用的微反应器的概略剖面图,(b)为本发明的另一实施方式涉及的流体处理方法的实施中使用的微反应器的概略剖面图。图2为图1(a)(b)中所示的微反应器的处理用面的主要部分放大图。图3为实施例1中制作了的铜-氧钛酞菁微粒等的吸收光谱测定结果。图4为实施例1、2中制作了的铜-氧钛酞菁微粒的吸收光谱测定结果。图5为实施例1中制作了的铜-氧钛酞菁微粒等的透射光谱测定结果。图6为实施例1、2中制作了的铜-氧钛酞菁微粒的透射光谱测定结果。图7为实施例1中制作了的铜-氧钛酞菁微粒的透射电子显微镜(tem)观察照片(观测倍率50000倍)。图8为实施例1中制作了的本发明的铜-氧钛酞菁微粒的透射电子显微镜(tem)观察照片(观测倍率10000倍)。图9为比较例1-2的铜-氧钛酞菁微粒的透射电子显微镜(tem)观察照片(观测倍率50000倍)。图10为比较例1-2的铜-氧钛酞菁微粒的透射电子显微镜(tem)观察照片(观测倍率10000倍)。图11为实施例3-1~3-5、比较例3-1~3-5中制作了的铜-钴酞菁微粒或铜-氧钛-钴酞菁微粒的吸收光谱测定结果。图12为实施例3-1~3-5、比较例3-1~3-5中制作了的铜-钴酞菁微粒或铜-氧钛-钴酞菁微粒的透射光谱测定结果。图13为实施例1中制作了的铜-氧钛酞菁微粒等的xrd测定结果。图14为比较例3-1~3-5中制作了的铜-钴酞菁微粒或铜-氧钛-钴酞菁微粒的xrd测定结果。图15为实施例3-1~3-5中制作了的铜-钴酞菁微粒或铜-氧钛-钴酞菁微粒的xrd测定结果。图16为实施例3-1、3-1-1~3-1-3、比较例3-1中制作了的铜-钴酞菁微粒的吸收光谱测定结果。图17为实施例3-2、3-2-1~3-2-2、比较例3-2中制作了的铜-氧钛-钴酞菁微粒的吸收光谱测定结果。图18为实施例3-3、3-3-1、比较例3-3中制作了的铜-氧钛-钴酞菁微粒的吸收光谱测定结果。图19为实施例2中制作了的铜-氧钛酞菁微粒等的吸收光谱测定结果。图20为实施例2中制作了的铜-氧钛酞菁微粒等的透射光谱测定结果。图21为实施例4-1-1~4-1-4、比较例4-1中制作了的铜-氧钛-钴酞菁微粒的吸收光谱测定结果。图22为实施例4-2-1~4-2-4、比较例4-2中制作了的铜-氧钛-钴酞菁微粒的吸收光谱测定结果。图23为本发明的实施例5~8中的制造程序例。图24为实施例5-2的工序2(清洗)后得到的本发明的复合酞菁微粒的透射电子显微镜(tem)观察照片。图25为实施例5-2的工序2(清洗)后得到的本发明的复合酞菁微粒的透射电子显微镜(tem)观察照片。图26为实施例5-2的工序3(作用)后得到的本发明的复合酞菁微粒的透射电子显微镜(tem)观察照片。图27为实施例5-2的工序3(作用)后得到的本发明的复合酞菁微粒的透射电子显微镜(tem)观察照片。具体实施方式以下对本发明的实施方式详细地说明。本发明的复合酞菁微粒的制造方法,其特征在于,包含:工序(1):使作为原料的、至少铜酞菁与氧钛酞菁和/或钴酞菁溶解于第1溶剂而制备溶解液;工序(2):将上述工序(1)中得到的溶解液与对于上述原料成为不良溶剂的第2溶剂混合而使复合酞菁析出;和工序(3):使有机溶剂作用于上述工序(2)中得到的复合酞菁。本发明涉及的复合酞菁微粒为纳米级,优选为100nm级,但根据用途,例如可以为1~200nm,也可以为2~80nm,也可以为5~50nm,还可以为10~30nm。例如,通过使用本发明的制造方法,高效率地得到上述范围的微粒成为可能。在本发明的制造方法中,具有使作为原料的、至少铜酞菁与氧钛酞菁和/或钴酞菁溶解于第1溶剂而制备溶解液的工序(1)。其中,第1溶剂作为相对于原料成为良溶剂的溶剂。在本发明中,在上述工序(1)中的上述第1溶剂中,优选使用对于上述铜酞菁和/或上述氧钛酞菁成为良溶剂的溶剂、或者、对于上述铜酞菁和/或上述钴酞菁成为良溶剂的溶剂。作为上述第1溶剂,不受特别限定,例如在酸性水溶液的情况下可使用硫酸、盐酸、硝酸、三氟乙酸、磷酸、甲磺酸、十二烷基苯磺酸、三氟乙酸等。特别是在制作被表面处理了的铜-氧钛酞菁微粒等的情况下,优选使用发烟硫酸、氯硫酸、发烟硝酸等。另外,作为上述良溶剂,除此之外,也可使用:1-甲基-2-吡咯烷酮、1,3-二甲基-2-咪唑啉酮、2-吡咯烷酮、ε-己内酰胺、甲酰胺、n-甲基甲酰胺、n,n-二甲基甲酰胺、乙酰胺、n-甲基乙酰胺、n,n-二甲基乙酰胺、n-甲基丙酰胺、六甲基磷酰三胺那样的酰胺系溶剂、二甲基亚砜、吡啶、或者这些物质的混合物等。另外,除此之外,也可以如下实施:以将上述铜酞菁和上述氧钛酞菁溶解于在各种有机溶剂中加入了碱或酸的物质的溶液的物质作为上述溶解液。作为在上述有机溶剂中加入了的碱,可举出氢氧化钠、氢氧化钾、甲醇钠、乙醇钠等。作为酸,与上述同样,可举出硫酸、盐酸、硝酸、三氟乙酸、磷酸、甲磺酸、十二烷基苯磺酸、三氟乙酸、氯硫酸等。这些物质可单独使用,也可混合2种以上来使用。在使用铜酞菁、氧钛酞菁以及钴酞菁作为原料的情况下,在上述第1溶剂中,可以使用对于3种酞菁中至少1种酞菁成为良溶剂的溶剂,希望的是,优选使用对于3种全部的酞菁成为良溶剂的溶剂。另外,在上述工序(1)中,就将铜酞菁与氧钛酞菁或钴酞菁在第1溶剂中溶解的溶解液(铜酞菁/氧钛酞菁溶液或铜酞菁/钴酞菁溶液)而言,可通过使铜酞菁与氧钛酞菁或钴酞菁同时溶解于上述良溶剂而制备,也可用如下方法制备:使铜酞菁与氧钛酞菁或钴酞菁分别溶解于上述良溶剂等、将它们适当地混合。另外,在本发明中,上述铜酞菁/氧钛酞菁溶液和上述铜酞菁/钴酞菁溶液中使用的铜酞菁、氧钛酞菁和钴酞菁并无特别限定,能够使用公知的物质。另外,在本发明中,优选上述工序(1)中的上述铜酞菁和上述氧钛酞菁的混合重量比(铜酞菁/氧钛酞菁)为1以上且不到20,可以为1.5以上且不到9.0,也可以为2.0以上且不到6.0,还可以为2.5以上且不到4.0。通过为上述范围内,更可靠地鲜明的青色的发色可成为可能。另外,在本发明中,优选上述工序(1)中的上述铜酞菁和上述钴酞菁的混合重量比(铜酞菁/钴酞菁)为1以上且不到20,可以为1.5以上且不到9.0,也可以为2.0以上且不到6.0,还可以为2.5以上且不到4.0。通过为上述范围内,更可靠地鲜明的青色的发色可成为可能。另外,在本发明的复合酞菁微粒的制造方法中,在上述工序(1)中能够使氧钛酞菁和钴酞菁同时或依次溶解。通过具有上述构成,在上述工序(1)中得到的溶解液中除了铜酞菁以外也包含氧钛酞菁和钴酞菁,由此得到的复合酞菁微粒即铜-氧钛-钴酞菁可与上述微粒同样地显现出上述效果。予以说明,所谓上述依次,可使铜酞菁、氧钛酞菁和钴酞菁以任意的顺序溶解,也可在制备了2种或3种各溶解液后适当地混合。另外,在本发明中,上述工序(1)中的上述铜酞菁、上述氧钛酞菁和钴酞菁的混合重量比(铜酞菁:氧钛酞菁:钴酞菁)例如能够设为60:30:10、60:20:20、65:30:5,可以是70:30:0、70:0:30,也可以是80:5:15、85:15:0、85:0:15、90:5:5、95:5:0、95:0:5。通过使其成为上述构成,根据目的区分制作粒径、粒子的形状、或者色特性等特性可成为可能。上述工序(1)是使至少铜酞菁与氧钛酞菁和/或钴酞菁在第1溶剂中溶解或分子分散而制备溶解液的工序。上述工序(1)优选使用搅拌叶片的周速度为1m/s以上的高速搅拌机来进行。由此当然能够抑制目前为止溶解液中的未溶解物成为原因的粗大粒子的产生,而且在将2种以上的分子、元素溶解的情况下也能够迅速地制作更为均一的溶解状态的溶解液。因此,在对置配设了的、可接近·分离的、至少一方相对于另一方相对地进行旋转的至少2个处理用面间所形成的薄膜流体中,将溶解液和与上述溶解液相比对于上述原料成为不良溶剂的第2溶剂混合而使复合酞菁微粒析出的情况下,可以在目前为止以上的程度上制作均一且均质的微粒。高速搅拌的方法不受特别限定,能够使用各种剪切式、摩擦式、高压喷射式、超声波式等的搅拌机、溶解机、乳化机、分散机、均化器等进行实施。作为一例,可以列举出ウルトラタラックス(ika制造)、ポリトロン(キネマティカ制造)、tkホモミキサー(プライミクス制造)、エバラマイルダー(荏原制作所制造)、tkホモミックラインフロー(プライミク制造)、胶体磨(神钢パンテック制造)、スラッシャー(日本焦炭工业制造)、トリゴナル湿式微粉碎机(三井三池化工机制造)、キャビトロン(ユーロテック制造)、ファインフローミル(太平洋机工制造)等连续式乳化机、クレアミックス(エム·テクニック制造)、クレアミックスディゾルバー(エム·テクニック制造)、フィルミックス(プライミク制造)等的间歇式或连续两用乳化机。此外,可使用超声波式的均化器、超声波清洗机等。另外,在本发明的制造方法中,具有将上述工序(1)中得到的溶解液和与上述溶解液相比对于上述原料成为不良溶剂的第2溶剂混合而使复合酞菁析出的工序(2)。其中,所谓对于原料成为不良溶剂的第2溶剂,设为对于原料的溶解度比第1溶剂低、可成为不良溶剂的溶剂。应予说明,将上述溶解液和第2溶剂混合而析出了的复合酞菁也包含本发明的复合酞菁微粒的前体。作为上述工序(2)中的对于上述原料成为不良溶剂的第2溶剂,优选使用与上述第1溶剂相比对于上述铜酞菁及/或上述氧钛酞菁成为不良溶剂的溶剂、或与上述第1溶剂相比对于上述铜酞菁和/或上述钴酞菁成为不良溶剂的溶剂。作为与上述第1溶剂相比对于上述原料成为不良溶剂的第2溶剂,不受特别限定,可以使用与溶解了上述铜酞菁和/或上述氧钛酞菁(或者上述钴酞菁)的溶剂相比对于上述铜酞菁和/或上述氧钛酞菁(或者上述钴酞菁)的溶解度低的溶剂来实施。例如,可举出水、醇化合物溶剂、酮系溶剂、胺化合物溶剂、酮化合物溶剂、醚化合物溶剂、芳香族化合物溶剂、二硫化炭、脂肪族化合物溶剂、腈化合物溶剂、亚砜化合物溶剂、卤素化合物溶剂、酯化合物溶剂、离子性液体溶剂、羧酸化合物溶剂、磺酸化合物溶剂、环丁砜系化合物溶剂等。这些有机溶剂可单独地使用,另外也可将2种以上混合来使用。予以说明,在本发明中,所谓可成为不良溶剂的溶剂,优选上述铜酞菁和上述氧钛酞菁及/或上述钴酞菁的溶解度为0.01质量%以下的溶剂。即使在第2溶剂中,在将多种成分搅拌的情况下或溶解的情况下,优选使用上述的高速搅拌机来制备。进而,可在包含上述溶解液的流体或者包含对于上述原料成为不良溶剂的第2溶剂的流体、或者这两者中包含嵌段共聚物、高分子聚合物、表面活性剂或其他分散剂。另外,上述的分散剂也可包含在与包含上述溶解液的流体和包含相对于上述原料成为不良溶剂的第2溶剂的流体都不同的第3流体中。作为表面活性剂及分散剂,可以使用在颜料的分散用途中使用的各种市售品。不受特别限定,例如,可以举出十二烷基硫酸钠或ネオゲンr-k(第一工业制药制)这样的十二烷基苯磺酸系、ソルスパース20000、ソルスパース24000、ソルスパース26000、ソルスパース27000、ソルスパース28000、ソルスパース41090(以上、アビシア制)、ディスパービック160、ディスパービック161、ディスパービック162、ディスパービック163、ディスパービック166、ディスパービック170、ディスパービック180、ディスパービック181、ディスパービック182、ディスパービック183、ディスパービック184、ディスパービック190、ディスパービック191、ディスパービック192、ディスパービック2000、ディスパービック2001(以上、ビックケミー制)、ポリマー100、ポリマー120、ポリマー150、ポリマー400、ポリマー401、ポリマー402、ポリマー403、ポリマー450、ポリマー451、ポリマー452、ポリマー453、efka-46、efka-47、efka-48、efka-49、efka-1501、efka-1502、efka-4540、efka-4550(以上、efkaケミカル制)、フローレンdopa-158、フローレンdopa-22、フローレンdopa-17、フローレンg-700、フローレンtg-720w、フローレン-730w、フローレン-740w、フローレン-745w、(以上、共栄化学制)、アジスパーpa111、アジスパーpb711、アジスパーpb811、アジスパーpb821、アジスパーpw911(以上、味の素制)、ジョンクリル678、ジョンクリル679、ジョンクリル62(以上、ジョンソンポリマー制)、アクアロンkh-10、ハイテノールnf-13(以上、第一工业制药制)等。这些可单独地使用,另外也可将2种并用。对于对上述复合酞菁进行表面处理的情况,在以下进行说明。就利用在上述复合酞菁的至少表面导入修饰基的表面处理而言,例如,如果在使用如图1中所记载的那样的微反应器的情况下进行例示,能够通过在导入到处理用面1、2间的流体中含有表面修饰剂来实施。就上述表面修饰剂而言,可以在含有上述溶解液的流体(第1流体)、或者含有对于上述原料成为不良溶剂的第2溶剂的流体(第2流体)的任一者、或者其两者中含有,也可以在与含有上述溶解液的流体、含有对于上述原料成为不良溶剂的第2溶剂的流体都不同的第3流体中含有。另外,作为第1流体及第2流体的组合不限于上述。作为表面修饰基团至少在颜料表面进行导入的修饰基团的种类,不受特别限定,在表面处理的目的为分散性的提高作为目的的情况下,例如,可以根据以分散为目的溶剂、分散剂种类来分开使用。例如可以举出,酸性基团、碱性基团等的极性基团、上述极性基の盐结构、酸素、硫黄等的极性大的原子及/或芳香环等被导入了的分极率大的结构、具有氢键合性基团、杂环、芳香环等的修饰基团等。作为酸性基团,可举出羟基(hudroxygroup)、磺酸基团(磺基)、羧酸基、磷酸基、硼酸基等。作为碱性基团,可举出氨基。作为氢键合性基团,可举出氨基甲酸酯部位、硫代氨基甲酸酯部位、脲部位、硫脲部位等。在表面处理的目的为分散性的提高以外的情况下,例如,在使上述复合酞菁的表面为防水性、亲油性、或亲有机溶剂性的情况下,能够通过上述第1流体或者第2流体、或其两者中含有包含亲油性官能基的表面修饰剂来将亲油性官能团作为修饰基团导入到从处理用面1、2间排出的复合酞菁的表面、进行亲油性处理。另外,上述表面修饰剂は也可以在与上述第1流体和上述第2流体都不同的第3流体中含有。在施加在复合酞菁的表面附加树脂作为表面修饰剂的处理的情况下,能够通过在上述第1流体或者第2流体、或其两者中含有包含树脂的物质来将从处理用面1、2间排出的复合酞菁的表面的至少一部分用树脂覆盖、例如进行亲水性处理。另外,上述树脂也可在与上述第1流体和上述第2流体都不同的第3流体中含有。就上述的表面处理而言,如上所述,不限于在处理用面1、2间进行复合酞菁的表面修饰,也可在复合酞菁从处理用面1、2间排出后来实施。在该情况下,能够以上述的复合酞菁的表面处理为目的、将使用的物质在含有复合酞菁的流体从处理用面1、2间排出后加入到该排出液中,通过搅拌等的操作来进行复合酞菁的表面处理。另外,也能够在含有复合酞菁的流体被排出后、通过透析管等从该含有复合酞菁的流体将杂质去除后加入以表面处理为目的的物质来实施。另外,能够将从处理用面1、2间排出的含有复合酞菁的流体的液体成分进行干燥而形成复合酞菁粉体后来进行上述表面处理。具体而言,能够将得到的复合酞菁粉体分散于目标溶剂中、加入以上述的表面处理为目的的物质而施加搅拌等的处理来实施。作为复合酞菁的制造方法,例如,在使用如图1中所记载的那样的微反应器的情况下,由于可以使其微小流路的雷诺数自由地变化,因此能够做成粒径、粒子形状、晶型等、根据目的单分散性、再分散性好的复合酞菁。该情况下,可以在微反应器的2个圆盘间的强制薄膜中结束析出反应。而且,通过其的自排出性,即使在伴有析出的反应的情况下,也没有产物的堵塞,不需要大的压力。而且,可稳定的制作复合酞菁微粒,另外安全性优异,几乎没有杂质的混入,清洗性也好。进而根据目标的生产量可放大,因此可提供生产率高的复合酞菁的制造方法。另外,在本发明的制造方法中,具有使有机溶剂(第3溶剂)作用于上述工序(2)中得到的复合酞菁的工序(3)。另外,在本发明的复合酞菁微粒的制造方法中,优选上述有机溶剂为芳香族化合物系溶剂或杂环式化合物系溶剂。其中,例如可以列举出对于α型铜酞菁通常诱发·促进向更为稳定的β型结晶结构等的结晶转变的芳香族化合物系溶剂或杂环式化合物系溶剂。在本发明中,作为上述有机溶剂,例如可以列举出苯乙烯、二甲苯、甲苯、苯、甲酚、枯烯等的芳香族化合物系溶剂、四氢呋喃(thf)、吡啶等的杂环式化合物系溶剂、甲乙酮(mek)、丙酮等的酮系溶剂、乙二醇、丙二醇等的多元醇系溶剂等。其中,例如优选苯乙烯、二甲苯、甲苯、苯、甲酚、枯烯、thf。这些有机溶剂可单独地使用,另外也可将2种以上混合使用。另外,在上述工序(3)中,作为使上述有机溶剂作用于工序(2)中得到的复合酞菁的方法(也称为有机溶剂处理),能够适当地采用公知的手法,例如可以列举出将复合酞菁投入上述有机溶剂中的方法、将复合酞菁用上述有机溶剂清洗的方法、一边将复合酞菁在水中搅拌一边投入上述有机溶剂来进行混合的方法、一边搅拌上述有机溶剂一边将复合酞菁在粉体的状态或含水、有机溶剂的湿饼的状态下投入来进行混合的方法等。另外,也可通过只是接触、喷雾等操作来使上述有机溶剂作用于复合酞菁。另外,在上述工序(3)中,在使上述复合酞菁浸渍于上述有机溶剂中的情况下,上述复合酞菁的浓度例如可以为0.0005wt%以上且95wt%以下,也可以为1wt%以上且50wt%以下,还可以为10wt%以上且30wt%以下。应予说明,上述有机溶剂的浓度在将2种以上的上述有机溶剂混合使用的情况下是指其合计量的浓度。铜酞菁、氧钛酞菁、钴酞菁各个单独的酞菁在特定的有机溶剂中粒子(结晶)生长。即,如果使特定的有机溶剂作用于单独的酞菁,在作用前/作用后发现结晶生长、晶型的变化和与其相伴的光谱等的变化。此时,晶型与光谱形状一致。通过使这些单独的酞菁为复合酞菁,相互抑制各自的生长方向,且有可能形成新的状态,在复合酞菁的情况下,通过至少在各个酞菁的生长点(在粒子或结晶中,受到特定的有机溶剂的作用而生长的点)各个酞菁作用而抑制生长,显现出了目前为止尚未显现过的新的光谱特性等。应予说明,复合酞菁的形态并不清楚,但推测至少在各个酞菁的生长点能够作用的位置存在各个酞菁。作为这种情况的粒子的状态,也可考虑固溶体化了的情况,也可设想固溶体以外的情况。予以说明,对于上述工序(3),优选与上述工序(1)同样地使用上述的高速搅拌机进行。由此,可以使上述有机溶剂均一地作用于上述工序(2)中得到的酞菁微粒,因此使粒径、粒子形状或复合酞菁微粒中的组成均一成为可能。另一方面,在本发明的制造方法中能够使用微反应器。另外,在本发明的制造方法中,优选至少上述工序(2)使用微反应器进行。就本发明中所使用的微反应器而言,只要能够实施本发明,则能够适当地使用公知的装置。例如,在本发明的复合酞菁微粒的制造方法中,至少上述工序(2)使用使至少2种被处理流体反应的微反应器来进行,上述被处理流体中,至少1个被处理流体为上述溶解液,可以使另一被处理流体为上述第2溶剂。其中,在本发明中,优选上述微反应器在被处理流体的反应部位具有通过处理用面之间保持微小间隔且相对地进行移动而促进反应的机构。另外,在本发明的复合酞菁微粒的制造方法中,至少上述工序(2)使用下述的微反应器进行:将至少2种被处理流体导入可接近和分离地相互对置配设、至少一方相对于另一方相对地进行旋转的第1处理用面与第2处理用面之间,通过在第1处理用面与第2处理用面之间所赋予的导入压力产生在使第1处理用面与第2处理用面分离的方向上发挥作用的分离力,通过上述分离力,将第1处理用面与第2处理用面之间保持为微小的间隔、且使上述至少2种被处理流体在保持为上述微小的间隔的第1处理用面与第2处理用面之间合流,在上述第1处理用面与第2处理用面之间通过,由此形成薄膜流体,在上述薄膜流体中使被处理流体之间反应;在上述被处理流体中,至少1个被处理流体为上述溶解液,可以使另一被处理流体为上述第2溶剂。图1中所示的微反应器与专利文献5和专利文献6中记载的装置相同。上述公报的内容在不脱离本申请发明的主旨的范围内并入作为本申请发明的内容,根据需要能够适当地组合使用。以下对微反应器进行详述。上述微反应器具有对置的第1和第2的、2个处理用部10、20,第1处理用部10旋转。两处理用部10、20的对置的面分别成为处理用面。第1处理用部10具有第1处理用面1,第2处理用部20具有第2处理用面2。将两处理用面1、2分别连接至被处理流体的流路d1、d2,构成被处理流体的流路的一部分。将该两处理用面1、2间的间隔通常调节至1mm以下、例如0.1μm至50μm左右的微小间隔。由此,通过该两处理用面1、2间的被处理流体成为被两处理用面1、2强制了的强制薄膜流体。而且,该装置在处理用面1、2间进行使第1、第2被处理流体反应而进行微粒的析出的流体处理。更具体地说明,上述装置具有:保持上述的第1处理用部10的第1支架11、保持第2处理用部20的第2支架21、接面压赋予机构43、旋转驱动机构(未图示)、第1导入部d1、第2导入部d2、和流体压赋予机构p1、p2。在流体压赋予机构p1、p2中能够采用压缩机、其他的泵。在上述实施方式中,第1处理用部10、第2处理用部20为环状的圆盘。就第1、第2处理用部10、20的材质而言,除了金属以外,能够采用碳、陶瓷、烧结金属、耐磨损钢、蓝宝石,此外能够采用对金属实施了硬化处理的产物、对硬质材料进行了衬里、涂覆、镀敷等施工的产物。在上述实施方式中,对两处理用部10、20的相互对置的第1、第2的处理用面1、2进行镜面研磨,算术平均粗糙度为0.01~1.0μm。在上述实施方式中,将第2支架21固定于装置,在同样固定于装置的旋转驱动机构的旋转轴中安装的第1支架11旋转,被该第1支架11支承的第1处理用部10相对于第2处理用部20进行旋转。当然,也可使第2处理用部20旋转,还可以使两者旋转。另外,在本发明中,能够使上述旋转速度例如为350~3600rpm。在上述实施方式中,相对于第1处理用部10,第2处理用部20在旋转轴50的方向上接近·分离,因此在设置于第2支架21的收容部41中,将与第2处理用部20的处理用面2侧相反侧的部位可出没地收容。不过,可与其相反地第1处理用部10相对于第2处理用部20接近·分离,也可两处理用部10、20相互地接近·分离。上述收容部41为第2处理用部20的、将与处理用面2侧相反侧的部位收容的凹部,为形成为环状的沟槽。该收容部41具有可使与第2处理用部20的处理用面2侧相反侧的部位出没的足够的间隙,将第2处理用部20收容。接面压赋予机构是用于在第1处理用部10的第1处理用面1与第2处理用部20的第2处理用面2接近的方向上产生挤压力(以下称为接面压力)的机构。通过该接面压力与由流体压力产生的使两处理用面1、2间分离的力的均衡,将两处理用面1、2间的间隔保持为规定的微小间隔,同时产生具有nm单位乃至μm单位的微小的膜厚的薄膜流体。在上述实施方式中,接面压赋予机构通过利用设置于第2支架21的弹簧43对第2处理用部20向着第1处理用部10赋能,从而赋予接面压力。另外,将被流体压赋予机构p1加压了的第1被处理流体从第1导入部d1导入两处理用部10、20的内侧的空间。另一方面,将被流体压赋予机构p2加压了的第2被处理流体从第2导入部d2经由设置于第2处理用部20的内部的通路,从在第2处理用面形成的开口部d20导入两处理用部10、20的内侧的空间。在开口部d20中,第1被处理流体与第2被处理流体合流、混合时,发生氧化还原、析出、晶析。此时,混合的被处理流体成为被保持上述的微小的间隙的两处理用面1、2强制的薄膜流体,要向环状的两处理用面1、2的外侧移动。由于第1处理用部10进行旋转,因此被混合了的被处理流体不是从环状的两处理用面1、2的内侧向外侧直线地移动,而是在环状的半径方向上的移动矢量与周向上的移动矢量的合成矢量作用于被处理流体,从内侧向外侧以大致漩涡状移动。在此,如图2中所示那样,可在第1处理用部10的第1处理用面1,形成从第1处理用部10的中心侧向外侧、即在径向上延伸的沟状的凹部13。该凹部13的平面形状可以是使第1处理用面1上弯曲或者以漩涡状延伸的形状,虽然没有图示,但也可以为笔直地在外方向上延伸的形状、以l字状等屈曲或弯曲的形状、连续的形状、断续的形状、分支的形状。另外,该凹部13也可在第2处理用面2形成而实施,也可在第1和第2处理用面1、2两者形成而实施。通过形成这样的凹部13,能够获得微泵效应,具有能够将被处理流体抽吸到第1和第2处理用面1、2间的效果。优选上述凹部13的基端到达第1处理用部10的内周。上述凹部13的前端向着第1处理用部面1的外周面侧延伸,因此随着从基端向前端,其深度逐渐地减小。在该凹部13的前端与第1处理用面1的外周面之间设置有无凹部13的平坦面。上述的开口部d20优选设置于与第1处理用面1的平坦面对置的位置。由此可以在层流条件下进行多个被处理流体的混合和微粒的析出。另外,向两处理用部10、20的外侧排出的流体经由容器v,作为排出液收集在烧杯b中。在本申请发明的实施方式中,如后述那样,在排出液中含有复合酞菁微粒。予以说明,烧杯b并不特别地限定于烧杯,也可以是罐、金属桶,可以与过滤机等下一工序直接连接。予以说明,上述的被处理流体的种类及其流路的数目在图1的例中设为2个,但也可以为3个以上。另外,就各处理用部中设置的导入用的开口部而言,对其形状、大小、数目并无特别限制,可适当地改变而实施。另外,可在上述第1和第2处理用面间1、2的正前面或者进一步的上游侧设置导入用的开口部。在本发明中,只要能够在处理用面1、2间进行上述处理即可,也可以从第1导入部d1导入第2被处理流体,从第2导入部d2导入第1被处理流体。例如,各流体中的第1、第2这样的表示只不过具有为存在多个的流体的第n号这样的用于识别的含义,如上述那样也可存在第3以上的流体。在本发明的制造方法中,优选至少工序(2)使用微反应器进行,但也可以使用微反应器连续地进行工序(2)和工序(3)。具体地,如图1(b)中所示那样,在第1导入部d1、第2导入部d2以外在微反应器中设置第3导入部d3,例如从第1导入部d1将作为第1流体的溶解液,从第2导入部d2将作为第2流体的第2溶剂,从第3导入部d3将作为第3流体的有机溶剂各自分别地导入微反应器。这种情况下,通过将导入有机溶剂的第3导入部d3设置在第1导入部d1和第2导入部d2的下游侧,更详细地说,将第3导入部d3的开口部d30设置在第2导入部d2的开口部d20的下游侧,由此能够使在处理用面1、2间析出的复合酞菁微粒与有机溶剂作用。具备上述的3个开口部(d10、d20和d30)的微反应器适于连续地进行工序(2)和工序(3)的情况。不过,对本发明进行实施时,在微反应器中进行工序(2)、在微反应器外进行工序(2)以后的工序的情况下,如图1(a)中所示那样,具有至少2个开口部(d10、d20)就足以,但在对于在处理用面1、2间析出的复合酞菁微粒、在上述薄膜流体中实施表面处理的情况等下,并不妨碍在具有3个以上的开口部的微反应器中实施工序(2)。另外,本发明根据需要可对上述工序(2)中得到的复合酞菁进行清洗和/或溶剂置换。清洗和/或溶剂置换可以适当地使用公知的手法。并无特别限定,对于包含复合酞菁微粒的液体,可以通过过滤·离心分离·超过滤等的操作,通过选择与目的相符的溶剂,进行上述复合酞菁的清洗和/或溶剂置换。另一方面,在本发明中,微粒是指亚微米级(纳米级)的微小的结晶或结晶的集合体。对上述微粒的形状并无特别限定,例如可以是大致圆柱状、大致球状、大致圆盘状、大致三棱柱状、大致四棱柱状、大致多面体状、椭圆球状等的形态的粒体或其集合体等。另外,本发明的复合酞菁微粒是至少包含铜酞菁与氧钛酞菁和/或钴酞菁的复合酞菁微粒,其特征在于,长径比为1.1以上且2.5以下,粒径为5nm以上且100nm以下。例如,通过使用本发明的制造方法,能够得到最适合作为色料的、纳米级、优选地100nm级的复合酞菁微粒。上述长径比可以为1.0以上且5.0以下,也可以为1.1以上且2.5以下,还可以为1.5以上且2.0以下。另外,上述粒径可以为2~80nm,也可以为5~50nm,还可以为10~30nm。另一方面,如果是以往方法,由于向更为稳定的β型结晶结构等的结晶转变等,上述长径比、上述粒径变大,得到本发明这样的具有小的长径比、小的粒径的各微粒非常困难,也没有制造例。另外,本发明的复合酞菁微粒优选紫外可见吸收光谱的655~700nm中的峰顶的abs(a)与550~640nm中的峰顶的abs(b)的相对值([abs(a)]/[abs(b)])为0.8以上。例如,通过使用本发明的制造方法,能够得到抑制光的散射、特别是作为具有更为鲜明的青色的色料具有最适性质的复合酞菁微粒。另外,上述峰顶的abs(a)例如可以为紫外可见吸收光谱的660~700nm中的峰顶的abs,也可以是紫外可见吸收光谱的660~690nm中的峰顶的abs,还可以是紫外可见吸收光谱的650~690nm中的峰顶的abs。另外,上述峰顶的abs(b)例如可以为紫外可见吸收光谱的560~640nm中的峰顶的abs,也可以是紫外可见吸收光谱的550~650nm中的峰顶的abs,还可以是紫外可见吸收光谱的540~630nm中的峰顶的abs。另外,上述abs(a)与abs(b)的相对值([abs(a)]/[abs(b)])优选为0.8以上,例如,可以为1.0~4.0,也可以为1.2~3.5,还可以为1.4~3.0,还可以为1.6~2.5。通过上述相对值([abs(a)]/[abs(b)])成为1.0以上,上述复合酞菁微粒的发色的红色减少,更鲜明的青色的发色成为可能。另外,在本发明中,复合酞菁的晶型是指通过使用干燥粉体进行x射线衍射(xrd)测定而确定的晶型。另外,本发明中的复合酞菁微粒为青色或青系色,特别是与以往的铜-氧钛酞菁结晶等相比可发出更为鲜明的青色。另外,本发明中的复合酞菁由于成为特别是具有更为鲜明的青色等的色料,因此可在墨、喷射用墨、热转印用墨、调色剂、涂料(建筑·汽车等)、着色树脂、滤色器等的各种用途中利用。实施例以下对于具体地示出本发明的构成和效果的实施例等进行说明。应予说明,本发明并不限定于下述的实施例。在实施例中,在使用强制薄膜型微反应器的情况下,a液是指从图1(a)中所示的装置的第1导入部d1所导入的第1被处理流体,b液是指从相同装置的第2导入部d2所导入的第2被处理流体。予以说明,微反应器的运转条件为圆盘转速:1700rpm。另外,实施例中的h2so4表示浓硫酸,cupc表示铜酞菁,tiopc表示氧钛酞菁,copc表示钴酞菁,tioso4表示硫酸氧钛。另外,例如,cupc_tiopc表示铜-氧钛酞菁。[实施例1](工序1、2)作为强制薄膜型微反应器,使用ulreass-11(エム·テクニック制造),在下述制作条件1下制造了铜-氧钛酞菁微粒。首先,在浓硫酸中使作为原料的铜酞菁和氧钛酞菁混合·溶解而制备溶解液(工序1),使用ulreass-11将该溶解液和对于原料成为不良溶剂的溶剂(纯水)混合而使复合酞菁微粒析出。将包含复合酞菁微粒的排出液从处理用面1、2间排出(工序2)。(制作条件1)a液:纯水b液:2.1wt%cupc/0.9wt%tiopc/97wt%(98wt%浓硫酸)cupc/tiopc=70/30=2.33(重量比)b液制备:クレアミックス(clm-2.2sエム·テクニック制造)转速:20000rpm制备时间:30min制备温度:30℃(制备量:470g=300cc)ulreass-11的a/b液流量:400/30ml/mina/b液送液温度:25/25℃圆盘转速:1700rpm。(清洗和溶剂置换)接着,作为后工序,将排出液过滤、将复合酞菁微粒回收。将得到的复合酞菁微粒的湿饼投入到纯水中,使用クレアミックス以5000rpm处理10分钟,清洗。将得到的复合酞菁微粒的浆料再次过滤,将复合酞菁微粒清洗。进行了3次上述清洗的操作。然后,将得到的复合酞菁的水的湿饼投入到乙醇中,使用クレアミックス以5000rpm处理10分钟,使复合酞菁在乙醇中分散。将得到的复合酞菁微粒的以乙醇作为分散介质的浆料再次过滤,进行复合酞菁微粒的溶剂置换。进行了3次上述溶剂置换的操作。(工序3)接着,对于得到的复合酞菁的乙醇的湿饼,使用苯乙烯进行与溶剂置换同样的处理(苯乙烯处理),使苯乙烯作用于复合酞菁微粒,最终得到了苯乙烯的湿饼。由得到的苯乙烯的湿饼制作干燥粉体。在实施例2~4中也进行了与实施例1同样的溶剂置换、苯乙烯处理(各有机溶剂处理)。另外,将得到的苯乙烯的湿饼的一部分用苯乙烯稀释而进行分散处理,制作了分散液。另外,实施例1中得到的复合酞菁微粒的粒径为24.6nm,长径比为1.31。应予说明,粒径由通过透射电子显微镜(tem)观察对于100个粒子测定粒径的结果的平均值来求出,长径比由通过透射电子显微镜(tem)观察对于100个粒子测定长径和短径的结果的平均值来求出。予以说明,tem观察中使用透射型电子显微镜、jem-2100(jeol制造)。作为观察条件,使加速电压为80kv,使观察倍率为10000倍和50000倍。将上述的分散液滴至火棉胶膜,使用在室温下干燥了的tem观察用试样,进行了tem观察。另外,将实施例1和相对于实施例1的以下3个比较例中的吸收光谱测定结果示于图3,将透射光谱测定结果示于图5。将上述的分散液作为吸收·透射光谱的测定试样,测定了吸收·透射光谱。应予说明,吸收·透射光谱是使用岛津制作所制造的紫外可见分光光度计(uv-2540)测定300nm~800nm的波长区域。应予说明,比较例1-1为本实施例1的b液中使用的cupc的原料,是晶型为β型的铜酞菁。比较例1-2为实施例1的工序3中使苯乙烯作用前的铜-氧钛酞菁微粒。比较例1-3为替代实施例1的氧钛酞菁而使用硫酸氧钛制作的酞菁微粒。由上述比较例1-1~1-3得到的微粒的粒径分别为116.4nm、14.8nm、976.9nm,长径比分别为4.52、1.03、5.99。进而,苯乙烯处理后的粒径(实施例1的粒径)对于苯乙烯处理前的粒径(比较例1-2的粒径)的比率为1.66,通过上述苯乙烯处理能够抑制粒子(结晶)的生长。由图3可知,在实施例1中得到的铜-氧钛酞菁微粒中,将673nm附近的峰顶的值设为abs(a)、将605nm附近的峰顶的值设为abs(b)时,abs(a)与abs(b)的相对值([abs(a)]/[abs(b)])为2.74。这表示实施例1中得到的铜-氧钛酞菁微粒的波长660nm~700nm附近的红色光的吸收能力优异。但是,在比较例1-2或者使用了tioso4的比较例1-3中,没有得到如实施例1那样的光谱形状,特别地,比较例1-3由于苯乙烯的处理而粗大化,停留在显示出与晶型为β型的cupc(比较例1-1)接近的吸收光谱形状。另外,由图5可知,实施例1中得到的铜-氧钛酞菁微粒的400~550nm附近的透射区域的峰顶与比较例1-2相比,向长波长侧迁移,因此从以往的铜-氧钛酞菁微粒(比较例1-2)中将紫色成分去除,进而由图3可知,实施例1中得到的铜-氧钛酞菁微粒在600~720nm的波长区域中显示出吸收,因此从以往的铜-氧钛酞菁微粒中将红色成分去除。因此,实施例1与以往的铜-氧钛酞菁微粒相比,发出鲜明的青色。而使用了tioso4的比较例1-3中,由图3可知,虽然在600~720nm的波长区域中显示出吸收,但由图5可知,400~550nm附近的透射区域的峰顶与比较例1-2相比,向长波长侧过度迁移,认为绿色调过强。另外,使用实施例1中得到的干燥粉体进行了透射电子显微镜(tem)观察。图7、8分别表示实施例1中的、分别采用50000倍、10000倍的透射电子显微镜(tem)观察照片。另外,图9、10表示实施例1的工序3中使苯乙烯作用前的铜-氧钛酞菁微粒(比较例1-2)的分别采用50000倍、10000倍的透射电子显微镜(tem)观察照片。另外,使用实施例1中得到的干燥粉体进行了x射线衍射(xrd)测定。将其结果示于图13的下段。另外,在图13的上段示出了本实施例的b液中使用的cupc的原料即β型cupc(比较例1-1)的xrd测定结果,在图13的中段示出了实施例1的工序3中的使苯乙烯作用前的铜-氧钛酞菁微粒(比较例1-2)的xrd测定结果。应予说明,在xrd测定中,使用了粉末x射线衍射测定装置(制品名:x‘pertprompd、panalytical制造)。测定条件为测定范围:6~60°、cu对阴极、管电压45kv、管电流40ma、扫描速度16°/min。由图13的结果能够确认:尽管使通常使α型cupc结晶转变为β型的苯乙烯进行作用,实施例1的铜-氧钛酞菁微粒与比较例1-2相比,晶型本身也没有大的变化。[实施例2]将上述实施例1中的、cu/ti=70/30=2.33(重量比)替换为cu/ti=85/15=5.67(重量比),此外在与实施例1相同的制作条件1下制造了铜-氧钛酞菁微粒。实施例2中得到的铜-氧钛酞菁微粒的粒径为43.1nm,长径比为1.84。另外,将实施例1、2中的吸收光谱测定结果示于图4中,将透射光谱测定结果示于图6中。由图4可知,在实施例2中得到的铜-氧钛酞菁微粒中,将673nm附近的峰顶的值设为abs(a)、将605nm附近的峰顶的值设为abs(b)时,abs(a)与abs(b)的相对值([abs(a)]/[abs(b)])为1.89。[比较例2]作为比较例2,用与实施例2同样的方法制作上述实施例2中的、代替氧钛酞菁而使用了无金属酞菁(以下记载为h2pc)的颜料微粒,测定了吸收光谱、透射光谱以及粒径。由比较例2得到的微粒的粒径为634.9nm,长径比为5.12。图19中示出实施例2和比较例2的吸收光谱的测定结果。另外,同样地,在图20中示出实施例2和比较例2的透射光谱的测定结果。予以说明,实施例2、比较例2都为了参考,关于实施工序3中的苯乙烯处理前的微粒的吸收·透射光谱的测定结果以及比较例1-1中的吸收·透射光谱,也示于图19或图20中。另外,在比较例2中,655~700nm中的峰顶的abs(a)与550~640nm中的峰顶的abs(b)的相对值([abs(a)]/[abs(b)])不到0.8。如由这些结果判断那样,认为:在利用h2pc的比较例2中,虽然在600~720nm的波长区域中显示出吸收,但400~550nm附近的透射区域的峰顶与实施例1、2相比,向长波长侧迁移,绿色调强。即,可知实施例1、2的铜-氧钛酞菁微粒发挥不仅与铜-氧钛酞菁微粒相比而且与无金属酞菁相比也优异的特性。[实施例3-1~3-5](工序1、2)在实施例3-1~3-5中,在以下所示的制作条件3下将a液和各b液制备、混合,采用不良溶剂晶析方法,使包含cupc和copc的复合酞菁微粒或者包含cupc、copc和tiopc的复合酞菁微粒析出。在实施例3-1~3-5中,与实施例1、2不同,没有使用微反应器,将反应容器变为烧杯,在以下的制作条件3下使复合酞菁颜料微粒析出。(制作条件3)a液:纯水b液:作为实施例3-1~3-5的各实施例,使用了按照下述比率将cupc、copc、tiopc溶解于浓硫酸的溶液、b1~b5。[实施例3-1]b1:cupc/copc/98%h2so4=2.1/0.9/97wt%(cupc/copc=70/30=2.33:重量比)[实施例3-2]b2:cupc/tiopc/copc/98%h2so4=1.95/0.9/0.15/97wt%(cupc/tiopc/copc=65/30/5:重量比(cupc/tiopc=2.17、cupc/copc=13.00))[实施例3-3]b3:cupc/tiopc/copc/98%h2so4=1.8/0.9/0.3/97wt%(cupc/tiopc/copc=60/30/10:重量比(cupc/tiopc=2.00、cupc/copc=6.00))[实施例3-4]b4:cupc/tiopc/copc/98%h2so4=1.95/0.75/0.3/97wt%(cupc/tiopc/copc=65/25/10:重量比(cupc/tiopc=2.60、cupc/copc=6.50))[实施例3-5]b5:cupc/tiopc/copc/98%h2so4=1.8/0.6/0.6/97wt%。(cupc/tiopc/copc=60/20/20:重量比(cupc/tiopc=3.00、cupc/copc=3.00))b液制备:在实施例3-1~3-5中,都如下所述制备b液。クレアミックス(clm-2.2sエム·テクニック制造)转速:20000rpm制备时间:30min制备温度:30℃(制备量:470g=300cc)混合·微粒的析出:一边搅拌烧杯内的a液100ml,一边滴加上述的b液30ml,使复合酞菁微粒析出。(工序3)实施例3-1~3-5均为:作为后工序,过滤将上述a液与b液混合了的混合液,使用クレアミックス用纯水将得到的复合酞菁微粒清洗3次。从得到的水的湿饼用乙醇将溶剂置换后,使用苯乙烯进行同样的处理(苯乙烯处理),使苯乙烯作用于复合酞菁微粒,最终得到苯乙烯的湿饼。由得到的苯乙烯的湿饼制作了干燥粉体。另外,将得到的苯乙烯的湿饼的一部分用苯乙烯稀释,进行分散处理,制作了分散液。tem观察、xrd测定、吸收·透射光谱的各测定试样的制作以及测定方法与实施例1同样。实施例3-1~3-5中得到的复合酞菁微粒的粒径分别为86.4nm、79.4nm、87.1nm、93.1nm、63.1nm,长径比分别为2.42、2.41、2.13、1.48、1.69。将实施例3-1~3-5的吸收光谱测定结果示于图11,将透射光谱测定结果示于图12。与实施例1的情况同样地,作为相对于实施例3-1~3-5的比较例,对于各实施例的工序3中的使苯乙烯作用前的复合酞菁微粒,作为比较例3-1~3-5在图11、12中一并示出。予以说明,比较例3-1~3-5中得到的复合酞菁微粒的粒径分别为63.1nm、69.3nm、61.0nm、72.3nm、59.9nm,长径比分别为1.24、1.12、1.86、2.21、1.54。由图11、图12可知,对于用虚线表示的实施例3-1~3-5,示出了与上述的实施例1、2同样的优选的光谱形状。另外,对于实施例3-1~3-5,655~700nm中的峰顶的abs(a)与550~640nm中的峰顶的abs(b)的相对值([abs(a)]/[abs(b)])分别为1.45、1.51、1.51、1.51、1.46,对于比较例3-1~3-5,655~700nm中的峰顶的abs(a)与550~640nm中的峰顶的abs(b)的相对值([abs(a)]/[abs(b)])全部不到0.8。进而,苯乙烯处理后的粒径(实施例3-1~3-5的粒径)对于苯乙烯处理前的粒径(比较例3-1~3-5的粒径)的比率分别为1.37、1.15、1.43、1.29、1.05,通过苯乙烯处理能够抑制粒子(结晶)的生长。接着,使用比较例3-1~3-5、实施例3-1~3-5中得到的干燥粉体,与实施例1同样地进行x射线衍射(xrd)测定,将其结果示于图14(比较例3-1~3-5)和图15(实施例3-1~3-5)中。由图14和图15的结果能够确认:即使使通常使α型cupc结晶转变为β型的苯乙烯进行作用,但实施例3-1~3-5的复合酞菁微粒与比较例3-1~3-5相比,晶型本身也没有大的变化。由以上的结果,首先由实施例3-1的结果可理解:对于铜-钴酞菁,也获得与实施例1、2的铜-氧钛酞菁同样的效果。另外,由实施例3-2~3-5的结果可理解:对于使铜酞菁和氧钛酞菁以及钴酞菁这3种复合了的酞菁,也获得与上述铜-氧钛酞菁或铜-钴酞菁同样的效果。[实施例3-1-1~3-1-3]对于对上述实施例3-1中得到的铜-钴酞菁微粒使苯乙烯以外的有机溶剂作用了的情况示出。除了将实施例3-1的苯乙烯变为以下所述的有机溶剂以外,采用与实施例3-1同样的方法制作复合酞菁微粒,测定了吸收光谱。将用二甲苯处理了的例子作为实施例3-1-1,将用thf处理了的例子作为实施例3-1-2,将用甲苯处理了的例子作为实施例3-1-3,将结果示于图16中。予以说明,为了参考,在图16中也示出了实施例3-1和比较例3-1的吸收光谱测定结果。根据其结果,可理解无论有机溶剂的种类如何,都实现了本发明的效果。[实施例3-2-1~3-2-2]对于对上述实施例3-2中得到的铜-氧钛-钴酞菁微粒使苯乙烯以外的有机溶剂作用了的情况示出。除了将实施例3-2的苯乙烯变为以下所述的有机溶剂以外,用与实施例3-2同样的方法制作复合酞菁微粒,测定了吸收光谱。将用二甲苯处理了的例子作为实施例3-2-1,将用thf处理了的例子作为实施例3-2-2,将结果示于图17中。予以说明,为了参考,也示出了实施例3-2和比较例3-2的吸收光谱测定结果。根据其结果,可理解无论有机溶剂的种类如何,都发挥了本发明的效果。[实施例3-3-1]对于对上述实施例3-3中得到的铜-氧钛-钴酞菁微粒使苯乙烯以外的有机溶剂作用了的情况示出。予以说明,为了参考,也示出了实施例3-3和比较例3-3的吸收光谱测定结果。根据其结果,可理解无论有机溶剂的种类如何,都发挥了本发明的效果。除了将实施例3-3的苯乙烯变为甲苯以外,用与实施例3-3同样的方法制作复合酞菁微粒(实施例3-3-1),测定了吸收光谱。将结果示于图18中。将实施例3-1-1~实施例3-3-1的各实施例中的、粒径、长径比、655~700nm中的峰顶的abs(a)与550~640nm中的峰顶的abs(b)的相对值([abs(a)]/[abs(b)])示于表1中。[表1]实施例粒径[nm]长径比[abs(a)]/[abs(b)]3-1-112.41.561.493-1-225.11.251.843-1-331.42.131.323-2-143.71.991.973-2-233.31.251.973-3-145.92.121.22[实施例4-1-1~4-1-4、4-2-1~4-2-4](工序1、2)与实施例1、2同样地,使用ulreass-11(エム·テクニック制造)作为强制薄膜型微反应器,在下述制作条件4下制造了铜-氧钛-钴酞菁微粒。首先,在浓硫酸中使铜酞菁、氧钛酞菁和钴酞菁混合·溶解,制备溶解液,使用ulreass-11将该溶解液与对于原料成为不良溶剂的溶剂(纯水)混合,使复合酞菁析出。使包含复合酞菁微粒的排出液从处理用面1、2间排出。(制作条件4)a液:纯水b液:按照下述b6、b7的比率将cupc、copc和tiopc溶解于浓硫酸而成的液体。[实施例4-1-1~4-1-4]b6:cupc/tiopc/copc/98%h2so4=1.8/0.9/0.3/97wt%(cupc/tiopc/copc=60/30/10:重量比(cupc/tiopc=2.00、cupc/copc=6.00))[实施例4-2-1~4-2-4]b7:cupc/tiopc/copc/98%h2so4=1.8/0.6/0.6/97wt%。(cupc/tiopc/copc=60/20/20:重量比(cupc/tiopc=3.00、cupc/copc=3.00))b液制备:在实施例4-1-1~4-1-4和实施例4-2-1~4-2-4中,都是如下所述制备了b液。クレアミックス(clm-2.2sエム·テクニック制造)转速:20000rpm制备时间:30min制备温度:30℃(制备量:470g=300cc)ulreass-11的a/b液流量:600/30ml/mina/b液送液温度:10/25℃、圆盘转速:1700rpm。(工序3)接着,与实施例1、2同样地,作为后工序,将排出液过滤,将复合酞菁微粒回收。使用クレアミックス用纯水将得到的复合酞菁微粒清洗4次。从得到的水的湿饼用乙醇将溶剂置换后,使用苯乙烯实施了同样的处理(苯乙烯处理)(实施例4-1-1、4-2-1)。另外,代替苯乙烯处理而使用二甲苯(实施例4-1-2、4-2-2)、甲苯(实施例4-1-3、4-2-3)、以及thf(实施例4-1-4、4-2-4)进行同样的处理,使各个有机溶剂作用于复合酞菁微粒,最终得到了各个有机溶剂的湿饼。由得到的湿饼制作了干燥粉体。另外,将得到的各个有机溶剂的湿饼的一部分用最终置换了的有机溶剂稀释,进行分散处理,制作了分散液。tem观察、xrd测定、吸收·透射光谱的各测定试样的制作以及测定方法与实施例1同样。将实施例4-1-1~4-1-4的吸收光谱测定结果示于图21中,将实施例4-2-1~4-2-4的吸收光谱测定结果示于图22中。予以说明,在图21中,作为实施例4-1-1~4-1-4的比较例,示出了各实施例的工序3中的使苯乙烯、二甲苯、甲苯或thf作用前的复合酞菁微粒(比较例4-1)的吸收光谱测定结果。同样地,在图22中,作为实施例4-2-1~4-2-4的比较例,示出了使苯乙烯、二甲苯、甲苯或thf作用前的复合酞菁微粒(比较例4-2)的吸收光谱测定结果。以上的实施例和比较例中得到的复合酞菁微粒的粒径为比较例4-1:11.4nm、实施例4-1-1:14.6nm、实施例4-1-2:23.5nm、实施例4-1-3:22.9nm、实施例4-1-4:56.4nm,长径比分别为1.19、2.11、1.45、1.54、1.78。另外,为比较例4-2:9.5nm、实施例4-2-1:13.1nm、实施例4-2-2:13.6nm、实施例4-2-3:15.4nm、实施例4-2-4:7.4nm,长径比为1.01、1.33、1.29、2.14、2.46。进而,有机溶剂处理后的粒径(实施例4-1-1~4-1-4的粒径)对于有机溶剂处理前的粒径(比较例4-1的粒径)的比率分别为1.32、3.21、2.42、1.11,有机溶剂处理后的粒径(实施例4-2-1~4-2-4的粒径)对于有机溶剂处理前的粒径(比较例4-2的粒径)的比率分别为1.38、1.43、1.62、0.78。通过有机溶剂处理能够抑制粒子(结晶)的生长。由图21,对于实施例4-1-1~4-1-4,示出了与上述的实施例1、2同样的优选的光谱形状。另外,对于实施例4-1-1~4-1-4,655~700nm中的峰顶的abs(a)与550~640nm中的峰顶的abs(b)的相对值([abs(a)]/[abs(b)])分别为1.97、1.36、1.07、1.72,对于比较例4-1,655~700nm中的峰顶的abs(a)与550~640nm中的峰顶的abs(b)的相对值([abs(a)]/[abs(b)])为0.51。由图22可知,对于实施例4-2-1~4-2-4,示出了与上述的实施例1、2同样的优选的光谱形状。另外,对于实施例4-2-1~4-2-4,655~700nm中的峰顶的abs(a)与550~640nm中的峰顶的abs(b)的相对值([abs(a)]/[abs(b)])分别为1.83、1.24、0.91、2.62,对于比较例4-1,655~700nm中的峰顶的abs(a)与550~640nm中的峰顶的abs(b)的相对值([abs(a)]/[abs(b)])为0.52。由以上的结果示出:关于使铜酞菁和氧钛酞菁以及钴酞菁这3种复合的铜-氧钛-钴酞菁,也实现本发明的效果。接着,对实施例5~8进行说明。应予说明,实施例5~8的xrd测定条件与实施例1相同。另外,在tem观察中,与实施例1同样地使用了透射型电子显微镜、jem-2100(jeol公司制造)。作为观察条件,使加速电压为80kv,使观察倍率为25000倍。另外,在图23中示出了实施例5~8中的实验程序例。[实施例5、6]使用微反应器将a液和b液在以下的条件下混合,通过图23中所示的程序制造了复合酞菁微粒。应予说明,在实施例5(在后述的表4中所示的实施例5-1~5-6)、实施例6(在后述的表4中所示的实施例6-1~6-6)中,作为微反应器,使用了ulreass-11(エム·テクニック制造)。这种情况下,a液相当于从图1(a)中所示的微反应器的第1导入部d1所导入的第1被处理流体,b液相当于同样从第2导入部d2所导的第2被处理流体。第1导入部d1、第2导入部d2的替换是任意的。将实施例5、6中的实验配方示于表2中。[表2]图23中所示的、实施例5、6中的处理内容如下所述。(工序0)(a液·b液制备)按照上述实验配方使用ulreass-11实施混合·析出时,如以下所述制备了a液和b液。有机颜料粒子析出溶剂(a液)制备条件:如上述实验配方中记载那样单一溶剂的情况下,不需要制备,例如应用日本特开2009-82902号公报中记载的实验配方的情况下,优选使用クレアミックス进行搅拌。例如,在本实施例中使用clm-2.2s以10000rpm搅拌30分钟。有机颜料粒子的原料溶液(b液)制备条件:使用クレアミックスclm-2.2s以20000rpm进行了30分钟搅拌。另外,a液、b液都是使制备温度为40℃。(工序1)(混合·析出)在表3中所示的运转条件下使用ulreass-11,将有机颜料粒子析出溶剂(a液)与有机颜料粒子的原料溶液(b液)混合,使复合酞菁微粒析出。[表3](工序2)(清洗)将工序1中得到的包含复合酞菁微粒的浆料过滤,使用纯水将复合酞菁微粒清洗,得到了复合酞菁微粒的湿饼(或者通过真空干燥法等干燥处理得到了复合酞菁微粒的干燥粉体)。(工序3)(作用)将工序2中得到的复合酞菁微粒的湿饼(或干燥粉体)投入到在有机溶剂(以下的表4中简单地记载为溶剂)中添加了表面活性剂和/或分散剂的溶液中,投入后,使用クレアミックス进行了一定时间的搅拌处理。予以说明,将实施例5-1~5-6、实施例6-1~6-6中使用的有机溶剂与表面活性剂和/或分散剂示于以下的表4中。对于使用了微反应器时的搅拌处理前后的复合酞菁微粒的粒径的变化与结晶度变化,示于以下的表4中。[表4]予以说明,关于表2~表4中的缩写、用语的定义,示于表5中。[表5]表4和后述的表7中的、评价结果◎、○、△的定义如下所述。“◎”是如下的情况:设为da:工序3的作用后的粒子的平均一次粒径,db:工序2的清洗后的平均一次粒径时,da/db为1.0~4.0的范围,并且设为xa:工序3的作用后的粒子的结晶度,xb:工序2的清洗后的粒子的结晶度时,xa/xb为1.05以上,并且da为80nm以下,并且从微粒的均一性的观点出发,以25000倍进行了3视野的tem观察时,工序3的作用后的各个青色颜料微粒中完全没有确认有db超过8.0倍的粒子。“○”是如下的情况:da/db为1.0~4.0的范围,并且xa/xb为1.05以上,并且da比80nm大,并且从微粒的均一性的观点出发,以25000倍进行了3视野的tem观察时,工序3的作用后的各个青色颜料微粒中完全没有确认有db超过8.0倍的粒子。“△”是如下的情况:da/db为1.0~4.0的范围,并且xa/xb为1.05以上,并且从微粒的均一性的观点出发,以25000倍进行了3视野的tem观察时,工序3的作用后的各个青色颜料微粒中确认有最大1个db超过8.0倍的粒子。对于工序2(清洗)后和工序3(作用)后的复合酞菁微粒分别通过tem观察算出平均一次粒径,通过xrd测定对结晶度进行了测定比较(表4)。另外,示出了上述实施例中得到的tem图像(图24~图27)。根据上述各实施例可知,通过使添加了表面活性剂或分散剂的有机溶剂作用于析出了的复合酞菁(工序3),能够抑制颈缩、生长。[实施例7、8]采用间歇方式在以下的条件下将a液和b液混合,通过图23中所示的下述程序制造了复合酞菁微粒。将实施例7(后述的表7中所示的实施例7-1~7-6)、实施例8(后述的表7中所示的实施例8-1~8-6)中的实验配方示于表6中。[表6]实施例7、8中的处理内容如下所述。(工序0)(a液·b液制备)按照上述实验配方使用间歇方式实施混合·析出时,如以下所述制备了a液和b液。有机颜料粒子析出溶剂(a液)制备条件:如实验配方中记载那样单一溶剂的情况下,不需要制备,例如应用日本特开2009-82902号公报中记载的实验配方的情况下,优选使用クレアミックス进行搅拌。例如,在本实施例中使用clm-2.2s以10000rpm搅拌30分钟。有机颜料粒子的原料溶液(b液)制备条件:使用クレアミックスclm-2.2s以20000rpm进行了30分钟搅拌。另外,a液、b液都是使制备温度为40℃。(工序1)(混合·析出)通过使用磁力搅拌器和搅拌子以300rpm对烧杯内的有机颜料粒子析出溶剂(a液)进行搅拌,同时投入有机颜料粒子的原料溶液(b液),从而将a液和b液混合,使复合酞菁微粒析出。(工序2)(清洗)将工序1中得到的包含复合酞菁微粒的浆料过滤,使用纯水将复合酞菁微粒清洗,得到了复合酞菁微粒的湿饼(或者通过真空干燥法等干燥处理得到了复合酞菁微粒的干燥粉体)。(工序3)(作用)与实施例5、6同样地将工序2中得到的复合酞菁微粒的湿饼(或干燥粉体)投入到在有机溶剂(以下的表7中简单地记载为溶剂)中添加了表面活性剂和/或分散剂的溶液中,投入后,使用クレアミックス进行一定时间的搅拌处理。予以说明,将实施例7-1~7-6、实施例8-1~8-6中使用的有机溶剂和表面活性剂和/或分散剂示于以下的表7中。对于用间歇方式的搅拌处理前后的复合酞菁微粒的粒径的变化和结晶度变化,也一并示于以下的表7中。[表7]对于工序2(清洗)后和工序3(作用)后的复合酞菁微粒分别通过tem观察算出平均一次粒径,通过xrd测定对结晶度进行了测定比较(表7)。符号、缩写等的含义与上述实施例5、6相同。根据上述的实施例7、8,可知与使用了上述微反应器的情况的实施例5、6同样地,即使在间歇式的情况下,也能够通过使添加了表面活性剂或分散剂的有机溶剂作用于析出了的复合酞菁(工序3)而抑制颈缩、生长。予以说明,在使用了微反应器的情况下,间歇方式的情况下,在所有的实施例中,关于工序0的a液·b液制备,都可考虑各种方法。即使没有使用クレアミックス而是使用超声波式的均化器、超声波清洗机等或者磁力搅拌器和搅拌子,也能够实施。也可以如上述实施例那样只制备a液·b液一者,或者a液·b液都省略工序0。另外,除了作为a液、b液例示的实例以外,能够应用日本特开2009-82902号公报中记载的例子等公知的混合、析出的例子。进而,可替代本实施例中的工序3的搅拌处理而是没有进行搅拌地进行只是单纯地使其混合的处理,也可以是接触、喷雾。符号的说明1第1处理用面2第2处理用面10第1处理用部11第1支架20第2处理用部21第2支架d1第1导入部d2第2导入部d20开口部当前第1页12