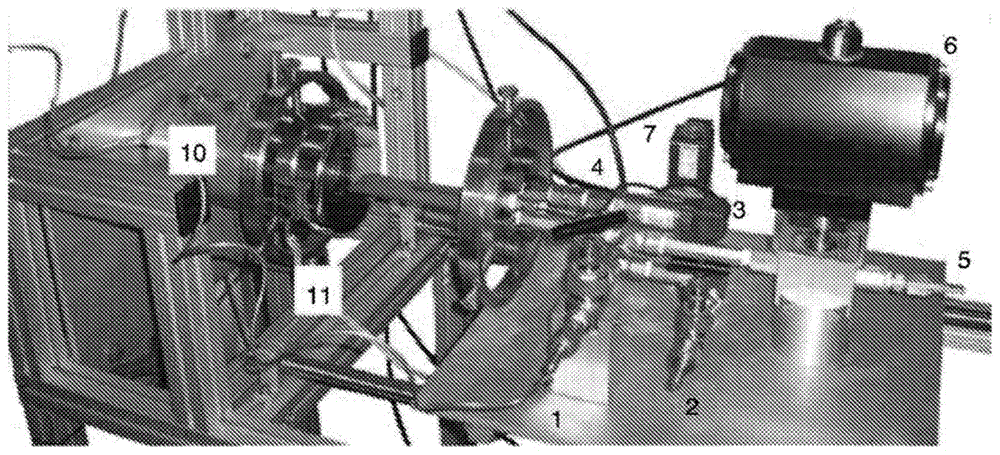
本发明涉及用于制备在泡孔形态方面和在密度方面的层状发泡聚合物材料的方法。特别地,该方法使用随后的发泡所必需的以随时间可变的条件为特征的用于物理发泡剂增溶的工序。更具体地,增溶步骤的随时间可变的条件产生物理发泡剂在聚合物中的浓度的非均匀分布,这在发泡后产生相应的非均匀形态和密度。
背景技术:
:最近,人们对“梯度”发泡材料产生兴趣,相对于以在泡孔密度和/或形态方面的均匀结构为特征的发泡材料,所述“梯度”发泡材料的结构和功能特性得以改善。通过最近的科学研究(理论数值和实验两者)都已证明这一点。专利文献描述了这样的层状发泡结构或具有梯度形态和/或密度的那些的用途和优点。专利申请第us2015125663号的公开描述了以“梯度”方式组装的不同层的聚合物泡沫在吸收来自头盔中的撞击的能量中的用途。其中层状泡沫是感兴趣的另一个领域是用于烧结的膨胀的领域(也称为蒸汽室模塑或珠粒发泡),这在烧结的发泡聚苯乙烯产品的生产中非常普遍,但最近,除了别的以外还使用聚丙烯、热塑性聚氨酯和聚乳酸。在该领域中,使用预发泡珠粒(形状几乎是球形并且尺寸接近毫米),在产品的制造中,将其插入模具中并用水蒸气或热气覆盖,以实现珠粒的最终发泡和烧结。最终发泡主要是由于发泡剂,例如戊烷,所述发泡剂仍然包含在预发泡珠粒中并随着加热而放出。实际上,在预发泡和最终发泡之间的期间防止通过扩散引起的发泡剂损失的可能性具有重大的技术重要性。当产品必须用已经经历不同保存期(储放)的珠粒生产时,这种由扩散现象引起的损失在预发泡珠粒的保存和过程标准化问题方面是一个限制。使具有径向层状形态的预发泡珠粒,例如具有用作防止内层中的发泡剂损失的屏障的致密的中间层或外层,将解决上述问题。一些商业产品,例如高尔夫球或运动撞击防护装置,是具有一个或更多个发泡层的层状产品(参见,例如,sullivan等,us2015/0283432和donzis,us4486901)。然而,适于产生这样的分层结构的技术似乎是人工的、长时间的和/或难以工业化的。例如,nikhilgupta等在“comparisonofcompressivepropertiesoflayeredsyntacticfoamshavinggradientinmicroballoonvolumefractionandwallthickness”mater.sci.enga427(2006)331-342中描述了一种实验室策略,其涉及在聚合物中放置具有不同尺寸的中空玻璃微球。在欧洲专利申请ep1452191a2和ep1878450a1中,描述了通过使用复合材料来产生层状结构的工序。特别地,在ep1452191a2中,使用两种聚合物材料的混合物,其中浓度梯度从主要由第一材料构成的步骤到主要由第二组分构成的步骤变化,在ep1878450a1中,复合材料预制件是使用填料和/或纤维与可发泡聚合物材料一起在模具中的精确定位制造的。这些工序既需要使用复合材料,也需要这些材料的组分的复杂的制备和分配。更频繁地描述并使用通过粘合或焊接来结合具有不同形态和/或密度的几个泡沫层,如在wo2016102291a1、wo2014041516a1和tw200918316中以及由erhengwang等在theblastresistanceofsandwichcompositeswithstepwisegradedcores”internationaljournalofsolidsandstructures46(2009)3492-3502中所描述的。除了结合工序的费力以外,还应注意的是,这些结合工序,尤其在通过粘合或热焊接执行时,在接合处具有不连续性,这在性能和设计方面是个问题。zhouc.等在“fabricationoffunctionallygradedporouspolymerviasupercriticalco2foaming",composites:partb42(2011)318-325中介绍了另一种方法,并考虑使用“发泡剂浓度的非平衡分布”。在该方法中,待发泡的材料已经通过增溶步骤被发泡剂部分饱和,该增溶步骤在恒定的温度和压力下随时间进行,比实现均匀浓度的发泡剂所需的时间更短。在这种情况下,待发泡的样品的最远的部分(相对于在压力下与发泡剂接触的自由表面,因此是最里面的部分)相对于邻近所述表面的部分(更外部的部分)含有较低浓度的发泡剂,其中发泡剂的浓度容易随着发泡剂的外部压力达到平衡条件。因此,样品的内部部分将较少发泡或缺乏泡沫,而外部部分将完全发泡。这样的结构的设计以发泡剂在聚合物中的扩散系数的知识、可用于大量的聚合物/发泡剂系统为前提。尽管描述的过程易于制造,但其是相当有限的,因为它仅允许构造以样品内部的发泡层较少,而外部的发泡层较多为特征的单梯度发泡材料。梯度的对称性明显取决于样品形状以及发泡剂可以进入哪些样品表面。技术实现要素:本发明的方法旨在克服本领域已知方法的缺点。特别地,申请人已经观察到,用本发明的方法,可以用简单、低成本的方法获得层状发泡结构。而且,申请人已经观察到,用本发明的方法获得的层状发泡结构在层之间的界面处不呈现出不连续性,而是相反地显示出发泡材料中存在的泡沫的密度和形态二者的逐渐变化。申请人还观察到,本发明的方法使得可以获得在层数及其形态和密度方面均具有广泛的设计选择的层状发泡结构。申请人观察到,这些和其他优点可以通过用于制备层状发泡材料的方法来获得,该方法包括在发泡之前的增溶步骤中使用至少一种随时间可变的条件的发泡剂在聚合物中的非平衡质量传输的至少一个步骤。申请人观察到,在一种或更多种发泡剂在聚合物中的增溶步骤中使用一种或更多种随时间可变的条件产生发泡剂在相同聚合物中的浓度的非均匀分布,这在发泡后相应地产生非均匀的形态和密度。申请人认为,以某一特征时间t(例如,正弦波的周期)为特征的质量传输中边界条件的任何变化的聚合物中的渗透深度lpen由方程式(1)给出:其中d为发泡剂在聚合物中的扩散率。如果在质量传输中边界条件的变化是瞬时的,则该关系本身表示厚度,在施加变化本身之后的每个时间t处,在该厚度内变化的影响是相关的。申请人观察到,在质量传输中边界条件的变化基本上可以受三个变量的影响,这些变量由以下组成:·压力变化·膨胀气体的组成的变化·温度变化申请人首先发现,通过使用能够引起以一定周期t和波形为特征的周期性变化的管理程序可以适当地调节压力变化,所述波形可以为例如正弦形、三角形、方形、锯齿形等。申请人还发现,通过使用管理程序可以适当地调节压力变化,该管理程序能够按照线性、抛物线、指数、脉冲形等快速或缓慢地操作非周期性变化。类似地,申请人发现,通过改变以不同扩散率d为特征的两种或更多种发泡剂(例如氮气和二氧化碳)的分压,可以适当地调节膨胀气体的组成的变化。最后,申请人观察到,温度变化(其动力学遵循能量传输的动力学并且以系统的其他特性(热扩散率)为特征的)可以以校准的方式叠加/耦合到取决于压力和膨胀气体的组成的质量传输的动力学,以获得不同的层。因此,申请人发现,通过借助于一种或更多种发泡剂的压力的周期性变化来适当地设计增溶步骤,还通过利用温度变化,可以获得具有多层结构的发泡聚合物,每个层具有特定且不同的形态和密度。因此,本发明的第一目的由通过使用一种或更多种发泡剂来制备层状发泡聚合物材料的方法表示,其中所述方法包括以下步骤:·提供可发泡聚合物材料;·在压力下和大于20℃的温度下使所述一种或更多种发泡剂在可发泡聚合物材料中增溶;和·将压力瞬间释放;其特征在于,增溶步骤在所述一种或更多种发泡剂的压力分布随时间可变的情况下进行。本发明的第二目的由通过根据本发明的第一目的的方法获得的具有多层结构的发泡聚合物材料表示。本发明的第三目的由具有多层结构和均匀组成的发泡聚合物材料表示,其中所述多层结构包括至少两个层并且其中所述至少两个层中的每一者具有特定且不同的形态和/或密度,其特征在于,所述发泡聚合物材料在存在于发泡材料中的所述至少两个层之间的界面处呈现出密度和/或形态的逐渐变化。特别地,根据本发明的第三目的的发泡聚合物材料的特征在于其在所述至少两个层之间的界面处不呈现出形态和/或密度的不连续性。本发明的第四目的由全部或部分用具有多层结构和均匀组成的发泡聚合物材料制成的制成品表示,其中所述多层结构包括至少两个层并且其中所述至少两个层中的每一者具有特定且不同的形态和/或密度,其特征在于,所述发泡聚合物材料在存在于发泡材料中的所述至少两个层之间的界面处呈现出密度和/或形态的逐渐变化。附图说明图1a示出了本发明中使用的不连续发泡装置的照片。图1b示出了本发明中使用的不连续发泡装置的图示。图2a示出了实施例1至6中使用的样品的图示,其中突出显示了基底表面σeσ’以及侧表面ω。图2b示出了临释放压力以允许发泡之前,实施例1中使用的发泡剂沿样品的整个轴向分布的轴向浓度分布。图2c示出了由经历实施例1的工序的样品得到的泡沫截面的扫描电子显微镜照片(比例尺等于500μm)。为了清楚起见,仅示出了相对于图中所示的垂直线对称的样品的一半。图3a示出了临释放压力以允许发泡之前,实施例2中使用的发泡剂的轴向浓度分布。图3b示出了由经历实施例2的工序的样品得到的泡沫截面的扫描电子显微镜照片(比例尺等于500μm)。示出样品的整个截面以突出显示5个对称层。图3c示出了图3b中所示的相同的图像,其中叠加的图示出了孔径的定性趋势。图4a示出了临释放压力以允许发泡之前,实施例3中使用的发泡剂沿样品的整个轴向分布的轴向浓度分布。图4b示出了由经历实施例3的工序的样品得到的泡沫截面的扫描电子显微镜照片(比例尺等于500μm)。图5a示出了临释放压力以允许发泡之前,实施例4中使用的发泡剂沿样品的整个轴向分布的轴向浓度分布。图5b示出了由经历实施例4的工序的样品得到的泡沫截面的扫描电子显微镜照片(比例尺等于500μm)。为了清楚,仅示出了相对于图中所示的垂直线对称的样品的一半。图6a示出了临释放压力以允许发泡之前,实施例5中使用的发泡剂的轴向浓度分布。图6b示出了由经历实施例5的工序的样品得到的泡沫截面的扫描电子显微镜照片(比例尺等于500μm)。为了清楚,仅示出了相对于图中所示的垂直线对称的样品的一半。图7a示出了临释放压力以允许发泡之前,实施例6中使用的发泡剂的轴向浓度分布。图7b示出了由经历实施例6的工序的样品得到的泡沫截面的扫描电子显微镜照片(比例尺等于500μm)。为了清楚,仅示出了相对于图中所示的垂直线对称的样品的一半。图8示出了实施例7至9中使用的样品的图示,其中突出显示了半径r。图8a示出了临释放压力以允许发泡之前,实施例7中使用的发泡剂的轴向浓度分布。图8b示出了由经历实施例7的工序的样品得到的泡沫截面的扫描电子显微镜照片(比例尺等于200μm)。图9a示出了临释放压力以允许发泡之前,实施例8中使用的发泡剂的轴向浓度分布。图9b示出了由经历实施例8的工序的样品得到的泡沫截面的扫描电子显微镜照片(比例尺等于200μm)。图10a示出了临释放压力以允许发泡之前,实施例9中使用的发泡剂的轴向浓度分布。图10b示出了由经历实施例9的工序的样品得到的泡沫截面的扫描电子显微镜照片(比例尺等于100μm)。图11a示出了临释放压力以允许发泡之前,实施例10中使用的发泡剂沿样品的整个轴向分布的轴向浓度分布。图11b示出了由经历实施例10的工序的样品得到的泡沫截面的扫描电子显微镜照片(比例尺等于500μm)。示出样品的整个截面以突出显示4个非对称层。图12a示出了具有在实施例11中使用的股骨的上端部分的形状的多孔金属容器。图12b示出了由经历实施例11的工序的样品得到的纵向泡沫截面的扫描电子显微镜照片(比例尺等于1mm)。图12c示出了由经历实施例11的工序的样品得到的横向泡沫截面的扫描电子显微镜照片(比例尺等于1mm)。图12d示出了股骨头的横截面。具体实施方式表述“聚合物材料”表示包括热塑性或热固性均聚物或共聚物或其混合物的聚合物材料。表述“可发泡聚合物材料”表示这样的聚合物材料:其能够在一定温度和压力下吸收发泡剂,在释放相同压力后允许泡沫成核并在泡沫生长期间抵抗拉直应力直至固化。表述“发泡剂”表示能够通过在聚合物材料内部形成泡沫而引起聚合物材料的膨胀的物质。表述“多层结构”表示包括两个或更多个层,优选三个或更多个层的结构。表述“均匀组成”表示由在其所有点处均匀且恒定的组成的聚合物材料组成的组成。术语“不连续性”表示两个相邻层之间的净的且明显的边界,是单独制成的具有不同结构的两个层通过热接合方法或用粘合剂制成的复合材料的典型边界。术语“密度”表示给定体积的聚合物材料层的重量与该体积之间的比率。术语“形态”表示在发泡聚合物材料内形成的泡沫的形状、尺寸和每体积的单位数量。术语“发泡聚合物材料”表示在其内部已经通过发泡剂形成泡沫的聚合物材料。本发明的第一目的由通过使用一种或更多种发泡剂来制备层状发泡聚合物材料的方法表示,其中所述方法包括以下步骤:·提供可发泡聚合物材料;·在压力下和大于20℃的温度下使所述一种或更多种发泡剂在可发泡聚合物材料中增溶;和·将压力瞬间释放;其特征在于,增溶步骤在所述一种或更多种发泡剂的压力分布随时间可变的情况下进行。根据本发明的第一目的,所述压力分布优选以周期性或非周期性方式随时间变化。根据本发明的第一目的,所述压力分布优选以具有选自正弦形、三角形、方形或锯齿型或其组合的波形的周期性方式随时间变化。根据本发明的第一目的,所述压力分布优选以按照线性、分段、曲线、抛物线、指数、脉冲形或其组合的非周期性方式随时间变化。根据本发明的第一目的,所述压力分布从等于大气压的最小压力变化至最大300巴,更优选从大气压变化至250巴,并且有利地从大气压变化至200巴。根据本发明的第一目的,所述压力分布优选包括压力分布随时间增加的至少一个步骤和压力分布随时间减小的至少一个步骤。根据本发明的第一目的,所述压力分布可以有利地包括压力分布随时间恒定的至少一个步骤。根据本发明的第一目的,增溶步骤用发泡剂或用两种或更多种发泡剂的混合物,优选用两种发泡剂的混合物进行。有利地,增溶步骤可以通过随时间改变发泡剂的浓度进行。特别地,所述混合物的发泡剂的浓度可以随时间变化。根据本发明的第一目的,增溶步骤优选在20℃至350℃,更优选30℃至250℃,并且有利地50℃至200℃的温度下进行。根据本发明的第一目的,所述一种或更多种发泡剂选自惰性气体、二氧化碳和经取代或未经取代的具有3至8个碳原子的脂族烃(线性、支化或环状的)。有利地,发泡剂选自包括氮气、二氧化碳、正丁烷、异丁烷、正戊烷和异戊烷的组。优选地,经取代的脂族烃包括卤代烃,特别是含氯烃、含氯氟烃和碳氟化合物,诸如,例如,1,1,1,2-四氟乙烷(freonr-134a)、1,1-二氟乙烷(freonr-152a)、二氟甲烷(freonr-32)、五氟乙烷(freonr-125)。根据本发明的第一目的,所述聚合物材料优选选自热塑性聚合物材料或热固性聚合物材料。有利地,所述热塑性聚合物材料选自包括聚烯烃、聚氨酯、聚酯和聚酰胺的组。优选地,所述热固性聚合物材料选自包括聚氨酯、环氧树脂、三聚氰胺树脂、多酚和聚酰亚胺的组。优选地,所述聚合物材料是苯乙烯、乙烯、丙烯和其他烯烃的聚合物和共聚物,例如聚苯乙烯、聚乙烯和聚丙烯。任选地,所述聚合物材料可以包含一种或更多种共聚单体。共聚单体可以包括例如烷基苯乙烯、二乙烯基苯、丙烯腈、二苯醚、α-甲基苯乙烯或其组合。举例而言,聚合物材料可以包含约0重量%至约30重量%,优选约0.1重量%至约15重量%,更优选约1重量%至约10重量%的共聚单体。优选地,聚合物材料的分子量mw(通过gpc测量)可以为约10000道尔顿至约500000道尔顿,更优选约150000道尔顿至约400000道尔顿,甚至更优选约200000道尔顿至约350000道尔顿。有利地,聚合物材料的根据标准astmd1238在200℃的温度和10kg的负载下测量的滑动指数为1.0g/10分钟至20g/10分钟。优选地,本发明中使用的聚合物材料对于其整个厚度具有均匀的组成,即,所述聚合物材料在其所有点处都具有均匀且恒定的组成。有利地,本发明的方法使得可以在避免使用包括如ep1452191a2和ep1878450a1中所述的组成梯度的复合材料的同时,生产具有两个或更多个层的多层产品。而且,本发明的方法有利地使得可以在发泡剂(或发泡剂的混合物)的增溶程序期间创建多个梯度,从而产生具有三个、四个、五个或甚至更多个具有不同形态和/或密度的层的多层材料。优选地,根据本发明的第一目的,将压力以不小于10巴/秒,更优选不小于100巴/秒的速度瞬间释放。本发明的第二目的由通过根据本发明的第一目的的方法获得的具有多层结构的发泡聚合物材料表示。有利地,根据本发明的第二目的,所述发泡聚合物材料包括具有不同密度和/或形态的至少两个层,在所述至少两个层之间的界面处不具有形态和/或密度的不连续性。优选地,所述发泡聚合物材料包括具有不同密度和/或形态的至少两个层,并且具有存在于发泡材料中的密度和/或形态的逐渐变化。根据本发明的第二目的,发泡聚合物材料优选由多层预发泡珠粒或多层发泡片材组成。有利地,所述多层发泡片材包括至少一个具有较低密度和较精细形态的层和至少一个具有较高密度和较粗糙形态的层。有利地,所述多层发泡片材包括至少一个具有较低密度和较粗糙形态的层和至少一个具有较高密度和较精细形态的层。有利地,所述多层发泡片材包括具有均匀形态的至少一个具有较低密度的层和至少一个具有较高密度的层。有利地,所述多层发泡片材包括具有均匀密度的至少一个具有较粗糙形态的层和至少一个具有较精细形态的层。有利地,所述多层预发泡珠粒包括至少一个非发泡层和至少一个预发泡层,其中所述非发泡层相对于所述预发泡层位于径向的外部位置。因此,用本发明的方法,首次可以获得具有多层结构的没有不连续性的(是通过将单独获得的层粘合或焊接在一起而获得的材料的典型特征)且具有均匀组成的发泡聚合物材料,因此避免使用复合材料。因此,本发明的第三目的由具有多层结构和均匀组成的发泡聚合物材料表示,其中所述多层结构包括至少两个层并且其中所述至少两个层中的每一者具有特定且不同的形态和/或密度,其特征在于,所述发泡聚合物材料在存在于发泡材料中的所述至少两个层之间的界面处呈现出密度和/或形态的逐渐变化。特别地,根据本发明的第三目的的发泡聚合物材料的特征在于其在所述至少两个层之间的界面处不呈现出形态和密度的不连续性。有利地,根据本发明的第二目的和第三目的,所述发泡聚合物材料包括具有不同的密度和/或形态并且具有存在于发泡材料中的密度和/或形态的逐渐变化的至少两个层。特别地,多层结构包括至少三个层,并且更特别地包括三个、四个、五个或更多个具有特定且不同的形态和/或密度的层。特别优选的是三层材料,其实施方案在实施例1、4、5和6中描述,并在图2c、图5b、图6b和图7b中示出,以及五层材料,其实施方案在实施例2和10中描述,并在图3b和图11b中示出。根据本发明的第二目的和第三目的的聚合材料使其自身用于产生具有多梯度和各向异性形态(即具有由孔隙率决定的形态)的复杂形状的制成品。本发明的第四目的由全部或部分用具有多层结构和均匀组成的发泡聚合物材料制成的制成品表示,其中所述多层结构包括至少两个层并且其中所述至少两个层中的每一者具有特定且不同的形态和/或密度,其特征在于,所述发泡聚合物材料在存在于发泡材料中的所述至少两个层之间的界面处呈现出密度和/或形态的逐渐变化。优选地,根据本发明的第四目的,所述多层结构包括多梯度形态。有利地,根据本发明的第四目的,所述多层结构包括各向异性形态。特别地,根据本发明的第四目的,所述制成品例如由以下表示:防护系统(护胫、后背支架、肩和肘部护垫、护膝垫、壳体和护垫、防弹背心)、头盔和盔、矫形假体、义齿、表皮修补物、组织工程支架、吸收和隔音板和系统、隔热系统和板、运动鞋的鞋底和元素、汽车面板、运动设备、家具、包装、过滤膜和系统、用于陶瓷材料和多孔金属的牺牲泡沫、用于扩散器和曝气器的泡沫、生物医学系统、用于受控药物递送的垫和贴剂、渐进式机械响应系统、渐进式功能响应系统、电磁屏蔽系统、催化系统、用于航空和航天的泡沫、用于光电子学的泡沫、浮选系统、框架和底盘以及眼镜框架。特别地,根据本发明的第四目的,所述制成品例如由矫形假体,即,能够以相同的结构特征复制人体或动物体的骨骼段的骨结构的医疗器材表示。特别地,根据本发明的第四目的的矫形假体包括下肢(足、踝、膝、股骨、髋)的矫形内置假体(endoprostheses)、上肢(手、腕、肘、肱骨、肩)的矫形内置假体、和脊柱的矫形内置假体。现在将参考在以下实验部分中出于说明性而非限制性目的描述的材料和方法来说明本发明。实验部分为了制备泡沫样品,使用图1所示的分批发泡系统,其一些细节在下面给出。图1示出了本发明中使用的不连续发泡装置的照片(图1a)和图示(图1b)。反应器是圆柱形的,温度调节的和加压的,容积为0.3l(hip,型号bc-1)。对反应器进行改进以允许测量和控制目的工艺参数。为了进行温度控制,将电加热器(11)用作加热元件,并将具有油浴的热交换器(12)用作冷却元件。所述加热器(11)和所述交换器(12)由pid温度调节器(ascon,型号x1)控制,该温度调节器使用pt100探针(4)读取反应器内部的温度。使用schaevitz压力传感器(型号p943)(3)测量饱和步骤期间的压力,并记录发泡剂释放期间的压力模式。阀(1)连接到膨胀气体供应,而阀(2)连接到真空泵。压力释放系统由hip球排出阀(型号15-71nfb)(5)、hip机电致动器(型号15-72nfbtsr8)(6)、以及连接到用于压缩空气的管道(8)和用于电磁阀致动信号(7)的电缆(9)的电磁阀(7)组成。该系统允许重现阀的开启。压力释放期间随时间的压力模式p(t)使用daqpci6036e数据采集系统(nationalinstruments,austin,tx,美国)记录。压力工序由teledyneisco500d容积泵(lincolnne,美国)管理。通过泵控制器的串行接口,可以经由计算机控制泵并执行任何压力工序。另外,该控制器可以处理多达四个用于不同流体的泵。增溶步骤的可变条件的产生可以通过以周期性模式(例如,三角形波或正弦波)或以非周期性模式(例如,线性或曲线分布)改变发泡剂的增溶压力来发生,如以下实施例中所述。实施例1-发明在该实施例中,使用的聚合物是由versalisspa(mantua,意大利)提供的聚苯乙烯(ps)(代码n2380),其平均分子量、密度和熔体流动指数分别等于300kda、1.05g/cm3以及在200℃和10kg下的2.0g/10分钟。样品由直径为25mm且厚度为2.2mm的ps圆柱形盘组成。用金属阻挡膜(对发泡剂完全不渗透)保护其侧表面(图2a中的ω),仅有的暴露于与发泡剂接触的表面是上下两个基底(图2a中的∑和∑′)。以这种方式,质量传输在圆柱轴线的方向上发生并且可以作为一维问题来研究。在这种情况下以及在其中待发泡的样品是圆柱形的,仅由致使材料传输的一维处理的需要决定的实施例2、3、4、5和6中所述的那些情况下,阻挡膜的使用更加严格。认为这对于获得多层结构的目的是没有必要的。在室温下将样品安置在图1中所示且以上描述的分批发泡系统中。然后关闭反应器并使其达到100℃的温度。然后使用表1中所述的压力分布使系统经历膨胀co2气体的增溶步骤。表1初始压力(巴)最终压力(巴)持续时间(分钟)步骤101500.2步骤21502002.6步骤32001005.2如表1所示,压力分布包括三个阶段:·在步骤1中,以线性斜坡在0.2分钟(12秒)内使膨胀co2气体的压力从大气压达到150巴;·在步骤2中,以线性斜坡在2.6分钟(156秒)内使膨胀co2气体的压力从150巴增加至200巴;·在步骤3中,以线性斜坡在5.2分钟(312秒)内使膨胀co2气体的压力从200巴减小至100巴。在步骤3结束时,将压力瞬间释放(以1000巴/秒的最大速度)以进行发泡。临释放压力之前,在步骤3结束时,使用由sato等在“solubilitiesanddiffusioncoefficientsofcarbondioxideinpoly(vinylacetate)andpolystyrene”,thejournalofsupercriticalfluids19(2001)187-198中报告的关于100℃下co2在ps中的扩散率的数据,如利用comsolmultiphysics10.0模拟软件计算的浓度分布以及上述几何结构导致图2b中示出的那样。特别地,在发泡的圆柱形盘中识别并区分出三个不同的发泡区域,具有高浓度发泡剂的靠近基底表面的两个区域,和具有低浓度发泡剂的中心区域。根据该浓度分布,在释放压力后,发现了不同区域的不同发泡能力。具有高浓度发泡剂的区域以取决于发泡条件(在此特别是100℃的温度、约6重量%的浓度以及1000巴/秒的压力释放速率)的形态和密度发泡,而缺少发泡剂的中心区域未发泡,即使其具有与高浓度区域相同的操作条件。特别地,图2c示出了所产生的泡沫的截面的扫描电子显微镜图像,具有明显的三层结构。靠近基底表面的两个区域均发泡,其中密度为约0.1g/cm3,最小孔径为约20μm,而中心区域未发泡。通过使用浓度分布的逐渐变化,在三个区域之间没有建立清晰的分离。相反,检测到密度和形态二者的逐渐变化。特别地,发泡剂朝向盘中心的减小的浓度导致泡沫尺寸的增加(从约20μm至约300μm)以及从0.1g/cm3至1g/cm3的密度的增加。使用特定的增溶程序,可以设计不同层的数量、厚度、形态和密度,如以下实施例中所述。实施例2-发明在室温下将关于阻挡膜的组成、几何结构和定位与实施例1中所述的样品类似的ps样品安置在图1中所示且先前描述的分批发泡装置的反应器中。然后关闭反应器并使其达到100℃的温度。然后使用表2中所述的压力分布使系统经历膨胀co2气体的增溶步骤。表2初始压力(巴)最终压力(巴)持续时间(分钟)步骤101300.2步骤2130130120步骤3130809.6步骤48013015.6如表2所示,压力分布包括四个阶段:·在步骤1中,以线性斜坡在0.2分钟(12秒)内使膨胀co2气体的压力从大气压达到130巴;·在步骤2中,将压力保持在130巴持续120分钟;·在步骤3中,以线性斜坡在9.6分钟(576秒)内使膨胀co2气体的压力从130巴减小至80巴;·在步骤4中,以线性斜坡在15.6分钟(936秒)内使膨胀co2气体的压力从80巴增加至130巴。在步骤4结束时,将压力瞬间释放(以1000巴/秒的最大速度)以进行发泡。临释放压力之前,在步骤4结束时,使用由sato等在“solubilitiesanddiffusioncoefficientsofcarbondioxideinpoly(vinylacetate)andpolystyrene”,thejournalofsupercriticalfluids19(2001)187-198中报告的关于100℃下co2在ps中的扩散率的数据,如利用comsolmultiphysics10.0模拟软件计算的浓度分布以及上述几何形状导致图3a中示出的那样。特别地,在发泡的圆柱形盘中识别并区分出五个不同的发泡区域,具有高浓度发泡剂的靠近基底表面的两个区域,具有较小浓度的两个中间区域,和再次具有高浓度发泡剂的中心区域。根据该浓度分布,在释放压力后,发现了不同区域的不同发泡能力。具有高浓度发泡剂的区域(接近表面的两个区域和中心区域)以取决于发泡条件(在此特别是100℃的温度、约5重量%的浓度以及1000巴/秒的压力释放速率)的形态和密度发泡(在图3b中以“高发泡区域”表示),而具有较少发泡剂(浓度为约3%)的两个中间区域具有较低的发泡程度(在图3b中以“较少发泡区域”示出)。特别地,图3b至图3d示出了用扫描电子显微镜拍摄的在不同放大倍数下产生的泡沫的截面的一些图像,具有清晰的五层结构。靠近基底表面的两个区域和中心区域发泡,其中密度为约0.1g/cm3,孔径为约20μm。两个中间区域发泡较少,其中密度为0.3g/cm3,孔径为约80μm。另外在该实施例中,通过使用所观察的浓度分布的逐渐变化,在不同区域之间没有建立清晰的分离。相反,检测到密度和形态二者的逐渐变化。图像3c和图像3d示出了过渡区的一些放大,其中可以注意到泡沫尺寸的变化。本发明的方法允许在设计上广泛的自由,这与zhouc.等在“fabricationoffunctionallygradedporouspolymerviasupercriticalco2foaming”,composites:partb42(2011)318-325中描述的方法不同。此外,如在图2c和图3b中可以看出,在发泡样品中观察到没有形成形态的不连续性,这与用本领域已知的方法获得的产品中存在的通过结合而分层的产品不同。实施例3-比较在室温下将关于阻挡膜的组成、几何结构和定位与实施例1中所述的样品类似的ps样品安置在图1中所示且先前描述的分批发泡装置的反应器中。然后关闭反应器并使其达到100℃的温度。然后使用表3中所述的压力分布使系统经历膨胀co2气体的增溶步骤。表3初始压力(巴)最终压力(巴)持续时间(分钟)步骤101000.2步骤2100100180如表3所示,压力分布包括两个步骤:·在步骤1中,以线性斜坡在0.2分钟(12秒)内使膨胀co2气体的压力从大气压达到100巴;·在步骤2中,将膨胀co2气体压力保持在100巴持续180分钟,以允许发泡剂的完全增溶。在步骤2结束时,将压力瞬间释放(以1000巴/秒的最大速度)以进行发泡。临释放压力之前,在步骤2结束时,浓度分布是恒定的,并且等于约6重量%的co2。根据该浓度分布,随着压力的释放,在密度(约0.1g/cm3)方面和在形态(平均泡沫尺寸为50μm)方面,均存在均匀的发泡。这种类型的均匀结构是现有技术的典型特征。图4a中示出了示出作为空间横坐标“圆柱轴线”x的函数的在阶段2结束时(临发泡之前)的co2浓度值(表示为相对于最大压力下的平衡浓度的百分比)的图。所得泡沫的扫描电子显微镜图像在图4b中示出。实施例4-比较在室温下将关于阻挡膜的组成、几何结构和定位与实施例1中所述的样品类似的ps样品安置在图1中所示且先前描述的分批发泡装置的反应器中。然后关闭反应器并使其达到100℃的温度。然后使用表4中所述的压力分布使系统经历膨胀co2气体的增溶步骤。表4初始压力(巴)最终压力(巴)持续时间(分钟)步骤101000.2步骤210010020如表4所示,压力分布包括两个步骤:·在步骤1中,以线性斜坡在0.2分钟(12秒)内使膨胀co2气体的压力从大气压达到100巴;·在步骤2中,将压力保持在100巴持续20分钟;在步骤2结束时,将压力瞬间释放(以1000巴/秒的最大速度)以进行发泡。临释放压力之前,在步骤2结束时,浓度分布是由误差函数(erf)描述的浓度分布,所述误差函数(erf)在科技文献中广泛描述。特别地,圆柱形盘中发泡剂的浓度从外到内逐渐变化,如zhouc.等在“fabricationoffunctionallygradedporouspolymerviasupercriticalco2foaming”,composites:partb42(2011)318-325中所描述的。在外层中,在外表面附近,气体浓度为6重量%,而在内层中,气体浓度为零,因为增溶时间(在这种情况下为20分钟)比完全增溶所需的时间少得多。图5a中示出了示出作为空间横坐标“圆柱轴线”x的函数的在阶段2结束时(临发泡之前)的co2浓度值(表示为相对于最大压力下的平衡浓度的百分比)的图。所得泡沫的扫描电子显微镜图像在图5b中示出。在这种泡沫中,可以识别并区分出三个不同的发泡区域,以约0.1g/cm3的密度和精细形态发泡的靠近基底表面的两个区域,和未发泡的中心区域。特别地,发泡区域具有非均匀形态,其中每单位体积的泡沫数量从外表面向内表面逐渐减少(并且相应地,较大的泡沫尺寸),表明从外向内气体的浓度降低。在现有技术(zhouc.等,在″fabricationoffunctionallygradedporouspolymerviasupercriticalco2foaming”,composites:partb42(2011)318-325中)中已知的这种类型的结构,源自于对恒定外部压力下发泡剂的质量传输问题的“误差函数”解决方案。这样,就不可能调整结构,例如以改变发泡/非发泡层的厚度和/或梯度区域的宽度。而且,更不用说,如果不是由相对于暴露于发泡剂气氛的外表面的对称性的原因所决定的那些,则不可能在厚度浓度上具有非单调图案。实施例5-发明在室温下将关于阻挡膜的组成、几何结构和定位与实施例1中所述的样品类似的ps样品安置在图1中所示且先前描述的分批发泡装置的反应器中。然后关闭反应器并使其达到100℃的温度。然后使用表5中所述的压力分布使系统经历膨胀co2气体的增溶步骤。表5初始压力(巴)最终压力(巴)持续时间(分钟)步骤102000.2步骤22002009.6步骤32001000.2步骤41001005如表5所示,压力分布包括四个阶段:·在步骤1中,以线性斜坡在0.2分钟(12秒)内使膨胀co2气体的压力从大气压达到200巴;·在步骤2中,将膨胀co2气体压力保持在200巴持续9.6分钟;·在步骤3中,在0.2分钟(12秒)内使膨胀co2气体的压力从200巴减小至100巴;·在步骤4中,将膨胀co2气体压力保持在100巴持续5分钟;在步骤4结束时,将压力瞬间释放(以1000巴/秒的最大速度)以进行发泡。临释放压力之前,在步骤4结束时,使用由sato等在“solubilitiesanddiffusioncoefficientsofcarbondioxideinpoly(vinylacetate)andpolystyrene”,thejournalofsupercriticalfluids19(2001)187-198中报告的关于100℃下co2在ps中的扩散率的数据,如利用comsolmultiphysics10.0模拟软件计算的浓度分布以及上述几何结构导致图6a中示出的那样。特别地,在发泡的圆柱形盘中识别并区分出三个不同的发泡区域,具有高浓度发泡剂的靠近基底表面的两个区域,和具有低浓度发泡剂的中心区域。不同于图5a中示出的浓度分布,在这种情况下,在高浓度区域中分布最初是平坦的,然后向内减小。另一方面,在图5a的情况下,没有获得具有恒定气体浓度的区域。根据该浓度分布,在释放压力后,发现了不同区域的不同发泡能力。具有高浓度发泡剂的区域以取决于发泡条件的形态和密度发泡,而缺少发泡剂的中心区域未发泡,即使其具有与高浓度区域相同的操作条件。特别地,图6b示出了所产生的泡沫的截面的扫描电子显微镜图像,具有明显的三层结构。靠近基底表面的两个区域发泡,其中密度为约0.1g/cm3,最小孔径为约20μm,而中心区域未发泡。然而,与图5b中所述的情况不同,在这种情况下,由于最外面的区域具有恒定的浓度,因此发泡形态更加均匀,并且由于较低的气体浓度,因此泡沫数量仅在更内部减少(而平均尺寸增加)。实施例6-发明在室温下将关于阻挡膜的组成、几何结构和定位与实施例1中所述的样品类似的ps样品安置在图1中所示且先前描述的分批发泡装置的反应器中。然后关闭反应器并使其达到100℃的温度。然后使用表6中所述的压力分布使系统经历膨胀co2和134a(1,1,1,2-四氟乙烷)气体的增溶步骤。表6初始压力(巴)最终压力(巴)持续时间(分钟)步骤10100(co2)0.2步骤2100(co2)100(co2)9.6步骤3100(co2)100(134a)0.2步骤4100(134a)100(134a)2如表6所示,压力分布包括四个阶段:·在步骤1中,以线性斜坡在0.2分钟(12秒)内使膨胀co2气体的压力从大气压达到100巴;·在步骤2中,将膨胀co2气体压力保持在100巴持续9.6分钟;·在步骤3中,在0.2分钟(12秒)内使膨胀co2气体的压力从100巴减小至0巴;同时,在同一步骤中,使用较高分子量的第二134a气体将外部压力平衡,同时仍保持总的外部压力等于100巴;·在步骤4中,将134a气体压力保持在100巴持续2分钟;在步骤4结束时,将压力瞬间释放(以1000巴/秒的最大速度)以进行发泡。临释放压力之前,在步骤4结束时,使用由sato等在“solubilitiesanddiffusioncoefficientsofcarbondioxideinpoly(vinylacetate)andpolystyrene”,thejournalofsupercriticalfluids19(2001)187-198中报告的关于100℃下co2在ps中的扩散率的数据,如利用comsolmultiphysics10.0模拟软件计算的浓度分布以及上述几何结构导致图7a中示出的那样。为了使用该计算,将气体134a的扩散系数设置为比co2的扩散系数高得多,对于所有实际效果,忽略了134a在聚合物中的吸收。特别地,在发泡的圆柱形盘中识别并区分出三个不同的发泡区域,具有高浓度发泡剂的靠近基底表面的两个区域,和具有低(接近零)浓度发泡剂的中心区域。与图5a中所示的浓度分布不同,在这种情况下,靠近表面的co2的浓度低。根据该浓度分布,在释放压力后,发现了不同区域的不同发泡能力。具有高浓度发泡剂的区域以取决于发泡条件的形态和密度发泡,而缺少发泡剂的中心区域未发泡。特别地,图7b示出了所产生的泡沫的截面的扫描电子显微镜图像,具有明显的三层结构。靠近基底表面的两个区域发泡,但是中心区域未发泡。然而,与图5b中所述的情况不同,在这种情况下,发泡形态可以通过两个梯度来描述,其中泡沫的密度从外向内移动,首先增加然后减小,对应于图7a中所示的压力分布。实施例7-比较在该实施例中,使用的聚合物是由versalisspa(mantua,意大利)提供的聚苯乙烯(ps)(代码n2380),其平均分子量、密度和熔体流动指数分别等于300kda、1.05g/cm3以及在200℃和10kg下的2.0g/10分钟。样品由图8中示意性地示出的直径为1mm的ps球组成。这些物体用于制造所谓的预发泡珠粒,所述预发泡珠粒将在使用水蒸气的系统中烧结以产生预发泡珠粒的烧结过程的下游成品。在该系统中,质量传输在径向方向上发生并且可以作为一维问题来研究。在室温下,将没有任何阻挡层的样品安置在图1中所示且在上文描述的分批发泡系统中。然后关闭反应器并使其达到100℃的温度。然后使用表7中所述的压力分布使系统经历膨胀co2气体的增溶步骤。表7初始压力(巴)最终压力(巴)持续时间(分钟)步骤101000.2步骤210010010如表7所示,压力分布包括两个步骤:·在步骤1中,以线性斜坡在0.2分钟(12秒)内使膨胀co2气体的压力从大气压达到100巴;·在步骤2中,将膨胀co2气体压力保持在100巴持续10分钟,以允许发泡剂的完全增溶。在步骤2结束时,将压力瞬间释放(以1000巴/秒的最大速度)以进行发泡。临释放压力之前,在步骤2结束时,浓度分布是恒定的,并且等于约6重量%的co2。气体浓度分布在图8a中示出。根据该浓度分布,随着压力的释放,在密度(约0.1g/cm3)方面和在形态(平均泡沫尺寸为50μm)方面,均存在均匀的发泡。这种类型的均匀结构是现有技术的典型特征。所得泡沫的扫描电子显微镜图像在图8b中示出。实施例8-发明在室温下将关于阻挡膜的组成、几何结构和缺失与实施例7中所述的样品类似的ps样品安置在图1中所示且先前描述的分批发泡装置的反应器中。然后关闭反应器并使其达到100℃的温度。然后使用表8中所述的压力分布使系统经历膨胀co2和n2气体的增溶阶段。表8初始压力(巴)最终压力(巴)持续时间(分钟)步骤10100(co2)0.2步骤2100(co2)100(co2)10步骤3100(co2)100(n2)0.2步骤4100(n2)100(n2)0.5如表8所示,压力分布包括四个阶段:·在步骤1中,以线性斜坡在0.2分钟(12秒)内使膨胀co2气体的压力从大气压达到100巴;·在步骤2中,将膨胀co2气体压力保持在100巴持续10分钟,以允许发泡剂的完全增溶。·在步骤3中,用n2交换co2。·在步骤4中,将膨胀n2气体的压力保持在100巴持续0.5分钟。在步骤4结束时,将压力瞬间释放(以1000巴/秒的最大速度)以进行发泡。临释放压力之前,在步骤2结束时,两种气体的浓度分布在图9a中示出。根据该浓度分布,随着压力的释放,在密度方面和在形态方面,均存在双峰发泡。所得泡沫的扫描电子显微镜图像在图9b中示出。特别地,注意,在已经使用n2作为发泡剂发泡的外层中,形态非常精细,而在用co2发泡的中心区域中,泡沫密度较低。在文献中,已经广泛证明了n2具有比co2更大的成核能力,尽管浓度较低(在相同压力下),这在使用co2的情况下决定较低的密度。实施例9-发明在室温下将关于阻挡膜的组成、几何结构和缺失与实施例7中所述的样品类似的ps样品安置在图1中所示且先前描述的分批发泡装置的反应器中。然后关闭反应器并使其达到100℃的温度。然后使用表9中所述的压力分布使系统经历膨胀co2和134a(1,1,1,2-四氟乙烷)气体的增溶步骤。表9初始压力(巴)最终压力(巴)持续时间(分钟)步骤10100(co2)0.2步骤2100(co2)100(co2)10步骤3100(co2)100(134a)0.2步骤4100(134a)100(134a)2如表1所示,压力分布包括四个阶段:·在步骤1中,以线性斜坡在0.2分钟(12秒)内使膨胀co2气体的压力从大气压达到100巴;·在步骤2中,将膨胀co2气体压力保持在100巴持续10分钟,以允许发泡剂的完全增溶;·在步骤3中,用另外的气体(134a)交换co2;·在步骤4中,将膨胀134a气体压力保持在100巴持续2分钟。在步骤4结束时,将压力瞬间释放(以1000巴/秒的最大速度)以进行发泡。临释放压力之前,在步骤2结束时,两种气体的浓度分布在图10a中示出。根据该浓度分布,在释放压力时,仅在中心层中发现发泡。所得泡沫的扫描电子显微镜图像在图10b中示出。特别地,注意,存在约50微米的未发泡的外层,然后是发泡的内芯。该形态,除了通过改变饱和条件以外,无法获得。实施例10-发明将关于阻挡膜的组成、几何结构和定位与实施例1中所述的样品类似的ps样品涂覆在两个基底表面之一(图2a的表面∑)上,所述两个基底表面之一具有100微米厚的聚(乙烯醇)pva的聚合物膜。该聚合物具有比所讨论的聚苯乙烯的二氧化碳扩散率低约两个数量级的二氧化碳扩散率,并且可以有效地用于获得圆柱形样品的中心线的相对于与基底平面平行的平面的非对称浓度分布。在室温下将该样品安置在图1中所示且先前描述的分批发泡系统的反应器中。然后关闭反应器并使其达到100℃的温度。然后使用表10中所述的压力分布使系统经历膨胀co2气体的增溶步骤。表10初始压力(巴)最终压力(巴)持续时间(分钟)步骤10130(co2)0.2步骤2130(co2)130(co2)600步骤3130(co2)80(co2)10步骤480(co2)130(co2)10如表10所示,压力分布包括四个阶段:·在步骤1中,以线性斜坡在0.2分钟(12秒)内使膨胀co2气体的压力从大气压达到130巴;·在步骤2中,将膨胀co2气体压力保持在130巴持续10小时(600分钟),以允许发泡剂的完全增溶;·在步骤3中,以线性斜坡在10分钟内使膨胀co2气体的压力减小至80巴;·在步骤4中,以线性斜坡在10分钟内使膨胀co2气体的压力增加至130巴。在步骤4结束时,将压力瞬间释放(以1000巴/秒的最大速度)以进行发泡。临释放压力之前,在步骤2结束时,两种气体的浓度分布在图11a中示出。根据该浓度分布,在释放压力后,发现了不同区域的不同发泡能力。具有高浓度发泡剂的区域以取决于发泡条件的形态和密度发泡较多,而具有低浓度发泡剂的区域发泡较少。特别地,图11b示出了所产生的泡沫的截面的扫描电子显微镜图像,相对于样品的中心(在图11b中的图像中表示为“样品的中心线”)具有明显的非对称四层结构。为了引导目光,插入了图示,该图示示出了在sem显微照片的不同区域处的孔径的定性趋势。垂直虚线勾画出不同的区域。实施例11-发明将聚己内酯pcl(一种用于组织工程领域的生物可相容聚酯)的样品引入到图12a中所示的具有股骨上端部分形状的多孔金属容器中,以限制发泡材料并使其成形,并且在室温下将容器安置在图1中所示且先前描述的分批发泡装置的反应器中。然后关闭反应器并使其达到80℃的温度持续5分钟,然后达到60℃。然后使用表11中所述的压力分布使系统经历膨胀co2和n2气体的增溶阶段。表11初始压力(巴)最终压力(巴)持续时间(分钟)步骤10100(co2)0.2步骤2100(co2)100(co2)600步骤3100(co2)100(n2)0.2步骤4100(n2)100(n2)3如表8所示,压力分布包括四个阶段:·在步骤1中,以线性斜坡在0.2分钟(12秒)内使膨胀co2气体的压力从大气压达到100巴;·在步骤2中,将膨胀co2气体压力保持在100巴持续10分钟,以允许发泡剂的完全增溶。·在步骤3中,用n2交换co2。·在步骤4中,将膨胀n2气体的压力保持在100巴持续3分钟。在步骤4期间,使温度达到40℃,并且在步骤4结束时将压力瞬间释放(以1000巴/秒的最大速度)以进行发泡。临释放压力之前,在步骤4结束时,两种气体的浓度分布与图9a中示出的浓度分布类似。根据该浓度分布,随着压力的释放,在密度方面和在形态方面,均存在双重发泡。所得泡沫的扫描电子显微镜图像在图12b和图12c中示出。图12b示出了纵截面,而图12c示出了横截面。图12d中所示的与股骨的骨结构的相似性是令人惊讶的。特别地,图12d的直虚线表示真实股骨结构的区域,该区域与图12b所示的发泡样品的区域非常相似,而图12d的圆形线表示真实股骨结构的区域,该区域与图12c所示的发泡样品的区域非常相似。注意,图12c中的取向和细长的孔形状,就像在填充模具期间获得的真实股骨中的一样(在发泡阶段期间孔遵循聚合物的流动线)。因此,用本发明的方法,可以容易地且以低成本产生人造骨假体。通常,通过适当地设计模具、聚合物填充水平、增溶步骤和在发泡期间聚合物的模具填充的流体动力学,可以产生具有期望的泡孔形态、密度和取向的多梯度多孔结构,优化了发泡材料的结构和功能各向异性特性。当前第1页12