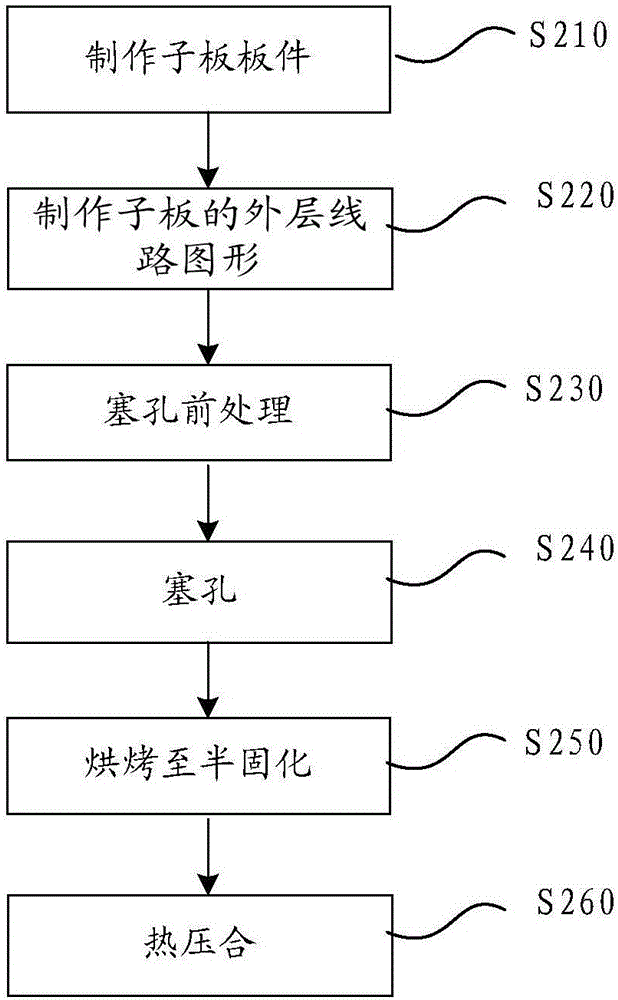
本发明涉及印刷电路板(PCB)领域,具体而言,涉及一种方法。
背景技术:多层PCB的内层埋孔的制作方法通常是,先进行钻孔、电镀,塞孔前处理(孔壁粗化)、塞孔、烘烤固化、研磨,再进行后续的线路及增层制作等。图1示出了根据相关技术的制作多层PCB的流程图,包括:步骤S110、制作子板板件:将多个双面板经压合后制成子板板件。步骤S120、制作子板的外层线路图形:在压合完成的子板上进行机械钻孔,电镀,线路图形制作。此制作过程中对干膜的盖孔能力要求较高,否则会造成破孔。可以依据埋孔的大小和盖孔能力来选择干膜类型和工艺参数。步骤S130、塞孔前处理:对完成线路图形制作的子板进行粗化处理,增强树脂与铜箔的结合力。步骤S140、塞孔:进行塞孔制作,为了确保塞孔饱满,控制树脂塞孔的饱和度为120%左右,即略微过饱和。步骤S150、烘烤固化:对塞孔树脂进行烘烤,使塞孔树脂完全固化。步骤S160、对塞孔后的子板进行磨刷,去除溢出埋孔的树脂。步骤S170、将子板进行氧化处理以及热压合,以制成多层PCB。发明人发现,此方法的制作流程较长,成本较高。
技术实现要素:本发明旨在提供一种多层PCB及其制作方法,以解决现有技术的成本较高的问题。在本发明的实施例中,提供了一种多层PCB的制作方法,包括:采用树脂对子板塞孔,塞孔的树脂的饱和度小于100%;对塞孔的树脂进行烘烤至半固化;将子板与粘结片交错叠加并热压合,以得到多层PCB。在本发明的实施例中,还提供了采用上述方法制作的多层PCB。本发明上述实施例的多层PCB及其制作方法因为塞孔树脂不多于100%,所以省略了磨刷步骤,降低了多层PCB的制作成本。附图说明此处所说明的附图用来提供对本发明的进一步理解,构成本申请的一部分,本发明的示意性实施例及其说明用于解释本发明,并不构成对本发明的不当限定。在附图中:图1示出了根据相关技术的多层PCB制作方法的流程图;图2示出了根据本发明实施例的多层PCB制作方法的流程图。具体实施方式下面将参考附图并结合实施例,来详细说明本发明。图2示出了根据本发明实施例的多层PCB制作方法的流程图,包括:步骤S210、制作子板板件,可以将多个双面板经压合后制成子板。步骤S220、制作子板的外层线路图形,可以在压合完成的子板上进行机械钻孔(用于制作埋孔)。步骤S230、塞孔前处理,可以对完成线路图形制作的子板进行粗化处理,增强树脂与铜箔的结合力。步骤S240、塞孔:采用树脂对预制的子板塞孔,塞孔的树脂的饱和度小于100%,这为省略磨刷步骤和保证压合平整度提供条件。步骤S250、烘烤至半固化:对塞孔的树脂进行烘烤至半固化。步骤S260、将子板与粘结片交错叠加并热压合,以制成多层PCB,在压合过程中可以让树脂完全固化。相关技术的塞孔步骤中,为了确保塞孔饱满,控制树脂塞孔的饱和度为120%左右,即略微过饱和;而本实施例中,采用树脂对预制的子板塞孔至不多于100%,即欠饱和。因为相关技术的塞孔步骤是过饱和,所以在塞孔树脂固化后,需要磨刷掉多余的树脂。而本实施例中因为是欠饱和,所以无需磨刷步骤,但是需要控制对塞孔树脂的固化程度,使得在热压合时,利用粘结片的半固化树脂 来填充未填满的埋孔。本实施例省略了磨刷步骤,因此降低了多层PCB的制作成本。另外,现有技术的埋孔烘烤固化通常是在常压下进行,树脂中的溶剂不易挥发完全,而且容易产生塞孔空洞,制作的成品板存在进行焊接时存在爆板隐患。本实施例在压合过程中让埋孔树脂完全固化,因为压合是真空环境,所以这样可以让塞孔树脂中的溶剂挥发更加完全,也可以避免塞孔空洞。优选地,根据在热压合中用于粘结子板的粘结片的厚度确定塞孔的树脂的饱和度。如果粘结片较厚,则可以填充埋孔较少的树脂;如果粘结片较薄,则填充埋孔较厚。在实际生产过程中,采用首件检测的方法确定塞孔树脂的饱和度。饱和度的检测方法为取塞孔固化后的样品做微切片,测量孔中间树脂段长度除以塞孔孔长度。由于后续压合的叠片结构变化,有可能采用不同种类、不同树脂含量、不同数量的半固化片,甚至多种类型组合等,所以可以计算单位区间半固化片中的树脂量和单位区间的塞孔数量确定塞孔的饱和度。优选地,确定塞孔的树脂的饱和度为80%-100%。优选地,对塞孔的树脂进行烘烤至固化度为50%-60%。本发明实施例还提供了采用上述的制作方法制作而成的多层PCB。从以上的描述中可以看出,本发明能有效地缩短埋孔制作流程,降低生产成本。以上所述仅为本发明的优选实施例而已,并不用于限制本发明,对于本领域的技术人员来说,本发明可以有各种更改和变化。凡在本发明的精神和原则之内,所作的任何修改、等同替换、改进等,均应包含在本发明的保护范围之内。