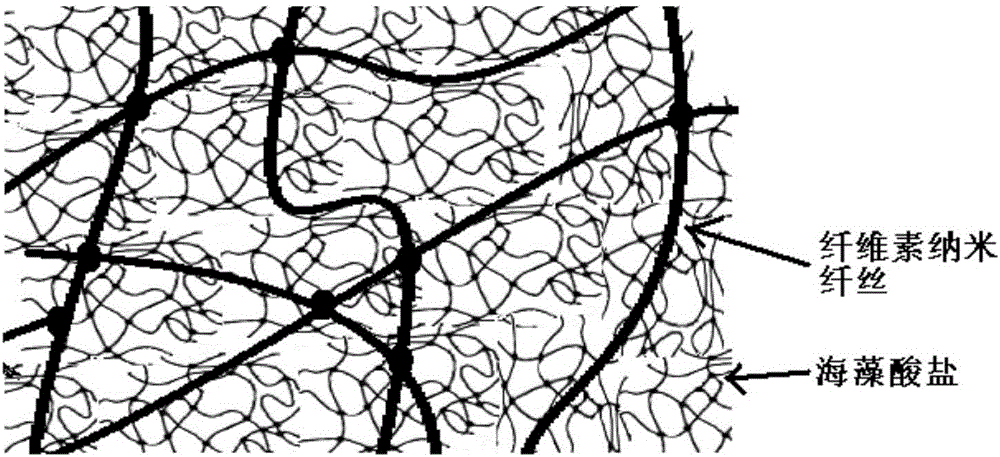
本发明涉及一种海藻酸盐复合纤维的生产方法,尤其涉及一种纤维素纳米纤丝/海藻酸盐复合纤维的制备方法。
背景技术:
:纯海藻酸盐纤维普遍存在强度较低、脆性较大、可纺性差、物理综合性能指标不佳的问题,这直接限制了海藻酸盐纤维的应用开发。因此,生产高强度海藻酸盐纤维,提高其综合物理机械性能指标,是海藻纤维生产中需要解决的重点问题之一。现有技术中,普遍采用的解决办法是采用共聚、共混或者添加无机纳米材料方式等增强海藻酸盐纤维。其中:共聚手段不仅工艺复杂,且有化学反应参与,需使用较多化学药品,经化学反应后,得到的纤维,不可避免地将失去海藻酸钠天然的优异的绿色环保性能,用于医疗卫生用材料时还存在安全性问题;添加无机纳米材料制备海藻酸盐复合纤维,目前主要是使用碳纳米管或碳纳米管与石墨烯的混合物,加入碳纳米管虽然能提高海藻酸盐纤维强度,但对纤维断裂伸长率有不良影响,造成纤维的柔韧性进一步降低;虽然加入碳纳米管和氧化还原石墨烯的混合物时可形成网络结构,对海藻酸盐纤维有增强增韧效果,但其成本较高,生物降解性较差,将会限制其在组织工程支架等医学材料中的应用;添加胶原、明胶、聚乙烯醇、粘胶溶液等制备的共混纤维,虽然对海藻酸盐纤维具有一定增强作用,亦不会影响海藻酸盐纤维的体内安全性和体内降解性,但该方法属于两种高分子的简单共混,现有报道未显示有对添加物进行取向调控的技术,且该方法有时还存在易分相、添加化学助剂等问题,如添加粘胶溶液制备共混纤维时,制备粘胶溶液涉及到复杂的工艺过程并使用大量的化学药品;中国专利申请CN103741257B公开了一种丙烯酰胺类网络增强海藻酸钙纤维,该方法中使用丙烯酰胺类化合物、引发剂、交联剂等化学试剂,通过化学反应来形成共价交联的网络结构。虽然其所制得的纤维强度高,且可通过改变反应条件调控强度,但因其添加化学试剂、有共价交联等因素,导致复合纤维的生物安全性和体内降解性受到影响,同样会限制其在组织工程支架等医疗卫生材料方面的应用。技术实现要素:本发明的目的是,提供一种绿色环保的纤维素/海藻酸盐复合纤维的生产方法,所制备出的复合纤维具有良好的生物降解性能和综合物理性能指标,适于组织工程支架等医疗卫生材料方面的应用。本发明为实现上述目的,所采用的技术方案是,一种纤维素纳米纤丝/海藻酸盐复合纤维的制备方法,其特征在于,包括以下步骤:第一步,原料制备取纤维素纳米纤丝,加入去离子水,在超声波作用下分散均匀,配制成浓度为1~5wt%的凝胶状纤维素纳米纤丝悬浮液,备用;边搅拌边将海藻酸钠粉末加入去离子水中,静置3h,待海藻酸钠充分溶胀后,继续搅拌4h,配制成质量百分比浓度为4~8%的海藻酸钠溶液,滤除杂质后,备用;第二步,纺丝原液的制备按质量比1~10︰100的比例,边搅拌边将上述凝胶状纤维素纳米纤丝悬浮液缓慢加入到海藻酸钠溶液中,并持续进行超声波分散处理20~90min,配制出纤维素纳米纤丝/海藻酸钠混合溶液;然后,将纤维素纳米纤丝/海藻酸钠混合溶液静置8h,脱泡后得到纺丝原液;第三步,纺丝成形将所得纺丝原液经喷丝板挤出,形成的丝条在第一道牵伸下,经过凝固浴凝固成形,得到初生纤维;上述凝固浴为质量百分比为浓度为1%~8%的氯化钙、氯化锌、氯化铁、氯化铜或氯化镁溶液;凝固浴的温度为10℃~60℃,第一道牵伸的牵伸比为100~300%;第四步,塑化牵伸在牵伸机的牵伸下,初生纤维进入沸水浴中进行塑化牵伸,塑化牵伸比为120%,得到纤维素纳米纤丝/海藻酸钙复合纤维半成品;第五步,后处理将所得纤维素纳米纤丝/海藻酸钙复合纤维半成品,依次经水洗、上油、干燥后,即得成品。上述技术方案直接带来的技术效果是,制备工艺简单,在海藻酸钠原料中引入用作增强相的是纤维素纳米纤丝(具有高比表面积、高结晶度、高杨氏模量、高强度等特性,且质轻、可再生、生物相容性好等特点),所制得的纤维素纳米纤丝/海藻酸钙复合纤维内部呈三维网络结构,具有较好的强度和韧性。详细说明如下:纤维素纳米纤丝从天然纤维素纤维中分离得到,化学成分是纤维素分子,其结构单元为C~6羟基被部分氧化成羧基的葡萄糖,与海藻酸的组成结构海藻多糖极为相似,因此,二者相容性良好,不管是在共混溶液中,还是复合纤维中,均不易产生分相问题。纤维素纳米纤丝与海藻酸钠二者的共混溶液作为纺丝原液,在超声波分散和机械搅拌过程中,以及湿法纺丝过程中受到多重剪切力作用,在这些力的作用下,纤维素纳米纤丝的取向可发生改变,且改变剪切力如机械搅拌速度、搅拌时间、喷丝速度等均可改变纤维素纳米纤丝在海藻酸钠溶液中的取向,但复合纤维干燥后,这种取向便会固定下来。在纤维经凝固浴成型后且干燥之前受到的牵伸作用,可进一步调整纤维素纳米纤丝在复合纤维中的取向。当混合溶液即纺丝原液从喷丝孔挤出、在凝固浴中成型并经干燥后,海藻酸依靠分子上的羧基形成海藻酸钙、海藻酸镁、海藻酸锌等离子交联网络,纤维素纳米纤丝依靠其高长径比的长丝状结构、纤维素纳米纤丝表面的羟基和羧基产生的氢键作用形成三维网状结构,同时海藻酸与部分氧化的纤维素分子中均含有羟基和羧基,他们之间除了可以形成氢键作用外,亦可共同与钙、镁、锌等离子形成离子交联,从而海藻酸盐离子交联网络与纤维素纳米纤丝的氢键结合三维网络形成了互穿网络结构。上述技术方案所制备出的纤维素纳米纤丝/海藻酸盐复合纤维,借助纤维素纳米纤丝的网络结构与海藻酸盐的离子交联网络形成的互穿结构(参见说明书附图2),其拉伸断裂强度较纯海藻酸盐纤维提高了52.9%,断裂伸长率提高了52.6%。因此,本发明的纤维素纳米纤丝/海藻酸盐复合纤维属于高强度海藻酸盐纤维,且具有良好的柔韧性。优选为,上述纤维素纳米纤丝的长径比大于50。该优选技术方案直接带来的技术效果是,纤维素纳米纤丝作为纳米材料,其本身的比表面积巨大,纤维表面暴露出大量的羟基和部分羧基,纤丝之间形成强烈的氢键作用。选择长径比大于50的纤维纳米纤丝,将使得纤维素纳米纤丝形成更优异的网络交织结构,尤其是把其中的水分脱除后,这种靠氢键结合的网络缠结结构会变得更加牢固选择长径比大于50的纤维纳米纤丝所制得的复合纤维具有高强度和高模量,可用作防弹衣和电子行业如耳机膜材料等的制备原料。进一步优选,上述海藻酸钠的重均分子量为2.0×104~7.0×104。该优选技术方案直接带来的技术效果是,海藻酸钠分子量对纺丝加工的难易程度、纺丝所得纤维的强度、纤维的体内降解性和血液相容性具有重要影响。通常情况下,海藻酸钠分子量越高,纺丝所得纤维强度越高,但纺丝液粘度大,纺丝加工困难,纤维体内降解性差。因此,选择中等分子量的海藻酸钠原料,且中等分子量的海藻酸钠具有良好的血液相容性,在生物材料中应用潜力较大。进一步优选,上述纤维素纳米纤丝是以来自植物、动物或微生物的天然纤维素为原料,经2,2,6,6-四甲基哌啶-1-氧基、二氧化氮的磷酸水溶液、氯酸钠、溴酸钠、亚氯酸钠的磷酸溶液、亚硝酸钠或硝酸钠的磷酸溶液对纤维素葡萄糖环C~6位羟基选择性氧化后,再经物理机械作用分离出来的。该优选技术方案直接带来的技术效果是,采用预氧化加机械分离的方法制备出的纤维素纳米纤丝,结晶区与无定形区共存,可有效保留纤维素原料所具有的良好的刚性与韧性,用在复合材料中弹性、抗冲击性、抗弯性能表现较好,优于采用化学降解法制备的只含结晶区的纤维素纳米晶体,以及碳纳米管等其它纳米增强剂。并且,由于采用预氧化加机械分离的方法制备出的纤维素纳米纤丝,其表面不仅有羟基,在C~6位还有羧基存在。因此,上述技术方案所制得的纤维素纳米纤丝/海藻酸盐复合纤维,不仅改善了海藻酸盐纤维的强度和柔韧性,而且,纤维素纳米纤丝/海藻酸盐复合纤维具有良好的生物安全性、体内降解性、绿色环保性,可满足组织工程支架等医疗卫生材料的原料要求。这是因为,虽然纤维素材料体内降解性较差,但采用氧化剂部分氧化后分离出来的纤维素纳米纤丝,经羧基化改性后,大大提高了纤维素纳米纤丝的体内降解性能,且纤维素纳米纤丝之间以及纤维素纳米纤丝与海藻酸盐之间为氢键和离子键交联,对复合纤维体内降解性的影响显著低于共价交联。附表1:采用预氧化加机械分离的方法制备出的纤维素纳米纤丝与其它增强体材料的机械性能对比情况表。增强体材料弹性模量/GPa拉伸强度/GPa纤维素纳米纤丝1507.5纤维素纤维(亚麻)270.81Kevlar491253.5碳纤维1503.5碳纳米管30020不锈钢2000.5综上所述,本发明相对于现有技术,具有以下有益效果:1、本发明的纤维素纳米纤丝/海藻酸盐复合纤维产品,其基体和增强相材料均为以存量丰富的生物质资源为原料,具有轻质、可降解、生物相容及可再生等特性,符合未来材料发展方向。2、本发明的工艺简单易操作,制备过程未添加其它化学助剂,工艺绿色环保。3、本发明的纤维素纳米纤丝/海藻酸盐复合纤维既改善了海藻酸盐纤维的强度和柔韧性,又未影响其生物安全性、体内降解性、绿色环保性等优秀性能,可满足组织工程支架等医疗卫生材料的原料要求。附图说明图1为实施例1所制得的纤维素纳米纤丝/海藻酸盐复合纤维的红外光谱图;图2为本发明的纤维素纳米纤丝/海藻酸盐复合纤维的微观网络结构示意图。具体实施方式下面结合实施例和附图,对本发明进行详细说明。说明:1、以下各实施例中,所使用的纤维素纳米纤丝均是以来自植物、动物或微生物的天然纤维素为原料,采用2,2,6,6-四甲基哌啶-1-氧基、二氧化氮的磷酸水溶液、氯酸钠、溴酸钠、亚氯酸钠的磷酸溶液、亚硝酸钠或硝酸钠的磷酸溶液对纤维素葡萄糖环C~6位羟基选择性氧化后,再经物理机械作用分离出来的。2、以下各实施例中,所使用的海藻酸钠(原料)为市售产品,重均分子量为2.0×104~7.0×104。实施例1在超声波作用下,将长径比大于50的纤维素纳米纤丝均匀分散在去离子水中,配制成2wt%浓度的凝胶状悬浮液,备用。称取海藻酸钠溶于去离子水中,静置3h,使海藻酸钠充分溶胀,再搅拌4h,配制成质量百分比为4%的海藻酸钠溶液,过滤备用。按质量比1︰100的比例,边搅拌边将上述凝胶状纤维素纳米纤丝悬浮液缓慢加入到海藻酸钠溶液中,并持续进行超声波分散处理20min,配制出纤维素纳米纤丝/海藻酸钠混合溶液;静置8h脱泡后形成纺丝原液。纺丝原液经湿法纺丝设备以10m/min的速度挤入25℃的凝固浴,喷丝孔直径为0.33mm,凝固浴是浓度为5%的氯化钙溶液。以一定速度经过第一道凝固浴的初生纤维进入沸水浴中进行第二道拉伸。经过第一道凝固浴时牵伸倍率为150%,第二道沸水浴为120%牵伸。所得纤维再经过水洗、干燥后获得纤维素纳米纤丝/海藻酸钙复合纤维。产品检测与检验结果:拉伸断裂强度为2.51cN/dtex,断裂伸长率为9.88%,在磷酸盐缓冲溶液中降解14天的失重率为58%。实施例2在超声波作用下,将长径比大于50的纤维素纳米纤丝均匀分散在去离子水中,配制成2wt%浓度的凝胶状悬浮液,备用。称取海藻酸钠溶于去离子水中,静置3h,使海藻酸钠充分溶胀,再搅拌4h,配制成质量百分比为4%的海藻酸钠溶液,过滤备用。按质量比3︰100的比例,边搅拌边将上述凝胶状纤维素纳米纤丝悬浮液缓慢加入到海藻酸钠溶液中,并持续进行超声波分散处理20min,配制出纤维素纳米纤丝/海藻酸钠混合溶液;静置8h脱泡后形成纺丝原液。纺丝原液经湿法纺丝设备以10m/min的速度挤入25℃的凝固浴,喷丝孔直径为0.45mm,凝固浴是浓度为5%的氯化钙溶液。以一定速度经过第一道凝固浴的初生纤维进入沸水浴中进行第二道拉伸。经过第一道凝固浴时牵伸倍率为150%,第二道沸水浴为120%牵伸。所得纤维再经过水洗、干燥后获得纤维素纳米纤丝/海藻酸钙复合纤维。产品检测与检验结果:拉伸断裂强度为3.11cN/dtex,断裂伸长率为11.87%,在磷酸盐缓冲溶液中降解14天的失重率为51%。实施例3在超声波作用下,将长径比大于50的纤维素纳米纤丝均匀分散在去离子水中,配制成2wt%浓度的凝胶状悬浮液,备用。称取海藻酸钠溶于去离子水中,静置3h,使海藻酸钠充分溶胀,再搅拌4h,配制成质量百分比为4%的海藻酸钠溶液,过滤备用。按质量比5︰100的比例,边搅拌边将上述凝胶状纤维素纳米纤丝悬浮液缓慢加入到海藻酸钠溶液中,并持续进行超声波分散处理60min,配制出纤维素纳米纤丝/海藻酸钠混合溶液;静置8h脱泡后形成纺丝原液。纺丝原液经湿法纺丝设备以10m/min的速度挤入25℃的凝固浴,喷丝孔直径为0.65mm,凝固浴是浓度为5%的氯化钙溶液。以一定速度经过第一道凝固浴的初生纤维进入沸水浴中进行第二道拉伸。经过第一道凝固浴时牵伸倍率为150%,第二道沸水浴为120%牵伸。所得纤维再经过水洗、干燥后获得纤维素纳米纤丝/海藻酸钙复合纤维。产品检测与检验结果:拉伸断裂强度为2.35cN/dtex,断裂伸长率为12.24%,在磷酸盐缓冲溶液中降解14天的失重率为44%。实施例4在超声波作用下,将长径比大于50的纤维素纳米纤丝均匀分散在去离子水中,配制成2wt%浓度的凝胶状悬浮液,备用。称取海藻酸钠溶于去离子水中,静置3h,使海藻酸钠充分溶胀,再搅拌4h,配制成质量百分比为4%的海藻酸钠溶液,过滤备用。按质量比10︰100的比例,边搅拌边将上述凝胶状纤维素纳米纤丝悬浮液缓慢加入到海藻酸钠溶液中,并持续进行超声波分散处理90min,配制出纤维素纳米纤丝/海藻酸钠混合溶液;静置8h脱泡后形成纺丝原液。纺丝原液经湿法纺丝设备以10m/min的速度挤入25℃的凝固浴,喷丝孔直径为0.95mm凝固浴是浓度为5%的氯化钙溶液。以一定速度经过第一道凝固浴的初生纤维进入沸水浴中进行第二道拉伸。经过第一道凝固浴时牵伸倍率为150%,第二道沸水浴为120%牵伸。所得纤维再经过水洗、干燥后获得纤维素纳米纤丝/海藻酸钙复合纤维。产品检测与检验结果:拉伸断裂强度为2.28cN/dtex,断裂伸长率为13.71%,在磷酸盐缓冲溶液中降解14天的失重率为36%。选取实施例1作为代表性实施例,将所制得的纤维素纳米纤丝/海藻酸盐复合纤维进行红外光谱检测,所得图谱为图1。从图1从可以看出:纯的纤维素纳米纤丝在3415cm-1处显示了一个吸收峰(曲线NCF),这是由于纤维素分子上-OH基和因羟基部分氧化而产生的羧基中O-H键伸缩振动引起的;纯的海藻酸盐纤维在3421cm-1附近形成了一个较宽的吸收带(曲线A),可归属于羧基中O-H键的伸缩振动。在纤维素纳米纤丝/海藻酸盐复合纤维的红外光谱图中(曲线NCF/A),羟基的特征吸收峰明显变强,并向低波数位移,C-O键的伸缩振动吸收峰也由1630cm-1位移到1410cm-1,说明纤维素纳米纤丝与海藻酸盐间形成了氢键结合,二者表现出了良好的相容性。这种相互作用改善了复合纤维的力学性能。为更好地理解本发明的技术特点,下面结合本发明的纤维素纳米纤丝/海藻酸盐复合纤维的微观网络结构示意图作进一步的说明。如图2所示,海藻酸依靠分子上的羧基形成海藻酸钙、海藻酸镁、海藻酸锌等离子交联网络,纤维素纳米纤丝依靠其高长径比的长丝状结构、纤维素纳米纤丝表面的羟基和羧基产生的氢键作用形成三维网状结构,同时海藻酸与部分氧化的纤维素分子中均含有羟基和羧基,它们之间除了可以形成氢键作用外,亦可共同与钙、镁、锌等离子形成离子交联,从而海藻酸盐离子交联网络与纤维素纳米纤丝的氢键结合三维网络形成了互穿网络结构。当前第1页1 2 3