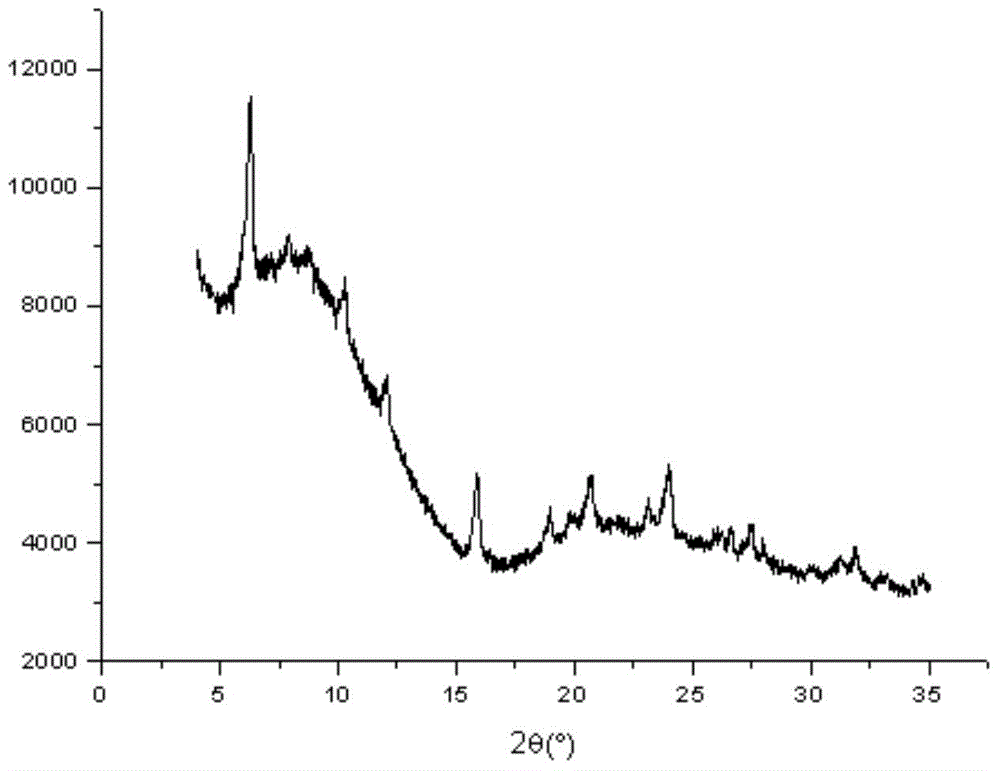
本发明涉及一种催化裂化废催化剂再利用的方法。
背景技术:
:催化裂化装置每年都要排放大量的废催化剂,由于催化裂化废催化剂的重金属含量较高,特别是具有一定的放射性,它对人以及周围环境有害,在国外已将其作为有害物质处理,其运输、排放、处理的费用很高;同时催化剂金属中毒也使催化剂的裂化性能和选择性大幅下降,使轻质油的收率降低,直接影响了炼油厂的经济效益。因此,开发催化裂化废催化剂再生回用技术将带来极大的经济效益和环境效益。废催化剂掩埋是较易实现的处理方法,至今仍被采用,但这种方法花费大,并且不是治本的方法。国内外有部分企业采用磁选法对FCC废催化剂进行物理处理,这种方法是通过物理方法优选出污染轻,性能较好,尚可继续使用的平衡剂,而那些已经失活的催化剂的性能并没有得到改善,因而无法从根本上解决废催化剂的处理问题。另外,人们曾试图将FCC废催化剂用于生产水泥和铺路,但因不同FCC装置的废催化剂细粉含量不同,固化时间不一致,固化产品的硬度也不一样,生产过程中需要根据不同的废催化剂调整配方,但连续性生产不能频繁调变配方,这就成为阻碍废催化剂在此领域应用的一个因素。专利CN101219396A公开了一种无机和有机耦合法复活FCC废催化剂的方法,即通过无机酸的扩孔作用和有机酸的配位功能,二者协同完成重金属的脱除及FCC废催化剂孔结构上的修复。但该化学复活法在脱除污染金属的同时,也会造成催化剂上活性组分损失,而且并未解决分子筛骨架破坏 引起的不可逆失活,复活后的催化剂活性稳定性不足。专利CN201010236528公开了一种利用FCC废催化剂为原料制备NaY分子筛的方法,主要特征为:首先将FCC废催化剂碱熔活化,再在外加硅源的条件下利用结构导向水热合成技术制备Y型分子筛。该方法由于须先对废催化剂进行高温碱熔活化,工艺复杂,制备成本较高。另外,得到的NaY分子筛晶粒较小,仅为200nm左右。专利CN102247880B公开了一种通过“原位晶化”再利用废裂化剂的方法,其特征在于使用催化裂化废催化剂为原料原位合成催化裂化催化剂,制备方法是首先采用酸洗的方法去除催化裂化废催化剂中的钒和镍等重金属组分,然后将酸洗后废催化剂和碱的混合物在高温下进行焙烧对其进行活化,再将活化后的废催化剂与水玻璃、高岭土、助剂、分散剂或/和粘结剂等经喷雾干燥成型为微球A,然后将微球A与水玻璃、水以及导向剂等进行晶化反应,得到NaY沸石含量为20%~70%、沸石硅铝比4.0~6.0的晶化微球,再经改性处理得到裂化催化剂产品。虽然该方法通过原位晶化能够提高微球中分子筛含量,增加催化剂活性,但制备过程中需要预先对废裂化剂进行酸洗及高温碱焙烧处理,制备成本高且操作复杂。以高岭土为原料同时制备活性组分NaY分子筛和基质的“原位晶化”技术是一种重要的催化裂化催化剂制备方法。Engelhard公司在专利US4493902公开的制备方法中,通过在高岭土母体微球中添加超细高岭土,可以将晶化微球中NaY分子筛含量提高到40%以上,成为Engelhard公司的标志性专利技术。由于要使用超细高岭土,使得该方法的制备成本较高。专利CN1232862A公开的原位晶化制备方法中,将高岭土微球分别在700~900℃及900℃~1000℃的温度下焙烧,按一定比例混合后进行晶化反应,得到的晶化微球中NaY分子筛含量为30%左右。该方法由于要使用两种温度焙烧的高岭土微球,使得制备工艺较为复杂,制备成本较高。技术实现要素:本发明的目的是提供一种催化裂化废催化剂再利用的方法。该方法以催化裂化废催化剂、焙烧高岭土微球为主要原料,在补充硅源、不添加外加铝源的情况下,通过原位晶化的方法制备新鲜催化裂化催化剂从而使催化裂化废催化剂得到再利用。为了实现上述目的,本发明提供一种催化裂化废催化剂再利用的方法,该方法包括:a、按照Na2O:Al2O3:SiO2:H2O=(1-12):1:(4-20):(40-400)的总摩尔配比将催化裂化废催化剂、焙烧高岭土微球、硅源、碱源、导向剂和水混合,得到混合浆液;其中,以干基重量计,所述催化裂化废催化剂与所述焙烧高岭土微球的重量之比为(1:99)-(99:1);并且其中,所述导向剂中所含氧化铝的重量占所述混合浆液中所含氧化铝总重量的1-5重%;b、将步骤a中所得的混合浆液在70℃-120℃下晶化5h-40h,将所得产物过滤、洗涤、干燥,得到晶化微球;c、将步骤b中所得的晶化微球进行铵交换和/或稀土交换和/或酸改性处理,得到新鲜催化裂化催化剂。优选地,其中,以干基重量计,所述催化裂化废催化剂与所述焙烧高岭土微球的重量之比为(20:80)-(80:20)。优选地,其中,以干基重量计,所述催化裂化废催化剂与所述焙烧高岭土微球的重量之比为(30:70)-(70:30)。优选地,其中,所述焙烧高岭土微球的制备方法包括如下步骤:将高岭土、分散剂和水依次进行混合打浆,得到高岭土浆液;其中,以SiO2计的所述分散剂的重量为以干基计的所述高岭土总重量的2-4重%,所述高岭土浆液的固含量为35-45重%;将所述高岭土浆液进行喷雾干燥,得到高岭土微球;将所述高岭土微球在650-1000℃进行焙烧0.5-20小时,得到焙烧高岭土微球。优选地,其中,所述导向剂的制备方法包括如下步骤:按照(15-18)Na2O:Al2O3:(15-17)SiO2:(280-380)H2O的摩尔配比将碱源、铝酸钠、硅源和水混合,并在室温至70℃下静置老化0.5-48小时,得到所述导向剂。优选地,其中,所述硅源为选自水玻璃、硅胶、硅溶胶、白炭黑和硅藻土中的至少一种,所述碱源为氢氧化钠。优选地,其中,步骤b中所述晶化为搅拌状态下的动态晶化。优选地,其中,所述酸改性处理所使用的酸为无机酸和/或有机酸,所述无机酸为选自盐酸、硝酸和硫酸中的至少一种,所述有机酸为选自草酸、柠檬酸和酒石酸中的至少一种。本发明提供的催化裂化废催化剂的再利用方法与现有催化裂化废催化剂的再利用方法相比,方法简单,能耗低,并且所制备的新鲜催化裂化催化剂中,Y型分子筛含量(结晶度)在20%-70%,骨架硅铝比在4.8以上,催化裂化废催化剂的活性及重油裂化产物分布都得到明显改善,能够进行工业应用。本发明的其他特征和优点将在随后的具体实施方式部分予以详细说明。附图说明附图是用来提供对本发明的进一步理解,并且构成说明书的一部分,与下面的具体实施方式一起用于解释本发明,但并不构成对本发明的限制。在附图中:图1是采用本发明的方法所制备的晶化微球的扫描电镜照片(即实施例2所制备的晶化微球KEY-B2的扫描电镜照片);图2是本发明实施例所使用的催化裂化废催化剂YH-3的XRD谱图;图3是采用本发明的方法所制备的晶化微球的XRD谱图(即实施例2所制备的晶化微球KEY-B2的XRD谱图)。具体实施方式以下结合附图对本发明的具体实施方式进行详细说明。应当理解的是,此处所描述的具体实施方式仅用于说明和解释本发明,并不用于限制本发明。本发明提供一种催化裂化废催化剂再利用的方法,该方法包括:a、按照Na2O:Al2O3:SiO2:H2O=(1-12):1:(4-20):(40-400)的总摩尔配比将催化裂化废催化剂、焙烧高岭土微球、硅源、碱源、导向剂和水混合,得到混合浆液;其中,以干基重量计,所述催化裂化废催化剂与所述焙烧高岭土微球的重量之比为(1:99)-(99:1),优选为(20:80)-(80:20),进一步优选为(30:70)-(70:30);并且其中,所述导向剂中所含氧化铝的重量占所述混合浆液中所含氧化铝总重量的1-5重%;b、将步骤a中所得的混合浆液在70℃-120℃下晶化5h-40h,将所得产物过滤、洗涤、干燥,得到晶化微球;c、将步骤b中所得的晶化微球进行铵交换和/或稀土交换和/或酸改性处理,得到新鲜催化裂化催化剂。根据本发明,所述催化裂化废催化剂是本领域技术人员所熟知的,可以来自催化裂化装置,也可以来自催化裂化催化剂生产装置,对其组成也没有特别限制。需要说明的是,本发明的催化裂化废催化剂进行晶化前可以无需经过粉碎、酸洗以及碱洗等处理,与焙烧高岭土一样可以直接作为分子筛生长的载体。根据本发明,所述焙烧高岭土微球是指采用原位晶化法制备催化裂化催化剂时,进行原位晶化前的经过高温焙烧的高岭土微球,是本领域技术人员所熟知的,例如,其制备方法可以包括如下步骤:将高岭土、分散剂和水依次进行混合打浆,得到高岭土浆液;其中,以SiO2计的所述分散剂的重量为以干基计的所述高岭土总重量的2-4重%,所述高岭土浆液的固含量为35-45 重%;将所述高岭土浆液进行喷雾干燥,得到高岭土微球;将所述高岭土微球在650-1000℃进行焙烧0.5-20小时,得到焙烧高岭土微球。根据本发明,所述导向剂是指具有一定数量Y型分子筛晶核的分子筛合成原料,用于加快Y型分子筛的晶化速率,是本领域技术人员所熟知的,例如,所述导向剂的制备方法可以包括如下步骤:按照(15-18)Na2O:Al2O3:(15-17)SiO2:(280-380)H2O的摩尔配比将碱源、铝酸钠、硅源和水混合,并在室温至70℃下静置老化0.5-48小时,得到所述导向剂。其中,制备导向剂所用的硅源和碱源可以与步骤a中的硅源和碱源相同,也可以不同,但优选相同。根据本发明,所述硅源和碱源是本领域技术人员所熟知的,例如,所述硅源可以为选自水玻璃、硅胶、硅溶胶、白炭黑和硅藻土中的至少一种,所述碱源可以为氢氧化钠。根据本发明,步骤b中所述晶化是本领域技术人员所熟知的,本发明不再赘述。需要注意的是,由于本发明步骤a中所制备的混合浆液中含有成型的催化裂化废催化剂和焙烧高岭土微球,晶化时容易沉积,因此本发明混合浆液的晶化状态优选为动态晶化,所述动态晶化是本领域技术人员所熟知的,本发明不再赘述。根据本发明,步骤b中所述干燥是本领域技术人员所熟知的,其条件可以为:干燥的温度为80-150℃,干燥的时间为8-24小时。根据本发明,步骤c中所述改性处理是本领域技术人员所熟知的,可以为铵交换和/或稀土交换和/或酸改性处理。所述铵交换改性所使用的铵盐可以为选自氯化铵、硫酸铵、硝酸铵、碳酸铵、碳酸氢铵、硫酸氢铵、磷酸铵、磷酸二氢铵和磷酸氢二铵中的至少一种;所述稀土交换改性所使用的稀土化合物可以为选自氯化稀土、硝酸稀土和硫酸稀土中的至少一种;所述酸交换改性所使用的酸可以为无机酸和/或有机酸,所述无机酸可以为选自盐酸、硝 酸和硫酸中的至少一种,所述有机酸可以为选自草酸、柠檬酸和酒石酸中的至少一种。下面将通过实施例对本发明进行进一步的说明,所用的仪器设备如无特别说明,均为现有
技术领域:
中常规仪器设备,本发明不再赘述,但并不因此而限制本发明。本发明实施例所制备的新鲜催化裂化催化剂中Y型分子筛的结晶度采用RIPP146-90标准方法测定。骨架硅铝比采用下列公式测定:SiO2/Al2O3=2×(25.8575-a0)/(a0-24.191);其中,a0是分子筛的晶胞参数,采用RIPP145-90标准方法测定。新鲜催化裂化催化剂的Na2O含量采用RIPP129-90方法测定,RE2O3含量采用RIPP131-90方法测定。微反应活性采用RIPP92-90标准方法测定。此处所提及的RIPP标准方法具体可参见《石油化工分析方法》,杨翠定等编,1990年版。本发明实施例所采用导向剂的制备过程如下:按照16Na2O:Al2O3:15SiO2:320H2O的摩尔配比将氢氧化钠、铝酸钠、水玻璃(齐鲁催化剂公司提供,SiO2262g/L,模数3.43,密度1260g/L)和化学水混合,并在30℃下静置老化24小时,得到了导向剂。实施例1本实施例说明焙烧高岭土微球的制备。15Kg化学水中加入300g水玻璃(齐鲁催化剂公司提供,SiO2262g/L,模数3.43,密度1260g/L)作为分散剂,搅拌状态下加入10Kg干基高岭土(苏州高岭土公司产品,SiO250.8%,Al2O344.3%,K2O0.59%,Fe2O30.83%)打浆,经喷雾干燥得到高岭土微球。将高岭土微球在马弗炉中900℃焙烧3h, 得到焙烧高岭土微球。实施例2本实施例说明本发明提供的晶化微球的制备。将75g焙烧高岭土微球和75g催化裂化废催化剂(燕山石化公司催化车间提供,记为YH-3:SiO237.4%,Al2O352.8%,RE2O33.2%,Fe0.84%,Ni1.19%,V0.39%)与371g水玻璃(齐鲁催化剂公司提供,SiO2262g/L,模数3.43,密度1260g/L)、214g导向剂和90g水于合成釜中混合均匀,搅拌状态下升温至98℃,并保持动态晶化26h。然后将晶化产物卸出,经过滤、洗涤,烘箱中120℃干燥过夜,得到本发明提供的晶化微球,记为KEY-B2,其结晶度为33.7%,骨架硅铝比为5.4。催化裂化废催化剂YH-3的XRD谱图如图2所示,晶化微球KEY-B2的扫描电镜图(SEM)和XRD谱图分别如图1和图3所示(由于后面实施例所制备的晶化微球的扫描电镜图和XRD谱图与KEY-B2相似,不再列出)。从扫描电镜图可以看出,晶化微球KEY-B2的表面存在大量Y型分子筛的晶粒,而从XRD图也可以看出,晶化微球的Y型分子筛的特征峰大大增强。这都说明通过本方法的处理,催化裂化废催化剂内分子筛含量增加。实施例3本实施例说明本发明提供的晶化微球的制备。将120g焙烧高岭土微球和30g催化裂化废催化剂(燕山石化公司催化车间提供,记为YH-3:SiO237.4%,Al2O352.8%,RE2O33.2%,Fe0.84%,Ni1.19%,V0.39%)与397g水玻璃(齐鲁催化剂公司提供,SiO2262g/L,模数3.43,密度1260g/L)、222g导向剂和101g水于合成釜中混合均匀,搅拌状态下升温至95℃,并保持动态晶化33h。然后将晶化产物卸出,经过滤、 洗涤,烘箱中120℃干燥过夜,得到本发明提供的晶化微球,记为KEY-B3,其结晶度为44.0%,骨架硅铝比为5.2。实施例4本实施例说明本发明提供的晶化微球的制备。将48g焙烧高岭土微球和72g催化裂化废催化剂(燕山石化公司催化车间提供,记为YH-3:SiO237.4%,Al2O352.8%,RE2O33.2%,Fe0.84%,Ni1.19%,V0.39%)与480g水玻璃(齐鲁催化剂公司提供,SiO2262g/L,模数3.43,密度1260g/L)、10.2gNaOH(北京化工厂试剂,分析纯)、171g导向剂和61g水于合成釜中混合均匀,搅拌状态下升温至93℃,并保持动态晶化20h。然后将晶化产物卸出,经过滤、洗涤,烘箱中120℃干燥过夜,得到本发明提供的晶化微球,记为KEY-B4,其结晶度为51.2%,骨架硅铝比为5.3。实施例5本实施例说明本发明提供的晶化微球的制备。将36g焙烧高岭土微球和84g催化裂化废催化剂(燕山石化公司催化车间提供,记为YH-3:SiO237.4%,Al2O352.8%,RE2O33.2%,Fe0.84%,Ni1.19%,V0.39%)与465g水玻璃(齐鲁催化剂公司提供,SiO2262g/L,模数3.43,密度1260g/L)、14.5gNaOH(北京化工厂试剂,分析纯)、240g导向剂和89g水于合成釜中混合均匀,搅拌状态下升温至90℃,并保持动态晶化29h。然后将晶化产物卸出,经过滤、洗涤,烘箱中120℃干燥过夜,得到本发明提供的晶化微球,记为KEY-B5,其结晶度为65.2%,骨架硅铝比为5.1。实施例6本实施例说明本发明提供的晶化微球的制备。将70g焙烧高岭土微球和30g催化裂化废催化剂(燕山石化公司催化车间提供,记为YH-3:SiO237.4%,Al2O352.8%,RE2O33.2%,Fe0.84%,Ni1.19%,V0.39%)与517g水玻璃(齐鲁催化剂公司提供,SiO2262g/L,模数3.43,密度1260g/L)、12.5gNaOH(北京化工厂试剂,分析纯)、142g导向剂和105g水于合成釜中混合均匀,搅拌状态下升温至88℃,并保持动态晶化37h。然后将晶化产物卸出,经过滤、洗涤,烘箱中120℃干燥过夜,得到本发明提供的晶化微球,记为KEY-B6,其结晶度为58.6%,骨架硅铝比为5.1。实施例7本实施例说明本发明提供的晶化微球的制备。将16g焙烧高岭土微球和64g催化裂化废催化剂(燕山石化公司催化车间提供,记为YH-3:SiO237.4%,Al2O352.8%,RE2O33.2%,Fe0.84%,Ni1.19%,V0.39%)与635g水玻璃(齐鲁催化剂公司提供,SiO2262g/L,模数3.43,密度1260g/L)、17.9gNaOH(北京化工厂试剂,分析纯)、113g导向剂和115g水于合成釜中混合均匀,搅拌状态下升温至95℃,并保持动态晶化32h。然后将晶化产物卸出,经过滤、洗涤,烘箱中120℃干燥过夜,得到本发明提供的晶化微球,记为KEY-B7,其结晶度为48.5%,骨架硅铝比为5.6。实施例8本实施例说明本发明提供的晶化微球的制备。将9g焙烧高岭土微球和81g催化裂化废催化剂(燕山石化公司催化车 间提供,记为YH-3:SiO237.4%,Al2O352.8%,RE2O33.2%,Fe0.84%,Ni1.19%,V0.39%)与590g水玻璃(齐鲁催化剂公司提供,SiO2262g/L,模数3.43,密度1260g/L)、15.4gNaOH(北京化工厂试剂,分析纯)、127g导向剂和113g水于合成釜中混合均匀,搅拌状态下升温至98℃,并保持动态晶化27h。然后将晶化产物卸出,经过滤、洗涤,烘箱中120℃干燥过夜,得到本发明提供的晶化微球,记为KEY-B8,其结晶度为52.3%,骨架硅铝比为5.5。实施例9本实施例说明本发明提供的晶化微球经改性制备成催化剂的裂化性能。将实施例8制备的晶化微球KEY-B8,通过常规的“两交两焙”工艺分别与稀土溶液和氯化铵溶液进行交换改性。稀土交换的配比(重量)为:晶化微球:RE2O3:H2O=1:0.08:8;第一次焙烧的温度为550℃,时间为2小时;铵交换的配比为:晶化微球:NH4Cl:H2O=1:0.35:8;第二次焙烧的温度为550℃,时间为2小时;交换过程中,交换液分别用10重%盐酸溶液调整pH值在3.0-3.5之间,以保证脱钠效果。得到的催化剂记为KEY-CB8,Na2O含量为0.30%、RE2O3含量为7.4%,800℃/17h水热老化后测定微反活性为70%,而催化裂化废催化剂的微反活性直接测定为55%。在ACE装置上对比评价了催化剂KEY-CB8和催化裂化废催化剂的重油(大庆蜡油添加30wt%的减压渣油,原料油性质见表1)裂化性能,结果见表2。从表2中可见,通过本发明提供的催化裂化废催化剂再利用方法得到的 催化剂,可使催化裂化废催化剂的裂化活性明显提高,裂化产物分布显著改善。表1原料油的性质项目分析数据项目分析数据密度(20℃)/g/cm30.8731粘度(80℃)/mm2/s17.56减压馏程/℃折光(70℃)1.4682初馏点189酸值/mgKOH/g0.075%398残碳/%0.710%418灰分/%0.0530%457C/%86.4350%497H/%13.5370%549S/%0.1290%73.5%,560℃N/%0.11表2催化裂化废催化剂YH-3以及本发明提供的新鲜催化裂化催化剂KEY-CB8的重油裂化性能样品名称YH-3KEY-CB8反应温度/℃500500剂油比5.925.92原料油WH-3WH-3产物分布/%干气1.421.39液化气16.3315.44汽油44.1054.05柴油16.6415.08重油11.418.75焦炭10.108.28合计100.00100.00转化率71.9479.17当前第1页1 2 3