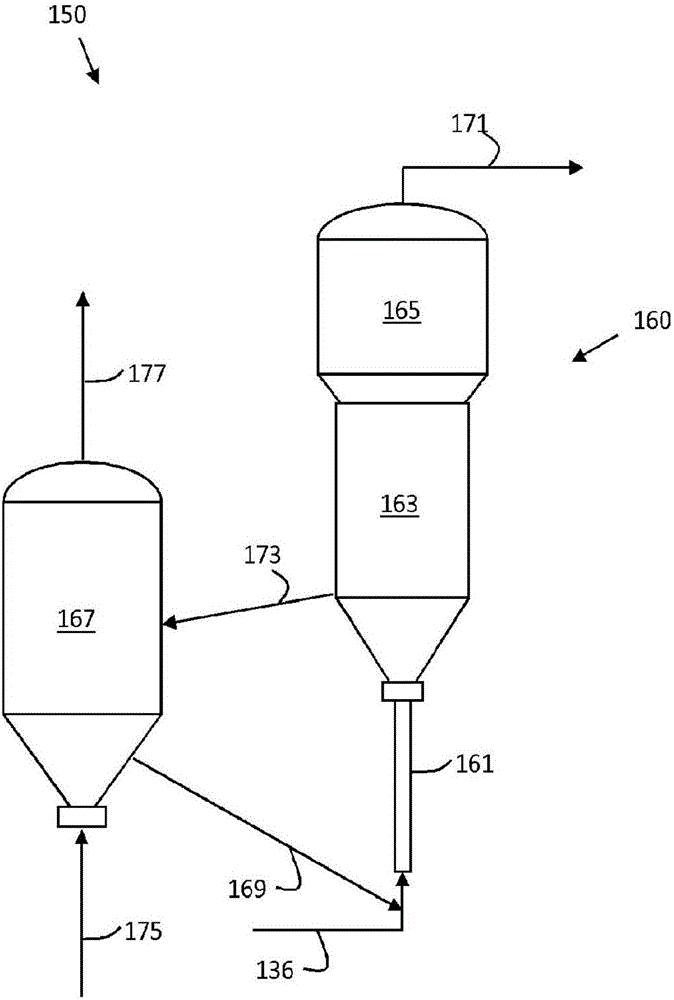
本申请要求2014年5月22日提交的美国临时专利申请62/001971的权益,其公开内容在此以其全部通过参考引入。发明背景发明领域本发明具体涉及一种用于流化催化裂化烃油的催化剂,该催化剂能够促进由重质烃例如减压瓦斯油(下文也称作“VGO”)等来生产汽油和轻质烯烃。相关领域说明在流化催化裂化(FCC)方法中,石油来源的烃用保持在流化态的酸性催化剂来催化裂化的,该催化剂在连续的基础上再生。来自于这种方法的主要产物通常是汽油。其他产物也以更小的量经由FCC方法来生产,例如液化石油气和裂化瓦斯油。沉积在催化剂上的焦炭在高温和空气存在下烧除,然后将再生的催化剂再循环回到反应区。虽然FCC方法取得了诸多进展,但是工业上持续寻找改进的催化剂材料,特别是能够降低干燥气体和焦炭产生的那些。技术实现要素:流化催化裂化催化剂包含沸石作为载体,其中构成沸石骨架的一部分铝原子被锆原子和/或铪原子代替,并且具有对于生产轻质烯烃和汽油来说有效的高裂化活性以及产生了较少的干燥气体和焦炭。在某些实施方案中,用于流化催化裂化烃油的催化剂包括超稳定Y型沸石,其中该超稳定Y型沸石是骨架取代的沸石,其中构成其沸石骨架的一部分铝原子被锆原子和/或铪原子取代。在某些实施方案中,上述催化剂的骨架取代的超稳定Y型沸石包含基于氧化物计算的0.1-5质量%的锆原子和/或铪原子。上述催化剂的骨架取代的超稳定Y型沸石可以进一步包含钛原子。在这些实施方案中,骨架取代的超稳定Y型沸石可以包含基于氧化物计算的0.1-5质量%的钛原子。上述催化剂的骨架取代的超稳定Y型沸石可以进一步地特征在于形成沸石骨架的一部分铝原子进一步用钛原子取代。在这些实施方案中,骨架取代的超稳定Y型沸石可以包含基于氧化物计算的0.1-5质量%的钛原子。在某些实施方案中,用于流化催化裂化烃油的催化剂包括超稳定Y型沸石,其中该超稳定Y型沸石是骨架取代的沸石,其中构成该超稳定Y型沸石的骨架的一部分铝原子用钛原子取代,在某些实施方案中仅是钛原子。在这些实施方案中,骨架取代的超稳定Y型沸石包含基于氧化物计算的0.1-5质量%的钛原子。上述实施方案的催化剂可以单独使用或者与一种或多种另外的流化裂化催化剂材料有效组合来提供催化剂混合物。在上述实施方案的催化剂中,骨架取代的超稳定Y型沸石可以特征在于晶格常数是2.430-2.450nm,比表面积是约600-约900m2/g,和SiO2与Al2O3的摩尔比通常是约5:1-约100:1,在某些实施方案中约20:1-约100:1,在另外的实施方案中约25:1-约80:1。还提供了一种用于裂化烃油的方法,其将上述实施方案的催化剂用于流化催化裂化单元中来生产轻质烯烃和汽油燃料。在该方法的某些实施方案中,提供了烃油混合物,其沸点范围高于约350℃,并且反应器在反应温度范围约450℃-约700℃,压力约1-约10巴,停留或接触时间约0.1-约60秒,和催化剂与油之比约2:1-约30:1操作。流化催化裂化可以在有效地使汽油和轻质烯烃的生产最大化的条件下进行,和/或在有效地使轻质烯烃的生产最大化的条件下进行。作为本文使用的,“重质烃”指的是名义沸点高于约350℃的石油馏分,包括常用的炼厂料流例如减压瓦斯油(VGO),加氢裂化单元未转化的底部物或再循环油,获自溶剂脱沥青方法的脱沥青油(DAO),脱金属油,获自炼焦器方法的轻质或重质炼焦器瓦斯油,获自单独的流化催化裂化方法或者从使用本发明的催化剂的FCC方法再循环的循环油,获自减粘裂化方法的瓦斯油,或者包含前述来源的至少一种或油的氢化衍生物的组合。附图说明将在下面和参考附图来进一步详细描述本发明,附图中相同或类似的元素用相同的附图标记表示,其中:图1是提升管流化催化裂化单元的示意图;和图2是下流式流化催化裂化单元的示意图。具体实施方式本发明涉及一种用于流化催化裂化操作的有用的和有效的催化剂组合物。催化剂组合物是骨架取代的沸石催化剂,其包括骨架取代的超稳定Y型沸石,其中一部分骨架铝原子用锆原子和/或铪原子取代。钛原子也可以作为骨架中铝原子的替代而存在。在特别是增强丙烯或更轻质烯烃和汽油的生产,同时降低干燥气体和焦炭的生产的某些实施方案中,这些催化剂组合物单独使用或者与一种或多种另外的流化裂化催化剂材料(其对于流化催化裂化方法是已知的或变成已知的)有效组合,由此形成适于流体催化裂化操作的催化剂混合物。骨架取代的沸石-1本文提供的使用FCC操作来转化重质烃的催化剂包括骨架取代的沸石,其包含部分构成超稳定Y型沸石(“USY”)的骨架的锆原子和/或铪原子。骨架取代的沸石是USY型沸石,其中硅原子和铝原子形成沸石骨架,和其中形成沸石骨架的一部分铝原子被锆原子、铪原子或锆和铪原子二者取代。作为本文使用的,形成沸石骨架的一部分铝原子被锆原子、铪原子或锆和铪原子二者取代的USY型沸石被称作“骨架取代的沸石-1”。此外,形成沸石骨架的一部分铝原子仅被锆原子取代的骨架取代的沸石-1被称作“锆取代的沸石”或“Zr-USY”,形成骨架取代的沸石-1的沸石骨架的一部分铝原子仅被铪原子取代的骨架取代的沸石-1被称作“铪取代的沸石”或“Hf-USY”,和形成沸石骨架的一部分铝原子仅被锆原子和铪原子取代的骨架取代的沸石-1被称作“锆-铪-取代的沸石”或“Zr-Hf-USY”。取代了形成超稳定Y型沸石的骨架的铝原子的锆原子和/或铪原子充当了该超稳定Y型沸石的骨架的成分。在本文所述的骨架取代的沸石-1中,一部分锆原子和/或铪原子可以任选地负载于孔的内表面上或与之结合,例如以金属氧化物形式,即氧化锆颗粒和/或氧化铪颗粒。锆和/或铪的金属氧化物与USY沸石的中孔的内表面结合。具有高中孔体积的沸石如下来制备:将骨架取代的沸石-1与pH约0.8至并包括约2的强酸性水溶液接触,在约50℃-约200℃的温度使沸石干燥,和将干燥沸石在约350℃-约600℃烧制,来制备金属氧化物超细颗粒与孔的内表面结合(也称作“负载于其上”)的沸石。该程序更详细地描述在日本未审专利申请公布2002-255537中,其在此通过参考引入。骨架取代可以通过例如X射线荧光法、高频等离子体发射光谱法、原子吸收光谱法、紫外光-可见光-近红外光谱法(UV-Vis-NIR)、傅里叶转换红外光谱法(FT-IR)或核磁共振光谱法(NMR)来验证。要注意的是,在β-沸石的骨架用锆原子取代的骨架取代的沸石中,已知指示锆原子存在的UV光谱在200纳米(nm)-220nm的范围显示(例如参见“B.Rakshe等人,JournalofCatalysis188,252,1999”中的图3)。本文的骨架取代的沸石-1通常包含约0.1%-约5%的锆原子和/或铪原子,在某些实施方案中约0.2%-约4%,在另外的实施方案中约0.3%-约3%,其按锆和/或铪氧化物(即ZrO2和/或HfO2)计,基于骨架取代的沸石-1的质量百分比。在这方面中,锆原子和/或铪原子的含量范围(基于氧化物)包括取代了形成沸石骨架的铝原子的锆原子和/或铪原子,和未取代铝原子的锆原子和/或铪原子的全部含量,例如负载于骨架取代的沸石-1的孔的内表面上。按氧化物计基于骨架取代的沸石-1的质量,小于约0.1质量%的骨架取代的沸石-1的锆和/或铪含量未产生用于烃油的FCC反应的有效量的固体酸。类似地,按氧化物计基于骨架取代的沸石-1的质量,超过约5质量%的锆原子和/或铪原子含量未产生用于烃油的FCC反应的有效孔体积,因此倾向于降低催化活性。在包括锆取代的沸石、铪取代的沸石和/或锆-铪取代的沸石的沸石-1的另外的实施方案中,可以提供钛原子来骨架取代形成沸石骨架的一部分铝原子。在这些实施方案中,钛原子可以以约0.1%-约5%的比例包含在骨架取代的沸石-1中,在某些实施方案中约0.5%-约4%,在另外的实施方案中约0.6%-约3%,按氧化钛(即TiO2)的质量百分比计,基于骨架取代的沸石-1。在这方面中,如果上述钛原子在骨架取代的沸石-1中按氧化物计的含量小于约0.1质量%,则当使用上述骨架取代的沸石-1作为载体制备的催化剂施用到流化催化裂化反应器时,没有获得对于流化催化裂化反应器有效量的固体酸,因此烃油在流化催化裂化反应器中的活性倾向于降低。类似地,如果钛原子在骨架取代的沸石-1中按氧化物计的含量超过约5质量%,则当使用上述骨架取代的沸石-1作为载体制备的催化剂施用到流化催化裂化反应器时,没有获得对于流化催化裂化反应器有效的孔体积,因此烃油在流化催化裂化反应器中的活性倾向于降低。钛原子在骨架取代的沸石-1中的含量可以通过例如X射线荧光分析仪、高频等离子体发射分光计、原子吸收分光计等来测量。骨架取代的沸石-2(构成)在本文的FCC催化剂的另外的实施方案中,除了上述骨架取代的沸石-1之外,可以包含作为载体的骨架取代的沸石(下文称作“骨架取代的沸石-2”),其中形成了超稳定Y型沸石的一部分铝原子仅用钛原子和/或无机酸(限于不对应于骨架取代的沸石-1中所用的那些的无机酸)取代。没有取代上述铝原子的钛原子可以包含在骨架取代的沸石-2(“骨架取代的沸石-2”被称作“钛取代的沸石”或“Ti-USY”)中。沸石-2可以如PCT公布WO2007/032232中所述来制备,其在此通过参考引入,其中已经开发了包含作为载体的Y型沸石的催化剂,该沸石含有引入沸石骨架中的钛原子(换言之,构成骨架的铝原子用钛原子取代的Y型沸石)。上述沸石可以如下来制备:将Y型沸石用含有钛的pH约1.5或更低的酸性水溶液处理,随后过滤、清洗和干燥。由此,可以制成沸石来包含引入沸石骨架结构中而不堵塞中孔的钛原子。本文的骨架取代的沸石-2通常包含约0.1%-约5%的钛原子,在某些实施方案中约0.5%-约4%,在另外的实施方案中约0.6%-约3%,按氧化钛(即TiO2)的质量百分比计,基于骨架取代的沸石-2。上述钛原子的含量范围(基于氧化物)包括取代形成了沸石骨架的铝原子的钛原子和没有取代上述铝原子的钛原子的全部含量。按氧化物计基于骨架取代的沸石-2的质量,小于约0.1质量%的骨架取代的沸石-2的钛含量不产生用于FCC反应器的有效量的固体酸,因此倾向于降低烃油在FCC反应器中的催化活性。骨架取代的沸石-1和骨架取代的沸石-2的特性为骨架取代的沸石-1和骨架取代的沸石-2提供某些范围的晶格常数、比表面积和二氧化硅与氧化铝之比。在本发明的用于烃油的流化催化裂化催化剂中,其比表面积优选落入200-450m2/g;直径或更低的孔体积优选落入0.40-0.75ml/g;和裂化金属组分的携带量优选落入0.01-40质量%。晶格常数(UD)本文的骨架取代的沸石-1和沸石-2材料的晶格常数是2.430nm-2.450nm,在某些实施方案中2.435nm-2.445nm。骨架取代的沸石-1或沸石-2的晶格常数小于2.430nm时倾向于降低使用各自的骨架取代的沸石作为载体的FCC催化剂的活性,这是由于骨架结构中的SiO2/Al2O3摩尔比高,并且充当了烃裂化的活性位的固体酸位少。超过2.450nm的骨架取代的沸石-1或沸石-2的晶格常数,由于低耐热性导致骨架取代的沸石-1或沸石-2的晶体结构在FCC反应过程中破裂,并且倾向于引起使用各自的骨架取代的沸石作为载体的FCC催化剂的活性降低。晶格常数可以参考ASTM方法D3942来测量。在氧化钛(锐钛矿型)的(111)平面处的Kα的角度使用充当主参考材料的硅(Si)来测定。来自于Y沸石的(533)和(642)平面的X射线衍射峰使用充当次参考材料的氧化钛来测定。比表面积(SA)本文所述的骨架取代的沸石-1和沸石-2的比表面积是约600m2/g-约900m2/g,在某些实施方案中约650m2/g-约800m2/g。该比表面积是通过BET(Brunauer-Emmett-Teller)方法,使用氮气吸附测定的值。骨架取代的沸石-1的比表面积小于约600m2/g潜在地降低FCC反应中有效催化活性的固体酸位的数目。超过约900m2/g的比表面积在提交本申请时是不现实的,这是由于生产限制,但是发现在加工沸石材料的开发中能够获得优势。SiO2与Al2O3的摩尔比(二氧化硅与氧化铝之比)本文所述的骨架取代的沸石-1和沸石-2的SiO2与Al2O3的摩尔比(二氧化硅与氧化铝之比)通常是约5:1-约100:1,在某些实施方案中约20:1-约100:1,在另外的实施方案约25:1-约80:1。二氧化硅与氧化铝之比小于约20,在某些实施方案中小于约5,不产生有效孔体积和因此容易引起裂化反应中活性降低。骨架取代的沸石-1超过约100的二氧化硅与氧化铝之比倾向于引起裂化活性降低,这是由于固体酸位的数目减少。用于生产骨架取代的沸石-1的方法USY沸石骨架内的一部分铝原子用锆原子取代。在某些实施方案中,进一步处理沸石-1来用钛原子取代骨架内的部分铝原子,其用作FCC催化剂组合物和在此称作“USY沸石”。在本发明时共同拥有的和在此通过参考引入的WO2012/018819的公开内容描述了一种类似的可用于加氢处理操作的催化剂组合物,并且可以依照其合成程序。在某些实施方案中,骨架取代的沸石-1通过将超稳定Y型沸石在约500℃-约700℃烧制来生产,该超稳定Y型沸石的晶格常数是2.430-2.450nm,比表面积是约600-约900m2/g,和SiO2与Al2O3的摩尔比通常是约5:1-约100:1,在某些实施方案中约20:1-约100:1,在另外的实施方案中约25:1-约80:1。形成含有经烧制的超稳定Y型沸石的悬浮液,该悬浮液的液体/固体质量比是5至并包括15。添加无机酸或有机酸,以使得悬浮液的pH是约1.0-约2.0。随后混合含有锆化合物和/或铪化合物的溶液。将溶液用例如氨水中和,以使得pH是约7。超稳定Y型沸石在制造本文的骨架取代的沸石-1的一个实施方案中,将超稳定Y型沸石用作原材料。本领域技术人员已知用于生产超稳定Y型沸石的方法。用于本文的制造方法的实施方案中的超稳定Y型沸石通常是这种沸石,其晶格常数(UD)是2.430-2.450nm,比表面积是约600-约900m2/g,和SiO2与Al2O3的摩尔比通常是约5:1-约100:1,在某些实施方案中约20:1-约100:1,在另外的实施方案中约25:1-约80:1。例如,一种生产上述超稳定Y型沸石的方法,将通过常规方法合成的Y型沸石(Na-Y)经过钠离子与铵离子通过常规方法的交换,例如:将Y型沸石分散在水中来制备悬浮液,向其中添加硫酸铵,用水清洗固体物质,将它用硫酸铵水溶液在约40℃-约80℃的温度清洗,随后将它用水在约40℃-约95℃的温度清洗,和在约100℃-约180℃干燥约30分钟。因此获得铵交换的Y型沸石,NH4-50-70Y,其中约50重量%-约70重量%的Y型沸石中所含的Na被NH4取代。随后,氢型Y型沸石(HY)通过将上述铵交换的Y型沸石(NH4-50-70Y)在例如饱和蒸气气氛中,在约500℃-约800℃煅烧约10分钟-约10小时来制备。然后,如下来获得约80重量%-97重量%的初始Y型沸石(Na-Y)中所含的Na用NH4离子交换的铵交换的Y型沸石(NH4-80-97Y):将上面获得的氢型Y型沸石分散在温度约40℃-约95℃的水中来制备悬浮液,向其中添加硫酸铵,然后将悬浮液在约40℃-约95℃的温度搅拌约10分钟-约3小时,用温度约40℃-约95℃的水进一步清洗固体物质,接着将它用硫酸铵水溶液在约40℃-约95℃的温度清洗,随后将它用温度约40℃-约80℃的水清洗,然后将它在约100℃-180℃干燥约30分钟-约30小时。在某些实施方案中,最终的铵离子交换率是约90%或更大。将因此获得的铵交换的Y沸石(NH4-80-97Y)在例如饱和蒸气气氛中在约500℃-约700℃煅烧约10分钟-约10小时。因此制备了超稳定Y型沸石(USY),其晶格常数(UD)是2.430nm或更大和2.450nm或更小,比表面积是约600m2/g-约900m2/g,和SiO2与Al2O3的摩尔比是约5:1-约100:1。在用于生产本文的催化剂的方法中,非骨架铝(不形成沸石骨架的一部分的铝原子)可以从作为原材料的上述超稳定Y型沸石中除去,以获得晶格常数2.430-2.450nm的超稳定Y型沸石。非骨架铝可以通过例如下面的方法来除去:将上述超稳定Y型沸石分散在温度约40℃-约95℃的水中来制备悬浮液,将硫酸添加到因此形成的悬浮液中,和将它搅拌约10分钟-约3小时,同时将温度保持在约40℃-约95℃,由此溶解非骨架铝。在非骨架铝溶解后,将悬浮液过滤,并且将过滤器上的残留物用纯净水在约40℃-约95℃清洗,和在约100℃-180℃的温度干燥约3-约30小时,由此可以获得除去了非骨架铝的超稳定Y型沸石。在用于生产本文的催化剂的方法中,作为原材料的超稳定Y型沸石在约500℃-约700℃的温度,在某些实施方案中在约550℃-约650℃的温度煅烧。煅烧时间通常不重要,只要获得目标的骨架取代的沸石-1即可,例如约30分钟-约10小时。如果超稳定Y型沸石的煅烧温度低于约500℃,则当用锆原子、铪原子或钛原子在随后步骤的步骤进行骨架取代处理时,与在约500℃-约700℃煅烧相比,锆原子、铪原子和钛原子的骨架取代量倾向于降低。在超过700℃的煅烧温度,超稳定Y型沸石的比表面积会降低,并且当用锆原子、铪原子或钛原子在随后步骤的步骤进行骨架取代处理时,锆原子、铪原子和钛原子的骨架取代量因此会降低。在某些实施方案中,超稳定Y型沸石的煅烧气氛是空气。将煅烧的超稳定Y型沸石悬浮于温度约20℃-约30℃的水中来形成悬浮液。关于超稳定Y型沸石的悬浮液的浓度,液体/固体质量比通常是约5:1-约15:1,在某些实施方案中是约8:1-约12:1。接着,向其中添加无机酸或有机酸,以使得上述悬浮液的pH控制到约1.0-约2.0,随后添加含有锆化合物和/或铪化合物的溶液,并且混合。将因此混合的溶液中和(例如到pH约7.0-约7.5),并且干燥(例如在约80℃-约180℃),由此可以获得上述的骨架取代的沸石-1。所用无机酸通常可以是硫酸、硝酸、盐酸等。在某些实施方案中,所选择的无机酸是硫酸或盐酸。此外,羧酸可以合适地用作上述的有机酸。无机酸或有机酸的量不重要,只要悬浮液的pH控制在约1.0-约2.0即可。例如,可以使用0.5-4.0倍摩尔量,在某些实施方案中0.7-3.5倍摩尔量,基于超稳定Y型沸石中Al2O3的量,不过这些范围不重要。上述合适的锆化合物包括硫酸锆、硝酸锆、氯化锆等中的一种或多种。在某些实施方案中,选择硫酸锆和/或硝酸锆。锆化合物的添加量通常相对于上述超稳定Y型沸石基于氧化锆是约0.1-约5质量%,在某些实施方案中是约0.2-约4质量%。小于约0.1质量%的锆化合物添加量不能改进沸石的固体酸特性。超过5质量%的锆化合物添加量倾向于造成沸石的孔堵塞。通过将锆化合物溶解在水中而制备的锆化合物的水溶液可以用作锆化合物。上述合适的铪化合物包括氯化铪、硝酸铪、氟化铪、溴化铪、草酸铪等中的一种或多种。在某些实施方案中,选择氯化铪和/或硝酸铪。铪化合物的添加量相对于超稳定Y型沸石基于氧化铪通常是约0.1-约5质量%,在某些实施方案中约0.2-约4质量%。小于约0.1质量%的铪化合物的添加量不能改进沸石的固体酸特性。通过将铪化合物溶解在水中而制备的铪化合物的水溶液可以用作铪化合物。钛化合物可以添加到上述的混合溶液中。合适的钛化合物包括硫酸钛、醋酸钛、氯化钛、硝酸钛和乳酸钛中的一种或多种。在某些实施方案中,选择硫酸钛和/或醋酸钛。钛化合物的添加量相对于超稳定Y型沸石基于氧化钛通常是约0.1-约5质量%,在某些实施方案中约0.2-约4质量%。小于约0.1质量%的钛化合物的添加量导致沸石的无效量的固体酸位。超过5质量%的钛化合物的添加量倾向于引起沸石的孔堵塞。通过将钛化合物溶解在水中而制备的钛化合物的水溶液可以用作钛化合物。将上述悬浮液的pH控制到约1.0-约2.0,以防止在锆化合物、铪化合物或钛化合物的水溶液与上述的超稳定Y型沸石的悬浮液混合过程中产生沉淀物。在某些实施方案中,锆化合物、铪化合物或钛化合物的水溶液与超稳定Y型沸石的悬浮液的混合通过将所述水溶液逐渐添加到悬浮液来进行。在将上述水溶液向悬浮液中添加完成后,溶液可以通过在例如室温(约25℃-约35℃)搅拌约3小时-约5小时来混合。此外,在完成上述混合后,混合溶液通过添加碱性化合物例如氨水和/或类似物,以使得其pH控制到约7.0-约7.5来中和,由此获得本文所述的骨架取代的沸石-1。在这方面中,当仅锆化合物(或其水溶液)用作添加到上述悬浮液中的化合物(或其水溶液)时,形成锆原子取代形成了超稳定Y型沸石的骨架的一部分铝原子的骨架取代的沸石-1(Zr-USY);当仅使用铪化合物(或其水溶液时),形成铪原子取代形成了超稳定Y型沸石的骨架的一部分铝原子的骨架取代的沸石-1(Hf-USY);和当使用锆化合物和铪化合物(或其水溶液)时,形成锆原子和铪原子取代形成了超稳定Y型沸石骨架的一部分铝原子的骨架取代的沸石-1(Zr·Hf-USY)。当钛化合物(或其水溶液)与添加锆化合物和/或铪化合物(或其水溶液)相组合来添加到上述悬浮液时,形成锆原子、铪原子和钛原子形成了超稳定Y型沸石的骨架的一部分的骨架取代的沸石-1(Zr·Hf·Ti-USY)。形成的骨架取代的沸石-1可以过滤,如果需要,用水清洗,和在约80℃-约180℃干燥。流化催化裂化催化剂制备FCC催化剂组合物包含例如15-60质量%、优选20-50质量%的沸石,10-30质量%、优选15-25质量%的无机粘合剂作为粘合剂,和非沸石的无机氧化物作为余量。二氧化硅基粘合剂和氧化铝基粘合剂可以用作无机粘合剂。二氧化硅基粘合剂可以是硅溶胶、水玻璃(硅酸钠)和硅酸液体中的任一种或两种或更多种。例如,包含浓度10-15质量%的SiO2的硅溶胶可以通过同时和连续添加包含浓度12-23质量%的SiO2的水玻璃和浓度20-30质量%的硫酸来制备。铝化合物粘合剂可以是(a)碱性氯化铝,(b)磷酸氢铝,或(c)铝溶胶。通过将结晶氧化铝例如三水铝矿、三羟铝石和勃姆石中的任何种类或两种或更多种溶解在酸溶液所获得的溶液可以替代地用作铝化合物粘合剂。这里,碱性氯化铝如式1所示。[Al2(OH)nCl6-n]m(1)(其中0<n<6和1<m<10,优选4.8<n<5.3和3<m<7,和符号m表示自然数。)磷酸氢铝(也称作磷酸二氢铝或磷酸伯铝)用Al(H2PO4)3表示。铝溶胶可以通过例如用酸调节假勃姆石型氧化铝的pH来生产。除了高岭土和其他粘土矿物之外,无机氧化物可以是活性氧化铝、多孔二氧化硅、稀土金属化合物和金属捕捉剂(金属捕集剂)。任何稀土金属氧化物可以以RE2O3形式和0-3质量%的含量比包含在催化剂中。本文所用的稀土金属包括铈(Ce)、镧(La)、镨(Pr)和钕(Nd),并且催化剂组合物可以带有这些中的任一种或两种或更多种作为金属氧化物。下面描述了催化剂组分的制造方法的例子。首先,将高岭土和活性氧化铝添加到上述硅溶胶(二氧化硅基粘合剂的一个例子)中,然后用20-30质量%的硫酸制备pH3-5的TiZrUSY沸石的浆料;以此方式制备浆料混合物。将该浆料混合物喷雾干燥来形成球形颗粒。清洗获得的球形颗粒,与稀土金属(RE)氯化物的水溶液接触来进行离子交换,以使得RE2O3的含量比率是0-3质量%,然后干燥;以此方式获得催化剂。获得的催化剂的平均粒径没有特别限制,但是它在60-70微米的量级。在USY沸石制备后,将催化剂用蒸汽准平衡化,例如在约600-约800℃的温度和进行约10-约20小时。基于本发明的用于流化催化裂化的催化剂的流化催化裂化可以在用于流化催化裂化烃油的常规条件下进行。例如,可以适当地使用下述条件。使用本文的催化剂来流化催化裂化烃油将用于本文所述的烃油的FCC催化剂添加到反应器容器中,并且合适地用于根据已知的FCC方法来催化裂化烃油,来生产汽油和/或轻质烯烃包括乙烯、丙烯和丁烯。在本文的流化催化裂化中,烃油可以来源于原油、合成原油、沥青、油砂、页岩油和煤液体中的一种或多种。这些进料可以包括正常沸点高于350℃的石油馏分,包括石脑油、柴油、减压瓦斯油(VGO)、获自溶剂脱沥青方法的脱沥青油(DAO)、脱金属油、获自炼焦器方法的轻质或重质炼焦器瓦斯油、获自单独的流化催化裂化方法或从使用本发明催化剂的FCC方法再循环的循环油、获自减粘裂化方法的瓦斯油,或者包含前述至少一种的组合。例如,向催化裂化设备中添加上述FCC催化剂,并且沸点高于约350℃、在某些实施方案中约350℃-约850℃的烃油可以使用流化催化裂化在约450℃-约700℃的温度,1-10巴的压力,约0.1秒-约60秒的停留或接触时间,和约2:1-约30:1的催化剂与油之比进行裂化。在某些实施方案中,提供配置有提升管反应器的流化催化裂化单元,其在促进轻质烯烃、特别是丙烯形成,和使消耗轻质烯烃的反应包括氢转移反应最小化的条件下操作。图1是提升管流化催化裂化单元的简化示意图。流化催化裂化单元150包括提升管反应器。流化催化裂化单元150包括反应器/分离器160,其具有提升管部分161、反应区163和分离区165。流化催化裂化单元150还包括用于再生用过的催化剂的再生容器167。将装料136引入反应区,在某些实施方案中伴随有蒸汽或其他合适的气体,用于雾化进料(未示出)。将装料136与有效量的经加热的新鲜的或者经由管道169从再生容器167输送的再生的固体裂化催化剂颗粒进行混合和密切接触。将进料混合物和裂化催化剂在条件下接触来形成悬浮液,其引入到提升管361中。在一种连续方法中,裂化催化剂和烃原料的混合物向上前进穿过提升管161进入反应区163。在提升管161和反应区163中,热的裂化催化剂颗粒通过碳-碳键断裂来催化裂化相对大的烃分子。在反应过程中,如流化催化裂化操作中常规的,裂化催化剂变得结焦,因此限制或不存在到活性催化位的通路。反应产物使用流化催化裂化单元中已知的任何合适的构造来与结焦的催化剂分离,该构造通常称作流化催化裂化单元150中的分离区165,例如位于反应区163上的反应器160的顶上。分离区可以包括本领域技术人员已知的任何合适的设备,例如旋风分离器。反应产物通过管道171来取出。来自于烃原料的流化裂化的含有焦炭沉积物的催化剂颗粒经过管道173到再生区167。根据本文的方法,因为轻质溶剂原料与作为进料136的重质原料合并,所以选择初始的溶剂脱沥青/脱金属方法中的溶剂与油之比,以提供足够的催化剂结焦来提供再生过程中的热平衡。在再生区167中,结焦的催化剂与经由管道175进入再生区167的含氧气体例如纯氧或空气的流接触。再生区167以典型的流化催化裂化操作中已知的构造和条件来操作。例如,再生区167可以作为流化床来操作,来生产包含燃烧产物的再生废气,其通过管道177排出。热的再生的催化剂从再生区167穿过管道169转移到提升管161的底部部分,来与烃原料混合,如上所述。在一个实施方案中,可以使用本文所述的催化剂的合适的流化催化裂化单元150可以类似于美国专利号7,312,370、6,538,169和5,326,465中所述,其在此通过参考引入。通常,用于使用本文的催化剂的合适的提升管流化催化裂化单元的反应器的操作条件包括:反应温度约480℃-约650℃,在某些实施方案中约500℃-约620℃,在另外的实施方案中约500℃-约600℃;反应压力是约1Kg/cm2-约20Kg/cm2,在某些实施方案中约1Kg/cm2-约10Kg/cm2,在另外的实施方案约1Kg/cm2-约3Kg/cm2;接触时间(反应器中)是约0.5秒-约10秒,在某些实施方案中约1秒-约5秒,在另外的实施方案中约1秒-约2秒;和催化剂与进料之比是约1:1-约15:1,在某些实施方案中约1:1-约10:1,在另外的实施方案中约8:1-约20:1。在某些实施方案中,提供配置有下流式反应器的流化催化裂化单元,其在促进轻质烯烃、特别是丙烯形成,和使消耗轻质烯烃的反应包括氢转移反应最小化的条件下操作。图2是下流式流化催化裂化单元的简化示意图。流化催化裂化单元250包括反应器/分离器260,其具有反应区262和分离区264。流化催化裂化单元250还包括用于再生用过的催化剂的再生区266。具体地,将装料236引入反应区,在某些实施方案中伴随有蒸汽或其他合适的气体,用于雾化进料(未示出)。将来自于再生区266的有效量的经加热的新鲜的或热的再生的固体裂化催化剂颗粒输送到反应区262的顶上,其也例如穿过向下导向的管道或管268(通常称作转移管线或立管)转移到反应区262顶部的取出井或料斗(未示出)。热的催化剂流典型地进行稳定化,以均匀导入反应区262的混合区或进料注入部分中。将装料236通过典型地与再生的催化剂进入反应区262的引入位置紧邻布置的进料注入喷嘴来注入混合区中。这些多个注入喷嘴使得催化剂和油彻底和均匀地混合。一旦装料接触热的催化剂,发生裂化反应。烃裂化产物、未反应的进料和催化剂混合物的反应蒸气快速流过反应区262的其余部分,和进入反应器/分离器260底部的快速分离区264中。裂化的和未裂化的烃穿过管道或管270导入本领域已知的常规产物回收段,来产生流化催化裂化产物轻质烯烃、汽油和循环油,并且丙烯收率最大化。如果需要控制温度,可以在紧邻分离区264之前在接近反应区262底部提供骤冷注入。该骤冷注入快速降低或停止裂化反应,可以用于控制裂化烈度。反应温度,即下流式反应器的出口温度,可以通过打开和关闭控制再生的催化剂从再生区266进入反应区262顶部的流动的催化剂滑阀(未示出)来控制。吸热裂化反应所需的热通过再生的催化剂来提供。通过改变热的再生的催化剂的流速,可以控制操作烈度或裂化条件来生产所需的产品方案。还提供汽提器272来将油与催化剂分离,其转移到再生区266。来自于分离区264的催化剂流到汽提器272的下段,其包括通过物流管线274将合适的汽提气体例如蒸汽引入到其中的催化剂汽提段。汽提段典型地具有几个挡板或规整填料(未示出),在其上向下流动的催化剂280与流动的汽提气体逆流经过。使用向上流动的汽提气体(其典型地是蒸汽)来“汽提”或除去任何留在催化剂孔中或催化剂颗粒之间的另外的烃。汽提的或用过的催化剂通过来自于燃烧空气流276的上升力穿过再生区264的提升管来运输。也可以与另外的燃烧空气接触的该用过的催化剂经历任何聚集的焦炭的受控燃烧。废气经由管道278从再生器除去。在再生器中,副产物焦炭燃烧所产生的热被转移到催化剂,升高到提供用于反应区262中的吸热裂化反应的热所需的温度。根据本文的方法,因为轻质溶剂原料与作为进料236的重质原料合并,所以选择初始溶剂脱沥青/脱金属方法中的溶剂与油之比,以提供足够的催化剂结焦来提供再生过程中的热平衡。在一个实施方案中,可以用于本文所述的方法中的合适的流化催化裂化单元250可以类似于美国专利号6,656,346和美国专利公布号2002/0195373中所述的那些,其二者在此通过参考引入。下流式反应器的重要性能包括在反应器顶部引入进料,并且向下流动,与提升管反应器相比更短的停留时间,和高的催化剂与油之比,例如约20:1-约30:1。通常,用于合适的丙烯生产的下流式FCC单元的反应器的操作条件包括:反应温度是约550℃-约650℃,在某些实施方案中约580℃-约630℃,在另外的实施方案中约590℃-约620℃;反应压力是约1Kg/cm2-约20Kg/cm2,在某些实施方案中约1Kg/cm2-约10Kg/cm2,在另外的实施方案中约1Kg/cm2-约3Kg/cm2;接触时间(在反应器中)是约0.1秒-约30秒,在某些实施方案中约0.1秒-约10秒,在另外的实施方案中约0.2秒-约0.7秒;和催化剂与进料之比是约1:1-约40:1,在某些实施方案中约1:1-约30:1,在另外的实施方案中约10:1-约30:1。为了清楚起见,在上面的FCC单元的说明中,在所附的示意图中未包括众多的阀门、温度传感器、电子过程控制器等,其是常规使用的,并且其是溶剂脱沥青/脱金属和流化催化剂裂化领域技术人员公知的。未示出用于常规流化催化剂裂化系统中的附件系统,例如空气补给、催化剂料斗、火炬油补给、烟气处置和热回收、用于存储可以添加或从再生器除去补充的和用过的/平衡催化剂的新鲜的和用过的催化剂料斗。实施例下面将描述用于本发明的分析方法。组成分析使用X射线荧光分析仪(由RigakuCorporation制造的“RIX3000”)来进行样品的组成分析(Zr、Hf、Ti)。用于测量的样品通过玻璃珠方法来制备。具体来说,将5g样品置于35nm内径的氯乙烯制环中,并且依靠压力模制机通过施加20吨的压力20秒来模制,以制备用于测量的样品。X射线荧光分析的条件如下所示;靶:Rh,分析晶体:LiF,检测器:闪烁计数器,激励:4kW的Rh容器,测量电压:55kV,电流:70mA。沸石中钠的测量使用原子吸附分光计(由HORIBALtd.制造的“Z5300”)来测量样品(沸石)中的钠含量。测量波长范围控制到190-900nm。晶格常数:使用X射线衍射计(由RigakuCorporation制造的“RINT2100”)来测量样品(沸石)的X射线衍射峰,并且晶格常数由其结果来计算。一种计算晶格常数的方法已经描述在本说明书中。下面显示了X射线衍射的条件;容器:Cu-K(α射线),2θ扫描范围:20-50度,扫描速度:0.01度/分钟,扫描步骤:0.01度。结晶度:结晶度由样品(沸石)的X射线衍射峰来计算。所以计算方法已经描述在本说明书中。SiO2/Al2O3摩尔比:Si和Al的峰强度比由样品(沸石)的X射线衍射峰测定,并且它产生SiO2与Al2O3的摩尔比。比表面积和孔体积:使用吸附测量装置(由QuantachromeInstrumentCorporate制造的全自动气体吸附装置“AUTOSORB-1”)来将0.02-0.05g样品(沸石或加氢裂化催化剂)在室温脱气5小时,然后在液氮温度下测量吸附解吸等温曲线,来使用多点方法的BET式计算比表面积/质量。实施例1在USY沸石制备后,将催化剂例如在750℃用蒸汽准平衡化13小时。催化剂是新鲜的,并且不包含任何金属。进行该制备步骤来制备用于FCC催化剂性能测试的催化剂,如表1所示。FCC催化剂A超稳定Y沸石首先,将50.0kg的NaY沸石(下文也称作“NaY”)悬浮于500升(下文也表达为“L”)温度60℃的水中,NaY的SiO2/Al2O3摩尔比是5.2,单位晶胞尺寸(UD)是2.466nm,比表面积(SA)是720m2/g和Na2O含量是13.0质量%。此外,向其中添加14.0kg硫酸铵。将形成的悬浮液在70℃搅拌1小时,并过滤。将形成的固体用水清洗。然后将固体用温度60℃的硫酸铵溶液(14.0kg硫酸铵溶解在500L水中)清洗,用温度60℃的500L水清洗,在130℃干燥20小时,由此提供约45kg的Y沸石(NH465Y),其中NaY中所含的65%的钠(Na)与铵离子进行离子交换。NH465Y中Na2O的含量是4.5质量%。将NH465Y40kg在饱和水蒸气气氛中在670℃烧制1小时来形成氢-Y沸石(HY)。将HY悬浮在温度60℃的400L水中。然后向其中添加49.0kg的硫酸铵。将形成的混合物在90℃搅拌1小时,并且用温度60℃的200L水清洗。混合物然后在130℃干燥20小时,由此提供约37kg的Y沸石(NH495Y),其中初始NaY中所含的95%的Na与NH4离子交换。将NH495Y33.0kg在饱和水蒸气气氛中在650℃烧制1小时,由此提供约15kg的超稳定Y沸石(下文也称作“USY(a)”),其SiO2/Al2O3摩尔比是5.2,单元晶胞尺寸(UD)是2.438nm,结晶度是98%,比表面积(SA)是635m2/g,和Na2O含量是0.60质量%。接着,将2.0kg的该USY(a)悬浮于温度25℃的20L水中。制备3.82kg的25质量%硫酸。然后添加106g的含有18质量%硫酸锆的溶液和37g的含有33质量%硫酸钛的溶液。将形成的混合物在室温搅拌1小时。将溶液添加到悬浮的USY溶液中,并且在室温搅拌3小时。在混合物过滤和形成的固体用20L水清洗并在130℃干燥20小时之后,回收了约1.2kg的钛-锆取代的沸石(下文也称作“Ti-Zr-USY”),其SiO2/Al2O3摩尔比是29.6,单元晶胞尺寸(UD)是2.436nm,结晶度是83%,比表面积(SA)是697m2/g,TiO2含量是0.96质量%,和ZrO2含量是0.49质量%。重量4000g的包含浓度12.5质量%的SiO2的硅溶胶(二氧化硅基粘合剂的一个例子)如下来制备:同时和连续添加2941g的包含浓度17质量%的SiO2的水玻璃和1059g的浓度25质量%的硫酸。向该硅溶胶中添加重量基于干重给出的950g高岭土和250g活性氧化铝,并且添加800g的用25质量%硫酸制备以使pH是3.9的TiZrUSY沸石浆料。将该浆料混合物喷雾干燥来形成平均粒径60微米的球形颗粒。将获得的球形颗粒清洗,与稀土金属(RE)氯化物的水溶液(该溶液包含铈和镧的氯化物;以下同样适用)接触来离子交换,以使得RE2O3的含量比是1.0质量%,然后在135℃的烘箱中干燥。以此方式获得了FCC催化剂A,其比表面积(SA)是279m2/g,TiO2含量是1.19质量%,ZrO2含量是0.53质量%,Al2O3含量是23.2质量%,稀土氧化物含量0.78质量%。流化催化裂化反应测试流化催化裂化催化剂性能测试以ASTM微活性测试(MAT)装置和ASTM方法号D3907-03(2008),标题为“StandardTestMethodforTestingFluidCatalyticCracking(FCC)CatalystsbyMicroactivityTest”中定义的方案来进行。在反应测试之前,将用于流化催化裂化的催化剂在750℃的温度用蒸汽准平衡化13小时。两组ASTM-MAT测试使用来源于阿拉伯原油的VGO进行,其性质显示在表1中。测试在两个温度,515℃(常规FCC条件)和600℃(丙烯生产FCC条件),使用3:1-6:1的催化剂与油之比和30秒的停留时间来进行。收集两种液体和气体产物,并且使用气相色谱法来分析。基于质量计算转化率和产物收率。在完成ASTM-MAT之后,从测试反应器收集催化剂样品,并且测量固体焦炭沉积物的量。气体产物应当分析以下组分:氢气、甲烷、乙烷、丙烷、丙烯、异丁烷和正丁烷以及丁烯。液体产物分析以下组分:汽油,其沸点范围从戊烷沸点到216℃的温度,轻质循环油(LCO),其沸点范围是216℃-343℃,和重质循环油(HCO),其沸点是343℃和更高,表示为343+馏分。转化率典型地是作为气体产物加上焦炭和加上汽油馏分的质量百分比的总和来计算。产物收率定义为产物组分的质量除以全部产物包括气体、液体和固体产物的总重量的百分数。表2和3显示了分别在常规FCC条件和丙烯生产条件,包含Ti-Zr嵌入的USY沸石的催化剂的转化率和产物收率。表1减压瓦斯油性质性质方法单位值密度g/cc0.882API°29.1碳重量%85.08氢重量%12.08硫重量%2.46氮ppmw960SimDistD2887IBP℃2145/10V%℃311/33740/50℃409/42870/90℃468/518FBP℃588表2FCC催化剂A在常规FCC条件的MAT测试结果运行No.1234裂化温度,(℃)515515515515T.O.S.(s)30303030催化剂/油(重量/重量)3.114.065.126.60转化率(%)54.1068.4872.5878.41收率(重量%)氢0.020.030.030.04甲烷0.310.450.420.63乙烷0.370.530.460.67乙烯0.490.720.630.91丙烷0.440.700.760.98丙烯2.954.224.655.29异丁烷2.063.233.734.20正丁烷0.340.560.680.801-丁烯1.221.751.942.06异丁烯0.871.241.371.47顺式-2-丁烯1.401.811.811.80叔-2-丁烯0.861.231.391.441,3-丁二烯0.000.000.000.00汽油41.4650.1452.1454.78LCO20.5518.0817.2014.30HCO25.3513.4410.227.29焦炭1.321.842.573.33组(重量%)干燥气体(H2-C2)1.191.731.542.26LPG(C3-C4)10.1414.7616.3318.04轻质烯烃(C2=-C4=)7.7810.9911.7912.97LPG烯烃(C3=+C4=)7.2910.2611.1612.06总丁烯(C4=)4.346.046.506.77总气体11.3216.4917.8720.29表3FCC催化剂A在丙烯生产FCC条件的MAT测试结果运行No.5678裂化温度,(℃)600600600600T.O.S.(s)30303030催化剂/油(重量/重量)3.284.255.536.73转化率(%)75.2180.3182.9483.40收率(重量%)氢0.080.090.110.12甲烷1.671.892.282.06乙烷1.721.852.231.91乙烯2.462.603.052.51丙烷1.281.491.791.81丙烯7.148.139.409.26异丁烷1.692.052.322.93正丁烷0.630.760.921.021-丁烯2.382.733.062.95异丁烯1.982.242.522.44顺式-2-丁烯3.023.333.693.55叔-2-丁烯1.792.052.292.221,3-丁二烯0.050.050.050.05汽油47.7948.9346.2047.22LCO15.3012.6911.3111.03HCO9.497.005.755.57焦炭1.542.133.053.35组(重量%)干燥气体(H2-C2)5.926.437.676.60LPG(C3-C4)19.9622.8226.0326.23轻质烯烃(C2=-C4=)18.8121.1224.0522.98LPG烯烃(C3=+C4=)16.3618.5221.0020.47总丁烯(C4=)9.2210.3911.6011.20总气体25.8829.2533.6932.83液体和气体产物使用气相色谱法(GC)装置来分析。重量百分比收率是组分的质量除以产物的总质量。转化率作为产物的总质量除以原料的总质量来计算。在表2和3中,氢、C1+C2和C3的和被称作干燥气体。丙烯表示为C3=。异C4、正C4和C4=的和称作轻质烯烃。LCO指的是轻质循环油,HCO指的是重质循环油,两种流体是FCC方法的典型产物。对比催化剂性能测试结果揭示,在78重量%转化率水平,分别对于常规和丙烯生产FCC条件来说,丙烯生产是8.0重量%和5.3重量%,轻质烯烃生产是13重量%和21重量%。实施例2两组高级催化剂评价(ACE)测试使用来自于阿拉伯轻质/重质VGO的加氢裂化的二级加氢裂化单元未转化的底部物来进行,其性质显示于表4中。第一测试用市售的轻质烯烃来进行,这产生了基于USY沸石的催化剂,其包括添加剂(25%的催化剂)来增加轻质烯烃生产。第二测试用Ti-Zr-Y沸石催化剂(FCC催化剂A)来进行。测试在600℃(丙烯生产FCC条件),使用3:1-6:1的催化剂与油比率和30秒的停留时间来进行。收集液体和气体产物二者,并且使用气相色谱法进行分析。基于质量计算转化率和产物收率。在完成ACE测试后,从测试反应器中收集催化剂样品,并且测量固体焦炭沉积物的量。气体产物分析以下组分:氢气、甲烷、乙烷、丙烷、丙烯、异丁烷和正丁烷以及丁烯。液体产物分析以下组分:汽油,其沸点范围从戊烷沸点到216℃的温度,轻质循环油(LCO),其沸点范围是216℃-343℃,和重质循环油(HCO),其沸点是343℃和更高,表示为343+馏分。表5显示了与市售的生产轻质烯烃的包含添加剂的催化剂相比,Ti-Zr嵌入的USY沸石对于增加在丙烯生产条件用加氢裂化器底部物的轻质烯烃生产的转化率和产物收率。表4加氢裂化器底部物油的性质密度@15℃g/cm30.8342粘度@50℃15.1粘度@100℃4.643CCR重量%0.01苯胺点℃119.8C重量%85.57H重量%14.07N重量%<0.01S重量%0.0004碱氮ppm0Feppm<1Vppm<1Nippm<1IBP℃3025℃36610℃38920℃41130℃42450℃44470℃46880℃48490℃51195℃536FBP℃653表5市售FCC催化剂和Ti-Zr-USY催化剂(FCC催化剂A)在丙烯生产FCC条件的MAT测试结果本发明的方法和系统已经在上面和附图中进行了描述;但是,对本领域技术人员来说很显然可以进行改变,并且本发明的保护范围通过所述权利要求书来限定。当前第1页1 2 3