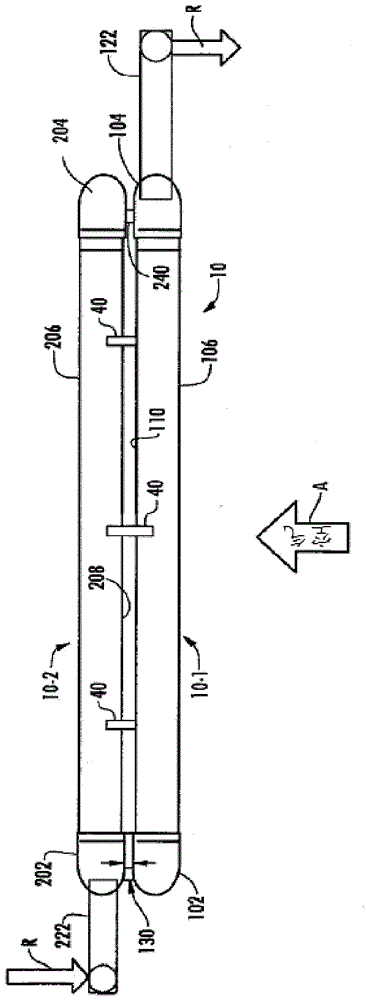
用于制造扁平管翅片热交换器的方法发明背景本发明通常涉及热交换器,更特别涉及扁平管和翅片热交换器及其制造。发明背景热交换器已长期被用作加热、通风、空调和制冷(HVACR)应用中的蒸发器和冷凝器。从历史上看,这些热交换器一直是圆管和板翅(RTPF)热交换器。然而,与传统的RTPF热交换器相比,由于具有紧凑性、热工水力学性能、结构刚度、低重量和降低的制冷剂充注量,所有的铝扁平管和翅片热交换器正被发现越来越广泛地使用于工业中,包括HVACR行业中。典型的扁平管和翅片热交换器包括第一歧管、第二歧管和由多个以间隔平行关系布置的且在第一歧管和第二歧管之间延伸的多个纵向延伸的扁平热交换管所形成的单个管组。在热交换器技术领域中的第一歧管、第二歧管和管组总成通常被称之为板片。此外,在每个邻近对的热交换管之间布置多个翅片以在流过扁平管的外表面且沿翅片表面的流体(通常为HVACR应用中的空气)以及在扁平管内流动的流体(通常为HVACR应用中的制冷剂)之间增加热传递。也被称作单一板片热交换器的这种单一管组热交换器具有纯横流式配置。在HVACR应用中常用的扁平管的实施方案中,扁平管的内部被细分成多个平行的流道。在该技术领域中,这种扁平管通常被称为多通道管、迷你通道管或微通道管。双组扁平管和翅片热交换器在本技术领域中也是已知的。在热交换器技术领域中也被称为双板片热交换器的传统双组扁平管和翅片热交换器通常是由两个传统的翅片和管板片形成的,其中的一个被布置在另一个的后面,且通过外部管道在歧管之间实现流体连通。然而,在除平行横流设置以外的流体流动连通中连接两个板片需要复杂的外部管道。例如,美国专利号6,964,296示出在具有水平管通路和垂直延伸翅片的单板片和双板片实施方案中的扁平管和翅片热交换器。美国专利申请公开号US2009/0025914A1示出双板片扁平管和翅片热交换器,其中每个板片具有在一对水平延伸的歧管之间延伸的垂直管通路并包括被布置在相邻管之间的波纹翅片。发明概要本发明提供了一种用于制造大型多板片扁平管和翅片热交换器的方法。所公开的方法便于进行大量的半自动化生产。在一个方面,提供了一种用于装配具有第一管组和第二管组的扁平管热交换器的方法。该方法包括:以平行间隔的关系排列第一组多个扁平热交换管段;在第一组多个扁平热交换管段中的每个热交换管段的纵向延伸的边缘上安装至少一个间隔夹;以及以与每个第二热交换管成平行间隔的关系排列第二组多个扁平热交换段,其中以与各个第一热交换管段对齐且与安装在各个第一热交换管段上的至少一个间隔夹相结合的方式布置每个第二热交换管。该方法还包括:将第一歧管安装至第一组多个扁平热交换管中每一个的各自的第一端,将第二歧管安装至第一组多个扁平热交换管中的各自的第二端,将第三歧管安装至第二组多个扁平热交换管中每一个的各自的第一端并将第四歧管安装至第二组多个扁平热交换管的各自的第二端,从而形成最终的总成。该方法还包括将多个第一和第二热交换管段冶金结合至各歧管。可通过在钎焊炉内钎焊最终的总成而实现冶金结合。在一个方面,提供了一种用于装配具有第一管组和第二管组的扁平管翅片热交换器的方法。该方法包括通过以下方式形成管阵列:以平行间隔的关系排列第一组多个扁平热交换管段;在第一组多个扁平热交换管段中的每个热交换管段的纵向延伸的边缘上安装至少一个间隔夹;以及以与每个第二热交换管成平行间隔的关系排列第二组多个扁平热交换段,其中以与各个第一热交换管段对齐且与安装在各个第一热交换管段上的至少一个间隔夹相结合的方式布置每个第二热交换管。该方法还包括在每组邻近且平行的第一和第二对齐的扁平热交换管段之间插入折叠翅片以形成部分组装的翅片和管包。该方法还包括通过以下方式形成最终的总成:将第一歧管安装至第一组多个扁平热交换管中每一个的各自的第一端,将第二歧管安装至第一组多个扁平热交换管中的各自的第二端,将第三歧管安装至第二组多个扁平热交换管的每一个的各自的第一端并将第四歧管安装至第二组多个扁平热交换管的各自的第二端。该方法还包括将折叠翅片冶金结合至第一和第二热交换管段并将多个第一和第二热交换管段冶金结合至各歧管。可通过在钎焊炉内钎焊最终的总成而实现冶金结合。在一个方面,该方法包括通过在每个歧管中布置插入深度控制杆并定位每个插入深度控制杆以平行于其所位于的歧管的纵轴线延伸并与管插入的方向相反的方式限定第一和第二热交换管段的各自端在各个歧管中的插入深度。附图简述为了进一步理解本公开,将结合附图参考下列详细描述,其中:图1为如本文所公开的多管组扁平管翅片热交换器的示例性实施方案的示意图;图2为部分地以截面示出的侧视图,其示出了图1所示的热交换器的翅片和扁平管总成的一个实施方案;图3为图1所示热交换器的俯视平面图;图4为部分地以截面示出的侧透视图,其示出了如在图1所示的多组热交换器的装配过程中安装的间隔夹的一个实施方案的布置;图5为部分地以截面示出的侧透视图,其示出了如在图1所示的多组热交换器的装配过程中安装的间隔夹的另一个实施方案的布置;图6为部分地以截面示出的侧透视图,其示出了如在图1所示的多组热交换器的装配过程中安装的间隔夹的另一个实施方案的布置;图7为部分地以截面示出的侧透视图,其示出了如在图1所示的多组热交换器的装配过程中安装的间隔夹的又一个实施方案的布置;图8为部分地以截面示出的侧透视图,其示出了在本文所公开的多组热交换器的装配过程中间隔前管和后管的另一种方法;图9为部分地以截面示出的平面图,其示出了在如本文所公开的多组热交换器的制造过程中各歧管和管组的装配;图10为部分地以截面示出的平面图,其示出了用于装配在图9所示的多组热交换器的右侧的歧管之间的外部流体流动连接的一种方法;图11为部分地以截面示出的平面图,其示出了用于装配在图9所示的多组热交换器的右侧的歧管之间的外部流体流动连接的另一种方法;以及图12为示出其中已定位台阶状插入深度控制杆的歧管的部分截面的侧视图。具体实施方式图1中示出了根据本公开的一种多组扁平管翅片热交换器10的一个示例性实施方案的透视图。第一热交换器板片10-1包括第一歧管102、与第一歧管102间隔开的第二歧管104以及以流体连通连接第一歧管102和第二歧管104且包括具有至少第一和第二管段的多个热交换管段106的第一管组100。类似地,第二热交换器板片10-2包括第一歧管202、与第一歧管202间隔开的第二歧管204以及以流体连通连接第一歧管202和第二歧管204且包括具有至少第一和第二管段的多个热交换管段206的第二管组200。第一和第二热交换器板片10-1和10-2以与被布置在热交换器10的制冷剂入口侧12(即如图1所示的热交换器10的左侧)的第一热交换器板片10-1的第一歧管102和第二热交换器板片10-2的第一歧管202以及被布置在热交换器10的制冷剂出口侧14(即如图1所示的热交换器10的右侧)的第一热交换器板片10-1的第二歧管104和第二热交换器板片10-2的第二歧管204大致成邻近关系的方式并置。尽管在图1中所示的为双板片热交换器构造,但该设计可被无限制地扩展至多个板片,其主要由经济性和可用占用空间所决定。此外,在每个热交换器板片中可考虑不同数量的制冷剂通道,其主要由制冷剂侧压降所决定。在图1所示的实施方案中,第一歧管102和202以及第二歧管104和204沿垂直轴线延伸。多个热交换管段106以间隔平行关系在第一歧管102和第二歧管104之间纵向延伸并以流体连通连接第一歧管102和第二歧管104。类似地,多个热交换管段206以间隔平行关系在第一歧管202和第二歧管204之间纵向延伸并以流体连通连接第一歧管202和第二歧管204。然而,要理解的是,管组100和200中的一组或两组可包括一个或多个蛇形管,其具有多个以纵向间隔平行关系延伸且通过回转弯头互连以形成在管组各自的第一和第二歧管之间的各端相连接的蛇形管的热交换管段。现在参照图2,其部分地以截面示出与被布置在相邻管段106和206中的每一组之间的折叠翅片320成间隔平行关系而进行布置的在图1中示出的多组热交换器10的双板片布置的多个管段106和206。在所示的实施方案中,热交换管段106和206中的每一个包括扁平热交换管,其具有前缘108和208、后缘110和210、上平面112和212以及下平面114和214。每个热交换管段106和206的前缘108和208相对于流经热交换器10的空气来说位于其各后缘110和210的上游。第一和第二管组100和200的热交换管段106和206中每一个的内部流路可分别通过内壁而被分成多个离散的流动通道120和220,其从管的入口端向管的出口端沿管的长度纵向延伸并在第一和第二管组100和200的各集管之间建立流体连通。在图2所示的多通道热交换管段106和206的实施方案中,第二管组200的热交换管段206具有比第一管组100的热交换管段106更大的宽度以为制冷剂侧压降管理提供额外的灵活度。此外,更宽的热交换管段206的内部流路可被分成比热交换管段106的内部流路所分成的离散流动通道120的数量更多的离散流动通道220。相对于通过热交换器10的空气流A来说,在第一(前)热交换器板片10-1的第一管组100后布置第二(后)热交换器板片10-2的第二管组200,使每个热交换管段106直接与各热交换管段206对齐,且使第二管组200的热交换管段206的前缘208以所需间隔G与第一管组100的热交换管段的后缘110间隔开。在图2所示的实施方案中,通过开放间隙建立所需间隔G,从而在沿热交换管段106和206的整个长度对齐的热交换管段106和206中每一组的后缘110和前缘208之间提供开放的水/冷凝水排放空间。通过热和排水特征限定扁平管段深度与间隙G之比,且该比例可位于1.2和6.0的范围中,最好位于1.5和3.0之间。本文所公开的扁平管翅片热交换器10还包括多个折叠翅片320。每个折叠翅片320是由以带状方式紧紧折叠的翅片材料的单个连续带所形成的,从而提供大致正交于扁平热交换管106和206延伸的多个紧密间隔的翅片322。通常,每个连续折叠翅片320的紧密间隔的翅片322的翅片密度可以是约每英寸18至25个翅片(约每厘米7至10个翅片),但也可采用较高或较低的翅片密度。在一个实施方案中,折叠翅片320的每个翅片322可设有分别形成于每个翅片322的第一和第三部分中的百叶窗330和332。百叶窗的数量和百叶窗的几何形状在翅片322的每个部分中可以是不同的且可与各自的扁平管深度相关。带状折叠翅片320中每一个的深度至少从第一管组100的前缘108延伸至第二组200的后缘210,如图2所示。因此,当在装配的热交换器10中的一组相邻的热交换管段之间安装折叠翅片320时,在第一管组100中布置每个翅片322的第一部分324,每个翅片322的第二部分326跨越第一管组100的后缘110和第二管组200的前缘208之间的间隔G,且在第二管组200中布置每个翅片322的第三部分328。在扁平管翅片热交换器10的一个实施方案(未示出)中,相对于第一管组100来说,每个折叠翅片320的前部336可相对于流经热交换器10的空气侧通道的空气在上游延伸,从而突出第一管组100的扁平管段106的前缘108。扁平管段深度(前缘至后缘)与翅片深度(前缘至后缘)的比例由热和排水特征所限定且在一个实施方案中,位于0.30和0.65之间(包含0.30和0.65),且在另一个实施方案中,位于0.34和0.53之间(包含0.34和0.53)。类似地,突出翅片与扁平管段深度的比例由热和排水特征所限定且其范围为0和0.5之间(包含0和0.5)且在一个实施方案中位于0.13和0.33之间(包含0.13和0.33)。制冷剂流R和空气流A之间的热交换分别通过共同形成一次热交换表面的热交换管段106和206的外表面112和114以及212和214而发生,且还通过形成二次热交换表面的折叠翅片320的翅片322的热交换表面而发生。在本文公开的多组扁平管翅片热交换器10中,由于折叠翅片320的翅片322跨越间隔G,一次热交换表面的表面区域与二次热交换表面所提供的表面区域的比例可选择性地进行调整,而不用改变管段的宽度或平行管段之间的间隔。除了在设计过程中外,可增加间隔G的深度以增加折叠翅片320所提供的表面区域,从而降低一次与二次热交换表面的比例,或可减少间隔G的深度以减少折叠翅片板320所提供的表面区域,从而增加一次与二次热交换表面的比例。也可通过增加折叠翅片320的前部336相对于空气流A越过热交换器10的面在上游延伸的距离以增加总的翅片深度和/或通过减少形成两个热交换器板片的管组的扁平管排的数量而降低一次热交换表面与二次热交换表面的比例。根据本文所公开的用于制造多组热交换器的方法的一个实施方案,为了在装配热交换器的过程中在管组100和200之间保持合适的间隔G,在每组对齐的前管段106和后管段206之间布置至少一个间隔夹40。通常,可在每组对齐的前管段106和后管段206之间布置多个间隔夹40,其中多个夹子40以纵向间隔进行布置,如图3所示。当在安装时,通过制造过程使每个间隔夹40保持在第一管组100的每个管段106的后缘110和第二管组200的每个管段206的前缘208之间的距离等于所需的间隔G。沿管段106和206的纵向长度布置的夹子40的数量取决于管段的长度。通常,管段越长,使用的夹子40数量越多。在一个实施方案中,夹子40之间的间隔与热交换管段的长度之间的比例范围可以在1:2和1:8之间。在图4-7中示出了间隔夹40的各种实施方案。在图4所示的实施方案中,间隔夹40包括大致为矩形的本体42,其具有在本体42的端面46向内延伸的单个凹槽44,该凹槽44具有深度和宽度。在图5所示的实施方案中,间隔夹40包括大致为矩形的本体42,其具有在本体42的端面46向内延伸的多个凹槽44,每个凹槽44均具有深度和宽度。这种形成梳状形状的夹子可延续包含所有管的整个热交换器的高度。在这种情况下,将在位于梳状夹子的两侧上的相邻管之间定位两个翅片条。在图6所示的实施方案中,间隔夹40包括大致为矩形的本体42,其具有在本体42的相对端面46和48中每一个上向内延伸的单个凹槽44,每个凹槽44均具有深度和宽度。在图7所示的实施方案中,间隔夹40包括大致为矩形的本体42,其具有在本体42的相对端面46和48中每一个上向内延伸的多个凹槽44,每个凹槽44均具有深度和宽度。再一次地,这种形成双梳状形状的夹子可延续包含所有管的整个热交换器的高度。类似地,将在位于双梳状夹子的两侧上的相邻管之间定位两个翅片条。在该实施方案中,双梳状形状可表示中间管板,其中凹槽变成孔,且在装配过程中可通过该孔插入管。当在热交换器10的装配过程中进行安装时,每个间隔夹40接收各个热交换管段106和206的前缘或后缘。相对于各热交换管段106和206的厚度调整每个凹槽宽度的大小以确保各热交换管段至凹槽44中的适贴过盈配合。相对于各热交换管段106和206的宽度调整每个凹槽44深度的大小以接收各热交换管段106和206的宽度中的至少很大的范围。在整个制造过程中以及后面制造过程的完成中,间隔夹40均保持在其位置上。在图4和图5所示的实施方案中,在每个间隔夹40的每个凹槽44中接收第二热交换管段206(即后管段)且对齐的第一热交换管段106(即前管段)的后缘110紧靠间隔夹40的本体42的相对端面48。在这些实施方案中,在每个凹槽44的基部和端面48之间的距离等于要在第一热交换管段106(即前管段)的后缘110与第二热交换管段206(即后管段)的前缘208之间保持的所需间隔G。在图6和图7所示的实施方案中,第二热交换管段206(即后管段)被接收在每个间隔夹40的本体42的端面46中的每个凹槽44中且对齐的第一热交换管段106(即前管段)的后缘110被接收在间隔夹40的本体42的相对端面48中的每个凹槽44中。在这些实施方案中,在本体42的端面46中的每个凹槽44的基部与本体42的端面48中每个凹槽44的基部之间的距离等于要在第一热交换管段106(即前管段)的后缘110与第二热交换管段206(即后管段)的前缘208之间保持的所需间隔G。在本文所公开的用于制造扁平管热交换器10的方法的一个实施方案中,装配第一和第二管组以形成多组管阵列。第一组多个扁平热交换管段,例如形成第二管组200的第二(后)热交换管段206,以与其平放在共同平面上的后缘210成平行间隔关系进行排列。至少一个间隔夹40以及通常以纵向间隔布置的多个间隔夹40被安装在形成第二管组200的扁平热交换管段阵列中的每个热交换管段206的纵向延伸的前缘208上。然后,通过以与每个热交换管段106成平行间隔关系排列第二组多个扁平热交换段106而装配第一管组100,每个热交换管段106均按与各个热交换管段206对齐且结合被安装在各个热交换管段206的前缘208上的至少一个间隔夹40或结合多个间隔夹40中每一个(视情况而定)的方式进行布置。在已装配多管组总成后,可在每组邻近且平行的第一和第二对齐的扁平热交换管段之间插入折叠翅片320以形成部分装配的翅片和管包。如前面所指出的,每个折叠翅片320限定多个翅片322,其中的每一个至少从第一管组100的热交换管段106的前缘108连续延伸至第二(后)管组200的热交换管段206的后缘210,且如果需要,其可突出第一(前)管组100的热交换管段106的前缘108。多组扁平管翅片热交换器10的最终的总成通过以下方式进行构造:将歧管102安装至形成第一管组100的多个扁平热交换管段106中每一个的各自的第一端,将歧管104安装至形成第一管组100的多个扁平热交换管段106的各第二端,将歧管202安装至形成第二管组200的多个扁平热交换管段206中每一个的各自的第一端,并将歧管204安装至形成第二管组200的多个扁平热交换管段206的各第二端。该方法还包括将折叠翅片320冶金结合至第一和第二热交换管段106和206并将多个第一和第二热交换管段106和206冶金结合至各歧管102和104以及202和204。可通过在钎焊炉内钎焊最终的总成而实现冶金结合。在上述方法的变形中,在以与第二管组200对齐的方式装配第一管组100前,可将折叠翅片320插入形成第二管组200的装配的间隔平行热交换管206的阵列中。在该变形中,在形成第二管组200的扁平热交换管段的阵列中的每个热交换管段206的纵向延伸的前缘208上安装间隔夹40后,将折叠翅片320插入形成第二管组200的扁平热交换管段的阵列中的每组相邻热交换管段206之间的空间中。然后,以与形成第二管组200的各个热交换管段206对齐且结合一个或多个间隔夹40的方式安装形成第一管组100的热交换管段106中的每一个,从而形成管和翅片包,其包括对齐的前热交换管段106和后热交换管段206的阵列,其中在前热交换管段106和后热交换管段206之间以交替的设置方式布置折叠翅片320,例如如图1所示。参照图8,在本文所公开的用于制造多组扁平管翅片热交换器10的方法的另一个实施方案中,消除了间隔夹40。在该实施方案中,为了在热交换器的装配过程中在管组100和200之间保持合适的间隔G,在紧靠对齐的热交换管段106和206的上表面的折叠翅片320的翅片322之间的折叠处切割间隔片50。在三侧切割间隔片50,且间隔片50沿其未切的基部向下弯回以提供支撑表面,当在制造过程中的装配期间进行放置时,第一热交换管段的后缘110紧靠在该支撑表面上。定位在翅片的折叠处的切口,从而当弯回时使间隔片50定位第一热交换管段106(即前管段)的后缘110,其与第二热交换管段206的前缘208之间的距离等于所需间隔G。要理解的是,在实践中,无需在折叠翅片320的每个折叠处切割间隔片50。相反地,将沿折叠翅片的长度以纵向间隔在所选的折叠处切割间隔片50。在该实施方案中,在热交换管段206以间隔平行的设置方式被设置于工作表面上的其各自的后缘上以形成其形成第二管组200的扁平热交换管段的阵列后,将折叠翅片320插入形成第二管组200的扁平热交换管段的阵列中的每组相邻的热交换管段206之间的空间中。每个折叠翅片在其中预切割至少一个间隔片50,如本文之前所述。然后,形成第一管组100的热交换管段106中的每一个以与形成第二管组200的各个热交换管段206对齐的方式进行安装且位于间隔片50的支撑表面上。在折叠翅片320所选的折叠处预切割间隔片50,从而当其位于间隔片所提供的支撑表面上时,使前热交换管段106的后缘110与后热交换管段206的前缘208以所需间隔G间隔开来。在热交换器10的装配中,需要分别限制热交换管段106和206的各端至歧管102和104以及202和204中的插入深度。在歧管102、104、202和204的制造过程中,在合适的位置切出、冲出或以其它方式机加工出至歧管中的槽162以接收管段106和206的各端。调整接收槽162的大小以适贴过盈配合接收各个热交换管段106和206的一端。如果相邻歧管104和204或102和202形成单件挤出物或是分别形成的但却焊接或以其它方式连接在一起,那么则可同时在该对的两个歧管中冲出槽162。如果相邻歧管为分开的本体,则可同时将覆盖每个歧管端并在歧管之间保持所需分离的整体式单件端帽插入位于成对的歧管的每一端的歧管的端部中,以在成对的歧管中同时冲出槽162的过程中以及在将热交换管段106和206装配至槽162中的过程中控制歧管间隔。现在参照图9-11,根据本文所公开的用于制造多组热交换器的方法的一个方面,在将歧管装配至热交换管段106和206的各端前将插入深度控制杆160插入每个歧管102、104、202和204。在各歧管的内室中定位每个插入深度控制杆160,各歧管与其中形成槽162且要将管端插入其中的歧管侧相对。在装配过程中,每个管端被插入各个歧管102、104、202和204中的各接收槽162中直到热交换管段的端部击中位于歧管中的插入深度控制杆160。相对于在其中定位控制杆以将插入深度限制为所需深度的在各歧管的插入方向的内部尺寸调整插入深度控制杆160的直径,从而防止将管端过度地插入歧管的内室中。在图9所示的实施方案中,插入深度控制杆160沿其纵向长度具有均匀的直径且靠着与槽162相对的歧管内壁进行定位。在图10所示的实施方案中,插入深度控制杆160被定位为远离歧管的内壁,同时还被定位以沿歧管的内室纵向延伸以限制延伸通过接收槽162的管段的端部的插入深度。在该实施方案中,插入深度控制杆160可包括台阶部分164,如图12所示,调整其大小以建立与歧管内壁的过盈配合,从而在将管段的端部插入接收槽的装配过程中将插入深度控制杆160保持在所需的位置上。在图9所示的实施方案中,以通过位于歧管104和204之间的块插入物240的中心孔242所限定的流路的直接流体流动连通连接歧管104和204,如图9所示。定位块插入物240,从而使中央孔242与分别通过歧管104和204的各壁所形成的孔244和246对齐。这样可建立对齐的连续的流路,通过该流路,制冷剂可从第二管组200的第二歧管204的内部通行并通过孔246,进而通过块插入物240的中央孔242,并进而通过孔244进入第一管组100的第二歧管104的内部。确定块插入物240侧面的轮廓以与各歧管104和204的邻接外表面的轮廓匹配和配合。将块插入物240冶金结合(例如通过钎焊或焊接)至第二歧管104和204中的每一个。在图10和图11所示的实施方案中,相邻的歧管104和204通过在第一端226向第二管组200的歧管204的内室开放且在第二端228向第一管组100的歧管104的内室开放的至少一个外部管道224以流体流动连通而进行连接。在热交换单元10的制造过程中,在分别将第二歧管104和204装配至第一和第二管组100和200后,将管道224的第一端226插入延伸通过第二管组200的第二歧管204的壁的配合孔并将管道24的第二端228插入延伸通过第二管组100的第二歧管104的壁的配合孔。可提供一个以上的管道224以在第二歧管104和第二歧管204之间建立流体流动连通。例如,可在纵向间隔提供多个外部管道224。在本文所公开的方法的一个实施方案中,在从歧管104和204移除插入深度控制杆160前安装每个管道224。因此,如图10所示,沿与接收孔162相对的歧管内壁布置的插入深度控制杆160分别限制端部226和228至歧管204和104中的插入深度,从而防止过度地将端部226和228插入歧管中。在本文所公开的方法的另一个实施方案中,从歧管104和204移除插入深度控制杆160并将端帽固定至位于外部管道224前的歧管的各端。为了分别预防管道224的第一和第二端226和228至歧管104和204的插入深度过深,可临时性地在管道224和歧管104和204的外表面之间定位块或杆230以限制管道230的第一和第二端226和228至第一歧管104和第二歧管204的各配合孔中的插入深度,如图11所示。在将管道224的第一和第二端226和228分别冶金结合(例如通过钎焊或焊接)至第二歧管104和204后,可移除块230。尽管已参照如图示的示例性实施方案具体地示出和描述了本发明,但是本领域的技术人员将认识到,在不脱离本发明的精神和范围的情况下可做出各种修改。例如,要理解的是本文所公开的多组扁平管翅片热交换器10可包括两个以上的管组。还要理解的是,管组100和200可包括具有热交换管段106和206的蛇形管,所述热交换管段106和206为通过U型弯头或蛇形弯连接以形成在热交换器板片的第一歧管和第二歧管之间其各自端部进行连接的蛇形管的平行线性管段。进一步地,虽然本文所公开的多管组热交换器被示为具有扁平管段,但本发明的各个方面也适用于具有圆管或其它形式的非圆形管的多组热交换器。因此,本公开并不限于所公开的特定实施方案,而是本公开将包括落在所附权利要求范围内的所有实施方案。