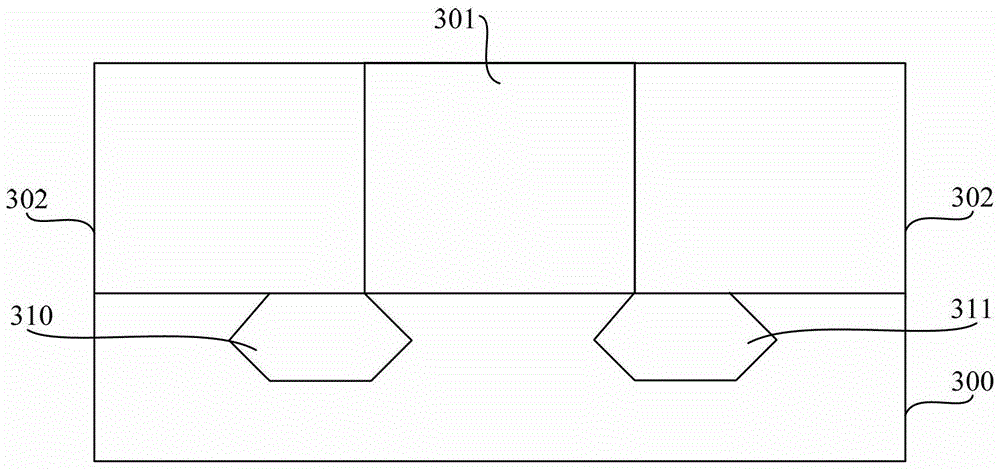
本发明涉及半导体技术领域,尤其涉及一种晶体管的形成方法。
背景技术:随着半导体技术的不断发展,MOS晶体管的特征尺寸不断缩小,MOS晶体管的栅介质层的厚度也按等比例缩小的原则变得越来越薄。当所述栅介质层的厚度薄到一定的程度后,其可靠性问题,尤其是与时间相关的击穿、热载流子效应、栅电极中的杂质向衬底的扩散等问题,将严重影响器件的稳定性和可靠性。现在,SiO2层作为栅介质层已经达到其物理厚度极限,利用高K栅介质层替代SiO2栅介质层,可以在保持等效氧化层厚度(EOT,EquivalentOxideThickness)不变的情况下大大增加栅介质层的物理厚度,从而减小了栅极漏电流。但是由于高K栅介质层大多是金属离子氧化物,且没有固定的原子配位,其与硅衬底之间键合的稳定程度较SiO2与硅衬底之间键合的稳定程度相比要差得多,造成高K栅介质层与硅衬底之间具有大量的界面缺陷。在现有技术中,一种典型的金属栅结构包括:界面层(interfaciallayer,IL)、位于界面层上的高K栅介质层、位于高K栅介质层上的金属栅极。在这种情况下,等效氧化层厚度(EOT)等于等效界面层厚度加等效高K栅介质层厚度。由于界面层的厚度已经达到物理极限,现有技术通过降低高K栅介质层的厚度来降低等效氧化层厚度。降低高K栅介质层的厚度可以提高沟道区中载流子的迁移率,抑制短沟道效应。但随着半导体工艺技术节点不断降低,尤其是从32nm技术节点进入22nm,甚至更低,现有技术为获得较低的等效氧化层厚度而减小高K栅介质层的物理厚度的空间也越来越小,沟道区中载流子的迁移率逐渐降低,栅极漏电流增加。由此,制造的晶体管的性能也降低了。更多关于等效氧化层厚度的知识,请参照2010年9月29日公开的公开号为CN101290880B的中国专利文献。
技术实现要素:本发明解决的问题是,现有技术为获得较低的等效氧化层厚度而减小高K栅介质层的物理厚度的空间也越来越小。由此,制造的晶体管的性能也降低了。为解决上述问题,本发明提供一种新的晶体管的形成方法,包括:提供具有伪栅极的半导体衬底,在半导体衬底上形成有层间介质层;去除所述伪栅极,形成第一沟槽;在所述第一沟槽底部形成氧化硅层,作为界面层;形成氧化硅层后,在所述第一沟槽中形成位于所述氧化硅层上的高K栅介质层、位于所述高K栅介质层上的氮化钛层,填充部分深度的第一沟槽;对所述氮化钛层进行吸氧物质掺杂;对所述氮化钛层进行吸氧物质掺杂后,形成多晶硅层,填充第一沟槽;去除所述多晶硅层,形成第二沟槽;在所述第二沟槽中形成导电物质,作为栅极。可选地,对所述氮化钛层进行吸氧物质掺杂的方法为物理气相沉积法,其中,在沉积反应腔内的温度范围为0℃~500℃。可选地,所述氮化钛层中的吸氧物质的质量浓度范围为0.01%~10%。可选地,所述吸氧物质包括铜、铁、钴、锌、锡或锰中的一种或多种。可选地,所述形成多晶硅层的方法为化学气相沉积法,其中,在沉积反应腔内温度范围为400℃~600℃。可选地,所述去除多晶硅层的方法,包括:在所述层间介质层上形成图形化的掩模层,定义第一沟槽中多晶硅层的位置;以所述图形化的掩模层为掩模,刻蚀去除第一沟槽中的多晶硅层;去除图形化的掩模层。可选地,形成高K栅介质层和氮化钛层的方法,包括:沉积高K介质层、氮化钛材料层,覆盖所述层间介质层、填充第一沟槽;去除高出层间介质层的高K介质层、氮化钛材料层,在所述氧化硅层上形成高K栅介质层和位于高K栅介质层上的氮化钛层。可选地,去除高出层间介质层的高K介质层、氮化钛材料层的方法,包括化学机械抛光或回刻工艺。可选地,所述高K介质层的材料包括氧化铬或氧化锆。可选地,在所述半导体衬底上形成层间介质层之前,在所述伪栅极两侧的半导体衬底中形成源极和漏极。可选地,所述形成源极和漏极的方法,包括:在所述伪栅极两侧的半导体衬底中形成sigma形凹槽;在所述sigma形凹槽中形成半导体材料;在所述半导体材料中进行离子注入形成源极和漏极。可选地,所述去除伪栅极还包括,去除所述伪栅极下部分深度的半导体衬底,形成第一沟槽的底部处于sigma形凹槽的尖角与半导体衬底表面之间。可选地,若晶体管为P型晶体管,所述半导体材料为锗硅;若晶体管为N型晶体管,所述半导体材料为碳硅。可选地,形成所述氧化硅层的方法,包括热氧化生长法或化学气相沉积。可选地,去除所述伪栅极的方法,包括:在层间介质层上形成图形化的光刻胶层,定义所述伪栅极的位置;以所述图形化的光刻胶层为掩模,干法刻蚀去除所述伪栅极,形成第一沟槽;去除图形化的光刻胶层;使用湿法腐蚀去除所述干法刻蚀中在第一沟槽侧壁和底部产生的聚合物。与现有技术相比,本发明具有以下优点:本发明在半导体衬底上形成伪栅极和覆盖衬底的层间介质层后,去掉伪栅极,形成第一沟槽;之后,在所述第一沟槽中形成占第一沟槽部分深度的氧化硅层、位于氧化硅层上的高K栅介质层和位于高K栅介质层上的氮化钛层;接着,对氮化钛层进行吸氧物质掺杂;紧接着,在第一沟槽的氮化钛层上形成多晶硅层。在形成多晶硅层过程中,多晶硅层用于阻挡外界环境的氧与氮化钛层中的吸氧物质发生氧化反应,并且,在形成多晶硅层的过程中,高K栅介质层中出现快速移动的氧空穴,氧化硅层中的氧原子进入高K栅介质层,并随氧空穴在高K栅介质层中移动。在到达高K栅介质与氮化钛层的界面处,大部分氧原子受到吸氧物质层的“吸引”而进入到氮化钛层,氧原子与吸氧物质反应,通过化学键结合生成稳定物质。而与此同时,氧化硅层中的氧损失,其中的硅又会与衬底重新结合而成为衬底的一部分。氧化硅层中的氧损失,使得氧化硅层的厚度减小,进而使得等效氧化层厚度减。与现有技术的高K栅介质层技术相比,本发明的等效氧化层厚度降到0.5nm以下,最终稳定并提升了沟道区中载流子的迁移率,抑制漏电流的产生。附图说明图1是本发明具体实施例的晶体管形成方法的流程示意图;图2~图8是本发明具体实施例的晶体管形成方法的剖面结构示意图。具体实施方式为使本发明的上述目的、特征和优点能够更加明显易懂,下面结合附图对本发明的具体实施方式做详细的说明。在下面的描述中阐述了很多具体细节以便于充分理解本发明,但是本发明还可以采用其他不同于在此描述的其它方式来实施,因此本发明不受下面公开的具体实施例的限制。参照图2,并结合参照图1,执行步骤S11,提供具有伪栅极301的半导体衬底300,在半导体衬底300上形成有层间介质层302。在具体实施例中,半导体衬底300的材料可以包括单晶、多晶或非晶结构的硅或硅锗(SiGe),也可以包括混合的半导体结构,例如碳化硅(SiC)、锑化铟、碲化铅、砷化铟、磷化铟、砷化镓或锑化镓、合金半导体或其组合;也可以是绝缘体上硅(SOI)或其他材料,在此不再一一列举。在具体实施例中,所述伪栅极301的材料可以选择多晶硅、无定形碳或氮化硅。形成所述伪栅极301的方法,包括:在半导体衬底300上形成刻蚀阻挡层(未示出),所述刻蚀阻挡层通常选择氧化硅,在后续刻蚀伪栅极层过程中起到刻蚀阻挡作用;沉积形成覆盖刻蚀阻挡层的伪栅极层;图形化所述伪栅极层,形成伪栅极301。其中,图形化所述伪栅极层的方法,可以为:在伪栅极层上形成硬掩模材料;图形化所述硬掩模材料,在待形成的伪栅极位置形成硬掩模层;以硬掩模层为掩模,刻蚀伪栅极层,至刻蚀阻挡层停止,剩余硬掩模层下的伪栅极层为伪栅极301。硬掩模层可以选择去除,也可以保留,在后续工艺中起到掩模作用。此为本领域技术人员所熟知的技术,在此不再赘述。在具体实施例中,在衬底300上形成层间介质层302的方法,包括:化学气相沉积,形成覆盖半导体衬底300、伪栅极301的介质层;化学机械抛光或回刻工艺或其他可选工艺,去除高出伪栅极301表面的介质层,形成层间介质层302。若在其他实施例中,在伪栅极301上还形成有硬掩模层,则去除高出硬掩模层表面的介质层,形成层间介质层。层间介质层的材料通常选择氧化硅。在具体实施例中,在形成层间介质层302之前,还要在伪栅极301两侧的半导体衬底300中进行离子注入,形成源极310和漏极311。在本实施例中,形成源极和漏极的方法引入嵌入式锗硅技术,包括:在半导体衬底300两侧的半导体衬底中形成sigma形凹槽;在sigma形凹槽中形成半导体材料;在所述半导体材料中进行离子注入形成源极310和漏极311。在具体实施例中,当晶体管为P型晶体管,半导体材料为锗硅,锗硅为沟道区提供压应力;当晶体管为N型晶体管,半导体材料为碳硅,碳硅为沟道区提供张应力。嵌入式锗硅技术的应用,可以明显提高沟道区中载流子的迁移率,提升晶体管的性能。参照图2和图3,并结合参照图1,执行步骤S12,去除伪栅极301,形成第一沟槽303。在具体实施例中,去除伪栅极301的方法,包括:在层间介质层302上形成图形化的光刻胶层,定义伪栅极301的位置;以图形化的光刻胶层为掩模,干法刻蚀去除伪栅极301,形成第一沟槽303,在该过程产生聚合物,该聚合物附着在第一沟槽303底部和侧壁;接着,去除图形化的光刻胶层;使用湿法腐蚀去除干法刻蚀中产生的聚合物。当本发明引入嵌入式锗硅技术,可选的,执行步骤S12去除伪栅极301中,还可以继续去除伪栅极301下的半导体衬底300,使得第一沟槽303的底部处于sigma形凹槽的尖角与半导体衬底300表面之间,大约地,第一沟槽303底部位于半导体衬底300表面下小于等于100nm处。由于靠近Sigma形凹槽的尖角处的半导体材料能够提供较大的应力,将第一沟槽303的底部处于sigma形凹槽的尖角与半导体衬底300表面之间,相对地将沟道区与栅介质层的界面下移,沟道区下移,沟道区受到较大应力作用,沟道区中载流子的迁移率得到提高,进一步提升晶体管的性能。参照图4,并结合参照图1,执行步骤S13,在第一沟槽303底部形成氧化硅层304,作为界面层(interfaciallayer,IL)。该界面层不仅能在衬底和界面层之间提供较佳品质的界面,还能在高K栅介质层和界面层之间提供较佳品质的界面,从而改善后续高K栅介质层与衬底之间的界面特性,进而提高晶体管的电学性能。在具体实施例中,在第一沟槽303底部形成氧化硅层304的方法包括热氧化生长法或化学气相沉积。热氧化生长法为公知的技术,不再赘述。若使用化学气相沉积,形成覆盖层间介质层302、填充第一沟槽303的介质层,之后,去除高出层间介质层302的介质层,在第一沟槽303底部和侧壁形成氧化硅层,作为界面层。参照图5,并结合参照图1,执行步骤S14,形成氧化硅层304后,在第一沟槽303中形成位于氧化硅层304上的高K栅介质层305、位于高K栅介质层305上的氮化钛层306,填充部分深度的第一沟槽303。高K栅介质层305除了覆盖氧化硅层304外,还覆盖第一沟槽303的侧壁。当然的,氮化钛层306也形成在第一沟槽303侧壁的高K栅介质层上。在本步骤,氧化硅层304、高K栅介质层305和氮化钛层306组成的叠层结构,并未填充满第一沟槽303。在具体实施例中,形成高K栅介质层305、氮化钛层306的方法,包括:沉积高K介质层、氮化钛材料层,覆盖层间介质层302、填充第一沟槽303;去除高出层间介质层302的高K介质层、氮化钛材料层,在氧化硅层304上形成高K栅介质层305和位于高K栅介质层305上的氮化钛层306。其中,在第一沟槽303侧壁上也形成有高K栅介质层和位于高K栅介质层上的氮化钛层。在具体实施例中,去除方法可选择化学机械抛光(CVD)或回刻工艺。在具体实施例中,高K栅介质层305的材料选择氧化铬或氧化锆。一方面,氮化钛层306可以阻挡氧化硅层304中的氧经高K栅介质层扩散至栅极,也阻止栅极中的元素向高K栅介质层扩散。另一方面,在本发明中,氮化钛层306是“接收”氧化硅层304中氧的“容器”,这会在后续步骤中说明。继续参照5,并结合参照图1,执行步骤S15,对氮化钛层306进行吸氧物质掺杂。在本实施例中,在同一条件下,吸氧物质与氧结合的能力大于硅与氧结合的能力,这样,在后续步骤中,氧化硅层304中的氧就会被“吸引”至氮化钛层306中而与吸氧物质结合。在具体实施例中,对氮化钛层306进行吸氧物质掺杂的方法,可以选择物理气相沉积(PVD)法,例如溅射法、离子镀等。首先,在层间介质层302上形成图形化的掩模层,定义氮化钛层306的位置;以图形化的掩模层为掩模,对氮化钛层306进行物理气相沉积,形成吸氧物质掺杂,在该过程中,沉积反应腔内的温度范围为0℃~500℃,可以保证吸氧物质可以对氮化钛层306形成掺杂。最终,在氮化钛层306中的吸氧物质的质量浓度范围为0.01%~10%。由于未进行掺杂的氮化钛层306不具备“吸引”氧而与氧结合的能力,而吸氧物质可以在后续沉积多晶硅过程中的高温条件下与氧结合。氮化钛层306充当了吸氧物质与氧结合的媒介作用。在本实施例中,吸氧物质为金属,包括铜、铁、钴、锌、锡或锰中的一种或多种。参照图5和图6,并结合参照图1,执行步骤S16,对氮化钛层306进行吸氧物质掺杂后,形成多晶硅层307,填充第一沟槽303。在具体实施例中,形成多晶硅层307的方法,使用化学气相沉积,其中,在沉积反应腔内提供的温度范围为400℃~600℃。使用化学气相沉积,形成的多晶硅层307不仅填充第一沟槽303,也覆盖层间介质层302。在沉积多晶硅层过程中,多晶硅层307用于阻挡外界环境中的氧与氮化钛层306中的吸氧物质发生氧化反应。在400℃~600℃的较高温度下,氧化硅层304中的氧与硅分离,扩散进入高K栅介质层305。在较高温度下,高K栅介质层中出现快速移动的氧空穴,氧化硅层304中的氧原子进入高K栅介质层,并随氧空穴在高K栅介质层中移动。在到达高K栅介质层305与氮化钛层306的界面处,大部分氧原子受到吸氧物质层的“吸引”而进入到氮化钛层306中,氧原子与吸氧物质反应,通过化学键结合生成稳定物质。而与此同时,氧化硅层304中的氧损失,其中的硅又会与衬底300重新结合而成为衬底300的一部分。氧化硅层304中的氧损失,使得氧化硅层304的厚度减小,进而使得等效氧化层厚度减。与现有技术的高K栅介质层技术相比,本发明的等效氧化层厚度降到0.5nm以下,最终稳定并提升了沟道区中载流子的迁移率,抑制漏电流的产生。在本实施例中,对沉积多晶硅层温度范围限制在400℃~600℃,一方面是沉积形成多晶硅层的要求。另一方面,在400℃~600℃下,氧化硅层304中的氧易分离,高K栅介质层305中的氧空穴可以形成稳定的移动,氧化硅层304中分离的氧在高K栅介质层305中也形成稳定移动扩散。而且,该温度范围提供了足够的能量促使氧与吸氧物质发生反应,并抑制了氧与氧化硅层304中的硅的结合重生成氧化硅。若温度高于600℃,也不会对氧空穴、氧的移动产生更积极的效果,反而会影响多晶硅层307的沉积形成。继续参照图6和图7,并结合参照图1,执行步骤S17,去除多晶硅层307,形成第二沟槽308。在具体实施例中,由于使用化学气相沉积,多晶硅层303也覆盖层间介质层302。所以,去除多晶硅层307的步骤:首先,去除高出层间介质层302的多晶硅层部分,可以使用化学机械抛光或回刻工艺;然后,在层间介质层302上形成图形化的掩模层,可以选择光刻胶,定义第一沟槽中多晶硅层的位置;以图形化的掩模层为掩模,刻蚀去除第一沟槽中的多晶硅层;去除图形化的掩模层。参照图7和图8,并结合参照图1,执行步骤S18,在形成第二沟槽308后,在第二沟槽308中形成导电物质309,作为栅极。其中,导电物质309的材料可以为金属,包括Al、Cu、Ag、Au、Pt、Ni、Ti、TiN、TaN、Ta、TaC、TaSiN、W、WN、WSi的一种或多种。除了金属外,还可包括其他可行材料。本发明虽然已以较佳实施例公开如上,但其并不是用来限定本发明,任何本领域技术人员在不脱离本发明的精神和范围内,都可以利用上述揭示的方法和技术内容对本发明技术方案做出可能的变动和修改,因此,凡是未脱离本发明技术方案的内容,依据本发明的技术实质对以上实施例所作的任何简单修改、等同变化及修饰,均属于本发明技术方案的保护范围。