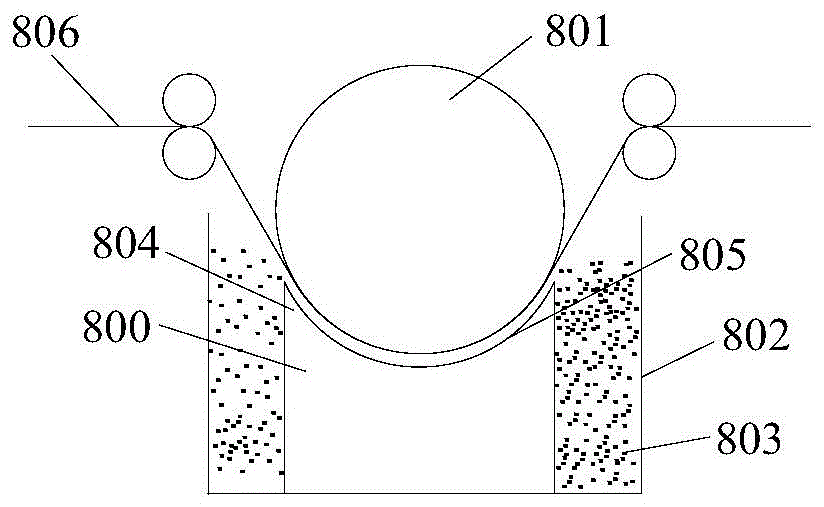
本发明属于制作太阳能薄膜电池设备技术领域,尤其涉及一种制备CIGS吸收层的电镀生产线。
背景技术:CIGS(铜铟镓硒)薄膜太阳能电池具有极佳的光吸收常数,只需1.5微米的超薄吸收层,光电转换效率稳定,光谱响应范围宽,能带可调,抗辐射能力强,无光致衰退,具有光致增益,弱光增益,并且还有重量轻,成本低,易安装的优点成为太阳能领域研究的重点。其典型结构为:金属背电极Mo层、CIGS吸收层、缓冲层CdS、窗口层高阻i:ZnO、低阻ZnO:Al、和前部栅电极。CIGS吸收层由Cu,In,Ga,Se四种元素组成,其电池的光电转换效率与四种元素的摩尔比相关,一般要求Cu/(In+Ga)在0.75~1之间,Ga/(In+Ga)在0.3~0.5之间。CIGS吸收层的制备是CIGS(铜铟镓硒)薄膜太阳能电池的核心技术。由于CIGS吸收层是多元化合物,多采用真空沉积的方法制备,真空沉积技术如溅射后硒化或者共蒸发,其设备都极其昂贵,过程复杂,难以大规模化生产。国外有报道采用非真空沉积的方法来制备CIGS吸收层,具体地,采用卷对卷电镀CIGS吸收层,如图1所示,镀液槽802内盛装有装有电镀液803,并设置有浸没于电镀液803中的阳极800和部分浸没于所述电镀液803中的大转轮801,所述大转轮801的直径较大与阳极800上下间隔设置,具有间隙。所述阳极800朝向大转轮801的面为一凹面805,所述凹面805的弧度与所述大转轮801的弧度相匹配,所述凹面805与所述阳极800侧面形成两个尖部804,柔性衬底806经过清洗绕在大转轮801的外周面上并浸没在电镀液803中进行电镀,沉积CIGS吸收层。此方案存在如下缺点:1、阳极800需要加工凹面805,制作工艺复杂,且在电镀时,阳极凹面两侧的尖部804会优先消耗,时间一长凹面805变浅,无法确保电镀沉积的CIGS吸收层的均匀性和镀速稳定性;2、当只需在所述柔性衬底806的一面上沉积CIGS吸收层时,其CIGS元素有可能沉积在衬底806的另一面;3、镀液槽802中电镀液803的流动不畅,不能及时有效的排出电镀时产生的气泡,容易在电镀沉积的CIGS吸收层上产生花斑,严重影响产品质量。另外,美国专利公开号US2007/0227633A1公开的一种水平电镀的方式,由于,采用的水平直线电镀,衬底没有弯绕,生产线过长,占用空间大,另外,采用该方式电镀时,阳极位于衬底下方,同样具有阴极析出的气泡排不出去的问题,而将阳极放置于衬底上面,又存在阴极面电镀液流动不畅的问题,都会对电镀沉积的CIGS吸收层的表面质量产生影响。
技术实现要素:本发明的目的在于提供一种制备CIGS吸收层的电镀生产线,旨在解决现有技术中的电镀生产线采用非真空电镀沉积法制作CIGS吸收层时,其均匀性难以控制的难题。本发明的实施例是这样实现的,一种制备CIGS吸收层的电镀生产线,用于在衬底上沉积铜铟镓硒元素形成CIGS吸收层,包括送料装置,用于连续供应所述衬底,位于所述电镀生产线的首端;至少四个电镀槽,各电镀槽分别盛装有镀铜液、镀镓液、镀铟液和镀硒液,用于将铜、镓、铟、硒元素分别沉积于所述衬底表面;各所述电镀槽均包括有可盛装电镀液的子槽,所述子槽的中间处设有携带所述衬底同步移动且传动路径呈由多线段首尾相接而成的封闭状的传送装置,所述子槽的侧面挂设有浸没于所述电镀液中且呈板状设置、用于沉积CIGS吸收层的阳极,所述阳极分别与所述传送装置上沉浸于电镀液中对称设置的侧面平行相对设置,所述衬底贴附于所述传送装置上沉浸于电镀液内的侧面且与所述阳极平行相对设置;清洗槽,用于清洗所述衬底表面;沿输送所述衬底的方向,设置于任一所述电镀槽的前后处;收料装置,用于收集表面形成CIGS吸收层的衬底,位于所述电镀生产线的末端;传动装置,用于夹持所述衬底并带动所述衬底一同移动,设置于任一所述电镀槽和所述清洗槽的入口处和出口处;以及控制系统,分别与所述送料装置、所述清洗槽、所述电镀槽和所述收料装置电性连接,并控制所述送料装置、所述清洗槽、所述电镀槽和所述收料装置同步动作。进一步地,所述传送装置包括一固定架、安装于所述固定架上部并抵顶所述衬底的至少一组主辊轮和安装于所述固定架下部并与所述主辊轮配合转动的至少一组从辊轮,以及贴设于所述主辊轮和所述从辊轮的外周面上并携带所述衬底一同运动的传输带,所述固定架截面呈矩形状,所述传送带呈矩形设置并贴设于所述主辊轮和所述从辊轮的外周面上并携带所述衬底一同运动。进一步地,所述主辊轮和所述从辊轮的外周面与所述固定架的外侧壁相切。进一步地,所述主辊轮和所述从辊轮的外周面凸出于所述固定架的外侧壁。进一步地,所述传送装置上还设有用于调节所述传输带张紧度的调整装置,所述调整装置与所述主辊轮和所述从辊轮可调节连接。进一步地,所述传输带上还设有可吸附所述衬底使其与所述传输带贴合的吸附部。进一步地,所述子槽内设置有至少一根用于搅拌电镀液的镀液喷管,各所述镀液喷管上设置有均匀分布的喷孔。进一步地,所述喷孔为锥形孔,所述喷孔的内壁沿所述镀液喷管的管内向管外方向逐渐扩大。进一步地,同一镀液喷管上设置的喷孔间的距离与所述喷孔的直径比在20:1至5:1之间。进一步地,同一所述镀液喷管上设置有两排喷孔,所述两排喷孔的喷射方向呈夹角设置。进一步地,所述喷孔的喷射方向朝向所述电镀子槽的底壁。进一步地,所述镀液喷管至所述子槽底部的距离与所述电镀子槽的电镀液的深度比在1:7至1:20之间。进一步地,所述电镀子槽内设置有用于平缓电镀液流速的均流网,所述均流网位于所述传送装置和所述镀液喷管之间。进一步地,所述均流网为平板,所述平板上设置有均匀分布的网孔。进一步地,所述平板的厚度与所述电镀子槽内的电镀液的深度比在1:50至1:300之间。进一步地,所述网孔为锥孔,所述网孔的内壁的直径沿竖直向上方向逐渐增大。进一步地,所述均流网至所述镀液喷管的距离与所述镀液喷管至所述电镀子槽底壁的距离比在2:1至于10:1之间。进一步地,所述均流网的网目在5‐50之间。进一步地,所述电镀子槽的侧壁上设有溢流槽,设置于所述电镀子槽侧壁的外侧,所述镀液回流管的一端连接于所述溢流槽的下部,另一端连接于所述电镀子槽的下部。进一步地,所述镀液回流管上连接有用以调节所述电镀子槽内的电镀液各成分浓度的电镀母槽。进一步地,于所述电镀母槽的出口处,所述镀液喷管上安装有用于电镀母槽内电镀液泵送至所述电镀子槽内的循环泵和用于过滤污垢残渣的过滤机。进一步地,所述传动装置包括相互啮合的压辊和托辊,所述衬底穿设于所述压辊和所述托辊啮合处,所述压辊和所述托辊分别抵顶所述衬底的上、下面。进一步地,所述托辊包括中间轴和连接于所述中间轴两端的圆饼,所述圆饼的中心线和所述中间轴的中心线相重合,所述圆饼的外径大于所述中间轴的外径,所述圆饼与所述压辊啮合。进一步地,所述清洗槽内设有喷管组和设于所述清洗槽下部用于传输所述衬底的转轮;所述喷管组包括置于所述转轮上方并位于所述清洗槽中间处由中间向所述清洗槽侧壁喷射用以清洗所述衬底背面的第一喷管组和相对于所述第一喷管组设置并位于所述清洗槽侧壁处并用以清洗所述衬底正面的第二喷管组;所述第一喷管组和所述第二喷管均包括至少一根竖向并排设置的喷管,任一所述喷管上均安设有均匀分布的清洗喷嘴。与现有技术相比,本发明提供的一种制备CIGS吸收层的电镀生产线,通过将衬底贴设于传送装置的侧面,如此,延长了衬底设置于电镀子槽中的沉积长度,增加了沉积CIGS吸收层的面积,这样,缩短了制备CIGS吸收层的电镀生产线的长度,节约了空间,而且衬底贴设于传送装置上,如此,仅对衬底的一面进行沉积,毋须对衬底的另一面做去除处理,简化了工艺步骤,同时,所述阳极挂设于电镀子槽侧面相对所述衬底设置,所述衬底和所述阳极平面对平面,整个沉积过程中,所述阳极平面的表面损耗一致,确保了所述衬底表面沉积的CIGS吸收层的良好均匀度和稳定的沉积速率。附图说明图1是现有技术中于衬底上电镀沉积CIGS吸收层的结构示意图;图2是本发明实施例提供的于衬底上沉积CIGS吸收层的电镀生产线流程示意图;图3是图2中一次镀铜槽的组成示意图;图4a是图3中传送装置的一结构示意图;图4b是图3中传送装置的又一结构示意图;图4c是图3中传送装置的另一结构示意图;图4d是图3中传送装置的再一结构示意图;图5是图2中一次镀铜槽内的局部剖视示意图;图5a是图5中一次镀铜槽内镀液喷管的截面示意图;图6是图2中一次镀铜槽入口处的传动装置示意图;图7是图2中第一清洗槽的结构示意图。标记说明:100控制系统525镀硒槽200送料装置526镀硒子槽300传动装置527镀硒母槽301压辊528镀硒液302托辊529硒阳极3021圆饼530调整装置3022中间轴531镀铜子槽底壁401第一清洗槽532溢流槽402第二清洗槽501B二次镀铜槽403第三清洗槽502B二次镀铜子槽404第四清洗槽503B二次镀铜母槽405第五清洗槽504B二次镀铜液406第六清洗槽600收料装置407转轮701不锈钢带408清洗喷嘴702镀有铜的不锈钢带409第一喷管组703镀有Cu/Ga的不锈钢带410第二喷管组704镀有Cu/Ga/Cu的不锈钢带501一次镀铜槽705镀有Cu/Ga/Cu/In的不锈钢带502一次镀铜子槽706镀有Cu/Ga/Cu/In/Se的不锈钢带503一次镀铜母槽800阳极504一次镀铜液801大转轮505铜阳极802镀液槽506传送装置803电镀液506A固定架804尖部507传输带805凹面508从辊轮806柔性衬底509主辊轮X1第一间距510均流网X2第二间距511镀液喷管X3第三间距512过滤机X4第四间距513循环泵X5第五间距514镀液回流管L镀液喷管长度515镀镓槽d1喷孔间距离516镀镓子槽d2喷孔直径517镀镓母槽d3均流网孔直径518镀镓液d4均流网孔间距519镓阳极d5均流网厚度520镀铟槽α喷孔开孔锥度521镀铟子槽β两排孔之间的夹角522镀铟母槽γ均流网孔开孔锥度523镀铟液h1镀液喷管与均流网的距离524铟阳极h2镀液喷管与子槽底部的距离S内截面具体实施方式为了使本发明的目的、技术方案及优点更加清楚明白,以下结合附图及实施例,对本发明进行进一步详细说明。应当理解,此处所描述的具体实施例仅用以解释本发明,并不用于限定本发明。本发明是一种制备CIGS吸收层的电镀生产线,用于在衬底上沉积铜铟镓硒元素形成CIGS吸收层。可以理解,所述衬底为利于沉积CIGS吸收层的导电材质制作而成,如铝箔、钛箔、钼箔、黄铜箔、不锈钢等。本实施例中,所述衬底为100~600mm宽,50~100nm厚的430不锈钢卷带,经过清洗吹干,按顺序真空溅射100~500nm厚的Cr、100~500nm的Mo、20~150nm的Cu制作而成。即所述衬底表面预先溅射有Cr/Mo/Cu。所述衬底具有上、下两表面,为便于后续说明,将所述衬底溅射有Cr/Mo/Cu的下表面定义为正面,所述衬底的上表面定义为背面。预先溅射有Cr/Mo/Cu的不锈钢带701通过本发明提供的制备CIGS吸收层的电镀生产线,将CIGS吸收层沉积于所述不锈钢钢带的正面。如图2‐7所示,为本发明提供的较佳实施例。本发明实施例提供的一种制备CIGS吸收层的电镀生产线呈横向线性排列,包括送料装置200、传动装置300、至少四个电镀槽、多个清洗槽、收料装置600和控制系统100。所述送料装置200位于所述电镀生产线的首端,用于连续供应所述不锈钢带701将其送置下一工位。通常,所述送料装置200输送的不锈钢带701的移动速度为0.5~2m/s。所述不锈钢带701呈卷状架设于所述送料装置200上,随着所述送料装置200带动卷状的不锈钢带701转动,使得不锈钢带701沿着与卷状不锈钢带701的周边相切的方向,逐步展开呈平板状。任一所述电镀槽和所述清洗槽的入口处和出口处均设有所述传动装置300,所述传动装置300夹持所述不锈钢带701并带动所述不锈钢带701一同移动,使得所述不锈钢带701蜿蜒穿设于各清洗槽和电镀槽中,同时可将卷状的不锈钢带701由所述送料装置200展开后碾压平整,从而确保电镀沉积于不锈钢带701上的平整度。如图2所示,本实施例中设置有五个电镀槽,沿所述不锈钢带701移动方向,依次为:一次镀铜槽501、镀镓槽515、二次镀铜槽501B、镀铟槽520和镀硒槽525。其中,一次镀铜槽501和二次镀铜槽501B中分别盛装有一次镀铜液504和二次镀铜液504B,镀镓槽515内盛装有镀镓液518,镀铟槽520内盛装有镀铟液523,镀硒槽525内盛装有镀硒液528,如此,可分别将铜、镓、铟、硒元素沉积于所述不锈钢带701的正面,形成Cu/Ga/Cu/In/Se的CIGS吸收层。可以理解地,根据不同的需要可以合理设置各个电镀槽的种类、个数和顺序,从而得到如:Cu/In/Cu/Ga/Se、Cu/In/Cu/Ga/Cu/In/Se、Cu/Ga/Cu/In/Cu/Ga/Se等多种样式的CIGS吸收层。当然,也可以理解,所述制备CIGS吸收层的电镀生产线也可竖向线性排列,使得所述不锈钢带701于竖直方向上输送移动。也可以将所述电镀生产线竖向与横向相结合的方式,使得所述不锈钢带701于竖向和横向来回穿梭缠绕输送都是可行的。本实施例中,各所述电镀槽均包括有盛装电镀液用于电镀工作的子槽,所述子槽的中间处设有携带所述不锈钢带701同步移动的传送装置506,传动路径呈由多线段首尾相接而成的封闭状,所述子槽的侧面挂设有浸没于所述电镀液中且用于沉积CIGS吸收层的阳极,所述阳极呈板状设置,所述阳极分别与所述传送装置506上沉浸于电镀液中两侧面平行相对设置,所述不锈钢带701贴附于所述传送装置506上沉浸于电镀液内的侧面且与所述阳极相对平行相对设置,并具有一个适当的间距。具体地,如图2和图3所示,所述一次镀铜槽501包括一个一次镀铜子槽502,所述一次镀铜子槽502的中间处设有传送装置506,所述传输装置外轮廓呈方体状,具有六个面,其中,传送装置506的左右侧面和所述一次镀铜槽501内壁的左右侧面相对。所述不锈钢带701贴附于所述传送装置506的左右侧面和底面,于电镀子槽中,延长了沉积不锈钢带701的长度,增加了沉积CIGS吸收层的面积,提高了沉积的效率,同时,缩短了制备CIGS吸收层的电镀生产线的长度,节约了空间。通过所述传送装置506的转动可携带所述不锈钢带701同步移动。不锈钢带701背面与传送装置506的左右侧面和底面相贴,并且两者同步移动,如此,避免不锈钢带701背面镀上金属层。即仅对不锈钢带701的正面进行沉积,毋须对不锈钢带701的背面做去除处理,简化了工艺步骤,提高了沉积效率,节约了成本。所述一次镀铜子槽502的左右侧面分别挂设有铜阳极505,所述铜阳极505为平板状,所述铜阳极505浸没于所述一次镀铜子槽502内的镀铜液中,如此,阳极加工简单,呈长条形,相对待镀的不锈钢带701稍宽,挂在电镀子槽的两侧,且更换阳极方便简单。所述铜阳极505分布于所述传动装置300的左右两侧并与所述不锈钢带701相对设置,具有一个间距。通过将所述不锈钢带701相对阳极设置,所述不锈钢带701和所述阳极平面对平面,整个沉积过程中,所述阳极平面的表面损耗一致,确保了所述不锈钢带701表面沉积的CIGS吸收层的良好均匀度和稳定的沉积速率。实际生产中,根据工艺需要调整所述铜阳极505和所述不锈钢带701之间的间距。基于同一设计理念,各个电镀子槽的构造和工作原理类似,如图2所示,所述镀镓槽515中的子槽为镀镓子槽516;其内壁的左右侧面挂设的阳极为镓阳极519;所述二次镀铜槽501B包括的子槽为二次镀铜槽502B;其内壁的左右侧面挂设的阳极为铜阳极505;所述镀铟槽520中的子槽为镀铟子槽521;其内壁的左右侧面挂设的阳极为铟阳极524;所述镀硒槽525中的子槽为镀硒子槽526;其内壁的左右侧面挂设的阳极为硒阳极529。为便于区分,将所述一次镀铜子槽502内铜阳极505与所述不锈钢带701之间的间距定义为第一间距X1;镀镓槽515内的镓阳极519与所述不锈钢带701之间的间距定义为第二间距X2;二次镀铜槽502B内铜阳极505与所述不锈钢带701之间的间距定义为第三间距X3;镀铟子槽521内的铟阳极524与所述不锈钢带701之间的间距定义为第四间距X4;镀硒子槽526内的硒阳极529与所述不锈钢带701之间的间距定义为第五间距X5;根据各镀层不同电镀工艺,合理设置各阳极板与所述不锈钢带701之间的间距,也就是说,所述第一间距X1、第二间距X2、第三间距X3、第四间距X4和第五间距X5的间距数值可以是相同也可以不同,只要满足相应的电镀工艺即可,通过调节阳极与所述不锈钢带701间的距离,当间隙较小时,电镀液高速逆向通过,使阴极上析出的气泡及时被镀液带走,保证了沉积层的表面没有花斑。为了更好的保持不锈钢带701表面的清洁度并避免电镀液的交叉污染,于任一所述电镀槽的前后处均设置有清洗槽,该处所述电镀槽的前后处指的是沿着所述不锈钢带701的移动方向而言。本实施例中,具有六个清洗槽,沿输送所述不锈钢带701的方向,依次为第一清洗槽401、第二清洗槽402、第三清洗槽403、第四清洗槽404、第五清洗槽405和第六清洗槽406,其中第一清洗槽401位于所述上料装置和所述一次镀铜子槽502之间,所述第二清洗槽402位于一次镀铜子槽502与镀镓子槽516之间,所述第三清洗槽403位于镀镓子槽516与二次镀铜槽502B之间,所述第四清洗槽404位于所述二次镀铜槽502B与镀铟子槽521之间,第五清洗槽405位于镀铟子槽521与镀硒子槽526之间,第六清洗槽406位于镀硒子槽526与收料装置600之间。如此,可实现不锈钢带701进入电镀子槽前都经过表面清洁,从而保证了不锈钢带701表面沉积的效果。所述收料装置600设置于所述电镀生产线的末端;用于将表面形成CIGS吸收层的不锈钢带701收集成卷,以便于存放运输。实际制作中,所述收料装置600包括一个支撑架和架设于所述支撑架上的旋转轮,将沉积有CIGS吸收层的不锈钢带701的一端固定于所述旋转轮上,随着旋转轮的转动,将沉积有CIGS吸收层的不锈钢带701收集成卷。通常,还会于所述收料装置600之前设置干燥装置和自动纠偏装置,将所述沉积有CIGS吸收层的不锈钢带701干燥后在送入所述收料装置600中收集成卷。所述控制系统100,分别与所述送料装置200、所述清洗槽、所述电镀槽和所述收料装置600电性连接。实际制作中,通过所述控制系统100控制所述送料装置200、所述清洗槽、所述电镀槽和所述收料装置600同步动作。根据各镀层的所需厚度,设置不锈钢带701的输送速度和各自对应的电镀电流,镀液流速等工艺参数,从而保证所述不锈钢带701上均匀沉积各种金属层,易于自动化。具体地,如图4a‐4d所示,所述传送装置506包括一固定架506A、至少一组主辊轮509和至少一组与所述主辊轮509配合转动的从辊轮508以及传输带507,所述固定架506A的截面呈矩形状,所述传送带507呈矩形设置并贴设于所述主辊轮509和所述从辊轮508的外周面上并携带所述衬底一同运动。所述主辊轮509安装于所述固定架506A上部并抵顶所述不锈钢带701;所述从辊轮508安装于所述固定架506A下部也抵顶所述不锈钢带701;所述传输带507贴设于所述主辊轮509和所述从辊轮508的外周面上随着所述主辊轮509和所述从辊轮508的转动而携带所述不锈钢带701一同移动。如此,结构简单,一方面,确保所述不锈钢带701的背面紧紧贴附于所述传输带507上具体地,如图4a所示,所述主辊轮509和所述从辊轮508的外周面与所述固定架506A的外侧壁相切。所示固定架506A的顶部的两个转角处各固设有一个可转动的主辊轮509,所述主辊轮509的外周面与所述固定架506A的顶边和左、右侧边相切,所示固定架506A的下部的两个转角处各固设有一个可转动的从辊轮508,所述从辊轮508的外周面与所述固定架506A的底边和和左、右侧边相切。所述传输带507分别绕两根主辊轮509和两根从辊轮508围成一个密封的长方体。于电镀子槽内,所述传动装置300均与所述主辊轮509相互啮合,不锈钢带701经过传动装置300和主辊轮509啮合处,向下绕设置于所述传送装置506下部的两个从辊轮508,贴附从所述传送装置506的另一侧绕出,不锈钢衬底背面与传输带507抵紧相贴,起到保护不锈钢带701背面不被沉积上金属层。又或者,如图4b所示,所述主辊轮509设有两个,固设于所述固定架506A顶部的转角处,所述从辊轮508设有两个,设置于所述固定架506A的下部的转角处,所述主辊轮509和所述从辊轮508的外周面凸出于所述固定架506A的外侧壁。所述传输带507套设于所述主辊轮509和所述从辊轮508的外周面上,所述主辊轮509和所述从辊轮508抵紧所述传输带507。如图4c所示,所述传送装置506的另一实施例。两个所述主辊轮509分别设置于所述固定架506A顶部的转角处,所述从辊轮508设有九个,其中,三个固设于所述固定架506A的下部的底边上,所述固定架506A的两边各固定有三个所述从辊轮508。所述传输带507套设于所述主辊轮509和所述从辊轮508的外周面上,所述主辊轮509和所述从辊轮508抵紧所述传输带507。如图4d所示,所述传送装置506上还设有用于调节所述传输带507张紧度的调整装置530,所述调整装置530与所述主辊轮509和所述从辊轮508可调节连接。具体地,图4d中未详细示出,所述调节装置具有一个固定柱穿设于所述固定架506A的中间位置,固定柱与所述主辊轮509和所述从辊轮508通过调节件连接,本实施例中的调节件为直动气缸,所述直动气缸的底座铰接于所述固定柱,所述直动气缸的活塞杆连接所述主辊轮509或所述从辊轮508上的固定轴。如此,可调节所述传输带507的张紧度,进而调节所述传输带507上不锈钢带701的张紧度。具体地,所述传输带507上还设有可吸附所述不锈钢带701的吸附部。本实施例中的所述吸附部为真空吸头,所述真空吸头设于所述传输带507上与所述不锈钢带701贴合的一面,如此,可使所述不锈钢带701更加紧实的贴合于所述传输带507上,避免电镀液渗入到所述不锈钢带701的背面。具体应用时,通过设置一个真空发生器与所述真空吸头连接,当所述不锈钢带701刚进入所述电镀子槽入口处时,所述不锈钢带701位于电镀液上方,与所述传输带507即将接触那一刻,所述传输带507上即将与所述不锈钢带701接触到的吸头开启,从而将所述不锈钢带701牢牢贴附于所述传输带507上;当所述不锈钢带701带出电镀液,即将离开电镀子槽时,也就是不锈钢带701即将与所述传输带507分开时,位于出口处的不锈钢带701上的真空吸头关闭,即可使得所述传输带507与所述不锈钢带701分离,如此,避免真空吸头倒吸所述电镀液,同时有保证了所述不锈钢带701吸附于所述传输带507上的牢固度,避免所述不锈钢带701的背面沉积金属镀层。当然,为进一步提高所述传输带507的使用寿命,可采用耐腐蚀的材质制作,并于所述真空吸头的气道上设置一个连通至所述电镀子槽内的回流通道,也就是,一旦所述真空吸头吸入所述电镀液,所述回流通道开启,将所述电镀液回流至对应的电镀子槽内。如此,进一步避免了所述不锈钢带701背面沉积金属层。如图2和图3所示,为了使得电镀槽内的电镀液混合的均匀,各个电镀子槽内均设置有至少一根镀液喷管511。由于各电镀子槽的构造和原理相似,为便于说明,现以一次镀铜子槽502为例进行说明。如图5和图5a所示,于所述一次镀铜子槽502内,所述镀液喷管511上设置有均匀分布的喷孔。具体地,所述喷孔为锥形孔,所述喷孔的内壁沿所述镀液喷管511的管内向管外方向逐渐扩大。进一步地,所述喷孔的喷射方向朝向所述电镀子槽的底壁。如此,电镀液经过设置于所述镀铜子槽底壁531的镀液喷管511向下喷出,触底反弹后向上搅拌电镀液,使电镀混合的更加均匀,各处浓度相同。通常,喷孔开孔锥度α为30°~60°。进一步地,同一镀液喷管511上设置的喷孔间距离d1与所述喷孔直径d2的比在20:1至5:1之间。本实施例中,所述喷孔间距离d1为2~20mm,喷孔直径d2为0.5~3.5mm。具体地,同一所述镀液喷管511上设置有两排喷孔,所述两排喷孔的喷射方向呈夹角设置。通常,两排喷孔之间的夹角β为60°~120°。进一步地,所述电镀子槽内设置有均流网510,所述均流网510用于平缓向上涌动的电镀液的流速,所述均流网510位于所述传送装置506和所述镀液喷管511之间。如此,当涌动的电镀液经过均流网510板后,激烈的涌动得以平缓,使所述电镀液变得平静,不易产生气泡,避免在电镀层表面产生花斑。具体地,所述镀液喷管511与子槽底部的距离与所述电镀子槽的电镀液的深度比在1:7至1:20之间。如此,将镀液喷管511设于所述电镀子槽中的合适位置,可确保电镀液具有较佳的搅拌效果,同时避免残存污垢堵塞,镀液喷管511上的喷孔。进一步地,所述均流网510为平板,所述平板上设置有均匀分布的网孔。具体地,所述网孔也为锥孔,也就是,开口朝上的喇叭孔,所述网孔的内壁的直径沿竖直向上方向逐渐增大,通常,均流网孔直径d3为0.5~3.5mm,均流网孔开孔锥度γ为20°~75°。具体地,所述均流网510的网目在5‐50之间。通常,均流网孔间距d4为1~5mm。进一步地,所述平板的厚度与所述电镀子槽内的电镀液的深度比在1:50至1:300之间。通常,均流网厚度d5为1~5mm。具体地,镀液喷管511与均流网510的距离h1与镀液喷管511与子槽底部的距离h2之比h1/h2在2:1至10:1之间。如此,既保证了镀铜子槽底部无循环死角,又使得往上涌流的电镀液匀速平静,从而不产生气泡,保证了镀层表面没有花斑。为便于说明,指定电镀子槽宽为xmm,长为ymm,通常,镀液喷管长度L为x‐(15mm~28mm),喷管的根数N为(1/2)*(y/h2)*ctg(β/2),N取整数。具体地,如图2所示,为避免一次镀铜子槽502内镀铜液的浓度波动过大,所述一次镀铜子槽502配设有一个一次镀铜母槽503。同理,所述二次镀铜槽502B配备有一个二次镀铜母槽503B,用于调节所述二次镀铜槽502B内的二次镀铜液504B浓度;所述镀镓子槽516均配设有一个镀镓母槽517,用于调节所述镀镓子槽516内的镀镓液518浓度;所述镀铟子槽521配设有一个镀铟母槽522,用于调节所述镀铟子槽521内的镀铟液523浓度;所述镀硒子槽526配设有一个镀硒母槽527,用于调节所述镀硒子槽526内的镀硒浓度;如此,可使得所述电镀子槽内的电镀液始终处于一个适宜沉积金属层的浓度。具体地,所述一次镀铜子槽502的侧壁上设有溢流装置,所述溢流装置通过镀液回流管514与所述一次镀铜子槽502的下部连通。具体地,所述溢流装置为溢流槽532,所述镀液回流管514的一端连接于所述溢流槽532的下部,另一端连接于所述一次镀铜子槽502的下部。进一步地,所述镀液回流管514上连接有电镀母槽,所述电镀母槽用以调节所述电镀子槽内的电镀液各成分的浓度。本实施例中,所述电镀母槽为一次镀铜母槽503。如图3所示,所述镀液回流管514的一端连接于所述溢流槽532的下部,另一端连接于所述一次镀铜母槽503。镀液流回电镀母槽,再经过循环泵,过滤桶,输送回电镀子槽,实现循环具体地,于所述一次电镀母槽的出口处的所述镀液喷管511上安装有循环泵513和用于过滤污垢残渣的过滤机512。本实例中的所述循环泵513可将电镀母槽内的电镀液泵送至所述电镀子槽内。如此,可实现一次镀铜液504的循环流动,并不断净化所述一次镀铜槽501内电镀液,保持一次镀铜槽501内的干净和镀液浓度保持稳定。所述镀液回流管514进入一次镀铜子槽502内分成多根镀液喷管511。如图5a所示,各镀液喷管511的内截面S之和等于或大于所述镀液回流管514的内截面。下面就一次镀铜液504的循环过程作简要说明:所述一次镀铜母槽503中的一次镀铜液504电镀液由循环泵513抽出,经过过滤机512过滤后,由于镀液回流管514分流至一次镀铜子槽502内的镀液喷管511,经镀液喷管511上的喷孔朝下喷出,触碰镀铜子槽底壁531后反弹向上涌动,经过均流网510平缓减速,波动的一次镀铜液504即刻变得平静,一次镀铜子槽502内的液面上升,消除了涌浪,穿过铜阳极505与不锈钢钢带之间的夹缝,溢出所述一次镀铜子槽502的侧壁,流入设置于所述一次镀铜子槽502侧壁上的溢流槽532中,再回流入一次镀铜母槽503中,与所述一次镀铜母槽503内的一次镀铜液504混合,再由循环泵513泵出至所述一次镀铜子槽502内,如此反复循环。进一步地,如图6和图2所示,所述传动装置300包括相互啮合的压辊301和托辊302,所述不锈钢带701穿设于所述压辊301和所述托辊302啮合处,所述压辊301和所述托辊302分别抵顶所述不锈钢带701的上、下面。实际应用中,所述托辊302为动力件,带动所述压辊301转动。位于电镀子槽进口处和出口处的托辊302还同时具有导电的作用,电镀时托辊302接电源阴极,把电流传导到待镀的不锈钢衬底上,使不锈钢衬底成为阴极。如此,将不锈钢带701穿设于所述压辊301与所述托辊302啮合处,可以将展开的卷状的不锈钢带701压平,同时还可传送和张紧不锈钢带701,使不锈钢带701以一定的速度移动,并处于张紧状态。再者,所述压辊301和所述托辊302均为转动体,可将不锈钢带701的变向,使不锈钢带701蜿蜒缠绕布置,节省设备占用的空间。为了避免托辊302与待镀的不锈钢带701面接触,本实施例中将托辊302中间处挖空设置,具体地,所述托辊302包括中间轴3022和连接于所述中间轴3022两端的圆饼3021,所述圆饼3021的中心线和所述中间轴3022的中心线相重合,所述圆饼3021的外径大于所述中间轴3022的外径,所述圆饼3021与所述压辊301啮合。如此,所述圆饼3021外周面仅抵压在不锈钢带701的侧边缘,而中间轴3022不与所述不锈钢带701的中间部分相接触,这样,可保证待镀不锈钢带701的表面不被划伤。由于六个清洗槽的构造和工作原理类似,下面以第一清洗槽401为例说明其内部布置:所述清洗槽内设有喷管组和设于所述清洗槽下部居中,用于传输所述不锈钢带701的转轮407;本实施例中,所述喷管组竖向设置,所述不锈钢带701缠绕于所述转轮407的外周面。所述喷管组包括第一喷管组409和第二喷管组410。所述第一喷管组409置于所述转轮407上方并位于所述清洗槽中间处,由中间向所述清洗槽侧壁喷射用以清洗所述不锈钢带701背面,所述第二喷管组410具有两组,相对于所述第一喷管组409设置,分别位于所述清洗槽的左右两侧壁,用以清洗所述不锈钢带701正面;所述第一喷管组409和所述第二喷管均包括至少一根竖向并排设置的喷管,任一所述喷管上均安设有均匀分布的清洗喷嘴408,所述清洗喷嘴408喷射方向均朝向所述不锈钢带701的表面。下面对整个所述的制备CIGS吸收层的电镀生产线的工作过程进行说明:成卷设置的不锈钢带701的表面预先溅射有Cr/Mo/Cu,经过送料装置200的旋转展开,穿过传动装置300上的所述压辊301与所述托辊302的啮合处,由所述压辊301和所述托辊302将不锈钢带701压平,进入第一清洗槽401内绕过转轮407,所述第一清洗槽401的喷管组同时清洗所述不锈钢带701的正面和背面,同时所述不锈钢带701始终处于一个运动状态,再由所述传动装置300进入一次镀铜子槽502内,所述不锈钢带701经过所述一次镀铜子槽502后,仅正面沉积有一层铜层,变成镀有铜的不锈钢带702,再进入第二清洗槽402清洗,而后经过镀镓子槽516,正面进一步沉积镓元素,变成镀有Cu/Ga的不锈钢带703,再进入第三清洗槽403清洗,再经过二次镀铜槽502B的二次沉铜,正面进一步沉积铜元素,变成镀有Cu/Ga/Cu的不锈钢带704,再进入第四清洗槽404清洗,再经过所述镀铟子槽521,正面进一步沉积铟元素,变成镀有Cu/Ga/Cu/In的不锈钢带705,再进入第五清洗槽405清洗,再经过所述镀硒子槽526,沉积硒元素,变成镀有Cu/Ga/Cu/In/Se的不锈钢带706,在进入第六清洗槽406清洗,再由所述收料装置600收集成卷,如此,便于不锈钢带701正面沉积有CIGS吸收层。以上所述仅为本发明的较佳实施例而已,并不用以限制本发明,凡在本发明的精神和原则之内所作的任何修改、等同替换和改进等,均应包含在本发明的保护范围之内。