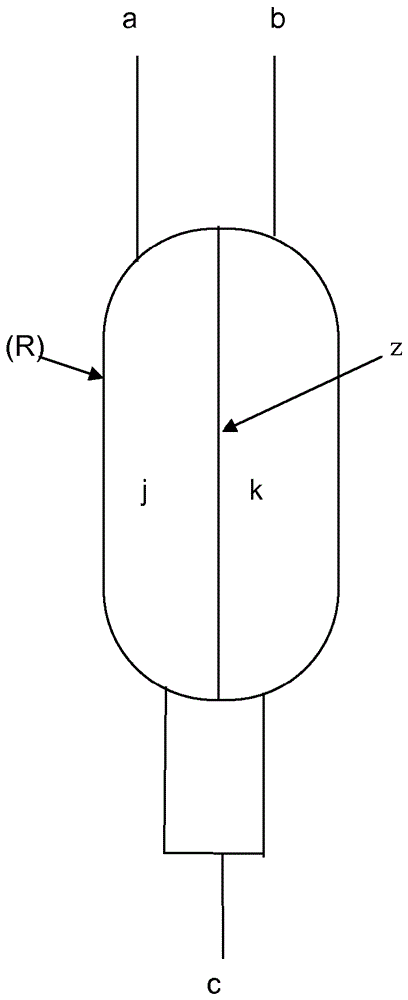
由甘油制造丙烯醛和/或丙烯酸的方法本发明的工作接受了基于第228867号补贴协议的来自欧洲共同体第七框架计划FP7/2007-2013的财政支持。技术领域本发明涉及由甘油制造丙烯醛和/或丙烯酸,更特别涉及通过甘油脱水连续制造包含丙烯醛的料流的方法,包括反应与再生脱水催化剂的循环。本发明还涉及在不具有高资本成本并具有良好的安全条件的情况下在能量消耗与生产率方面能有效制造丙烯醛连续流的设备。
背景技术:用于化工行业的化石来源的资源,如石油馏分将在现在起几十年内耗尽。这就是为何多年来工业企业已经将它们的研究和开发活动转向使用可再生天然原材料的所谓“生物来源”合成方法。丙烯醛,一种用于化工行业的重要合成中间体,在工业上通过在基于混合氧化物的催化体系存在下由空气中的氧气气相氧化丙烯来制得。其制造由此依赖于化石来源的原材料。丙烯醛是合成甲巯基丙醛和蛋氨酸(一种用作动物饲料添加剂的合成蛋白质,其已经广泛用作鱼粉的代用品)的关键中间体。丙烯醛还用于制造丙烯腈、戊二醛或吡啶。丙烯醛尤其是丙烯酸的非分离合成中间体,丙烯酸是非常重要的原材料,其可以直接用于获得丙烯酸的聚合物,或者在用醇酯化后用于制造相应的酯的聚合物。这些聚合物可以以其原样使用,或在各种领域中作为共聚物使用,所述领域如卫生用品(例如用于制造超强吸收剂)、清洁剂、涂料、清漆、粘合剂、纸张、织物、皮革等。在生物柴油燃料制造中获自植物或动物油的甘油是设想作为丙烯代用品的用于制造丙烯醛的原材料之一,甘油承受催化脱水反应,获得丙烯醛。此类方法由此能够解决替代丙烯的问题,并在保护环境的更大背景下响应绿色化学的概念。甘油脱水成为丙烯醛的反应已经是许多研究的主题,特别是在寻找确保甘油完全转化以及适于工业规模生产的对丙烯醛的产率与选择性的催化体系方面。我们可以提及例如文献US5,387,720和WO2006/087084,该文献描述了在由其哈米特酸度表征的固体酸催化剂的存在下合成丙烯醛的方法;此类催化剂尤其可以选自天然或合成的硅质材料、酸性沸石、用无机酸浸渍的氧化物、单酸、二酸、三酸或多元酸、氧化物或混合氧化物或杂多酸。已经提出了具有甘油脱水活性的其它催化体系,例如基于掺杂的磷酸铁的固体,部分成盐的杂多酸,负载在多孔氧化钛上的杂多酸,或磷和钒的混合氧化物(WO2009/044081;WO2009/128555;WO2011/033689;WO2010/046227)。但是,甘油催化脱水为丙烯醛的反应总是伴随着副反应,导致生成副产物如羟基丙酮、丙醛、乙醛和丙酮,并且还生成了高沸点化合物如苯酚、聚芳族化合物或来自于甘油缩聚的化合物。副产物的存在需要分离/提纯步骤以回收提纯的丙烯醛,或含有丙烯醛的料流,所述丙烯酸可以随后施以氧化步骤以制造丙烯酸。高沸点化合物部分是在催化剂上生成焦炭的原因。这导致催化剂失活,并随后导致甘油转化率方面和丙烯醛选择性方面的降低。该催化剂因此必须周期性更换以保持令人满意的经济效率。催化剂寿命取决于系统的运行条件,并可以为几小时至几天。周期性再生催化剂至少部分补偿了失活,再次提供令人满意的催化活性,但是极大地降低了设备生产率。由此许多研究涉及改善生产率,尤其是通过组合各种运行条件。因此,在本申请人名下的文献WO2006/087083中,提出了在甘油脱水为丙烯醛的反应过程中使用分子氧以减少在催化剂上生成焦炭。在所述制造丙烯醛的方法中,可以离位进行催化剂再生,例如对于流化床可以通过以下进行:连续抽取废催化剂并在空气中燃烧,随后在不停止生产的情况下重新装载新鲜催化剂。在这种情况下,在不一定与那些反应相同的温度和压力下进行再生。考虑到在反应器中存在少量分子氧,催化剂再生还可以与该反应同时地原位连续进行。在这种情况下,再生在该反应的温度和压力下进行,并且更类似于部分抑制失活:事实上,在数十小时至数日后,氧含量不足以保证该催化剂的足够的活性。在文献DE102008038273中描述的用于由甘油制造丙烯酸的两步骤方法中,在分为至少两部分的催化剂的存在下进行甘油的脱水,一部分催化剂为反应模式,另一部分为再生模式。该反应在200℃至400℃的温度下进行,而催化剂再生在300℃至600℃的温度下使用含氧气体(特别是包含小于10体积%氧气的气体混合物)在氧化性条件下进行,或在含氢气体存在下在还原性条件下进行。两个催化剂床(固定床或流化床)在平行的两个反应器中以反应模式和以再生模式交替运行。在文献WO2008/052993中描述的制造丙烯醛的方法中,通过使用在200℃至650℃的温度下运行的循环床反应器来解决脱水催化剂的再生问题;该催化剂,在与反应料流分离后,在400℃至700℃的温度下在含氧气体的存在下连续再生,焦炭燃烧提供用于该反应、特别是用于气化该反应器进料流的热量。文献US2008/0214384描述了在包含至少一种选自元素列表的助催化剂的钨基酸催化剂的存在下由甘油制造丙烯醛的方法,该助催化剂的存在降低了催化剂碳化的倾向,并促进其再生。该脱水反应在150℃至450℃的温度下进行。对于在氧或氢的存在下进行再生来说,使用100℃至800℃的高温,这与反应温度并不对应。该方法可以使用反应/再生循环在两个分离的反应器中实施以获得丙烯醛的连续流。在专利申请JP2008-137950中,提出了在由甘油制造丙烯醛的方法中使用含有选自Pt、Pd、Ru、Ir、Cu和Au的金属的脱水催化剂,能够延长催化剂寿命和降低温度和再生时间。在专利申请JP2008-110298中描述的方法中,用于甘油脱水的催化剂的再生在高于煅烧温度的温度下进行以减少再生时间,并将催化活性恢复到与初始催化活性相同级别的水平。基于再生温度、氧化剂浓度和氧化剂流量来控制再生过程中的催化剂温度。在反应中或在再生中运行的多个反应器能够避免中断丙烯醛生产。文献US2011/0152582描述了用于进行脱水反应和用于再生所用的磷基催化剂的特定设备配置。在该设备中,顺序停止反应性料流的进料,以便将再生该催化剂用的氧化性气体或还原性气体进料至该反应器。尽管存在这些不同的进展,仍然需要新的方法以便在工业规模下进一步改善甘油脱水为丙烯酸的反应的生产率并由此改善由甘油制造丙烯酸的生产率。现在,发明人发现,可以通过在精确的运行条件下结合反应循环与再生循环来满足这一需要,这些循环可以集成在用于连续制造含丙烯醛料流的特定反应器配置中。本发明的一个目的因此是提供制造通过甘油脱水获得的包含至少丙烯醛的料流的方法与装置,其可以在能耗和生产率方面有效地用甘油连续进料,并且不具有高资本成本和具有良好的安全性条件。发明概述本发明由此涉及连续制造包含至少丙烯醛的料流的方法,包括下列步骤:-与保持在250℃至350℃温度下的反应器区域中所含固体酸催化剂接触时包含至少甘油的气态反应料流反应以获得包含至少丙烯醛的转化料流的步骤(a),-用包含至少氧的气态料流再生所述固体催化剂的步骤(b),其特征在于:(i)步骤(b)在类似于步骤(a)中的反应温度的再生温度下进行,并且(ii)步骤(b)过程中该催化剂的热点不超过高于再生模式下含有该催化剂的反应器区域温度100℃,和(iii)步骤(a)和步骤(b)同时施加,各自以反应模式和以再生模式以循环形式施加在至少一个反应器区域上,所述反应模式和再生模式由一个区域向另一个区域移动(décalé)。本发明还涉及由甘油制造丙烯酸的方法,包括通过上述方法制造包含至少丙烯醛的料流的第一步骤,和将丙烯醛氧化成丙烯酸的步骤。本发明还涉及用于连续制备至少包含至少丙烯醛的料流的设备。本发明能够克服现有技术的缺点。更特别地,本发明提供了用于制造丙烯醛的紧凑型设备,能够最优地控制导致含有丙烯醛的连续气态料流的运行条件。本发明特别适于导致形成丙烯醛的甘油脱水反应,为此催化剂失活具有幅度大于一小时并小于一个月的特征持续时间(失活时间定义为在其结束时丙烯醛产率相对于最大产率下降15%的反应时间),并且失活时间是再生时间(定义为在其结束时经受失活的催化剂恢复其初始效率——即能够恢复与在先循环相同的最大产率和相同的失活时间——的时间)的0.05倍至20倍。附图概述-图1和2示意性显示了根据具有两个平行的反应器的配置的本发明的实施方案。-图3和4示意性显示了根据具有含两个区的单一反应器的配置的本发明的实施方案,一个区以反应模式运行,另一个区以再生模式运行。-图5示意性显示了根据具有含四个区的单一反应器的配置的本发明的实施方案,四个区交替地处于反应模式和再生模式。-图6和7示意性显示了具有包含2个反应区的多管反应器的实施方案。在阅读下面给出的详细说明后本发明的其它特定特征和优点将变得显而易见。发明详述本发明的制造方法包括一系列连续循环,各循环在包含至少两个含有催化剂的区的反应器中或在至少两个含有催化剂的反应器中连续包含反应步骤(a)和再生步骤(b)。根据本发明的方法的步骤(a),使包含甘油的气态反应料流与能够催化甘油脱水成丙烯醛的反应的酸性固体接触。浓度为20至100重量%的水溶液通常用作甘油的来源。甘油的任何来源都是可能的:该甘油可以例如来自植物或动物油或循环油的水解或皂化或酯交换的工艺。所用甘油可以以通常低于5%的量任选包含有机杂质。除了甘油之外,该气态反应料流可以包含水蒸汽,以及惰性化合物如CO、CO2和/或N2、Ar。其可以如申请WO06/087083与WO06/114506中所述那样进一步含有氧或含氧气体。水/甘油重量比可以例如在0.04/1至9/1和优选在0.3/1至3/1之间宽泛变化。甘油脱水的反应在固体酸催化剂的存在下在1至5巴(100至500kPa)的绝对压力下进行。反应器温度为250℃至350℃、优选为280℃至340℃,特别为290℃至330℃。合适的催化剂是以非均相用于气态或液体反应介质中的材料,其具有小于+2的哈米特酸度(表示为H0)。如专利US5,387,720中指出的那样,其引证了“StudiesinSurfaceScienceandCatalysis”,第51卷,1989,第1和2章中K.Tanabe等人的论文,哈米特酸度通过使用指示剂用氨滴定来测定,或通过碱的气相吸附来测定。这些催化剂可以选自天然或合成的硅质材料或酸性沸石;矿物载体,如氧化物,涂有无机酸,单酸、二酸、三酸或多元酸;氧化物或混合氧化物或杂多酸或杂多酸的盐。还有可能使用前述物类的组合。这些催化剂可以由杂多酸的盐组成,其中所述杂多酸的质子与至少一种阳离子交换,所述阳离子选自属于周期表第I至XVI族的元素,这些杂多酸的盐含有至少一种选自W、Mo和V的元素。在混合氧化物中,特别可以提到基于铁和磷的那些,和基于铈、磷和钨的那些。该催化剂特别选自沸石、氟化聚合物的磺酸-基复合材料(Nafion®)、氯化的氧化铝、磷钨酸或硅钨酸的酸或盐、以及各种金属氧化物类型的固体,如用酸官能(例如硼酸根BO3、硫酸根SO4、钨酸根WO3、磷酸根PO4、硅酸根SiO2或钼酸根MoO3)浸渍的氧化钽Ta2O5、氧化铌Nb2O5、氧化铝Al2O3、二氧化钛TiO2、二氧化锆ZrO2、氧化锡SnO2、二氧化硅SiO2或铝硅酸盐SiO2-Al2O3,或这些化合物的混合物。前述催化剂可以进一步包含助催化剂如Au、Ag、Cu、Pt、Rh、Pd、Ru、Sm、Ce、Yt、Sc、La、Zn、Mg、Fe、Co、Ni或蒙脱石。优选的催化剂是包含钨的酸性固体,如氧化钨或负载在二氧化硅、氧化铝、二氧化锆或氧化钛载体上的钨的杂多酸,如硅钨酸或磷钨酸或其盐。本发明的方法的步骤(b)由借助再生料流再生该脱水催化剂组成,所述再生料流优选含有氧化性物质如氧,以便能够燃烧造成催化剂失活的焦炭。该再生料流可以是纯粹的气态,或者可以包含液体组分,并且优选是纯粹的气态。其包含氧,并且可以任选包含一种或多种惰性传热化合物,如CO、CO2和/或N2。例如,该再生料流是空气。有利地,该气体再生料流可以进一步含有水作为传热流体,其在再生后产生含有水与碳氧化物的气体混合物,该混合物可以再循环到反应中用于稀释甘油的反应料流。当向催化剂上进料甘油停止时,该再生步骤开始。在类似于步骤(a)的反应温度的温度下进行催化剂再生,并且,相互关联地,该反应步骤在类似于在先循环的步骤(b)中的再生温度的温度下进行。特别地,在借助于传热流体恒温控制的反应器或反应器区的情况下,通过控制传热流体的温度来进行反应。根据本发明,在类似于步骤(a)中反应温度的温度下实施再生表明步骤(b)过程中反应器区中传热流体的温度处在类似于步骤(a)中传热流体温度的温度下。为简便起见,在说明书的剩余部分,“催化剂区”指的是含有催化剂的反应器区。“类似的”温度表明等于在±20℃内,优选等于在±10℃内,更特别等于在±5℃内。该方法避免了在每一反应/再生循环中不得不改变反应器或反应器区的热水平。事实上,在每一反应/再生循环中改变热水平在时间和能量方面颇为昂贵,并且将需要适当的设备。令人惊讶地,申请人发现,这些温度足以在下一反应步骤过程中完全恢复催化剂活性。焦炭燃烧是放热反应;结果,在再生步骤过程中存在催化剂温度升高,通常称为热点。催化剂或部分催化剂的温度随之高于含有该催化剂的反应器或反应器区的温度。特别地,在借助传热流体恒温控制反应器的情况下,催化剂或部分催化剂的温度随之高于传热流体的温度。在升高的温度高于450℃或500℃下的催化剂中的热点很可能导致热击穿,也会导致催化剂的过早老化。这也需要具有特别改装的反应器冶金。根据本发明的方法,控制该热点,并将其保持在高于再生模式下含有该催化剂的反应器或反应器区温度最大100℃、优选50℃下。特别地,在包含传热流体的反应器或反应器区的情况下,热点的温度保持在高于该传热流体温度最大100℃、优选50℃、特别是最大20℃下。为此目的,再生料流中的氧含量有利地低于10体积%,优选低于8体积%。或者,采用随再生过程提高的氧含量:在再生的第一部分(其持续总再生时间的5至100%和优选10至40%),氧含量低于10体积%,优选低于8体积%。在再生的第一部分后,当焦炭比例已经被消耗后,如果必要的话将有可能连续或分阶段提高氧浓度,直到达到大约9至22体积%或甚至更高的氧浓度。此外,可以通过使用少部分该管(通常小于15cm2和优选小于5cm2)与传热流体接触的多管反应器或包含热交换器的板型反应器或流化床反应器来促进除去生成的热量。在这种情况下,再生模式下的空速(以标准升数/小时为单位的送入反应器的气体的流速除以以升为单位的催化剂表观体积)可以在50至10000h-1和优选200至2000h-1的宽范围中改变。或者,用高空速(通常高于400h-1,优选高于700h-1,优选高于1500h-1)下的再生料流供应该催化剂区,该再生料流可以由此带走生成的热量。通常,在放热反应如再生中生成的热被回收,例如以水蒸气的形式。本发明的方法能够平顺热量的经时产生,避免在非常轻微的放热效应后具有强放热效应,如在以下情况中那样:在一段时间内过量生产水蒸气,但是在下一阶段生产不足,这在经济上不能令人满意。有利的是具有两个或多个平行的催化剂区,使得步骤(a)和步骤(b)可以同时施加在至少一个催化剂区上。同一催化剂区根据重复多次的反应/再生循环运行,并且该反应/再生的循环由一个区向另一个区移动。对于给定的催化剂区,该循环由通过输送含有甘油的气态反应料流开始步骤(a)组成。丙烯醛产率提高(催化剂活化阶段),随后达到最大,并缓慢降低(与结焦相关的催化剂失活)。当丙烯醛产率相对于最大产率降低一定值时步骤(a)结束,所述值由该工艺的技术条件(以便具有尽可能恒定的流量)和经济条件决定,通常为1至30%。步骤(a)的持续时间取决于使用的催化剂的性质和该催化剂的量,以及反应条件(尤其是使用的氧的量以及温度)。根据本发明,该持续时间为1小时至1个月不等。步骤(b)的持续时间取决于催化剂的性质、空速、温度和氧浓度。调节该持续时间以使得催化剂在下一循环的步骤(a)中保持其效率。根据本发明,该持续时间是步骤(a)的持续时间的0.05倍至20倍不等,并且为3分钟至7天不等。根据本发明的特定实施方案,在步骤(a)的整个持续时间中可以对反应器、或者如果合适的话对提供反应器的恒温控制的传热流体施加在步骤(a)的开始至结束之间为1至30℃的渐增的温度梯度。优选地,在步骤(a)的持续时间的0至50%的恒定初始温度后,在步骤(a)的第二部分中施加连续的升温。还有可能以0.1至10℃的等温差和等持续时间的阶段来提高该温度。以相同的方式,在步骤(b)的整个持续时间中可以对反应器或反应器区、或者如果合适的话对提供反应器或反应器区的恒温控制的传热流体施加在步骤(b)的开始至结束之间为1至30℃的渐增的温度梯度。优选地,在步骤(b)的持续时间的0至50%的恒定初始温度后,在步骤(b)的第二部分中施加连续的升温。还有可能以0.1至10℃的等温差和等持续时间的阶段来提高该温度。在步骤(b)结束时,反应器或反应器区的温度通常将返回至步骤(a)的温度。该反应/再生循环在同一区中施加,只要再生能够恢复催化剂效率。通常,同一催化剂装料可以使用超过4个月,优选超过1年。优选地,催化剂区的数量可以根据步骤(a)的持续时间对步骤(b)的持续时间的比来调节,以便优化所需反应器的尺寸:反应中区的数量对再生中区的数量的比将等于或略低于步骤(a)和(b)的持续时间的比。例如,如果步骤(a)的持续时间等于20小时,步骤(b)的持续时间等于9小时,有可能选择具有3个催化剂区,两个区在反应模式下运行,而一个区在再生模式下运行。或者,有可能具有6个催化剂区,4个区以反应模式运行,2个区以再生模式运行。根据本发明的第一实施方案,步骤(a)和(b)在置于至少两个平行的反应器中的两个或多个催化剂区上进行。在图1和2中显示的具有2个反应器的配置中,各反应器(h)和(i)包含单一催化剂区,其可以是固定床或流化床。在图1中显示的配置中,在该循环的第一部分的过程中,将气态反应料流送入“a”中,并将再生料流送入“b”中。在该循环的第二部分中,将气态反应料流送入“b”中,而将再生料流送入“a”中。在图2中显示的配置中,在该循环的第一部分的过程中,将气态反应料流“a”经由阀(d)送入反应器(h)中,阀(f)关闭。反应器(h)处于反应模式。将再生料流“b”经由开启的阀(g)送入反应器(i),阀(e)关闭。在该循环的第二部分中,阀(d)和(g)关闭,阀(e)和(f)打开。反应器(h)随后处于再生模式,反应器(i)随后处于反应模式。离开两个反应器的所有气态料流合并以形成料流“c”。根据本发明的第二实施方案,在包含至少2个催化剂区的同一反应器中进行步骤(a)和(b),各区分开供应。该配置显示在图3至5中,其中几个催化剂区在空间上位于同一反应器中,所述反应器包含与反应区同样多的分离的进料。该反应器的特征是各催化区中、以及在进料区中和/或在抽提区中气态料流的分离。这种分离例如可以用催化剂区之间和/或进料区中和/或抽提区中的隔板来实现。在图3中显示的配置中,反应器(R)含有由隔板(z)分离的2个催化剂区(j)和(k)。在该循环的第一部分中,将气态反应料流在“a”处送入催化剂区(j)中。将再生料流在“b”处送入区(k)中。区(j)随后处于再生模式,区(k)随后处于反应模式。离开这两个反应器的所有气态料流合并以形成料流“c”。在图4中显示的配置中,反应器(R)含有由隔板(z)分离的2个催化剂区(j)和(k)。在该循环的第一部分中,将气态反应料流“a”通过调节阀(d)和(f)的位置送入催化剂区(j)中。区(j)处于反应模式。将再生料流“b”通过调节阀(g)和(e)的位置送入区(k)中。在该循环的第二部分中,将阀(d)、(e)、(f)和(g)的位置反转:区(j)随后处于再生模式,而区(k)随后处于反应模式。离开这两个反应器的所有气态料流合并以形成料流“c”。在图5中示意性显示的反应器中,可以通过一组阀用气态反应料流“a”或再生料流“b”选择性供应四个催化剂区(t)、(u)、(v)和(w)。从4个催化剂区抽取是公共的,并形成料流“c”。在图3至5中的反应器中,以反应模式运行的催化剂区的数量可以等于以再生模式运行的区的数量。在这种情况下,50%的催化剂处于丙烯醛生产模式。或者,以反应模式运行的催化剂区的数量大于以再生模式运行的区的数量。例如,在图5中示意性显示的包含四个催化剂区的反应器的情况下,有可能以具有时间偏差的反应模式运行三个区,并以再生模式运行一个区,这将再生中的催化剂的比例限制为25%,能够固定在出口处的丙烯醛的平均产量。在图5中的反应器中,在该循环的第一部分中,区(t)、(u)、(v)处于反应中,区(w)处于再生中,通过将阀(p)、(s)、(l)和(o)设定在开启位置和将阀(q)、(r)、(m)和(n)设定在关闭位置,由此用气态反应混合物供应管道“a”而用气态再生混合物供应管道“b”。在该循环的第二部分中,通过将阀(p)和(o)设定在关闭位置并通过开启阀(q)和(n),由此使区(u)、(v)和(w)处于反应中,区(t)处于再生中。随后,在该循环的第三部分中,通过调节适当的阀使区(u)处于再生中,并使其它区处于反应中。在该循环的第四部分中,通过调节适当的阀使区(v)处于再生中,并使其它区处于反应中。随后该循环从起始处再次开始。在这些不同的配置中,获自反应的丙烯醛的气态料流和获自再生的气态料流不必在出口处混合,即各区可以具有单独的气态料流出口。任选地,可以通过在催化剂床后位于反应器中(或仅在反应器出口后在交换器中)的交换器将丙烯醛的气态料流冷却至低于250℃且优选低于230℃以避免丙烯醛的反应。任选地,其有可能通过将离开催化剂区的料流的一部分或全部(穿过风扇和热交换器)再循环至该区入口,由此以再生模式运行,以便通过再生气体除去再生生成的热,所述再生气体以高空速在催化剂上循环。任选地,离开以再生模式运行的区的气态料流可以再循环至以反应模式运行的区的入口,以便稀释甘油的气态反应料流,或可以引导至热氧化器以便去除。或者,一部分离开以再生模式运行的区的料流再循环到以反应模式运行的区的入口,其余部分引导至热氧化器。在这些不同的配置中,离开以再生模式运行的区的气态料流还可以与离开以反应模式运行的区的丙烯醛的气态料流混合。在一种特定配置中,例如如图1至5中所示,所有该气态料流在出口处混合。这提供了无需对来自再生的气态料流进行处理的优点,但是产生了稀释在惰性化合物中(CO、CO2、H2O)的丙烯醛的料流。随后在本发明的方法之后进行的步骤中对丙烯醛料流施以各种处理。本发明的方法可以在固定床或流化床中,优选在固定床中实施。本发明还涉及由甘油制造丙烯酸的方法,包括通过上述方法制造包含至少丙烯醛的料流的第一步骤,和将丙烯酸氧化为丙烯酸的步骤。当然,制造丙烯酸的方法可以包含其它初步、中间或后继步骤,只要它们能够制得一定等级的丙烯酸。因此,尤其可以在制造含有丙烯醛的料流的方法与丙烯醛氧化步骤之间提供中间步骤。该中间步骤可以是例如申请人名下的专利申请WO08/087315中描述的步骤,该步骤能够去除丙烯醛料流中所含的一部分水,以便将该气体调节至大致与前-丙烯法相同的组成,以便供应将丙烯醛氧化成丙烯酸的第二步骤。大致相同的组成尤其是指丙烯酸、水、氧和副产物的类似浓度。该中间步骤在于水的部分冷凝,并能够避免丙烯醛氧化成丙烯酸的第2阶段催化剂的劣化。此外,其能够除去一定比例的与丙烯醛同时形成的“重质”杂质。本发明还涉及用于连续制造包含至少丙烯醛的料流的设备,所述设备包含:-用于将甘油转化为丙烯醛的装置-包含至少甘油的气态反应料流的源-包含至少氧的再生料流的源其特征在于该转化装置包含:-包含至少两个含有催化剂的区的反应器R,各个区交错用作反应区和用作再生区,各区通过进料装置流体连接到反应料流的源“a”和连接到再生料流的源“b”,-适于各进料装置的系统,能够实现反应料流或再生料流的依序交错供应,-至少一个用于抽取气体混合物“c”的装置,该装置流体连接到该反应器,-用传热流体的单一系统恒温控制反应器区。“流体连接”指的是存在通过能够输送物质流的管道系统形成的连接。该连接系统可以包括阀、中间储存装置、支路连接、热交换器、压缩机,但是不包括化学反应器。各个区包含同一甘油脱水催化剂,优选以固定床形式。优选各区含有相同量的催化剂,并具有相同的热交换能力,该区以相同方式恒温控制。由此,优选地,该催化剂区是相同的。根据特定实施方案,该转化装置可以包含用于抽取气体混合物的单一装置,或各反应器区流体连接到用于抽取气体混合物的装置。该装置可以包含下列特征的一种或多种:-该转化装置包含位于各区出口与入口之间的再循环装置,以便能够将离开以再生模式运行的区的料流再循环至以反应模式运行的区的入口,或再循环至以再生模式运行的所述区的入口。-该转化装置包含用于冷却丙烯醛气态料流和/或去除再生所产生的热量的热交换器。根据本发明的一个优选实施方案,在两个催化剂区的特定情况下,该转化装置包含在例如图6和7中示意性显示的包含至少两个催化剂区的多管反应器。该多管反应器(R)包含大量管(10),所述管(10)含有催化剂并通过管板(20)固定。经由开口(15)供应和抽取传热流体,通过与该管(10)垂直布置的板(30)引导其在管(10)之间的循环以便更好地进行热交换。单一传热流体回路提供所有催化剂区的恒温控制。本发明的反应器的特征是分隔催化剂区,这通过安装安置在反应器(R)的圆顶与管板(20)之间的板(40)来提供。通过不同的开口供应气态反应料流“a”和再生料流“b”以及抽取c1和c2。图6中示意性显示的反应器可以以几种方式施用。在第一种使用方式中,经由开口(a)和(b)交替供应气态反应料流“a”和气态再生料流“b”,并且经由开口(c1)和(c2)抽取离开反应区和再生区的气体。在第二种使用方式中,在一部分时间中经由开口(c1)供应该气态反应料流,在剩余时间中经由开口(c2)供应气态反应料流,并在一部分时间中分别经由开口(b)和(a)供应气态再生料流和抽取反应气体,在剩余时间中经由开口(a)和(b)供应气态再生料流和抽取反应气体。图7中示意性显示的反应器仅包含单个分隔板(40)和单个开口(c3)。在第一实施方案中,气态反应料流和气态再生料流经由开口(a)和(b)交替供应,离开反应区的气体和离开再生区的那些气体混合并经由开口(c3)离开。在第二实施方案中,气态反应料流经由开口(c3)供应,经由开口(a)和经由开口(b)交替地供应气态再生料流和排出反应气体。在后一种情况下,离开再生的气态料流与进入到催化剂上并含有甘油的反应气体混合。可以使用具有位于反应器顶部的开口(c3)或如图7中那样具有位于底部的开口的反应器。在包含超过2个反应区的多管反应器的情况下,必须调节分隔板的数量和反应器圆顶中用于供应和抽取的开口的数量。由下面的实施例将更好地理解本发明,该实施例是纯说明性而非限制性的。实验部分实施例1(根据本发明)用根据专利申请WO2011/33689的实施例3制备的0.39升HPW/TiO2催化剂向316升直径为29毫米和高度为1米的不锈钢反应管中装料,所述反应管浸没在装有电阻加热的盐浴(低共熔混合物KNO3、NaNO3、NaNO2)中。正排量泵和2个质量流量调节器能够分别将甘油/水混合物、氮气和空气送入连接到该反应器的电加热蒸发器中。在该反应器下游,通过压力传感器控制的自动阀使得能够在该反应器中保持所需的压力。离开该阀的气态料流可以为分析目的送至塔中,以便用水萃取。可以将由此在该塔底部处经数分钟收集的液体流出物称重并随后通过气相色谱法进行分析。在整个实验中,盐浴保持在290℃下,压力保持在1.7巴(相对)下。在时间点t=0和最高t=24h处,通过将780Nl/h(每小时的标准升数)的体积比为4.7/24.0/69.1/2.2的甘油/水/N2/O2混合物的连续料流在240℃下送至该反应器入口来进行反应阶段。反应器的热点在几分钟后升高至334℃并随后降低,稳定在305-310℃。在t=24h处,开始再生阶段。由时间点t=24h至t=24h15,供应743Nl/h的水/N2/O2混合物(25.2/72.5/2.3)的料流。由t=24h15至t=48h,供应780Nl/h的水/N2/O2混合物(24.0/69.0/7.0)的料流。在此期间,最大热点为316℃。在相同条件下由t=48h至t=96h重复进行反应/再生的第二循环,随后由t=96h至t=144h重复进行反应/再生的第三循环。分析来自用于吸附离开反应器的气态料流的塔的液体流出物能够由下式确定甘油的转化率和丙烯醛的产率:甘油转化率(%)=100–甘油残留摩尔数/引入的甘油的摩尔数。丙烯醛产率(%)=制得的丙烯酸摩尔数/引入的甘油的摩尔数。结果显示在表1中。表1根据本发明,丙烯醛产率在48小时的3个反应/再生循环后仍高于65%。实施例2(对比)在0至24h之间和在24h至24h15小时之间重现实施例1的条件。在t=24h15处,供应780Nl/h的体积比为24.0/66.0/10.0的水/N2/O2混合物的料流。热点非常迅速地超过550℃,并存在热击穿。实施例3重现实施例1的条件,在t=0处将反应器温度设定在290℃,并每小时将该温度提高0.5℃,直到t=24h。丙烯醛产率在t=1h处为69%,在t=5h处为75%和在t=23h处为72%。实施例4使用实施例1的设备,反应管具有22毫米的内径。由t=0至24h重现实施例1的条件,将反应器温度设定在300℃。在t=24h处,开始再生阶段。在2小时内,温度由300℃提高至315℃,随后保持该温度,直到t=46h,并随后在2小时内降低至300℃。由时间点t=24h至t=34h,供应156Nl/h的体积比为25.0/73.0/2.0的水/N2/O2混合物的料流。由t=34h至t=48h,供应270Nl/h的体积比为22.0/63.0/15.0的水/N2/O2混合物的料流。在此期间,最高热点为363℃。该反应/再生循环重复两次以上。在第一反应阶段(t=23h)结束时的丙烯醛产率为70%。在第二反应阶段(t=71h)结束时的丙烯醛产率为70%,在第三阶段(t=119h)结束时其为71%。实施例5使用实施例1的设备,使用来自DaiichiKigenso的含钨的二氧化锆(供应商名称Z1044)作为催化剂(10%的WO3,90%的ZrO2)。由t=0至t=24h重现实施例1的条件,但是将盐浴温度设定在300℃。在t=24h处,开始再生阶段。盐浴的温度在3小时内由300℃提高至320℃,并随后保持该温度直到t=46h,并随后在2小时内降低至300℃。由时间点t=24h至t=34h,供应156Nl/h的体积比为25/72/3的水/N2/O2混合物的料流。由t=34h至t=48h,供应270Nl/h的体积比为22/68/10的水/N2/O2混合物的料流。在此期间,最高热点为353℃。该反应/再生循环在相同条件下重复一次以上。在第一反应阶段(由0至24小时)中丙烯醛的平均产率为69%。在第二反应阶段(由48至72小时)中丙烯醛的平均产率也为69%。