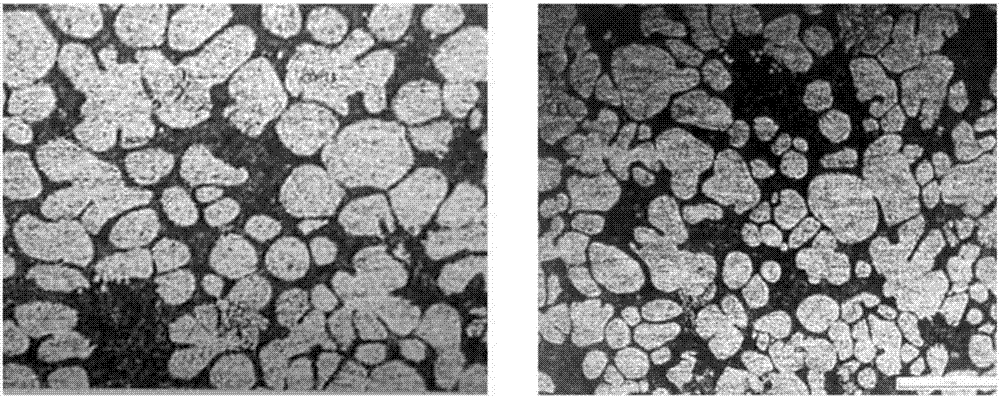
本发明属于金属/合金的半固态流变压铸生产及压铸成形
技术领域:
,涉及一种合金半固态浆料制备方法。
背景技术:
:半固态成形技术属于21世纪前沿性的金属加工技术,近年来得到快速发展。半固态流变压铸技术使传统压铸方式发生了深刻变化,半固态成形技术打破了传统的枝晶凝固模式,粒状晶组织提高了铸件密度,铸件的综合性能得到提高。在半固态流变压铸工艺中,半固态浆料的质量是半固态成形技术的关键因素,而精确控制液态合金温度和半固态浆料温度是保证半固态浆料质量的工艺基础。半固态浆料的制备方法,国内外学者进行了大量的研究工作,提出了许多半固态金属浆料制备工艺方法:包括机械搅拌法、电磁搅拌法、控制凝固法、应变诱发激活方法(sima法)、等温处理法、近液相线浇注法、喷射沉积法、粉末冶金法等。大多制浆方法仅适用实验室研究,由于技术受限,不能推广应用到实际压铸生产过程。目前,一般的机械搅拌法、机械搅拌结合空气冷却的制浆方法降温效率低,半固态组织粒状晶圆整度差,固体含量低。且使一般的制浆工艺在机械搅拌过程中卷气导致半固态浆料含气量高,半固态产品不能做t6热处理提高强度。技术实现要素:本发明一种半固态浆料制备方法,旨在提高半固态浆料的质量与稳定性,并使半固态产品可以进行t6热处理提高机械性能。根据本发明的一个方面,提供了一种半固态浆料制备方法,包括以下步骤:1s:将合金液转入密封保温炉,保持第一预定温度;2s:将第一预定质量的合金液以预定压力压入密封制浆装置,加入预定比例的形核合金,通入冷却介质,搅拌合金液降至第二预定温度,制得半固态浆料。其中,步骤2s中所述搅拌采用机械搅拌,搅拌转速在1200-2000r.min-1,搅拌时间为15-35s。其中,步骤1s中所述第一预定温度为660-675℃。其中,步骤2s中所述第一预定质量为4200-4300g;所述预定压力为0.1-0.2mpa。其中,步骤2s中所述第二预定温度为595-605℃。其中,步骤2s中所述预定比例为0.7%-1.8%。其中,步骤2s中所述冷却介质为液态或气体冷却介质;所述液态冷却介质为导热油,所述气态冷却介质为压缩空气,流量为10-30l/min。其中,包括以下步骤:1s:将铝合金液转入密封保温炉,保持670℃;2s:将4250g的合金液以0.15mpa的压力压入密封制浆装置,加入1%的al-si-sr形核合金,通入20l/min的压缩空气,搅拌转速在1500r.min-1,搅拌时间为25s,搅拌合金液降至600℃,制得半固态浆料。其中,包括以下步骤:1s:将铝合金液转入密封保温炉,保持665℃;2s:将4200g的合金液以0.1mpa的压力压入密封制浆装置,加入0.9%的al-si-sr形核合金,通入20l/min的压缩空气,搅拌转速在2000r.min-1,搅拌时间为20,搅拌合金液降至598℃,制得半固态浆料。本发明的半固态浆料制备方法,首先将合金液转入密封保温炉,保持在660-675℃,优选的,为670℃。660-675℃是压铸生产铝液需要保持的温度,在这个温度下的铝液舀入舀汤进行制浆,由于每个制浆循环需要的铝液进入汤勺后,离开密封保温炉液面到制浆前温度会下降到650℃;而在机械搅拌制浆后温度会降到610℃左右,610℃左右半固态浆料倒入压铸机料管后在595-605℃压铸。660-675℃铝液保证了铝液有足够的制浆温度区间,从而把铝液制备成有一定固相率的半固态浆料。然后,将第一预定质量的合金液以预定压力压入密封制浆装置,加入预定比例的形核合金,通入冷却介质,搅拌合金液降至第二预定温度,制得半固态浆料。其中,第一预定质量为4200-4300g;该重量范围是依据压铸的半固态产品重量所确定的,通过抽真空加压方式以0.1-0.2mpa的压力将以上质量的合金溶液压入到密封制浆装置中。用密封保温炉储存液态合金液,通过管道压力供液方式控制每个制浆循环需要的液态合金量,可以保证合金液温度偏差在5℃之内,每次输送的合金质量偏差在100g之内。通过与密封制浆装置相连通的外部管道通入冷却介质,冷却介质为液态或气体冷却介质,液态冷却介质为导热油;气态冷却介质为压缩空气,流量为10-30l/min。搅拌方式选用机械搅拌,搅拌转速在1200-2000r.min-1;搅拌时间为15-35s。本发明选用高速旋转引晶进行制浆,在该转速范围下,使半固态浆料组织更加细化,粒状晶元整。搅拌合金液降至第二预定温度,制得半固态浆料。第二预定温度为595-605℃,优选的,为600℃。在搅拌过程中当铝液温度降低到620℃以下时,就会出现固态物质,也就是形成了半固态浆料;生产过程中是通过控制半固态浆料的温度来控制半固态浆料的固体含量,通过一定的搅拌转速和搅拌时间是铝液温度降到第二预定温度而形成具有固定固体含量的半固态浆料。通过与密封制浆装置相连通的外部管道加入形核合金,形核合金是在制浆开始时加入,通过管道一次加入,加入比例为0.7%-1.8%。形核合金加入后在搅拌过程中熔化在铝合金液中,熔化的形核合金组织作为半固态粒状晶的成核核心,从而使半固态浆料的粒状晶细化圆整,既控制了半固态浆料粒状晶的晶粒尺寸,又保证了粒状晶的形状。压铸生产中制浆时间很短,在15-35s时间内把第一预定温度的铝液制备成第二预定温度的半固态浆料,通过大量实验确定出形核合金的加入量,形核合金加入量、搅拌转速、搅拌时间、冷却介质通入流量对半固态浆料的固相率都有影响,专利技术通过大量的试验优化出最佳制浆参数,在最佳制浆参数下制备出高质量的半固态浆料。机械搅拌、形核合金、气体或液态冷却介质冷却三者结合,在预设的参数下可以快速制备固体含量在40-50%的半固态浆料,半固态粒状晶组织元整度>0.80,晶粒尺寸<0.6μm。通过密封制浆设备制备半固态浆料,搅拌过程中规避了合金液卷气,制备的半固态浆料含氢量<0.2cc/100g,低含气量的半固态浆料生产的半固态产品可做t6热处理,从而提高了半固态产品的力学性能。本发明的半固态浆料制备方法,通过控制每次制浆所需的合金液的质量和温度,通过控制密封制浆装置的形核合金的加入量、搅拌转速、搅拌时间、冷却介质的流量,制备出温度恒定、含气量低的半固态浆料,保证了半固态浆料的质量;使半固态产品可以提高t6热处理提高性能,从而拓宽了半固态产品的应用领域。同时,密封定量制浆工艺开拓了半固态浆料制备的新思路,也推动了半固态压铸生产的进程。参照附图来阅读对于示例性实施例的以下描述,本发明的其他特性特征和优点将变得清晰。附图说明并入到说明书中并且构成说明书的一部分的附图示出了本发明的实施例,并且与描述一起用于解释本发明的原理。在这些附图中,类似的附图标记用于表示类似的要素。下面描述中的附图是本发明的一些实施例,而不是全部实施例。对于本领域普通技术人员来讲,在不付出创造性劳动的前提下,可以根据这些附图获得其他的附图。图1示例性地示出了根据本发明的半固态浆料制备方法的步骤图;图2示例性地示出了根据本发明的半固态浆料制备方法制备的半固态浆料金相组织图。具体实施方式为使本发明实施例的目的、技术方案和优点更加清楚,下面将结合本发明实施例中的附图,对本发明实施例中的技术方案进行清楚、完整地描述,显然,所描述的实施例是本发明一部分实施例,而不是全部的实施例。基于本发明中的实施例,本领域普通技术人员在没有做出创造性劳动前提下所获得的所有其他实施例,都属于本发明保护的范围。需要说明的是,在不冲突的情况下,本申请中的实施例及实施例中的特征可以相互任意组合。本发明提供的半固态浆料制备方法包括以下步骤:将合金液转入密封保温炉,保持660-675℃;将4200-4300g的合金液以0.1-0.2mpa的压力压入密封制浆装置,加入0.7%-1.8%的形核合金,通入导热油或流量为10-30l/min的压缩空气;机械搅拌,转速在1200-2000r.min-1,搅拌时间为15-35s,搅拌合金液降至595-605℃,制得半固态浆料。下面示出本发明的半固态浆料制备方法的具体实施例。实施例实施例1将铝合金液转入密封保温炉,保持670℃;2s:将4250g的合金液以0.15mpa的压力压入密封制浆装置,加入1%的al-si-sr形核合金,通入20l/min的压缩空气,搅拌转速在1500r.min-1,搅拌时间为25s,搅拌合金液降至600℃,制得半固态浆料。实施例2将铝合金液转入密封保温炉,保持665℃;2s:将4200g的合金液以0.1mpa的压力压入密封制浆装置,加入0.9%的al-si-sr形核合金,通入20l/min的压缩空气,搅拌转速在2000r.min-1,搅拌时间为20s,搅拌合金液降至598℃,制得半固态浆料。本发明的半固态浆料制备方法的实施例还可以如表1所示。表1实施例3实施例4实施例5实施例6实施例7实施例8第一预定温度(℃)660672675670665662第一预定质量(g)430043004250425042004200预定压力(mpa)0.10.10.150.150.20.2搅拌转速(r.min-1)120013001400180020001500搅拌时间(s)353028241625预定比例(%)0.80.911.21.51.8第二预定温度(℃)600605602603598595测试例下面对本发明半固态浆料的制备方法的各工艺参数进行了实验探究。表2固定搅拌速度和搅拌时间,固定合金溶液质量在第一预定质量范围内。表2不同温度下的半固态浆料的含气量从表2的实验数据可以看出,第一预定温度对第二预定温度和浆料密度有一定影响,第一预定温度为660-675℃,第二预定温度为595-605℃时制备的半固态浆料密度在2.65-2.68之间;当第一预定温度为670℃,第二预定温度为600℃,此时半固态浆料的密度为2.68g/cm3,含气量较低,半固态温度较佳。分别固定第一预定温度和第一预定质量以及搅拌相关参数(1500r.min-1,20s),以观察形核合金的预定比例的不同对半固态浆料质量的影响,具体如表3所示。表3添加不同重量的形核合金的半固态组织特性从表3的试验数据可以看出,加入形核合金的预定比例不同,所制备的半固态组织的圆整度和粒状晶尺寸有变化,在液态合金温度为670℃时,添加0.7-1.8%的形核合金时,制备的半固态浆料具有比较好的圆整度和粒状晶尺寸;添加1%的形核合金,制备的半固态浆料组织圆整度为0.89,粒状晶平均尺寸为38μm,半固态浆料质量较佳。固定第一预定质量4250g,第一预定温度为670℃,添加1%的形核合金,来观察不同搅拌转速下,分别搅拌20s的浆料质量情况,主要考察半固态组织的圆整度和粒状晶尺寸这两个方面。表4不同搅拌参数的制浆循环制备的浆料质量由表4中数据可以看到,搅拌速度越大,形成的半固态组织的粒状晶尺寸越小,粒状晶具有更好的圆整度;一般说来搅拌速度高,搅拌时间相对短,经过试验,不同转速下,搅拌时间在15-35s可以达到40-50%的固相率。由表3、表4可以看出,形核合金的预定比例以及搅拌转速均对半固态组织的粒状晶和圆整度有影响。表5每个连续的制浆循环制备的浆料的重量和温度从表5的试验数据可以看出,由于使用密封保温炉和密封制浆装置,保证了每个制浆循环所需的液态合重量稳定,在相同制浆参数下,液态合金重量偏差在100g以内,制备的半固态浆料温度偏差在5℃之内,半固态浆料固体含量恒定,保证了半固态浆料的质量。对比例下面就本发明的半固态制浆技术与传统半固态制浆技术制得的半固态浆料的质量作列表对比分析。表6由表6可以看到,本发明的半固态浆料制备方法,所制得的半固态浆料质量和稳定性更高,晶粒尺寸、圆整度等明显高于传统半固态制浆技术。综上,本发明的半固态浆料制备方法,通过控制每次制浆所需的合金液的质量和温度,通过控制密封制浆装置的形核合金的加入量、搅拌转速、搅拌时间、冷却介质的流量;并且每个压铸循环的半固态浆料重量由负压定量控制,搅拌不会卷气;形核金属使半固态浆料组织细化,粒状晶元整。从而制备出温度恒定、含气量低的半固态浆料,保证了半固态浆料的质量;使半固态产品可以提高t6热处理提高性能,产品合格率达到96%以上。半固态产品的性能得到提高,抗拉强度>290mpa,硬度达到hb120,可以做受力结构件,从而拓宽了半固态产品的应用领域。同时,密封定量制浆工艺开拓了半固态浆料制备的新思路,也推动了半固态压铸生产的进程。该高速旋转引晶制浆工艺方法制备的浆料,制浆过程连续、稳定,满足连续的半固态压铸生产,半固态浆料固相率稳定,半固态产品内部组织细小,半固态产品质量稳定。可以在连续压铸生产过程中生产出薄壁高导热壳体压铸件,制浆工艺时间与连续压铸生产节拍一致,不影响正常压铸生产效率,半固态生产节拍小于120s。所生产的薄壁结构产品减重30%,降低了生产材料费用,提高生产效益。需要指出的是,上面关于本发明的一种半固态浆料制备方法所包括的内容可以单独实施,或者以各种方式组合起来实施,而这些变型方式都在本发明的保护范围之内。最后应说明的是:以上实施例仅用以说明本发明的技术方案,而非对其限制。尽管参照前述实施例对本发明进行了详细的说明,本领域的普通技术人员应当理解:其依然可以对前述各实施例所记载的技术方案进行修改,或者对其中部分技术特征进行等同替换;而这些修改或者替换,并不使相应技术方案的本质脱离本发明各实施例技术方案的精神和范围。当前第1页12