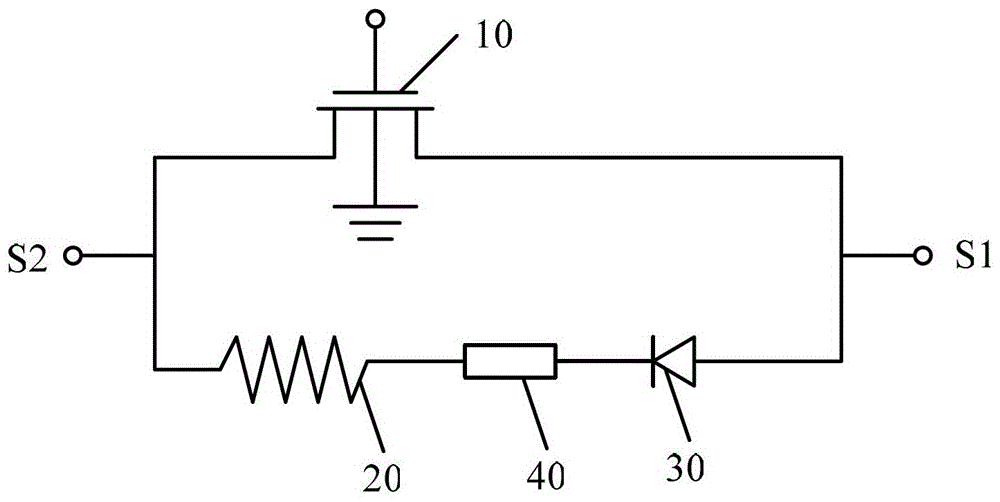
本发明涉及半导体领域,特别涉及一种半导体测试装置及测试方法。
背景技术:随着半导体器件集成度的不断提高,特征尺寸逐渐减小,MOS晶体管的沟道的长度也逐渐减小,栅氧化层的厚度也在不断降低。同时,作为芯片外围电路的输入/输出器件和作为存储器的核心器件都需要较高的驱动电压,这就导致这些器件的沟道中的电场变的很强,使得载流子在输送过程中发生碰撞电离,产生额外的空穴电子对,产生热载流子。纵向的栅极电压会使部分热载流子注入栅氧化层,导致器件的阈值电压等参数发生漂移,形成较为严重的热载流子注入效应(HotCarrierInjection,HCI)。由于电子与空穴的平均自由程不同,电子注入的几率要比空穴高3个数量级,因此NMOS晶体管更容易引起热载流子注入效应(HCI)。目前半导体工艺形成的MOS晶体管的寿命长达十年甚至十几年,采用与实际工作状态相仿的测试电压对热载流子注入效应进行失效测试是不可行的。因此,现有技术通常采用加速应力条件进行热载流子注入效应的失效测试。为了测试MOS晶体管的热载流子注入效应,公开号为CN1588104A的中国专利文献公开了一种MOS晶体管热载流子注入效应的测量方法,具体包括:确定漏极、栅极的应力电压值;在所述MOS晶体管的漏极和栅极施加所述应力电压值;在10秒、20秒、50秒等时间点处关断应力电压,快速测量MOS晶体管对应参数的退化幅度值并进行记录;一次测量并记录完毕后,继续将相应的应力电压施加在所述漏极、栅极上,如此反复,直到对应参数的退化幅度值超过失效标准。但利用所述测试方法进行热载流子注入效应的失效测试的测试结果不精确。
技术实现要素:本发明解决的问题是提供一种半导体测试装置及测试方法,可以提高测试精确度,降低测试成本。为解决上述问题,本发明技术方案提供了一种半导体测试结构,包括:第一测试端、第二测试端、待测试MOS晶体管、加热单元、二极管和第一电阻;所述待测试MOS晶体管的源极、漏极的其中一端与第一测试端相连接,另一端与第二测试端相连接;所述加热单元围绕所述待测试MOS晶体管设置,所述加热单元、第一电阻和二极管串联且与所述待测试MOS晶体管的源极、漏极并联,所述加热单元、电阻和二极管的串联结构的第一端与第一测试端相连接,第二端与第二测试端相连接,且所述二极管的正极对应于第一测试端,所述二极管的负极对应于第二测试端。可选的,还包括:围绕所述待测试MOS晶体管设置的隔离结构,所述加热单元位于所述隔离结构表面,使得所述加热单元与所述待测试MOS晶体管电学隔离。可选的,所述加热单元位于围绕待测试MOS晶体管设置的半导体衬底内,且所述加热单元与所述待测试MOS晶体管电学隔离。可选的,所述加热单元的材料为多晶硅或TiN。可选的,所述加热单元的图形的形状为蛇形或螺旋形。可选的,所述加热单元与所述待测试MOS晶体管之间的间距为最小设计尺寸。可选的,当所述加热单元的电阻值为R1,漏极应力电压的电压值为Vd1,漏极工作电压的电压值为Vd2,则所述第一电阻的电阻值R0=Vd1*R1/Vd2-R1。本发明技术方案还提供了一种采用所述半导体测试结构的测试方法,包括:确定待测试MOS晶体管对应的漏极应力电压、漏极工作电压,获得待测试MOS晶体管对应参数的初值参数值;在所述第一测试端施加漏极应力电压,所述第二测试端接地,加热单元工作,对待测试MOS晶体管的漏极施加电压应力;待测试MOS晶体管的漏极施加一段时间的电压应力后,所述第二测试端变为施加漏极工作电压,所述第一测试端变为接地,加热单元不工作,测试所述待测试MOS晶体管处于正常工作状态下的对应参数值,将所述参数值与初值参数值进行比较,获得对应参数值的退化幅度值;一次参数值测试完成后,继续对待测试MOS晶体管的漏极施加电压应力,直到下一次参数值测试,如此反复,直到对应参数值的退化幅度值达到失效标准,获得对应的失效时间。可选的,当对待测试MOS晶体管的漏极施加电压应力时,待测试MOS晶体管的栅极施加的电压为栅极应力电压,当进行参数值测试时,待测试MOS晶体管的栅极施加的电压为栅极工作电压,所述栅极应力电压和栅极工作电压的电压值相同或不同。可选的,当所述栅极应力电压和栅极工作电压的电压值相等时,所述电压值为饱和区漏极电流对应的栅极电压值。可选的,当所述栅极应力电压和栅极工作电压的电压值不相等时,所述栅极应力电压的电压值小于栅极工作电压的电压值,且所述栅极工作电压的电压值为饱和区漏极电流对应的栅极电压值。可选的,所述对应参数值为饱和区漏极电流。可选的,当所述对应参数值为饱和区漏极电流时,所述失效标准为饱和区漏极电流的退化幅度值达到初始饱和区漏极电流的10%。可选的,所述漏极应力电压大于漏极工作电压。与现有技术相比,本发明具有以下优点:所述半导体测试结构的加热单元与二极管串联,且利用所述二极管控制加热单元工作或不工作,施加电压应力时,第一测试端施加漏极应力电压,第二测试端接地,加热单元在施加电压应力时工作,利用加热单元将对应的待测试MOS晶体管的温度提高到正常工作时候的温度(例如接近125℃),有利于提高测试精确度。而当进行参数值测试时,只需要将第二测试端施加漏极工作电压,第一测试端接地,加热单元就不工作,二极管截止,利用所述漏极工作电压进行参数值测试时对应获得的电流为待测试MOS晶体管的漏极电流,所述加热单元不会影响待测试MOS晶体管的参数值测试。本发明的半导体测试结构不需要提供额外的加热装置,且利用所述半导体测试结构可以在一个测试结构中对待测试MOS晶体管的漏极施加电压应力和进行参数值测试,不需要再利用其他装置,有利于降低测试成本。所述测试方法在施加电压应力和参数值测试时,分别改变施加在第一测试端、第二测试端的电压,控制二极管的导通或截止,使得在施加电压应力时,加热单元工作,对应的待测试MOS晶体管的温度提高到正常工作时候的温度(例如接近125℃),有利于提高测试精确度,当进行参数值测试时,二极管截止,利用所述漏极工作电压进行参数值测试时对应获得的电流为待测试MOS晶体管的漏极电流,所述加热单元不会影响待测试MOS晶体管的参数值测试,且不需要提供额外的加热装置,有利于降低测试成本。附图说明图1是不同环境温度下待测试MOS晶体管的饱和区漏极电流退化幅度与时间的关系示意图;图2至图4是本发明实施例的半导体测试装置的结构示意图;图5是本发明实施例的测试方法的流程示意图。具体实施方式发明人发现,利用现有技术的测试方法进行热载流子注入效应的失效测试的测试结果与实际情况相差较大,经过研究后发现:这主要是由于环境温度对待测试MOS晶体管的热载流子注入效应有很大的影响。请参考图1,为不同环境温度下待测试MOS晶体管的饱和区漏极电流退化幅度与时间的关系示意图,其中虚线为环境温度为125℃的情况下测得的饱和区漏极电流退化幅度与时间的关系曲线,实线为环境温度为25℃的情况下测得的饱和区漏极电流退化幅度与时间的关系曲线。从图中可以很明显的看到,环境温度越高,饱和区漏极电流退化幅度越大,待测试MOS晶体管的失效时间越短。而对于核心器件(CoreDevice)区,由于器件较密集,且工作电压都较高,使得核心器件区的温度很高,通常可以达到125℃以上,而现有技术的测试方法对应的器件密度相对较小,所述器件产生的热量不及散失的热量多,使得进行热载流子注入效应的失效测试通常是在常温下进行测试,使得测得的失效时间往往能大于实际工作状态下对应的失效时间。为此,发明人经过研究,提出了一种半导体测试装置及测试方法,所述半导体测试装置中的待测试MOS晶体管的源极、漏极的其中一端与第一测试端相连接,另一端与第二测试端相连接;加热单元围绕所述待测试MOS晶体管设置,所述加热单元、电阻和二极管串联且与所述待测试MOS晶体管的源极、漏极并联,且所述二极管的正极对应于第一测试端,所述二极管的负极对应于第二测试端。当第一测试端施加有漏极应力电压,所述第二测试端接地时,所述二极管导通,所述加热单元进行加热,利用所述加热单元将待测试MOS晶体管的温度上升到实际的工作温度,且在所述工作温度下对待测试MOS晶体管的漏极施加电压应力。所述半导体测试结构的加热单元与二极管串联,且利用所述二极管控制加热单元工作或不工作,施加电压应力时,第一测试端施加漏极应力电压,第二测试端接地,加热单元在施加电压应力时工作,利用加热单元将对应的待测试MOS晶体管的温度提高到正常工作时候的温度(例如接近125℃),有利于提高测试精确度。而当进行参数值测试时,只需要将第二测试端施加漏极工作电压,第一测试端接地,加热单元就不工作,二极管截止,利用所述漏极工作电压进行参数值测试时对应获得的电流为待测试MOS晶体管的漏极电流,所述加热单元不会影响待测试MOS晶体管的参数值测试。本发明的半导体测试结构不需要提供额外的加热装置,且利用所述半导体测试结构可以在一个测试结构中对待测试MOS晶体管的漏极施加电压应力和进行参数值测试,不需要再利用其他装置,有利于降低测试成本。为使本发明的上述目的、特征和优点能够更为明显易懂,下面结合附图对本发明的具体实施方式做详细的说明。在以下描述中阐述了具体细节以便于充分理解本发明。但是本发明能够以多种不同于在此描述的其它方式来实施,本领域技术人员可以在不违背本发明内涵的情况下做类似推广。因此本发明不受下面公开的具体实施的限制。本发明实施例首先提供了一种半导体测试结构,请参考图2,为本发明实施例的半导体测试结构的结构示意图,具体包括:第一测试端S1、第二测试端S2、待测试MOS晶体管10、加热单元20、二极管30和第一电阻40;所述待测试MOS晶体管10的源极、漏极的其中一端与第一测试端S1相连接,另一端与第二测试端S2相连接;所述加热单元20、二极管30和第一电阻40串联且与所述待测试MOS晶体管10的源极、漏极并联,所述加热单元20、二极管30和第一电阻40的串联结构的第一端与第一测试端S1相连接,第二端与第二测试端S2相连接,且所述二极管30的正极对应于第一测试端S1,所述二极管30的负极对应于第二测试端S2。在本实施例中,所述第一测试端S1与二极管30的正极相连接,所述二极管30的负极通过第一电阻40、加热单元20的串联结构与第二测试端S2相连接。在其他实施例中,也可以将所述第二测试端与二极管的负极相连接,且在所述二极管的正极通过第一电阻、加热单元的串联结构与第一测试端相连接。在其他实施例中,也可以将所述第一测试端与第一电阻的一端相连接,所述第二测试端与加热单元的一端相连接,且所述二极管的正极与第一电阻的另一端相连接,所述二极管的负极与加热单元的另一端相连接。在其他实施例中,也可以将所述第一测试端与加热单元的一端相连接,所述第二测试端与第一电阻的一端相连接,且所述二极管的正极与加热单元的另一端相连接,所述二极管的负极与第一电阻的另一端相连接。所述加热单元20为高阻的导电材料图形,所述高阻导电材料为多晶硅或TiN等高阻材料,利用所述加热单元20对待测试MOS晶体管10进行加热,使得所述待测试MOS晶体管10可以在与正常工作的温度相仿的环境中进行失效测试,避免了温度对热载流子注入效应的影响,使得最终测得的失效时间更符合实际情况,测试结果更精确。请参考图3和图4,图3为本发明实施例的待测试MOS晶体管与加热单元之间的剖面结构示意图,图4为本发明实施例的待测试MOS晶体管与加热单元之间的俯视结构示意图,具体包括:位于半导体衬底01表面的待测试MOS晶体管10,位于所述待测试MOS晶体管10周围的隔离结构15,利用所述隔离结构15将所述待测试MOS晶体管10与其他半导体器件电学隔离,所述隔离结构15为浅沟槽隔离结构或利用硅的局部氧化(LOCOS)工艺形成的氧化硅层;位于所述隔离结构15表面且围绕所述待测试MOS晶体管的加热单元20。在本实施例中,所述加热单元20的俯视图形为螺旋形,所述螺旋形包括圆形螺旋或方形螺旋,所述螺旋的圈数范围为1圈~10圈,所述螺旋形的加热单元20的一端与第一电阻40相连接,所述螺旋形的加热单元20的另一端与第二测试端S2相连接。在其他实施例中,所述加热单元的俯视图形为蛇形,且所述待测试MOS晶体管位于所述蛇形的加热单元中间,所述蛇形加热单元的两端、第一电阻、二极管互相串联后与第一测试端、第二测试端相连接,利用所述蛇形的加热单元对待测试晶体管进行加热。由于所述加热单元的图形(螺旋形或蛇形)都围绕所述待测试MOS晶体管,使得所述待测试MOS晶体管受热均匀。在其他实施例中,所述加热单元位于半导体衬底内的沟槽中,且所述沟槽侧壁具有绝缘层,使得所述加热单元与半导体衬底表面的MOS晶体管电学隔离,且所述加热单元的俯视形状为蛇形或螺旋形,使得所述待测试MOS晶体管位于加热单元的正中间,使得所述待测试MOS晶体管受热均匀。在本实施例中,所述加热单元20与所述待测试MOS晶体管10之间的间距、所述待测试MOS晶体管10与隔离结构15边缘之间的间距、所述隔离结构15边缘与所述加热单元20之间的间距都为最小设计尺寸,使得加热单元20产生的热量能最大限度地提高待测试MOS晶体管10的温度。所述半导体测试结构的加热单元与二极管串联,且利用所述二极管控制加热单元工作或不工作,施加电压应力时,第一测试端施加漏极应力电压,第二测试端接地,加热单元在施加电压应力时工作,利用加热单元将对应的待测试MOS晶体管的温度提高到正常工作时候的温度(例如接近125℃),有利于提高测试精确度。而当进行参数值测试时,只需要将第二测试端施加漏极工作电压,第一测试端接地,加热单元就不工作,二极管截止,利用所述漏极工作电压进行参数值测试时对应获得的电流为待测试MOS晶体管的漏极电流,所述加热单元不会影响待测试MOS晶体管的参数值测试。本发明的半导体测试结构不需要提供额外的加热装置,且利用所述半导体测试结构可以在一个测试结构中对待测试MOS晶体管的漏极施加电压应力和进行参数值测试,不需要再利用其他装置,有利于降低测试成本。本发明实施例还提供了一种采用上述半导体测试结构的测试方法,请参考图5,为所述测试方法的流程示意图,具体包括:步骤S101,对待测试MOS晶体管对应参数进行测试获得初值参数值;步骤S102,在所述第一测试端施加漏极应力电压,所述第二测试端接地,加热单元工作,对待测试MOS晶体管的漏极施加电压应力;步骤S103,到达某个时间点,所述第二测试端变为施加漏极工作电压,所述第一测试端变为接地,加热单元不工作,测试所述待测试MOS晶体管处于正常工作状态下的对应参数值,将所述参数值与初值参数值进行比较,获得对应参数值的退化幅度值;步骤S104,一次参数值测试完成后,继续对待测试MOS晶体管的漏极施加电压应力,直到下一次参数值测试,如此反复,直到对应参数值的退化幅度值达到失效标准,获得对应的失效时间。首先,请参考图2,在对漏极施加电压应力之前,在所述第二测试端S2施加漏极工作电压,所述第一测试端S1接地,使得二极管30截止,且在所述待测试MOS晶体管10的栅极施加栅极工作电压,衬底接地,利用开尔文四端测试法测试所述待测试MOS晶体管的源极和漏极之间的漏极电流,获得待测试MOS晶体管对应参数的初值参数值。所述栅极工作电压的电压值为饱和区漏极电流对应的栅极电压值,所述漏极工作电压为正常工作时施加的工作电压。在本实施例中,所述对应参数为饱和区漏极电流,获得的初始参数值为待测试MOS晶体管的初始饱和区漏极电流。获得初始参数值后,在所述第一测试端S1施加漏极应力电压,所述第二测试端S2接地,在所述待测试MOS晶体管10的栅极施加栅极应力电压,所述待测试MOS晶体管10的衬底接地,对待测试MOS晶体管10的漏极施加电压应力,使得待测试MOS晶体管10的靠近漏极的沟道区内发生热载流子注入效应,使得待测试MOS晶体管10的栅介质层慢慢退化。所述漏极应力电压的电压值大于所述漏极工作电压的电压值,通过提高施加在漏极上的电压,加速电压应力,使得待测试MOS晶体管因热载流子注入效应的失效时间变短,从而可以节省测试时间。在其中一个实施例中,当所述漏极工作电压的电压值为5V时,所述漏极应力电压的电压值为5.5V或5.9V。且所述栅极应力电压的电压值可以与栅极工作电压的电压值相等或不相等。在本实施例中,所述栅极应力电压的电压值与栅极工作电压的电压值相等,所述电压值为饱和区漏极电流对应的栅极电压值。在其他实施例中,当所述栅极应力电压的电压值大于或小于栅极工作电压的电压值时,所述漏栅电压差变大,使得待测试MOS晶体管靠近漏极的电场变得更强,更容易产生热载流子,更容易产生热载流子注入效应。且由于在所述第一测试端S1施加漏极应力电压,所述第二测试端S2接地,而二极管30的正极对应于第一测试端S1,二极管30的负极对应于第二测试端S2,所述二极管导通,使得加热单元20工作产生热量,利用所述加热单元将待测试MOS晶体管的温度上升至待测试MOS晶体管的正常工作时的温度,使得最终测得的失效时间与正常工作时MOS晶体管的因热载流子注入效应的失效时间更接近、更精确。在本实施例中,当在所述第一测试端S1施加的漏极应力电压的电压值为Vd1,施加在所述加热单元20的电压值为V3,且所述加热单元20的电阻值为R1,第一电阻的电阻值为R0,则V3/R1=Vd1/(R0+R1)。对待测试MOS晶体管的漏极施加一段时间的电压应力后,在某些时间点,例如10秒、50秒、100秒、200秒、400秒、1000秒,停止在第一测试端S1施加漏极应力电压,所述第一测试端S1变为接地,而所述第二测试端S2变为施加漏极工作电压。由于第一测试端和第二测试端之间的电流方向发生了变化,所述二极管30截止,利用所述漏极工作电压进行参数值测试时对应获得的电流为待测试MOS晶体管的漏极电流,所述加热单元不会影响待测试MOS晶体管的参数值测试。在现有的测试方法中,在施加电压应力阶段和参数值测试时,源极和漏极通常是确定的,即通常是在一个测试端上交替施加漏极应力电压和漏极工作电压。而本发明实施例通过交替在第一测试端上施加漏极应力电压,在第二测试端上施加漏极工作电压,就能模拟真实芯片中高阻器件对附近的MOS晶体管的加热影响,而不用需要再采用其他装置,有利于降低测试成本。由于正常工作下的MOS晶体管产生的热量主要是由源漏电压施加在源极和漏极上,对应产生的漏极电流流经沟道区引起的,在本实施例中,为了使得施加电压应力时待测试MOS晶体管的温度更接近于MOS晶体管正常工作的温度,施加在所述加热单元20两侧的电压等于漏极工作电压Vd2,使得Vd2/R1=Vd1/(R0+R1)进而,R0=Vd1*R1/Vd2-R1。当所述第一电阻40的电阻值R0为“Vd1*R1/Vd2-R1”时,施加电压应力时待测试MOS晶体管的温度最接近于MOS晶体管正常工作的温度,使得最终测试获得的失效时间更精确。且利用开尔文四端测试法对待测试MOS晶体管进行测试,获得对应的饱和区漏极电流。将所述饱和区漏极电流与初始饱和区漏极电流进行比较,获得对应参数的退化幅度值,所述退化幅度值为:饱和区漏极电流与初始饱和区漏极电流两者之差除以初始饱和区漏极电流获得的百分比。当所述退化幅度值达到失效标准,在本实施例中,所述失效标准为饱和区漏极电流的退化幅度值达到初始饱和区漏极电流的10%,即认为MOS晶体管失效,对应的对待测试MOS晶体管的漏极施加电压应力的总时间即为失效时间。在其他实施例中,所述失效标准也可以为其他数值。当所述退化幅度值未达到失效标准时,在一次参数值测试完成后,重新在所述第一测试端S1施加漏极应力电压,所述第二测试端S2接地,在所述待测试MOS晶体管10的栅极施加栅极应力电压,所述待测试MOS晶体管10的衬底接地,对待测试MOS晶体管10的漏极施加电压应力,使得待测试MOS晶体管10的靠近漏极的沟道区内发生热载流子注入效应,使得待测试MOS晶体管10的栅介质层慢慢退化。再对待测试MOS晶体管的漏极施加一段时间的电压应力后,所述第二测试端重新变为施加漏极工作电压,所述第一测试端重新变为接地,测试所述待测试MOS晶体管处于正常工作状态下的对应参数值,将所述参数值与初值参数值进行比较,获得对应参数值的退化幅度值,判断所述退化幅度值是否已达到失效标准。如此反复,直到对应参数值的退化幅度值达到失效标准,获得对应的失效时间。所述测试方法在施加电压应力和参数值测试时,分别改变施加在第一测试端、第二测试端的电压,控制二极管的导通或截止,使得在施加电压应力时,加热单元工作,对应的待测试MOS晶体管的温度提高到正常工作时候的温度(例如接近125℃),有利于提高测试精确度,当进行参数值测试时,二极管截止,利用所述漏极工作电压进行参数值测试时对应获得的电流为待测试MOS晶体管的漏极电流,所述加热单元不会影响待测试MOS晶体管的参数值测试,且不需要提供额外的加热装置,有利于降低测试成本。本发明虽然已以较佳实施例公开如上,但其并不是用来限定本发明,任何本领域技术人员在不脱离本发明的精神和范围内,都可以利用上述揭示的方法和技术内容对本发明技术方案做出可能的变动和修改,因此,凡是未脱离本发明技术方案的内容,依据本发明的技术实质对以上实施例所作的任何简单修改、等同变化及修饰,均属于本发明技术方案的保护范围。