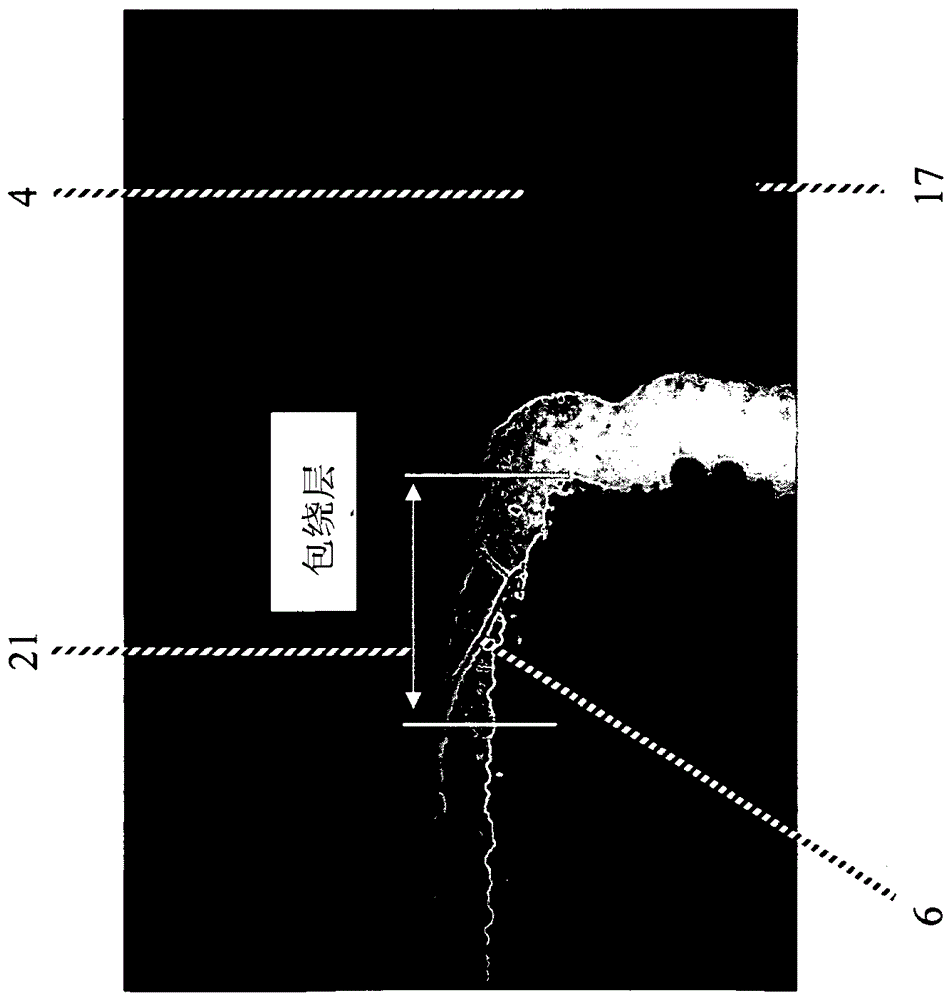
制造具有带包绕镀层的通道的印刷电路板的方法相关申请的交叉引用无关于联邦政府赞助的研发的声明无光盘中的序列表、表格或计算机程序无技术领域本发明总的涉及用于制造具有至少一个导电通道的多层式印刷电路板的方法。本发明更具体地涉及用于制造具有带包绕镀层(wrapplating)的至少一个通道(via)的电路板的改进的方法。
背景技术:现代电子设备中的多层式印刷电路或印刷电路板(“PCB”)包括一个或多个成对的电路层。每个成对的电路层包括绝缘芯层,该绝缘芯层也称为载体或基材。芯层包括相对的第一表面和第二表面,电子电路设置在第一表面和第二表面上。这些电子电路一般形成并图案化为通过焊盘或互连结构来接收电子部件。成对的电路层通过在绝缘芯的第一侧和绝缘芯的第二侧上用第一薄片层来层压绝缘芯而形成。层压的芯被处理(镀覆和蚀刻)以在层压芯的外侧表面上形成电路迹线和焊盘。所产生的夹在一对相对的电路层之间的绝缘基板能够用来形成多层式印刷电路板中的(成对的电路层的)子元件。在多层式印刷电路板中,上述成对的电路层(夹层布置)构成子元件,该子元件与一个或多个其他的子元件层叠,以形成多层式印刷电路板。所述多个成对的电路层被物理地和电子地连接以形成电路板。这种多层式印刷电路板通过将介电层(通常为预浸物或其他合适的绝缘粘结剂)布置在子元件之间以及在压力机中以介电层位于子元件之间的方式层叠子元件而创建。介电层一般是可热固的或者设置有粘结剂。在让介电层和/或粘结剂固化之后,形成包括多个成对的电路层的多层式基板。在基板中,介电层被插置在成对的电路层(子元件)之间。基板具有与第二侧处于相对的关系的第一侧。一种制造PCB的方法涉及在基板的第一侧和基板的第二侧上用第一薄片层层压包括所述一个或多个成对的电路层的基板。通常由铜制造的每个导电薄片继而可以包括一个或多个层。应用于基板的每侧的薄片层利用本领域已知的层压工艺附着于基板。这种层压工艺一般涉及向基板的两个主要表面应用粘结剂(预浸物或黏接片)以及然后向每个表面应用薄片层以形成薄片-基板-薄片叠层。以基板位于薄片层之间的方式层叠的薄片层被布置在压力机中并被允许固化。初始层压过程的最终结果是薄片层压基板。在形成薄片层压基板之后,在薄片层压基板的一个或两个侧面中钻出一个或多个导通孔(viahole)。所述一个或多个导通孔具有相对端。所述一个或多个导通孔的侧壁然后被镀覆导电材料以提供电路层之间的导电互连。在多层式PCB中,通道可以从PCB的外侧表面延伸穿过电路层的整个叠层并且延伸到相对的PCB外侧表面。可替代地,在多层式PCB中,通道可以是盲孔或埋孔。为了简便起见,术语“通道”在本申请中用来表示在此处描述的处理之后的镀覆通孔结构。术语“导通孔”用来表示在此处描述的PCB形成处理步骤中所涉及的孔结构。因此,如本文使用的,导通孔是未完成的通道。在一种PCB制造方法中,将形成通道的导通孔在上述层压步骤之后形成在层压基板中。常规地,导通孔通过机械或激光钻孔而形成。在导通孔形成在层压基板中之后,薄片层压基板被镀覆(一般通过化学镀)以向导通孔的侧壁添加(金属化)第一导电层。然后将图像点或凸点图案应用到薄片层压基板的表面,使得凸点镀层可以形成在导通孔的周围。薄片层压基板然后将伴随着导通孔的填充一起经历接下来的制备和镀覆步骤,以形成最终的印刷电路板。填充导通孔加强了PCB的导电性能并且可以提高最终的通道的结构可靠性。在PCB制造过程期间的哪个阶段填充导通孔取决于制造商。在涉及导电墨填充材料的一种示例性工艺中,在添加第一导电层到导通孔的侧壁上之后,导通孔被填充理想的填充材料。填充材料被允许固化。被填充的导通孔的端部然后被平坦化——通常产生凸点镀层的表面的去除的过程。在此最后的步骤之后,面板经历进一步的成像并且将另一导电层添加到薄片层压基板的两侧上,包括填充的导通孔的端部上,从而形成通道。在具有根据诸如以上所述之类的已知方法制造的墨填充通道的PCB中存在连接性和可靠性问题。这些问题通常将在部件被应用到完成的PCB上时显现出来。关于这一点,应用到通道的顶部的导电层或导电帽与通道的镀铜(金属化的)壁分离。已经研发了多种PCB制造方法来应对上述壁-表面导体分离。这些方法致力于改善PCB的“包绕镀层”。这种“包绕镀层”或“包绕层”指的是在围绕(即,包绕)导通孔的区域应用到PCB的导电材料。该包绕区域通常由于创建包绕区域所需的相继的镀覆步骤而称为“添加包绕层”。通过使包绕镀层变厚,减小了通道的侧部上的导体与表面导体分离的倾向。然而,仅仅使包绕镀层加厚并没有完全消除表面导体与金属化的通道壁的分离。实际上,包绕镀层的这种加厚可能由于层压基板的表面上的不一致的镀层厚度分布或者由于通道填充过程之后的不一致的平坦化而导致PCB的不可靠性。PCB制造时的接连的镀覆步骤还可能导致通道和通道包绕层上的镀层过厚。这种过厚是不理想的,因为其能够由于PCB的表面上的电路迹线和部件的不断增加的密度而导致问题。一种减少与变厚的包绕镀层相关联的问题的方法涉及PCB制造过程期间的导通孔周围的薄片层或导电层中的蚀刻间隙(clearance)。图1示出了根据已知的方法形成通道的工艺流程图。在该工艺中,在将钻出导通孔的位置处在薄片层压基板的薄片层中蚀刻出圆形间隙。该间隙的直径比期望得到的导通孔的直径大。因此,当在间隙区域中钻出导通孔之后,产生具有阶梯状边缘的导通孔。边缘的内部(“内缘”)由将薄片层粘结于基板的绝缘粘结剂形成。该内缘位于由薄片层形成的外缘的表面下方。通过在导通孔周围蚀刻出间隙,能够减少镀层的过厚以及与其相关联的问题。图2示出了根据这种间隙蚀刻方法形成的通道。然而,间隙蚀刻以实现通道包绕层完整性的方法存在缺点。当前实现高质量的通道包绕层和蚀刻精细特征的方法通常导致以废料形式的相对大量的材料损失。这种损失源自于需要接连地对薄片层压基板进行面板镀覆以形成包绕层。高废料损失转化成对制造商的较高制造成本并最终转化成对消费者的较高PCB成本。除了废料损失之外,这种面板镀覆还产生不均匀的表面铜,这迫使PCB制造商选择性地蚀刻不均匀的区域。因此,需要一种产生高质量的通道包绕层而不存在依赖于间隙蚀刻和相关联的接连镀覆的方法的缺点的改进的PCB制造工艺。
技术实现要素:根据本发明的一个实施例,一种用于制造具有至少一个导电通道的PCB的方法包括在基板的第一侧和基板的第二侧上用第一薄片层层压基板(包括一个或多个层叠的电路层对)。然后在薄片层压基板的第一侧上形成导通孔。(导通孔也可以形成在薄片层压基板的第二侧上)。导通孔具有第一端和第二端。导通孔的第一端形成在薄片层压基板的第一侧上的薄片层中。导通孔从层压基板的第一侧上的第一薄片层贯通地延伸到薄片层压基板的至少一个电路层。与现有技术的方法相比,形成在第一薄片层中的导通孔的第一端被加工埋头孔(countersink),以形成表面处的斜切开口。导通孔的埋头孔加工从孔的开口周围有角度地地去除了薄片层(表面铜)。在本发明的工艺的一个实施例中,在埋头孔加工过程期间,除了第一薄片层之外,位于薄片层下方的一些材料也被去除。在本发明的一个实施例中,导通孔从层压基板的第一侧上的第一薄片层延伸穿过层叠的电路层对并且穿过薄片层压基板的第二侧上的第一薄片层。在这种实施例中,导通孔的两端可以如本文所述地被加工埋头孔。在加工埋头孔之后,导通孔然后准备好被镀覆。例如,在准备好后,导通孔的侧壁和埋头孔表面被涂覆导电材料,优选地被化学镀铜或其他导电膜涂覆。在导电涂层被应用到导通孔的侧壁以及一个或多个埋头孔表面之后,可以根据常规的技术来处理层压基板。关于这一点,层压基板可以被闪熔镀覆一段较短的时期(例如,大约10分钟)以使导电涂层固化。面板可以具有根据客户定制所应用的图像凸点图案并且可以根据客户定制被电镀以添加凸点镀层铜。根据本发明的工艺形成的导通孔能够被填充非导电材料或导电材料。所述工艺通过从PCB形成的初始步骤中取消面板镀覆过程而提供紧密的行和间距。另外,所述工艺允许基部薄片不被二次镀覆接触,从而允许导电层在整个面板中保持一致并统一。这继而允许在面板的两端之间的精细特征的一致蚀刻。本发明的工艺还通过由于在蚀刻时具有较少的含金细条而具有较薄的基部薄片来允许需要非导电或导电通道填充的全金面板的更好的蚀刻。除了上述工艺之外,本发明还包括具有通过上述工艺形成的特征的层压基板和PCB。附图说明附图连同本文一起示出了本发明的示例性实施例,并且连同说明书一起用来阐释本发明的原理。除非另有说明,否则,所描述的实施例并不意在将总发明限制于特定的实施例。图1描绘了用于形成包绕镀层的现有技术的方法的工艺流。图2描绘了具有根据现有技术的方法形成的添加包绕镀层的通道。该通道填充有非导电墨材料。图3描绘了本发明的用于形成具有包绕镀层的通道的方法的一个实施例的工艺流。图4描绘了具有根据本发明的方法形成的包绕镀层的镀覆导通孔。该导通孔填充有非导电墨材料。图5是图4所示的导通孔的强化图,并且更详细地示出了导通孔的包绕区域,位于导通孔的端部的斜切侧壁表面的镀层在该包绕区域处与薄片层连接。图6是图4所示的导通孔的进一步的强化图,并且更加详细地示出了导通孔的包绕区域,位于导通孔的端部的斜切侧壁表面的镀层在该包绕区域处与表面铜有效地互锁。图7A至7D是示出了对于根据本发明形成的导通孔的优选示例性角度和尺寸的视图。图8描绘了具有根据本发明的方法形成的包绕镀层并且具有导电捕获焊盘的通道。具体实施方式在下面的详细描述中,仅仅通过说明的方式示出和描述了本发明的仅仅特定的示例性实施例。如本领域技术人员将认识到的,所描述的实施例可以在不偏离本发明的精神或范围的情况下通过多种不同的方式进行修改。因此,附图和说明书应当理解为在本质上是说明性的而非限制性的。在本发明的上下文中,用语“通道”包括通孔、盲孔、埋孔以及微孔。根据本发明的一个实施例,制造具有至少一个导电通道的PCB的方法包括在基板1的第一侧10和基板1的第二侧20中的每一侧上用第一薄片层2层压具有一个或多个层叠电路层对的基板1。在本发明的实施例中,起始表面铜薄片层2能够选择为任何合适的厚度。然后在薄片层压基板中形成具有第一和第二相对端4、5以及侧壁12的导通孔3。导通孔3的第一端4形成在基板的第一侧上的第一薄片层2中并且形成到基板中。导通孔3从薄片层压基板的第一侧10上的第一薄片层2贯通地延伸到薄片层压基板的至少一个电路层。位于薄片层压基板的第一侧上的通道3的第一端4然后被加工高精度埋头孔,以在薄片表面处形成“V形”或斜切的开口。导通孔3的埋头孔加工从孔的开口9周围有角度地去除薄片层(表面铜)并且为埋头孔3在其第一端4提供了斜切的侧壁表面6。该斜切的侧壁表面6产生导通孔3的端部处的凸起7。在本发明的工艺的一个实施例中,除了第一薄片层2之外,位于薄片层2下方的一些绝缘材料8在埋头孔加工过程期间也被去除。在本发明的替代实施例中,导通孔3从层压基板的第一侧10上的第一薄片层2延伸穿过电路层对的叠层并且穿过薄片层压基板的第二侧20上的第一薄片层2。在这种实施例中,导通孔3的第二端5形成在基板的第二侧上的薄片层2中,从而允许导通孔3的两端4、5都如本文所述地被加工埋头孔。在所述至少一个导通孔3被加工埋头孔之后,根据已知的方法对层压基板1进行处理。例如,在加工埋头孔之后,导通孔3准备好被涂覆。接下来,孔的侧壁6和斜切的侧壁表面6(或者在贯通的导通孔的情况下为多个表面)被涂覆导电材料15,优选地被涂覆化学镀铜或其他导电膜。在导电涂层被应用到孔的侧壁12和一个或多个斜切表面6之后,可以根据常规的技术对薄片层压基板进行处理。关于这一点,薄片层压基板可以被闪熔镀覆一段较短的时期(例如,10分钟)以使导电涂层固化。薄片层压基板然后被涂覆光刻胶(resist)并被成像以使间隙显像。薄片层压基板然后被镀覆到期望的铜厚度。光刻胶被剥离并且薄片层压基板然后被平坦化。导通孔3的埋头孔加工提供了间隙16,当被镀覆并被平坦化时,间隙16产生满足对于包绕层规格的IPC要求的通道包绕层。另外,从导通孔3的斜切的侧壁表面6延伸的镀层15根据规格与表面铜2邻接。埋头孔间隙(埋头孔的外径与导通孔的侧壁之间的距离)16通过孔的位置进行精确的定位并且产生间隙-孔位置的最优配准。本发明的工艺能够减少通常形成包绕所需的面板镀覆步骤的数量。这种减少产生了更细的行和空间,因为图像形成在未镀覆的铜薄片上。这继而产生了紧密且细小的特征的更一致且更统一的蚀刻。本发明因此消除了表面铜上的增加的镀覆铜厚度并且提供了印刷电路板的整个表面上的更一致的包绕镀覆厚度。这有助于将表面导体铜与镀覆的导通孔壁铜之间的结合保持在位,同时使得此时能够制造具有更细的特征和更紧密的几何尺寸的印刷电路板。图4、图5和图6描绘了具有根据本发明的方法形成的包绕镀层21的镀覆导通孔3。导通孔3能够填充有导电或非导电墨材料17。本发明的工艺的另一个优点源自于以下事实:导通孔的膝部18(包括斜切的侧壁表面)是成角度的,使得当被镀覆时,膝部可以具有与导通孔的侧壁一样多的铜,或者具有更多的铜。这与当前的工艺形成对比,其中在当前的工艺中,在平坦化之后,膝部上的镀层通常变薄到等于导通孔侧壁的厚度的一半的厚度(见图2)。此外,如图4、图5和图6所示,来自导通孔壁12并且延伸到斜切表面6上的铜包绕层21与层压基板的表面上的铜薄片2互锁,以便更好地结合。通过将新颖的埋头孔加工步骤集成到面板制备工艺中,总过程需要比当前方法少的处理步骤。特别地,面板制备工艺不包括从导通孔周围选择性地蚀刻铜所需的成像和蚀刻步骤。图7A至图7D示出了对于根据本发明形成的导通孔3的示例性角度和尺寸,其中示例性薄片层为大约0.0006英寸。在本发明的一个实施例中,利用130度钻尖将孔加工埋头孔至大约0.001英寸的深度。该实施例产生孔周围的、从孔的内侧(未镀覆)壁12开始测量的大约0.0021英寸的间隙16。在本发明的另一个实施例中,利用130度钻尖将孔加工埋头孔至大约0.002英寸的深度。该实施例产生孔周围的、从孔的内侧(未镀覆)壁12开始测量的大约0.0043英寸的间隙16。在本发明的另一个实施例中,利用127度钻尖将孔加工埋头孔至大约0.001英寸的深度。该实施例产生孔周围的、从孔的内侧(未镀覆)壁12开始测量的大约0.002英寸的间隙16。在本发明的另一个实施例中,利用127度钻尖将孔加工埋头孔至大约0.002英寸的深度。该实施例产生孔周围的、从孔的内侧(未镀覆)壁12开始测量的大约0.004英寸的间隙16。通过取消间隙蚀刻步骤,本发明的工艺完全消除了与在蚀刻间隙中定位导通孔相关的问题。另外,导通孔可以在一个步骤中被钻孔和加工埋头孔,从而允许间隙与导通孔的高精度配准。因此,间隙形成步骤能够与导通孔钻孔步骤相组合。图8描绘了根据本发明的方法形成、并且具有捕获焊盘(导电帽)25的优选的示例性完成通道。如图8所示,本发明的工艺还减少或消除了由当前的PCB制造工艺的接连的镀覆步骤产生的高凸点镀层。然而,原型PCB的制造已经表明,该工艺在捕获焊盘与通道之间的连接中产生较大量的铜,这种结果继而会导致更高的连接可靠性。此外,通过使用如本文公开的埋头孔加工工艺,最终的捕获焊盘25在其焊盘表面27中具有微凹的弯曲部分26。该弯曲部分26通过允许焊盘弯曲部分26托住芯片的锡球而加强了芯片焊接。本发明还包括一种印刷电路板(PCB),该PCB包括与第二外表面电路层处于相对关系的第一外表面电路层。该PCB还包括以叠层构型设置在第一外表面电路层与第二外表面电路层之间的一个或多个内部电路层。该PCB包括至少一个通道。所述至少一个通道具有侧壁12、第一端4以及第二端5。侧壁12具有导电镀层15。通道3的第一端4的侧壁镀层15被斜切(形成在斜切表面6上)并且与第一外表面电路层2电接触。通道从PCB的第一外表面电路层贯通地延伸到所述一个或多个内部电路层中的至少一个。在本发明的PCB的替代性实施例中,通道从层压基板的第一侧上的第一外表面电路层延伸,穿过整个层叠的内部电路层对,使得通道的第二端5延伸到第二外表面电路层并且形成在第二外表面电路层中。在这种实施例中,通道的第二端的侧壁镀层15被斜切(形成在斜切表面6上)并且与第二外表面电路层电接触。本发明还包括一种薄片层压基板1,该薄片层压基板1包括至少一个埋头导通孔3。薄片层压基板包括基板1,基板1具有处于层叠构型的一个或多个电路层对。基板具有第一侧10和第二侧20。基板的第一侧和第二侧对应于薄片层压基板的第一侧和第二侧。薄片层压基板包括层压到基板的第一侧和第二侧中的每一侧的薄片层2。薄片层压基板还进一步包括在薄片层压基板中的至少一个导通孔3。导通孔3具有第一端4和第二端5。导通孔3的第一端4从薄片层压基板的第一侧上的第一薄片层2贯通地延伸到薄片层压基板的至少一个电路层。导通孔3的第一端4的侧壁12具有与薄片层2的表面会合的斜切表面6。导通孔3的第一端4的斜切侧壁表面6包括薄片层。在本发明的层压基板的一个实施例中,除了薄片层2之外,导通孔3的第一端4的斜切表面6还包括绝缘材料8。在本发明的替代实施例中,导通孔3从层压基板的第一侧10上的第一薄片层2延伸,穿过电路层对的叠层,并且穿过薄片层压基板的第二侧上的第一薄片层2。在该实施例中,导通孔3的第二端5形成在薄片层压基板的第二侧20上的薄片层2中并且具有在薄片表面处的斜切开口。在薄片层压基板的优选实施例中,所述至少一个导通孔包括在所述至少一个导通孔的侧壁12和斜切侧壁表面6上的第一导电层15。在一个实施例中,导通孔的埋头孔表面6可以包括第一薄片层2和绝缘材料8。在薄片层压基板的一个实施例中,第一导电薄片层2具有大约0.0006英寸的厚度,导通孔的第一端4具有大约0.001英寸的埋头孔深度,并且导通孔的第一端的埋头孔表面6之间的角度30为大约130度。在薄片层压基板的另一个实施例中,第一导电薄片层2具有大约0.0006英寸的厚度,导通孔的第一端4具有大约0.002英寸的埋头孔深度,并且导通孔的第一端的埋头孔表面6之间的角度30为大约130度。在薄片层压基板的另一个实施例中,第一导电薄片层具有大约0.0006英寸的厚度,导通孔的第一端具有大约0.001英寸的埋头孔深度,并且导通孔的第一端的埋头孔表面之间的角度30为大约127度。在薄片层压基板的另一个实施例中,第一导电薄片层具有大约0.0006英寸的厚度,导通孔的第一端具有大约0.002英寸的埋头孔深度,并且导通孔的第一端的埋头孔表面之间的角度30为大约127度。根据以上所述,本发明的实施例增强了印刷电路板的通道的包绕镀层的一致性,从而向印刷电路板提供了额外的可靠性,并且使得印刷电路板的设计人员和/或制造商能够设计和制造具有相对精细的特征和/或紧密的几何尺寸的印刷电路板。此外,本发明增强了印刷电路板的通道的包绕镀层的一致性,从而向印刷电路板提供了额外的可靠性,并且使得印刷电路板的设计人员和/或制造商能够设计和制造具有相对精细的特征和/或紧密的几何尺寸的印刷电路板。尽管已经关于特定的示例性实施例描述了本发明,但本领域技术人员应当理解,本发明不局限于所公开的实施例;相反,本发明意在涵盖包括在本发明的精神和范围内的各种改动及其等同形式。