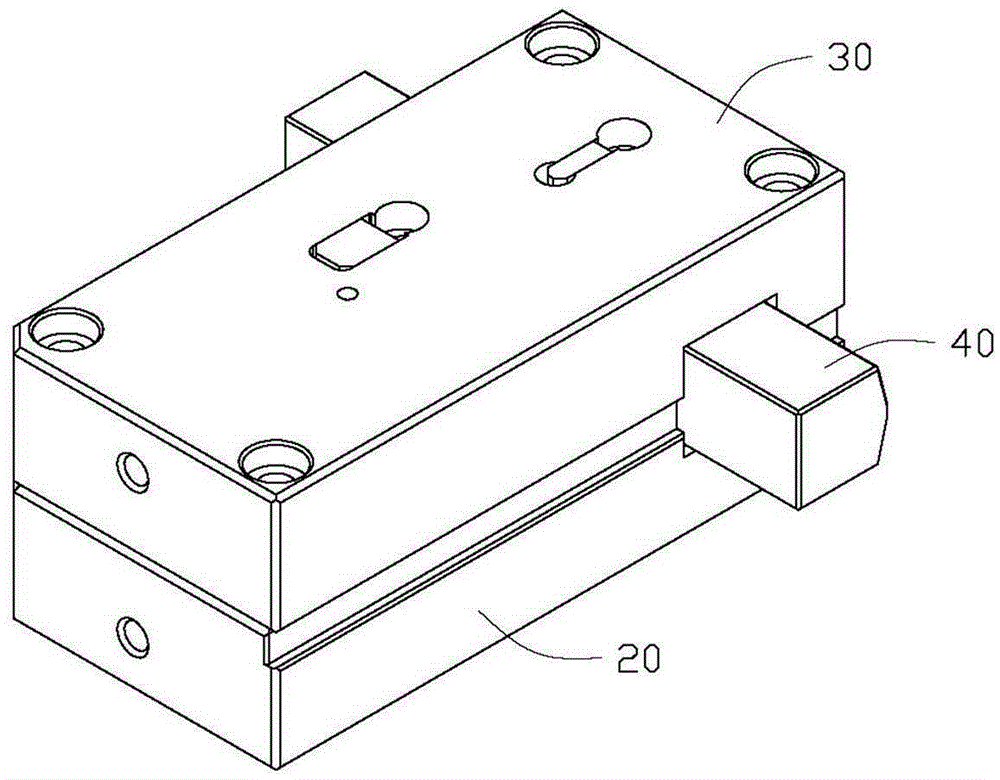
本发明涉及一种注塑模具,尤其涉及一种多次射出成型的注塑模具及其使用方法。
背景技术:
:在导电连接线加工过程中,通常需要进行包塑,即在导线外部包裹绝缘外皮。现有的包塑技术是将熔融的包塑材料与金属导线同时放入注塑模具,在注塑模具内部熔融的包塑材料附着在金属导线表面。而对于折弯处空间较小的导电连接线进行包塑时,主要通过先在一套注塑模具内成型导电连接线的部分结构,然后取出该导电连接线并将其放入另一套注塑模具内以成型该导电连接线的剩余结构。然而,该成型后的导电连接线结合处的分型线较大,从而导致两部分结构易分离,注塑效果较差。技术实现要素:鉴于上述状况,有必要提供一种注塑效果较好的注塑模具及其使用方法。一种注塑模具,用于注塑成型工件。该注塑模具包括第一模仁、与该第一模仁配合的第二模仁及与该第二模仁配合的第三模仁,该第一模仁包括第一本体及设置在该第一本体上的收容槽,该第二模仁包括第二本体、开设在该第二本体上的第一注塑通孔及与该第一注塑通孔连通的第一注塑腔,该第一注塑腔与该收容槽对应设置以成型该工件的部分结构,该第三模仁包括第三本体、开设在该第三本体上的第二注塑通孔及与该第二注塑通孔连通的第二注塑腔,该第二注塑腔与该第一注塑腔对应设置以成型该工件的剩余结构。一种注塑模具的使用方法,包括以下步骤:将待成型的工件定位放置在该第一模仁内;将该第二模仁定位扣合在该第一模仁上;注塑料进入该第二模仁的第一注塑腔内以注塑成型该工件的部分结构;将该第一模仁从该第二模仁上取下,成型部分结构的工件保留在该第二模仁内;将该第三模仁定位扣合在该第二模仁上;注塑料进入该第三模仁的第二注塑腔内以注塑成型该工件的剩余结构;将成型的工件从该第二模仁与该第三模仁内取出。上述注塑模具通过第一模仁的收容槽定位收容待注塑的工件,第一模仁与第二模仁相结合,注塑料通过第二模仁的第一注塑通孔进入第一注塑腔以成型工件的部分结构;保留有已成型部分结构的工件的第二模仁与第三模仁相结合,注塑料通过第三模仁的第二注塑通孔进入第二注塑腔以成型工件的剩余结构,第二模仁分别与第一模仁及第三模仁结合以先后成型工件的两部分结构,该两部分结构能够很好地结合为一个整体,从而使上述注塑模具的注塑效果较好。附图说明图1是本发明实施方式的注塑模具的部分立体示意图。图2是本发明实施方式的注塑模具的另一部分的立体示意图。图3是图1所示注塑模具的第一模仁与第二模仁的立体分解示意图。图4是图1所示注塑模具的第一模仁与第二模仁另一角度的立体分解示意图。图5是图2所示注塑模具的第二模仁与第三模仁的立体分解示意图。图6是图2所示注塑模具的第二模仁与第三模仁另一角度的立体分解示意图。图7是本发明实施方式的注塑模具的使用方法的流程图。主要元件符号说明注塑模具100工件200头部201第一模仁10第一本体11收容槽12顶出件121第一贯穿槽13第一顶出块131第一定位孔14第二模仁20第二本体21第一注塑通孔22第一导流道23第一注塑腔24第一注塑顶出块241第二贯穿槽25第二顶出块251第一定位柱26第三模仁30第三本体31第二注塑通孔32第二导流道33第二注塑腔34第二注塑顶出块341第三贯穿槽35第三顶出块351第二定位孔36挡块40收容孔41定位槽42如下具体实施方式将结合上述附图进一个步说明本发明。具体实施方式下面将结合本发明实施例中的附图,对本发明实施例中的技术方案进行清楚、完整地描述,显然,所描述的实施例仅仅是本发明部分实施例,而不是全部的实施例。基于本发明中的实施例,本领域普通技术人员在没有做出创造性劳动前提下所获得的所有其他实施例,都属于本发明保护的范围。需要说明的是,当组件被称为“固定于”另一个组件,它可以直接在另一个组件上或者也可以存在居中的组件。当一个组件被认为是“连接”另一个组件,它可以是直接连接到另一个组件或者可能同时存在居中组件。当一个组件被认为是“设置于”另一个组件,它可以是直接设置在另一个组件上或者可能同时存在居中组件。本文所使用的术语“垂直的”、“水平的”、“左”、“右”以及类似的表述只是为了说明的目的。除非另有定义,本文所使用的所有的技术和科学术语与属于本发明的
技术领域:
的技术人员通常理解的含义相同。本文中在本发明的说明书中所使用的术语只是为了描述具体的实施例的目的,不是旨在于限制本发明。本文所使用的术语“及/或”包括一个或多个相关的所列项目的任意的和所有的组合。请同时参阅图1及图2,本发明实施方式的注塑模具100包括第一模仁10、与第一模仁10配合的第二模仁20及与第二模仁20配合的第三模仁30。注塑模具100还包括固定机构、加热机构、冷却机构等各种功能机构,然而,为描述简洁,本实施方式重点介绍第一模仁10、第二模仁20及第三模仁30。第一模仁10与第二模仁20相结合以成型工件的部分结构,保留有已部分成型工件的第二模仁20与第三模仁30相结合以在上述已部分成型工件的基础上成型工件的剩余结构,从而注塑成型一个完整的工件。注塑模具100还包括用于定位待注塑工件的挡块40。挡块40首先收容在第一模仁10与第二模仁20之间,当注塑成型工件的部分结构后,挡块40保留在第二模仁20内不取出,第三模仁30扣合在第二模仁20上,挡块40收容在第二模仁20与第三模仁30之间以成型工件的剩余结构。请同时参阅图3及图4,第一模仁10包括第一本体11、设置在第一本体11内的收容槽12、设置在收容槽12一端的第一贯穿槽13及设置在第一本体11边缘位置上的多个第一定位孔14。收容槽12用于收容待注塑的工件200,收容槽12内设置有顶出件121以顶出收容槽12内的工件200。第一贯穿槽13内设置有第一顶出块131,第一顶出块131用于定位及顶出第一贯穿槽13内的挡块40。第二模仁20包括第二本体21、开设在第二本体21上的第一注塑通孔22、与第一注塑通孔22连通的第一导流道23、与第一导流道23连通的第一注塑腔24、设置在第一注塑腔24一端的第二贯穿槽25及设置在第二本体21边缘位置上的多个第一定位柱26。第一注塑腔24与收容槽12对应设置,用于注塑成型工件200。第一注塑腔24内设置有第一注塑顶出块241以顶出第一注塑腔24内的工件200。第二贯穿槽25与第一贯穿槽13对应设置并且第二贯穿槽25内设置有第二顶出块251,第二顶出块251用于定位及顶出第二贯穿槽25内的挡块40。多个第一定位柱26分别对应多个第一定位孔14设置,从而保证第二模仁20定位扣合在第一模仁10上。挡块40上开设有收容孔41及定位槽42。收容孔41用于定位收容工件200的头部201,在避免头部201被注塑的同时,能够定位整个工件200。定位槽42分别对应第一顶出块131与第二顶出块251设置,定位槽42与第一顶出块131及第二顶出块251配合以将挡块40定位收容在第一贯穿槽13与第二贯穿槽25内。注塑时,首先将工件200的头部201放置在挡块40的收容孔41内,之后通过定位槽42与第一顶出块131配合将挡块40放置在第一贯穿槽13内,此时工件200定位收容在收容槽12内。之后通过第一定位柱26与第一定位孔14配合将第二模仁20定位扣合在第一模仁10上。注塑料通过第一注塑通孔22经第一导流道23进入第一注塑腔24内,从而注塑成型工件200的部分结构。请同时参阅图5及图6,第三模仁30包括第三本体31、开设在第三本体31上的第二注塑通孔32、与第二注塑通孔32连通的第二导流道33、与第二导流道33连通的第二注塑腔34、设置在第二注塑腔34一端的第三贯穿槽35及设置在第三本体31边缘位置上的多个第二定位孔36。第二注塑腔34与第一注塑腔24对应设置,用于注塑成型工件200。第二注塑腔34内设置有第二注塑顶出块341以顶出第二注塑腔34内的工件200。第三贯穿槽35与第二贯穿槽25对应设置并且第三贯穿槽35内设置有第三顶出块351,第三顶出块351用于定位及顶出第三贯穿槽35内的挡块40。多个第二定位孔36分别对应多个第一定位柱26设置,从而保证第三模仁30定位扣合在第二模仁20上。注塑时,首先第二模仁20内保留有成型部分结构的工件200,之后通过第二定位孔36与第一定位柱26配合将第三模仁30定位扣合在第二模仁20上。注塑料通过第二注塑通孔32经第二导流道33进入第二注塑腔34内,从而注塑成型工件200的剩余结构。请参阅图7,本实施方式提供的注塑模具100的使用方法包括以下步骤:步骤S101:将工件200定位放置在第一模仁10内。将工件200的头部201放置在挡块40的收容孔41内,之后通过定位槽42与第一顶出块131配合将挡块40放置在第一贯穿槽13内,此时工件200定位收容在第一模仁10上的收容槽12内。步骤S102:将第二模仁20定位扣合在第一模仁10上。通过第一定位柱26与第一定位孔14配合将第二模仁20定位扣合在第一模仁10上。步骤S103:注塑料进入第二模仁20的第一注塑腔24内以注塑成型工件200的部分结构。注塑料通过第一注塑通孔22经第一导流道23进入第一注塑腔24内,从而注塑成型工件200的部分结构。步骤S104:将第一模仁10从第二模仁20上取下,成型部分结构的工件200保留在第二模仁20内。通过分别抵持顶出件121与第一顶出块131使工件200及挡块40从第一模仁10上分离开,之后将第一模仁10从第二模仁20上取下,成型部分结构的工件200与定位工件200的挡块40保留在第二模仁20内。步骤S105:将第三模仁30定位扣合在第二模仁20上。通过第二定位孔36与第一定位柱26配合将第三模仁30快速地定位扣合在第二模仁20上。步骤S106:注塑料进入第三模仁30的第二注塑腔34内以注塑成型工件200的剩余结构。注塑料通过第二注塑通孔32经第二导流道33进入第二注塑腔34内,注塑成型工件200的剩余结构,该两部分结构结合,从而成型完整的工件200。步骤S107:将成型的工件200从第二模仁20与第三模仁30内取出。通过分别抵持第一注塑顶出块241与第二顶出块251使工件200及挡块40从第二模仁20上分离开,通过分别抵持第二注塑顶出块341与第三顶出块351使工件200及挡块40从第三模仁30上分离开,之后将成型的工件200从挡块40上取下即可。本实施方式中的注塑模具100通过将待注塑的工件200定位放置在第一模仁10的收容槽12内,之后将第二模仁20定位扣合在第一模仁10上,注塑料通过第二模仁20的第一注塑通孔22进入第一注塑腔24,从而成型工件200的部分结构;将第一模仁10从第二模仁20上取下,工件200保留在第二模仁20内;将第三模仁30定位扣合在第二模仁20上,此时工件200已成型的部分结构尚未冷却,该部分结构的注塑料处于熔融状态;注塑料通过第三模仁30的第二注塑通孔32进入第二注塑腔34成型工件200的剩余结构,由于先前注塑的工件200的部分结构尚未冷却,该两部分结构在熔融状态下很好地结合为一个整体,从而注塑模具100的注塑效果较好。可以理解,挡块40可以省略,通过收容槽12、第一注塑腔24与第二注塑腔34分别定位工件200即可,另外,可以通过分别隔断第一注塑腔24与第二注塑腔34来防止注塑料到达头部201。另外,本领域技术人员还可在本发明精神内做其它变化,当然,这些依据本发明精神所做的变化,都应包含在本发明所要求保护的范围内。当前第1页1 2 3