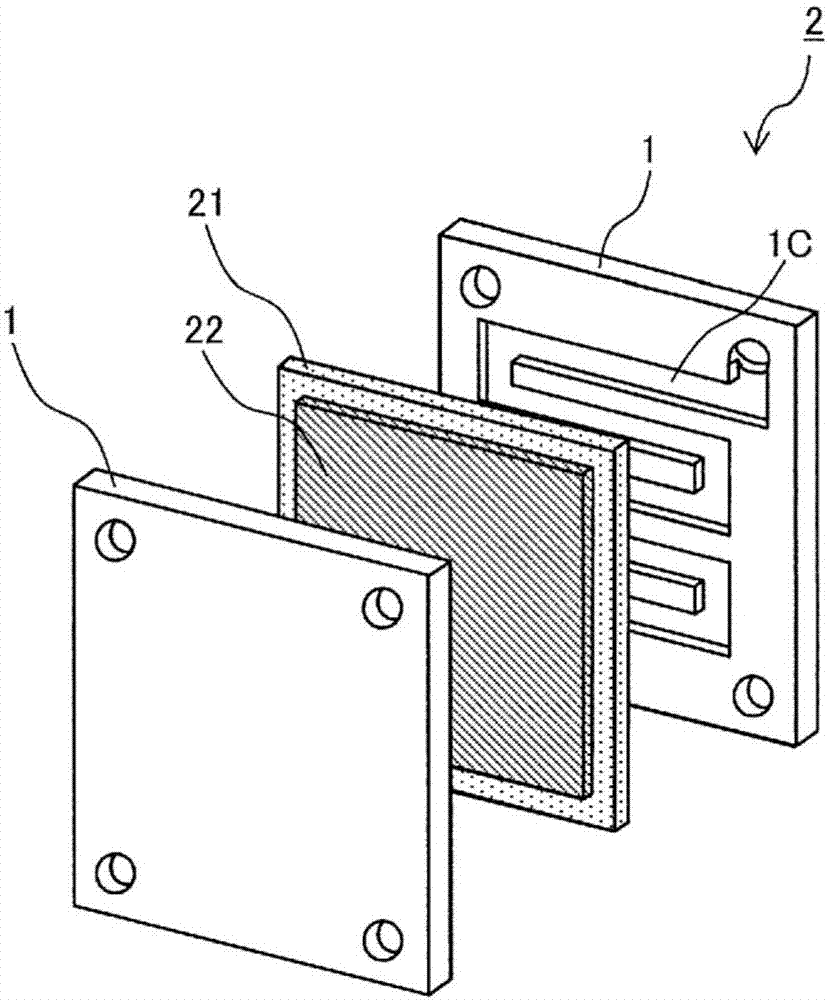
本发明涉及燃料电池用通电构件、燃料电池单元、燃料电池堆和燃料电池用通电构件的制造方法。
背景技术:
:在构成燃料电池堆的燃料电池单元中,一直将燃料电池用集电板、燃料电池用隔板等通电构件用作用于将所发的电汇聚起来的构件。燃料电池用集电板设于构成燃料电池堆的燃料电池单元的两端,燃料电池用集电板是用于从燃料电池堆获取电流的构件。燃料电池用隔板被用作构成燃料电池堆的燃料电池单元的构件,燃料电池用隔板具有下述功能:经由气体流路向电极供给燃料气体、空气,以及将电极产生的电子汇聚起来。以往,就上述这样的燃料电池用通电构件而言,通常使用通过在碳板形成气体流路做成的燃料电池用隔板。然而,在将碳板用作构成燃料电池用隔板的材料的情况下,存在这样的问题:材料成本、加工成本变大,气体阻隔性、强度不够。因此,期望代替碳板,而使用材料成本较低,且能够以更低的价格通过高速冲压加工形成气体流路的不锈钢、铝或钛合金等金属。相对于此,例如,专利文献1中公开了一种燃料电池用隔板,该燃料电池用隔板能够通过下述过程做成:将由金属制成的基材用作燃料电池用隔板的母材,通过电解镀,在基材上形成由规定金属构成的金属层和金镀层。现有技术文献专利文献专利文献1:日本特开2001-351642号公报技术实现要素:发明要解决的问题然而,就上述专利文献1所公开的燃料电池用隔板而言,有时,金镀层、金属层存在针孔等细微缺陷,导致金属层、基材的一部分从上述这样的针孔处暴露。而且,在将上述这样的燃料电池用隔板用作要在高温酸性气氛下使用的燃料电池单元的构件的情况下,存在这样的问题:有时,形成基材、金属层的成分从针孔部分大量溶出,导致燃料电池的性能降低。同样地,即使在将上述专利文献1所公开的燃料电池用隔板的结构,即通过在基材上形成由规定金属构成的金属层和金镀层做成的结构应用于燃料电池用集电板的情况下,也存在这样的问题:有时,燃料电池用集电板中的产生了针孔的部分的耐腐蚀性降低,导致燃料电池的性能降低。本发明的目的是,提供一种能够有效抑制基材、金属层的溶出,且耐腐蚀性优异的燃料电池用通电构件。用于解决问题的方案本发明人等发现,通过对在基材上形成至少一层金属镀层而成的表面处理基材,使用保护膜形成剂形成保护膜,之后,进行酸处理,能够达到上述目的,最终完成了本发明。即,采用本发明,能够提供一种燃料电池用通电构件,该燃料电池用通电构件是通过如下方式做成的,即:对于具有基材和形成在所述基材上的至少一层金属镀层的表面处理基材,使用保护膜形成剂在所述金属镀层上形成保护膜,之后,进行酸处理。本发明中,优选的是,所述保护膜形成剂包含由唑系化合物和具有硫醇基的化合物构成的混合物,和/或包含具有硫醇基的唑系化合物。本发明中,优选的是,所述酸处理是使用硫酸或硝酸进行的处理。本发明中,优选的是,燃料电池用通电构件在所述金属镀层上还具有金镀层。本发明中,优选的是,所述基材包括钢材或铝材。本发明中,优选的是,所述燃料电池用通电构件是燃料电池用隔板或燃料电池用集电板。采用本发明,能够提供一种燃料电池单元,该燃料电池单元是使用上述燃料电池用通电构件做成的。而且,采用本发明,能够提供一种燃料电池堆,该燃料电池堆是通过将多个上述燃料电池单元层叠起来做成的。而且,采用本发明,能够提供一种燃料电池用通电构件的制造方法,该燃料电池用通电构件的制造方法包括下述工序:在基材上形成至少一层金属镀层;使用保护膜形成剂,对形成有金属镀层的基材进行保护膜形成处理;及对经过所述保护膜形成处理的基材进行酸处理。而且,采用本发明,能够提供一种燃料电池用通电构件的制造方法,该燃料电池用通电构件的制造方法包括下述工序:在基材上形成至少一层金属镀层;在所述金属镀层上形成金镀层;使用保护膜形成剂,对形成有所述金属镀层和金镀层的基材进行保护膜形成处理;及对经过所述保护膜形成处理的基材进行酸处理。而且,采用本发明,能够提供一种燃料电池用通电构件,该燃料电池用通电构件具有基材和形成在所述基材上的金属镀层,所述金镀层在所述金镀层的暴露面的至少一部分具有使用保护膜形成剂形成的保护膜,所述基材在所述基材的暴露面的至少一部分具有通过酸处理形成的钝化膜。发明的效果采用本发明,能够提供一种燃料电池用通电构件,该燃料电池用通电构件能够有效抑制基材、金属镀层的溶出,由此,具有优异的耐腐蚀性。附图说明图1是表示使用本发明的实施方式的燃料电池用通电构件(隔板)做成的燃料电池单元的剖视图。图2是表示图1中的燃料电池单元的分解立体图。图3a是表示通过将燃料电池用通电构件(集电板)和图1及图2中的燃料电池单元层叠起来做成的燃料电池堆的立体图。图3b是表示图3a中的燃料电池堆的分解立体图。图4是表示用于形成本发明的燃料电池用通电构件的表面处理基材的一例的剖视图。图5是图4所示的表面处理基材10中的用附图标记v表示的部分的主要部分放大图。图6是对图4所示的表面处理基材10进行了使用保护膜形成剂进行的保护膜形成处理的情况下的、图4中用附图标记v表示的部分的主要部分放大图。图7是对图4所示的表面处理基材10进行了使用保护膜形成剂进行的保护膜形成处理并进行了酸处理的情况下的、图4中用附图标记v表示的部分的主要部分放大图。图8是表示本发明的另一实施方式的表面处理基材的剖视图。图9是表示本发明的又一实施方式的表面处理基材的剖视图。图10是表示评价实施例和比较例的燃料电池用通电构件的耐腐蚀性得到的结果的图表。图11是用于说明测量实施例和比较例的燃料电池用通电构件的电阻的方法的图。具体实施方式首先,将具有包含固体高分子的电解质膜21的固体高分子型燃料电池堆的结构作为使用本发明的燃料电池用通电构件(隔板)1的燃料电池堆3的一例来进行说明。图1是表示燃料电池堆3的结构单位即燃料电池单元2的剖视图,图2是表示燃料电池单元2的分解立体图,图3a是表示燃料电池堆3的立体图,该燃料电池堆3是通过将多个分别具有燃料电池用通电构件(隔板)1的燃料电池单元2和燃料电池用通电构件(集电板)31层叠起来做成的,图3b是表示燃料电池堆3的分解立体图。如图1所示,本实施方式的燃料电池单元2由电解质膜21、阳极22、阴极23、燃料电池用通电构件(隔板)1和燃料电池用通电构件(隔板)1构成。阳极22和阴极23从两侧夹着电解质膜21从而构成三明治结构,阳极22和阴极23是气体扩散电极。燃料电池用通电构件(隔板)1和燃料电池用通电构件(隔板)1再从两侧夹着该三明治结构,并且,燃料电池用通电构件(隔板)1和燃料电池用通电构件(隔板)1用于分别向阳极22和阴极23供给燃料气体和氧化气体,并且汇集通过电化学反应所产生的电力。为此,在阳极22与燃料电池用通电构件(隔板)1之间形成有燃料气体流路1a,在阴极23与燃料电池用通电构件(隔板)1之间形成有氧化气体流路1c。如图3a和图3b所示,在要实际地组装成燃料电池堆3的情况下,先将规定块数的上述燃料电池单元2层叠起来,再利用燃料电池用通电构件(集电板)31从两侧夹住层叠有规定块数的燃料电池单元。然后,向燃料电池单元2的阳极22供给含氢的燃料气体,向阴极23供给含氧的氧化气体,从而分别在阳极22和阴极23进行电化学反应,产生电力,利用上述的燃料电池用通电构件(隔板)1和燃料电池用通电构件(隔板)1将通过电化学反应产生的电力汇集起来,并且,利用燃料电池用通电构件(集电板)31进一步将上述电力汇集起来。因此,燃料电池用通电构件(隔板)1、燃料电池用通电构件(隔板)1和燃料电池用通电构件(集电板)31均为期望具有导电性的构件,本发明的燃料电池用通电构件能够用于上述这样的燃料电池用通电构件(隔板)1、燃料电池用通电构件(集电板)31等。接着,说明本实施方式的燃料电池用通电构件。另外,如上所述,本实施方式的燃料电池用通电构件能够应用于燃料电池用通电构件(隔板)1、燃料电池用通电构件(集电板)31。本实施方式的燃料电池用通电构件能够通过如下方式形成:对具有图4所示那样的结构的表面处理基材10依次先进行后述的使用保护膜形成剂进行的保护膜形成处理,再进行后述的酸处理。表面处理基材10通过如下方式做成:例如,如图4所示,在基材11上形成金属镀层12,再在金属镀层12上形成金镀层13作为最外层。另外,图4所示的例子表示的是表面处理基材10的最外层为金镀层13的例子,但是,在即使不形成金镀层13也能够确保足够的耐腐蚀性和导电性的情况下,也可以不在表面处理基材10形成金镀层13。在该情况下,金属镀层12构成表面处理基材10的最外层。下面,说明构成表面处理基材10的各层。基材11作为基材11,不受特殊限定,能够不受特别限制地使用钢、不锈钢、al、al合金、ti、ti合金、cu、cu合金、ni、ni合金等。基材11的厚度不受特殊限定,但优选为0.05mm~2.0mm,优选为0.1mm~0.3mm。在要将本实施方式的基材11用于燃料电池用隔板的用途的情况下,优选使用这样的基材:事先在该基材11的表面形成有发挥燃料气体、空气的流路的功能的凹凸(气体流路)。作为形成气体流路的方法,不受特殊限定,能够举出例如通过冲压加工来形成气体流路的方法。在要将本实施方式的基材11用于燃料电池用集电板的用途的情况下,能够举出通过冲压加工将基材11的平板形成为规定形状的方法。金属镀层12金属镀层12是形成在基材11的表面的那一层,如图4所示,在要在该金属镀层12上形成金镀层13的情况下,金属镀层12是作为用于良好地形成金镀层13的基底层发挥作用的那一层。或是,在不形成金镀层13的情况下,金属镀层12则变成构成燃料电池用通电构件的最外层的那一层。另外,金属镀层12既可以仅做成一层,也可以做成两层以上,而且,在做成两层以上的情况下,构成各层的成分既可以是不同的,或也可以是相同的。作为构成金属镀层12的成分,能够列举出例如从ni、fe、co、cu、zn、sn、pd、re、pt、rh、ag和ru中选择出来的至少一个元素、以及由上述这些元素和p或b构成的化合物等。就上述这些能构成金属镀层12的元素而言,既可以单独只含其中一种元素,或是,也可以将其中的两种以上的元素组合起来,例如组成为ni-pd-p、ni-p、pd-p、ni-sn等合金,特别优选为pd-p、ni-pd-p合金。从能够使后述的保护膜形成剂容易附着,能够良好地形成保护膜这样的观点出发,作为金属镀层12,优选含ni、pd和p的ni-pd-p合金。另外,在要利用ni-pd-p合金形成金属镀层12的情况下,优选的是,ni与pd的摩尔比(ni/pd)为0.005~0.5。通过使构成金属镀层12的pd和ni的摩尔比在上述范围,能够在基材11上良好地形成金属镀层12,而且,在要在金属镀层12上形成金镀层13的情况下,能够良好地形成金镀层13。作为形成含有ni-pd-p合金的金属镀层12的方法,能够列举出下述方法:使用通过将通常所使用的镀镍浴和镀钯浴混合起来得到的镀浴等,在基材11上实施镀敷。作为镀镍浴,能够列举出例如含有氯化镍、硫酸镍、硝酸镍、醋酸镍等镍盐、次磷酸盐等含磷的还原剂和柠檬酸等络合剂在内的镀浴等。作为镀钯浴,能够列举出例如含有氯化钯等钯盐、次磷酸盐、亚磷酸盐等含磷的还原剂和硫代二乙酸等络合剂在内的镀浴等。另外,在将镀镍浴和镀钯浴混合起来制作基底合金化学镀浴的情况下,优选将硫酸镍用作镍盐,将氯化钯用作钯盐。镀镍浴和镀钯浴的混合比率只要与构成金属镀层12的ni-pd-p合金的各元素的比率相应地适当地进行设定即可。另外,上述内容中,例示了利用ni-pd-p合金形成金属镀层12的情况,但是,在利用其他元素构成金属镀层12的情况下,也同样地使用通过适当地对含构成金属镀层12的各元素且添加有还原剂和络合剂的镀浴进行调整而成的镀浴即可。另外,优选的是,使用上述镀浴,在ph为4.0~7.0、浴温为30℃~50℃、浸泡时间为5分钟~20分钟的条件下形成金属镀层12。而且,金属镀层12的厚度优选为0.001μm~1.0μm,更优选为0.01μm~0.2μm。通过使金属镀层12的厚度在上述范围,在向金属镀层12上形成金镀层13时,能够良好地形成金镀层13。而且,在本实施方式中,由于会进行后述的使用保护膜形成剂进行的保护膜形成处理和后述的酸处理,因此,即使在像上述那样将金属镀层12做得较薄的情况下,也能够适当地抑制构成基材11的成分从金属镀层12的因做得较薄导致产生的针孔部分溶出。即,能够实现金属镀层12的薄膜化,并且能够适当地防止从成为底层的基材11的溶出。在此,在像上述那样地预先通过冲压加工等方式在要形成上述这样的金属镀层12的基材11上形成有气体流路的情况下,对所获得的燃料电池用隔板而言,能够有效防止金属镀层12的裂缝。即,通过使用预先形成有气体流路的基材11,无需在形成金属镀层12之后进行用于形成气体流路的冲压加工等,从而能够防止因冲压加工等的压力导致金属镀层12产生裂缝。而且,在本实施方式中,在向基材11上形成金属镀层12时,可以直接形成在基材11上,但是,为了提高基材11与金属镀层12的密合性,也可以设置改质层。作为改质层,能够与基材11、金属镀层12的特性相应地适当地形成,但是,从提高改制层与金属镀层12的密合性这样的观点出发,优选做成含有与构成金属镀层12的元素相同的元素的层。例如,在利用ni-pd-p合金形成金属镀层12的情况下,作为改质层,优选做成ni系的层,在通过化学还原镀形成上述这样的ni系的层的情况下,能够列举出ni-p镀层等。另外,作为改质层,既可以仅做成一层,也可以做成两层以上,而且,在做成两层以上的情况下,构成各层的成分既可以是不同的,或也可以是相同的。而且,形成改质层的方法不受特殊限定,能够通过电解镀、化学镀、溅射等方法来形成改质层。金镀层13金镀层13是根据需要形成在金属镀层12上的那一层,能够通过在金属镀层12上实施镀敷处理来形成金镀层13。另外,作为镀敷处理,优选化学镀,能够列举出化学置换镀敷处理、化学还原镀敷处理等。而且,在形成金镀层13时,例如可以是,先实施化学置换镀敷处理,再实施化学还原镀敷处理。在本实施方式中,通过化学镀形成金镀层13,由此,即使在使用像上述那样预先形成有气体流路的基材的情况下,对于构成气体流路的凹凸部,也能够以均匀状态形成金镀层13。金镀层13的厚度优选为1nm~200nm,更优选为2nm~100nm。通过使金镀层13的厚度在上述范围,能够在金属镀层12上形成均匀的金镀层13,从而能够提高所获得的燃料电池用通电构件的耐腐蚀性、导电性。而且,在本实施方式中,由于会进行后述的使用保护膜形成剂进行的保护膜形成处理和后述的酸处理,因此,即使在像上述那样将金镀层13做得较薄的情况下,也能够适当地抑制构成基材11和金属镀层12的成分从金镀层13的因做得较薄导致产生的针孔部分溶出。即,能够实现金镀层13的薄膜化,并且能够适当地防止从成为底层的基材11和金属镀层12的溶出。本实施方式的表面处理基材10如上述那样构成。在本实施方式中,通过对上述这样的表面处理基材10依次先进行使用保护膜形成剂进行的保护膜形成处理,再进行酸处理,能够获得燃料电池用通电构件。下面,参照图5,说明使用保护膜形成剂进行的处理和酸处理。另外,图5是图4中用附图标记v表示的部分的主要部分放大图。在此,如图5所示,有时,在图4所示的表面处理基材10的金镀层13、金属镀层12产生针孔等,在该情况下,会导致存在金属镀层12、基材11暴露出来的暴露部。而且,当存在上述这样的暴露部时,有时,构成金属镀层12、基材11的成分会在高温酸性气氛下等时溶出,在用作燃料电池用通电构件的情况下,会导致燃料电池的性能降低。相对于此,在本实施方式中,为了解决上述这样的问题,对图4所示的表面处理基材10依次先进行使用保护膜形成剂进行的保护膜形成处理,再进行酸处理。使用保护膜形成剂进行的保护膜形成处理如图6所示,首先,利用保护膜形成剂对表面处理基材10进行处理,从而在表面处理基材10中的金属镀层12暴露出来的部分的至少一部分形成保护膜14。即,如图6所示的主要部分放大图那样,通过利用保护膜形成剂进行处理,能够使保护膜形成剂附着在金属镀层12中的因金镀层13的针孔等导致金属镀层12暴露出来的部分,由此,能够形成保护膜14。在该情况下,优选在金属镀层12的暴露部分的实质整个部分形成有保护膜14,但也可以存在未形成有保护膜14的部分。或是,对本实施方式的表面处理基材10而言,在没有像上述那样地形成金镀层13的情况下,在金属镀层12的表面形成保护膜14。在该情况下,优选在金属镀层12的表面的实质整个部分形成有保护膜14,但也可以存在未形成有保护膜14的部分。在本实施方式中,在金属镀层12暴露出来的部分形成保护膜14之后,进行后述的酸处理,从而能够在基材11的暴露部形成钝化膜,在该情况下,保护膜14能够作为防止金属镀层12被酸处理影响的、金属镀层12的保护膜发挥作用。除此之外,通过形成上述这样的保护膜14,在将表面处理基材10用作燃料电池单元2的燃料电池用通电构件的情况下,就金属镀层12自身而言即使被曝于高温酸性气氛下,也能够有效抑制金属镀层12的溶出。另外,作为利用保护膜形成剂对表面处理基材10进行处理的方法,能够列举出下述方法等:将表面处理基材10浸泡在保护膜形成剂中,或向表面处理基材10喷射保护膜形成剂。作为保护膜形成剂,只要是能够附着于金属镀层12,能够抑制金属镀层12的溶出的物质即可,但优选不容易附着于基材11和金镀层13而容易附着于金属镀层12的物质。例如,在金属镀层12含ni的情况下,作为保护膜形成剂,优选容易附着于ni的物质,特别是,在金属镀层12由ni-pd-p合金形成的情况下,优选容易附着于ni-pd-p合金的物质。具体地讲,作为保护膜形成剂,优选使用这样的物质:该物质含由唑系化合物和具有硫醇基的化合物构成的混合物,或是含具有硫醇基的唑系化合物,或是含将上述这些物质组合起来得到的物质。作为具有硫醇基的化合物,不受特殊限定,能够列举出:三嗪硫醇系化合物、碳原子数为10以上且为20以下的直链烷烃硫醇、吡啶硫醇化合物、苯硫酚系化合物等。就上述这些具有硫醇基的化合物而言,能够单独使用其中一种化合物,或能够将上述化合物中的两种以上的化合物组合起来使用。作为唑系化合物,不受特殊限定,能够列举出:三唑系化合物、苯并三唑系化合物、咪唑系化合物、噻唑系化合物、吡咯化合物等。特别优选苯并三唑系化合物。就上述这些唑系化合物而言,能够单独使用其中一种化合物,或能够将上述化合物中的两种以上的化合物组合起来使用。作为具有硫醇基的唑系化合物,不受特殊限定,能够列举出:巯基三唑系化合物、巯基噻唑系化合物、巯基苯并噻唑系化合物等。就上述这些具有硫醇基的唑系化合物而言,能够单独使用其中一种化合物,或能够将上述化合物中的两种以上的化合物组合起来使用。而且,也可以是,保护膜形成剂中还含有非离子表面活性剂等表面活性剂、油等。在使用上述这些物质的情况下,这些物质的种类、使用量均不受特殊限定。而且,作为保护膜形成剂,可参考日本特开平9-170096、日本特开2012-172190所述的物质等。在本实施方式中,通过使用上述保护膜形成剂,与基材11、金镀层13相比,保护膜形成剂有选择性地容易附着于金属镀层12,能够在金属镀层12上良好地形成保护膜14。特别是,在金属镀层12含ni、ni-pd-p合金的情况下,上述保护膜形成剂所含的唑系化合物(含氮五元环化合物)的氮原子较容易附着于金属镀层12的ni等,因此,能够在金属镀层12上更良好地形成保护膜14。由此,能够抑制后述那样的酸处理的处理性降低的情况以及因保护膜14形成在金镀层13上导致表面处理基材10的表面的导电性降低的情况发生。另外,在本实施方式中,作为保护膜形成剂,优选使用这样的物质:该物质不容易附着于金镀层13,由此,不容易在金镀层13的表面形成保护膜14,但是,只要是不会导致表面处理基材10的导电性显著降低的程度的物质,就也可以在金镀层13上形成保护膜14。或是,在保护膜14的导电性较优异的情况下,也可以在金镀层13的整个面形成保护膜14。而且,作为保护膜形成剂,优选使用这样的物质:在成为保护膜14之后,即使被加热至300℃左右也不会被分解。由此,在将形成有保护膜14的燃料电池用通电构件用作燃料电池单元2或燃料电池堆3的构件的情况下,能够提高燃料电池用通电构件的耐热性。酸处理接着,对形成有上述保护膜14的表面处理基材10进行酸处理。在本实施方式中,如图7所示,通过进行酸处理,能够在图6所示的表面处理基材10中的基材11暴露出来的部分的至少一部分形成钝化膜111。即,如图7所示的主要部分放大图那样,在基材11上存在因金属镀层12的针孔等导致基材11暴露出来的部分的情况下,通过酸处理,能够将该暴露出来的部分钝化,形成钝化膜111。在该情况下,优选在基材11的暴露部分的实质整个部分形成有钝化膜111,但也可以存在未形成有钝化膜111的部分。在本实施方式中,通过在基材11暴露出来的部分形成钝化膜111,在将表面处理基材10用作燃料电池单元2、燃料电池堆3的燃料电池用通电构件(隔板)1、燃料电池用通电构件(集电板)31的情况下,即使被曝于高温酸性气氛下,也能够有效抑制基材11的溶出。特别是,在本实施方式中,如上所述,在金属镀层12上形成保护膜14,在金属镀层12被保护膜14保护起来的状态下进行酸处理,因此,能够抑制金属镀层12被酸溶解,并且能够在基材11形成钝化膜111。而且,在本实施方式中,表面处理基材10的金镀层13针对酸的耐腐蚀性本就优异,因此,也不会发生因酸处理导致金镀层13被腐蚀的情况。酸处理的方法不受特殊限定,能够举出使经过保护膜形成处理之后的表面处理基材10(参照图6)浸泡在酸中的方法。进行酸处理时的ph优选为4以下。作为酸处理使用的酸,不受特殊限定,但是,从能够良好地形成钝化膜111这样的观点出发,优选使用硫酸、硝酸,具体地讲,优选使用硫酸水溶液、硝酸水溶液。在酸处理使用硫酸水溶液的情况下,酸处理的条件优选为:硫酸水溶液中的硫酸的浓度为0.01重量%~10重量%,温度为30℃~90℃,浸泡时间为10秒~48小时,更优选的是,浸泡时间为10秒~24小时。在酸处理使用硝酸水溶液的情况下,硝酸水溶液中的酸处理的条件优选为:硝酸的浓度为0.01重量%~5重量%,温度为30℃~90℃,浸泡时间为10秒~60分钟。在本实施方式中,在基材11上形成金属镀层12,再根据需要来形成金镀层13,从而做成表面处理基材10,对该表面处理基材10像上述那样进行使用保护膜形成剂进行的处理和酸处理。由此,能够获得能够应用于燃料电池单元2或燃料电池堆3的构件等的燃料电池用通电构件。就本实施方式的燃料电池用通电构件而言,即使金属镀层12、金镀层13产生了针孔,但在针孔的部分形成有钝化膜111和保护膜14。因此,在将本实施方式的燃料电池用通电构件用作燃料电池单元2或燃料电池堆3的构件的情况下,能够有效抑制形成基材11和金属镀层12的成分的溶出,耐腐蚀性较优异。即,就以往的燃料电池用通电构件而言,当像图5所示的那样,在表面处理基材的金属镀层12、金镀层13产生了针孔时,在被用作燃料电池单元2或燃料电池堆3的构件的情况下,当被曝于高温酸性气氛下时,会导致基材11和金属镀层12溶出。例如,在基材11为不锈钢的情况下,fe、cr等会从基材11溶出。而且,在金属镀层12由ni-pd-p合金等形成的情况下,ni、pd等会从金属镀层12溶出。相对于此,就本实施方式的表面处理基材10而言,如图7所示,在基材11中的基材11暴露出来的部分形成有钝化膜111,在金属镀层12中的金属镀层12暴露出来的部分形成有保护膜14,因此,能够抑制基材11和金属镀层12的溶出。特别是,在本实施方式中,作为用于形成保护膜14的保护膜形成剂,如上述那样使用不容易附着于基材11和金镀层13而容易附着于金属镀层12的物质,从而能够有选择性地在金属镀层12形成保护膜14。由此,在形成保护膜14之后进行酸处理时,能够在基材11良好地形成钝化膜111,能够使所获得的燃料电池用通电构件在高温酸性气氛下的耐腐蚀性显著优异。即,根据本发明人等的见解,能够发现:在基材11是不锈钢等的情况下,通过酸处理等对基材11的暴露部形成钝化膜111的做法,在提高被长时间曝于高温酸性气氛下时的耐腐蚀性的方面较为有效。但是,另一方面,当在使用保护膜形成剂进行的保护膜形成处理中,在表面处理基材10的基材11形成了保护膜14时,即使之后进行酸处理,也难以在基材11中的形成有保护膜14的部分形成钝化膜111。因此,在本实施方式中,设法不对基材11形成保护膜14,而是有选择性地在金属镀层12形成保护膜14,之后,在基材11形成钝化膜111,从而能够进一步提高所获得的燃料电池用通电构件的耐腐蚀性。除此之外,在本实施方式中,设法有选择性地对金属镀层12形成保护膜14,而没有在金镀层13形成保护膜14,从而能够抑制因保护膜14形成在金镀层13上导致表面处理基材10的表面的导电性降低。另外,上述的图7所示的例子表示的是在表面处理基材10形成有金镀层13的例子,但是,在本实施方式中,也可以不在表面处理基材10形成金镀层13。在该情况下,如图8所示的燃料电池用通电构件那样,在基材11上形成金属镀层12,再进行上述的使用保护膜形成剂进行的处理,从而在金属镀层12的表面形成保护膜14,之后,进行上述酸处理,从而在基材11形成钝化膜111。在该情况下,由于要在金属镀层12的表面形成保护膜14,因此,作为保护膜形成剂,优选使用能够获得导电性优异的保护膜14的物质。在像图8所示的那样,在基材11上仅形成金属镀层12的情况下,作为金属镀层12,优选的是,做成例如像图9所示的燃料电池用通电构件那样依次形成有ni镀层12a和ni-sn合金层12b的双层构造。通过将金属镀层12做成上述这样的构造,能够使具有上述这样的构造的燃料电池用通电构件的耐腐蚀性和导电性优异。实施例下面,列举实施例来更具体地说明本发明,但本发明不被这些实施例所限定。实施例1首先,准备不锈钢材(sus316l)作为基材11。接着,使用镀浴对准备好的基材11在38℃的条件下实施4分钟的化学镀处理,从而在基材11上形成了厚度为40nm的ni-pd-p合金层作为金属镀层12,其中,该镀浴是通过将下述内容所示的镀钯浴和镀镍浴按照镀钯浴:镀镍浴=5.7:1(体积比)的比率混合起来做成的。另外,镀浴中的钯盐、还原剂和络合剂使用了现有的公知的化合物。而且,通过将镀钯浴和镀镍浴混合起来做成的镀浴中的ni:pd(摩尔比)为1.14:1.0。镀钯浴钯盐:能满足镀钯浴中的pd量为0.15重量%的量还原剂:1.8重量%络合剂:0.63重量%水:87.2重量%ph:1.8镀镍浴镍盐(硫酸镍):1.8重量%还原剂(次磷酸钠):2.4重量%络合剂:2.4重量%水:93.2重量%ph:5.2接着,使用化学置换镀金浴(奥野制药工业社制,フラッシュゴールドnc),对形成有ni-pd-p合金层的基材11在70℃的条件下实施两分钟的化学置换镀敷处理,之后,使用化学还原镀金浴(奥野制药工业社制,セルフゴールドotk),在60℃的条件下实施两分钟的化学还原镀敷处理,从而在ni-pd-p合金层上形成了厚度为20nm的金镀层13,获得了表面处理基材10。接着,使所得的表面处理基材10在50℃的条件下浸泡在已用水稀释成浓度为10%的保护膜形成剂中1分钟,从而在表面处理基材10上形成了保护膜14,之后,进行水洗。接着,使形成有保护膜14的表面处理基材10在90℃的条件下浸泡在浓度为0.049重量%(ph2)的硫酸水溶液中24小时,进行酸处理,从而在表面处理基材10的基材11形成了钝化膜111(不锈钢所含的cr与氧结合所形成的覆膜),之后,进行水洗。评价耐腐蚀性接着,对表面处理基材10的耐腐蚀性进行评价。通过如下方式评价耐腐蚀性,即:具体地讲,利用聚酰亚胺胶带对表面处理基材10的端面进行遮挡,使基材的正面和背面均暴露出纵向为35mm、横向为30mm的面积,将该基材浸泡在90℃的硫酸水溶液(体积为80ml,ph:2)中100小时,之后,将表面处理基材10取出,利用icp(岛津制作所制,icpe-9000)测量从表面处理基材10溶出到硫酸水溶液中的离子(ni、pd、p)的浓度。图10和表1表示结果。测量电阻接着,使用实施例1中获得的表面处理基材10,形成图11所示那样的测量系统,并按照下述条件测量表面处理基材10的电阻。另外,图11所示的测量系统由表面处理基材10的试验品、被金镀层包覆起来的铜电极20和电阻表30构成。测量电阻时,具体地讲,首先,将表面处理基材10加工成宽度20mm、长度20mm、厚度0.1mm的大小,获得试验品,像图11所示的那样,利用被金镀层包覆起来的铜电极20从两侧将该试验品夹起来并进行固定,从而做成图11所示的测量系统。接着,一边对铜电极20施加1mpa的负荷,一边使用电阻表(日置电机制,ミリオームハイテスタ3540)测量夹着试验品的、被金镀层包覆起来的铜电极20之间的电阻值。电阻值表示试验品自身的导电性。表2表示所得的测量结果。参考例1准备上述实施例1中使用的不锈钢材(sus316l),不对该不锈钢材形成金属镀层12和金镀层13,而直接对该不锈钢材进行上述的评价耐腐蚀性和测量电阻。另外,评价耐腐蚀性时,利用聚酰亚胺胶带对sus316l进行遮挡,使其暴露出纵向为50mm、横向为60mm的面积,然后进行评价。而且,测量电阻时,将sus316l加工成宽度20mm、长度20mm、厚度0.1mm的大小之后再进行测量。图10、表1和表2表示结果。比较例1除了没进行使用保护膜形成剂进行的处理也没进行酸处理以外,与实施例1同样地制成表面处理基材10,并同样地进行耐腐蚀性的评价。表1表示结果。比较例2除了没进行酸处理以外,与实施例1同样地制成表面处理基材10,并同样地进行耐腐蚀性的评价。表1表示结果。表1表2根据图10和表1中的结果可知,实施例1中,在基材11上形成金属镀层12和金镀层13,做成表面处理基材10,对该表面处理基材10进行使用保护膜形成剂进行的处理和酸处理,对实施例1评价耐腐蚀性的结果是,各元素的溶出量较少,耐腐蚀性优异。而且,根据表2中的结果可知,实施例1中,即使在对表面处理基材10形成金镀层13之后再进行使用保护膜形成剂进行的处理的情况下,电阻值也仍然较小,导电性优异。另一方面,根据图10和表1中的结果可知:与实施例1相比,在没形成金属镀层12和金镀层13的参考例1(sus316l)、没进行使用保护膜形成剂进行的处理和酸处理的比较例1、没进行酸处理的比较例2中,各元素的溶出量较多,耐腐蚀性较差。而且,根据表2中的结果可知:参考例1(sus316l)中,电阻值较高,导电性较差。参考例2准备上述实施例1中使用的不锈钢材(sus316l),使该不锈钢材在90℃的条件下浸泡在0.049重量%(ph2)的硫酸水溶液中24小时,来进行酸处理,从而在不锈钢材的表面形成了钝化膜111,之后,进行水洗。xps测量使用x射线光电子能谱装置(ulvac-phi,inc制,型号:versaprobeⅱ),分别对在不锈钢板的表面形成的钝化膜111的表面中的fe2p和cr2p的峰进行测量。然后,根据所得的峰的面积求出各峰的强度。表3表示结果。另外,表3中,是按照fe2p的峰的强度和cr2p的峰的强度之和为100来求出各峰的强度的。aes测量使用扫描式俄歇电子能谱分析装置(日本电子制,型号:jamp-9500f),对在不锈钢板形成的钝化膜111的表面中的fe和cr的原子%进行测量,基于所得的测量结果,求出cr/fe值(cr的原子%/fe的原子%)。表4表示结果。参考例3准备与上述参考例2相同的不锈钢材(sus316l),不对该不锈钢材进行酸处理,而直接对该不锈钢材进行上述的xps测量和aes测量。表3和表4表示结果。表3层结构酸处理条件fe(2p3/2)cr(2p3/2)参考例2sus316l浸泡在硫酸水溶液(ph2、90℃)中24小时22.377.7参考例3sus316l不进行处理91.68.4表4层结构酸处理条件cr/fe参考例2sus316l浸泡在硫酸水溶液(ph2、90℃)中24小时2.1559参考例3sus316l不进行处理1.4291根据表3和表4中的结果,能够确认的是,在对不锈钢材(sus316l)实施了酸处理的参考例2中,表面中的cr的比率较高,在不锈钢材的表面良好地形成了钝化膜111(不锈钢所含的cr与氧结合所形成的覆膜)。由此,可以认为,在上述实施例1中,即使在金属镀层12产生了针孔等导致金属镀层12的一部分暴露出来,也能够在该暴露出来的部分适当地形成钝化膜111。另一方面,根据表3和表4中的结果,能够确认的是,在没对不锈钢材(sus316l)实施酸处理的参考例3中,表面中的cr的比率较低,在不锈钢材的表面几乎没形成钝化膜111。实施例2除了使用ph为1以下且浓度为1重量%的硫酸水溶液在70℃的条件下浸泡两分钟来进行酸处理以外,与上述实施例1同样地制成表面处理基材10。然后,用肉眼确认所制成的表面处理基材10中的金镀层13是否发生了剥离。表5表示结果。实施例3除了使用ph为1以下且浓度为1重量%的硝酸水溶液在70℃的条件下浸泡两分钟来进行酸处理以外,与上述实施例2同样地制成表面处理基材10,并同样地进行评价。表5表示结果。比较例3除了没进行使用保护膜形成剂进行的处理以外,与上述实施例2同样地制成表面处理基材10,并同样地进行评价。表5表示结果。比较例4除了没进行使用保护膜形成剂进行的处理以外,与上述实施例3同样地制成表面处理基材10,并同样地进行评价。表5表示结果。表5根据表5中的结果,能够确认的是,在进行了使用保护膜形成剂进行的处理之后进行了酸处理的实施例2和实施例3中,即使经过了酸处理,金镀层13也没发生剥离。即,能够确认的是,实施例2和实施例3中,通过进行使用保护膜形成剂进行的处理,能够在金属镀层12适当地形成保护膜14,从而即使经过酸处理,也能够抑制金属镀层12的溶出,由此,能够防止金镀层13的剥离。另一方面,根据表5中的结果,能够确认的是,在没进行使用保护膜形成剂进行的处理而进行了酸处理的比较例3和比较例4中,经过酸处理之后,金镀层13发生了剥离。即,能够确认的是,比较例3和比较例4中,由于没进行使用保护膜形成剂进行的处理,因此,在金属镀层12上没形成保护膜14,由此,经过酸处理之后,导致金属镀层12发生溶出,在金属镀层12上形成的金镀层13发生了剥离。附图标记说明1、燃料电池用通电构件(隔板);2、燃料电池单元;21、电解质膜;22、阳极;23、阴极;1a、燃料气体流路;3c、氧化气体流路;3、燃料电池堆;31、燃料电池用通电构件(集电板);10、表面处理基材;11、基材;111、钝化膜;12、金属镀层;13、金镀层;14、保护膜。当前第1页12