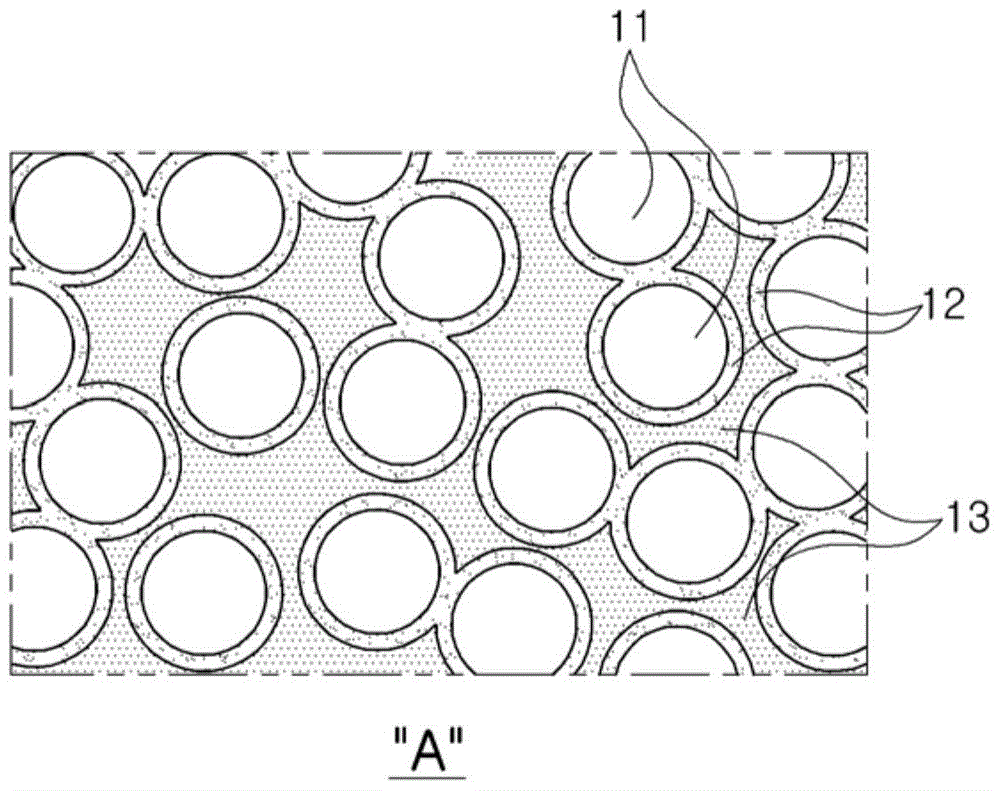
多层电子元件相关申请的交叉引用本申请要求2014年6月24日提交至韩国知识产权局的韩国专利申请号10-2014-0077157的优先权,其内容通过参考并入本文。技术领域本发明涉及一种多层电子元件。
背景技术:感应器是一种电子元件,是一种与电阻器和电容器共同构成电子电路以消除噪音的典型无源元件。在多层电子元件中,多层感应器可以具有如下结构:使用磁性材料如铁素体等作为主要材料在绝缘层上形成导电图案,其上形成有具有导电图案的绝缘层层叠以形成多层体中的内部线圈部分,且用于电连接内部线圈部分至外部电路的外部电极形成在多层体的外表面上。随着对能够在高频波段下使用且具有改善的能量消耗效率和直流(DC)偏压特性的多层感应器的需求的不断增长,已开发出使用金属粉末来代替铁素体的多层感应器。[现有技术文献](专利文献1)日本专利特许公开号:2007-027354。
技术实现要素:本发明的一种示例性实施方式可以提供一种具有优异的直流(DC)偏压特性和高品质(Q)因子以及改进的机械强度的多层感应器。根据本发明的一种示例性实施方式,多层电子元件的特征在于,在包含于磁性体周缘部分中的金属磁性颗粒的表面上形成的金属氧化物膜的平均厚度比在包含于磁性体中心部分中的金属磁性颗粒的表面上形成的金属氧化物膜的平均厚度要厚。在包含于磁性体周缘部分中的金属磁性颗粒的表面上形成的金属氧化物膜的平均厚度可以为200nm至300nm,在包含于磁性体中心部分中的金属磁性颗粒的表面上形成的金属氧化物膜的平均厚度可以为50nm至200nm。聚合物树脂可以填充在其上形成有金属氧化物膜的金属磁性颗粒之间的间隙。附图说明以下结合附图的详细说明,可以更清楚地理解本发明的以上和其它方面、特征及优点,其中:图1是根据本发明的一种示例性实施例的多层电子元件的局部剖切透视图;图2是图1的A部分的放大的示意图;图3是沿着图1的线I-I’的横截面图;以及图4是沿着图1的线II-II’的横截面图。具体实施方式在下文中,将参考附图来详细描述本发明的示例性实施方式。然而,本发明可以以多种不同形式体现,并且不应该被解释为限于本文描述的具体实施方式。相反地,提供这些实施方式是为了使本发明是充分的和完整的,并将本发明的范围充分传达给本领域技术人员。在图中,为清楚起见,元件的形状和大小可能被放大,并且在全文中相同的附图标记用于指代相同或相似的元件。多层电子元件在下文中,根据本发明的一种示例性实施方式的多层电子元件。尤其是,将多层感应器作为一个示例进行说明,但本发明并不限于此。图1是根据本发明的一种示例性实施例的多层电子元件的局部剖切透视图。参见图1,根据本发明的一种示例性实施方式的多层电子元件100可以包括磁性体110、设置在磁性体110中的内部线圈部分120和设置在磁性体110的外表面上且电连接至内部线圈部分120的外部电极130。在根据本发明的一种示例性实施方式的多层电子元件100中,图1的“L”方向是指“长度方向”,图1的“W”方向是指“宽度方向”,且图1的“T”方向是指“厚度方向”。磁性体110可以具有在厚度T方向上彼此相对的第一主表面S1和第二主表面S2,在宽度W方向上彼此相对的第一侧表面S5和第二侧表面S6和在长度L方向上彼此相对的第一端表面S3和第二端表面S4。磁性体110可以通过层叠多个金属磁性层10而形成,多个金属磁性层10可以处于烧结状态,相邻的金属磁性层10可以相互结合起来,使得它们之间的边界在没有扫描型电子显微镜(SEM)下不明显。所述磁性体110的形状和尺寸不限于本发明示例性实施方式所说明的那些形状和尺寸,金属磁性层10的厚度可以根据所述多层电子元件100的目标电容(targetcapacitance)而任意地改变。图2是图1的A部分的放大的示意图。参见图2,所述金属磁性层10可以包括金属磁性颗粒11和形成在所述金属磁性颗粒11的表面上的金属氧化物膜12。所述金属磁性颗粒11可以由软磁性合金如含有选自由Fe、Si、Cr、Al和Ni组成的组中的至少一种的合金形成,所述合金可以是Fe-Si-Cr系合金,但并不限于此。例如,所述金属磁性颗粒11可以由含有87重量%或更多的Fe,4重量%至6重量%的Cr和余量的Si的Fe-Si-Cr系合金形成。当所述金属磁性颗粒11由Fe-Si-Cr系合金形成时,在Fe的含量小于87重量%的情况下,磁特性会显著降低。此外,在Cr的含量为4重量%至6重量%的情况下,可以阻止在高烧结温度下的Fe的氧化;另一方面,在Cr的含量小于4重量%的情况下,则难以阻止制造所述多层感应器中在高烧结温度下的Fe的氧化,导致磁特性的损失;而在Cr的含量超过6重量%的情况下,会产生Cr氧化物的过量并增加更多的间隙,超出所需,导致磁特性的劣化。所述金属磁性颗粒11的最大粒子大小可以为15μm或更小。在所述金属磁性颗粒的最大粒子大小超过15μm的情况下,在高频下的磁心损耗(coreloss)会明显增加,使得在高频波段下的高品质(Q)因子会下降。所述金属磁性层10中的所述金属磁性颗粒11的粒子大小分布D50可以为3μm至5μm。粒子大小分布D50表示用激光衍射散射式粒度分布测定法(alaserdiffractionscatteringparticlesizedistributionmeasurementmethod)得到的在体积累积50%中的粒子大小。在所述金属磁性颗粒11的粒子大小分布D50小于3μm的情况下,磁导率(magneticpermeability)会降低;在在所述金属磁性颗粒11的粒子大小分布D50超过5μm的情况下,分散性会降低,且空气间隙的产生会增加,导致强度降低。进一步地,在高频下的磁心损耗会显著增加,导致Q因子的降低。所述金属磁性层10中的所述金属磁性颗粒11之间的间隔可以为5μm或更小。在所述金属磁性颗粒11之间的间隔超过5μm的情况下,填充因子(packingfactor)会减小,导致磁导率下降,以及空气间隙的产生会增加,导致强度下降。所述金属氧化物膜12可以通过所述金属磁性颗粒11中的至少一种组分的氧化而形成,例如,所述金属氧化物膜12可以含有Cr2O3。所述金属磁性颗粒11本身之间的以及所述金属磁性颗粒11与所述内部线圈部分120之间的绝缘性由所述金属氧化物膜12保证。在所述金属磁性颗粒的表面上形成的所述金属氧化物膜12可以结合到在与其相邻的金属磁性颗粒的表面上形成的所述金属氧化物膜12上,并且所述金属磁性颗粒11可以通过所述金属氧化物膜12的结合而结合。机械强度和绝缘性可以通过所述金属氧化物膜12的结合而得到提高。同时,所述金属磁性颗粒11可以通过没有彼此相互结合的所述金属氧化物膜12的部分而彼此相分离。在所述金属磁性颗粒相互结合的情况下,涡流损耗(eddycurrentloss)会增大,导致Q因子的下降。进一步地,所述金属磁性颗粒间的接触面积会增加,使得Q因子会由于交流电(AC)的增大而显著降低。在根据本发明的示例性实施方式的多层电子元件中,由于金属磁性颗粒11通过金属氧化物膜12的结合而结合,涡流损耗会降低,并且由于金属磁性颗粒11之间的直接接触面积不存在,由AC电流的增大导致的Q因子的降低会减小。因此,当将上述构造用于电感器时,具有高功率效率的优势。在根据本发明的示例性实施方式的多层电子元件中,在设置在磁性体110周缘部分中的金属磁性颗粒11的表面上形成的金属氧化物膜12的平均厚度比在设置在磁性体110中心部分中的金属磁性颗粒11的表面上形成的金属氧化物膜12的平均厚度要厚。如上所述,控制所述磁性体110的周缘部分和所述磁性体110的中心部分中的金属氧化物膜12的平均厚度不同于彼此,从而能够阻止磁导率的降低,增加电感(inductance),并改善直流(DC)偏压特性和Q因子。通过使用高倍率扫描型电子显微镜(SEM)观察磁性体110在厚度宽度(TW)方向上切割的横截面,测定所述金属氧化物膜的平均厚度。图3是沿着图1的线I-I’的横截面图;且图4是沿着图1的线II-II’的横截面图。参见图3和图4,在根据本发明的示例性实施方式的多层电子元件100中,从磁性体110的第一主表面S1和第二主表面S2、第一端表面S3和第二端表面S4、以及第一侧表面S5和第二侧表面S6分别到与磁性体110的厚度t的20%(即0.2t)在向内的方向上相对应的点的磁性体110的部分将被定义为磁性体110的周缘部分111;周缘部分111的内部边界内的磁性体110的部分将被定义为磁性体110的中心部分112。在此,在包含于周缘部分111中的所述金属磁性颗粒11的表面上形成的所述金属氧化物膜12的平均厚度比在包含于中心部分112中的所述金属磁性颗粒11的表面上形成的所述金属氧化物膜12的平均厚度要厚40nm至200nm。根据本发明的示例性实施方式,在包含于周缘部分111中的所述金属磁性颗粒的表面上形成的所述金属氧化物膜12的平均厚度可以为200nm至300nm。在包含于周缘部分111中的所述金属磁性颗粒的表面上形成的所述金属氧化物膜12的平均厚度小于200nm的情况下,DC偏压特性和高频波段下的Q因子会降低;在包含于周缘部分111中的所述金属磁性颗粒的表面上形成的所述金属氧化物膜12的平均厚度超过300nm的情况下,金属磁性颗粒的磁特性会由于金属氧化物膜而显著降低,使得磁导率、电感和低频波段下的Q因子降低(见表1)。在根据本发明的示例性实施方式的多层电子元件中,在包含于磁性体的中心部分112中的所述金属磁性颗粒的表面上形成的所述金属氧化物膜12的平均厚度可以为50nm至200nm。在包含于磁性体的中心部分112中的所述金属磁性颗粒的表面上形成的所述金属氧化物膜12的平均厚度小于50nm的情况下,高频波段下的Q因子和DC偏压特性会下降;在包含于磁性体的中心部分112中的所述金属磁性颗粒的表面上形成的所述金属氧化物膜12的平均厚度超过200nm的情况下,金属磁性颗粒的磁特性会由于金属氧化物膜而显著降低,使得磁导率、电感和低频波段下的Q因子降低(见表1)。所述金属磁性层10可以包括设置在其表面上形成有所述金属氧化物膜12的所述金属磁性颗粒11之间的间隙中的聚合物树脂13。可以通过将烧结的磁性体110在聚合物树脂中浸渍并进行压缩处理,或通过将聚合物树脂应用于烧结的磁性体110的表面并允许聚合物树脂被烧结的磁性体110所吸收而在所述金属磁性颗粒11之间的间隙填充聚合物树脂13。通过在属磁性颗粒11之间的间隙填充聚合物树脂13,可以改善强度并降低吸湿性。所述聚合物树脂13可以为选自由硅系树脂(siliconbasedresin)、环氧系树脂、酚醛系树脂、硅酸盐基树脂(silicatebasedresin)、聚氨酯系树脂、酰亚胺系树脂、丙烯酸系树脂(acrylbasedresin)、聚酯系树脂和聚乙烯系树脂组成的组中的至少一种。所述聚合物树脂13可以占所述金属磁性层10的横截面面积的10%至30%。在所述聚合物树脂13的面积小于10%的情况下,强度会降低,且在高湿条件下湿气会被吸收进所述磁性体内;而在所述聚合物树脂13的面积超过30%的情况下,磁导率会降低。下表1示出了根据在包含于磁性体110的周缘部分111和中心部分112中的所述金属磁性颗粒11的表面上形成的所述金属氧化物膜12的厚度变化的电感、Q因子和DC偏压特性的结果。在此,芯片尺寸(L*W)为2.00×1.20[mm],目标电感(Ls)为1.0[μH]。[表1]参见表1可以看出,当周缘部分中的金属氧化物膜的厚度为200nm至300nm且中心部分中的金属氧化物膜的厚度为50nm至200nm时,低频波段和高频波段下的Q因子以及DC偏压特性都是优异的。下面的表2示出了根据粒子大小分布D50和金属磁性颗粒(Fe-Si-Cr合金颗粒)的最大粒子大小变化的磁导率和Q因子的结果。[表2]参见表2可以看出,当金属磁性颗粒的粒子大小分布D50为3μm至5μm且金属磁性颗粒的最大粒子大小为15μm或更小时,低频波段和高频波段下的Q因子都是优异的。如上所述,根据本发明的示例性实施方式的多层电子元件具有优异的DC偏压特性、高Q因子和增强的机械强度。尽管示例性的实施方式已经示出并如上所述,但在不违背本发明所附的权利要求所限定的保护范围下,变型和修改对本领域的技术人员而言是显而易见的。