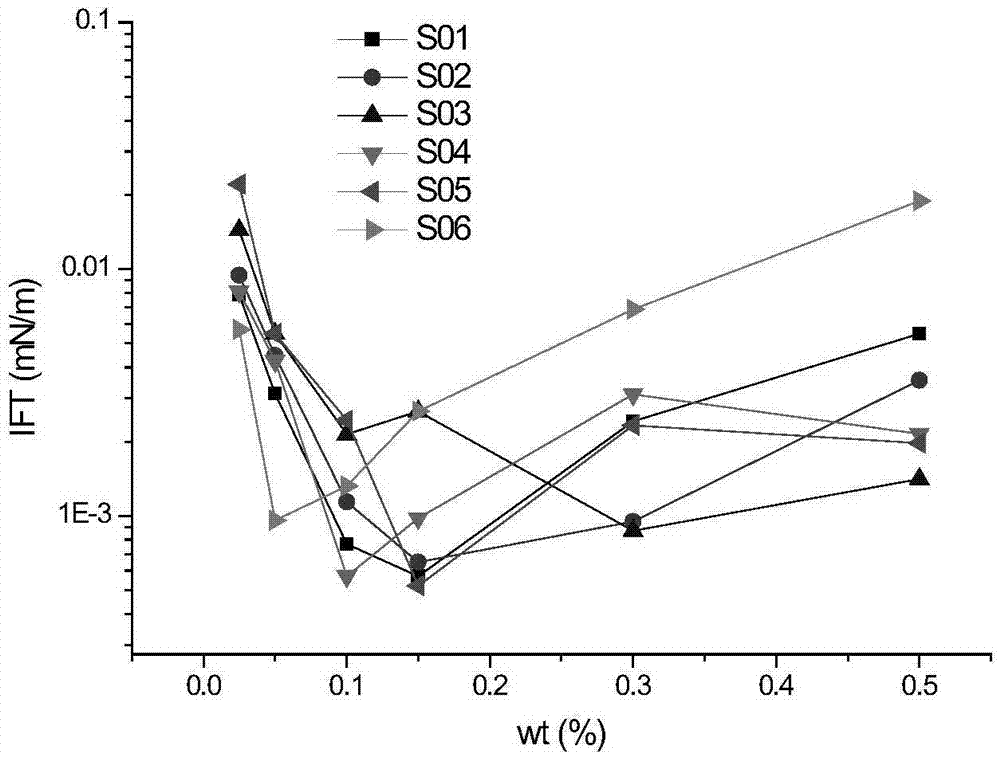
本发明涉及一种复合型表面活性剂及其低成本制备方法。
背景技术:
:表面活性剂作为化学驱的一个重要组成,根据其化学组成及分子结构不同,可以分为离子型与非离子型两大类。目前三次采油研究中所用表面活性剂的种类以阴离子型最多,其次是非离子型和两性离子型,应用最少的是阳离子型。美孚石油公司的专利US3927716、US4018281、US4216097相继报道了采用碱水驱油、表面活性剂或碱水驱油及使用两性离子表面活性剂驱油的结果,采用的两性离子表面活性剂为不同链长的羧酸或磺酸盐型甜菜碱表面活性剂,在总矿化62000~160000mg/L,钙镁离子1500~18000mg/L的模拟盐水中,对德克萨斯南部原油的界面张力达10-1~10-4mN/m。使用阳离子表面活性剂的亦有报道,如中国专利CN1528853、CN1817431、CN1066137等相继报道了双酰胺型阳离子型、含氟阳离子型及含吡啶基阳离子双子表面活性剂,但由于阳离子具有吸附损耗大、成本高等缺点,限制了其在油田现场的使用。不同类型表面活性剂相互复配后往往可以克服单一表面活性剂的缺点,发挥各组分的优点,从而赋予复合表面活性剂更加优越的性能。中国专利CN1458219A公开了一种三次采油应用的表面活性剂/聚合物二元超低界面张力复合驱配方,其中使用的表面活性剂是石油磺酸盐或以石油磺酸盐为主剂加稀释剂和其它表面活性剂复配的复合表面活性剂,其组份的重量百分比为石油磺酸盐50~100%,烷基磺酸盐0~50%,羧酸盐0~50%,烷基芳基磺酸盐0~35%,低碳醇0~20%,该表面活性剂体系过于复杂。美国德克萨斯大学的专利US8211837报道了采用简单廉价的线性醇在高温下催化二聚反应得到支链化的长碳醇,与环氧丙烷、环氧乙烷聚合后进行硫酸酯化反应,相对于昂贵的磺酸盐型表面活性剂,低成本合成了大亲水基聚醚硫酸盐表面活性剂,由于大亲水基团的存在,从而使得该硫酸盐表面活性剂在碱性条件下高温稳定性能优良,0.3%的支链醇聚醚硫酸盐(C32-7PO-6EO硫酸盐)与0.3%的内烯烃磺酸盐(C20~24IOS)盐水溶液在85℃与相同量的原油混合,其增溶参数为14。美孚石油公司的专利US4370243报道了采用油溶性的醇、磺酸甜菜碱及季铵 盐组成的驱油体系,该体系既可起到表面活性剂的作用,也可起到流度控制剂的作用,其中季铵盐为亲油基碳链长为16~20的阳离子表面活性剂,采用2%的十八烷基二羟乙基丙基磺酸盐甜菜碱与1.0%的正己醇作为驱油剂,注入1.9PV后,原油即可100%驱出,但表面活性剂的吸附损耗较大达到6mg/g,在此基础上加入价格相对低廉的2.0%四乙基溴化铵作为牺牲剂以降低表面活性剂的吸附量。国外研究使用的表面活性剂由于使用量大、成本高,作为驱油剂在实际应用中受到了一定的限制。阴阳离子复配表面活性剂亦是学者们热衷研究的课题。由于两者接近等比例混合时其水溶液容易形成沉淀,从而导致阴阳离子表面活性剂混合体系在应用中收到限制,如北京大学化学与分子工程学院赵国玺等(见《日用化学工业》1997年第2期,1~3)研究认为阴阳离子表面活性剂混合体系普遍具有浊点现象,显示非离子表面活性剂的特点,阎云等(见《物理化学学报》2002年第9期,830~834)研究了规则溶液理论应用于bola型两亲分子[(Me)3N+(CH2)6OC6H4O(CH2)6N+(Me)3]2Br-与异电性传统表面活性剂十二烷基硫酸钠(SDS)的相互作用,bola分子与SDS混合体系中的协同作用主要是由亲水基之间的静电相互作用产生的,而bola分子结构中疏水部分对相互作用没有显著影响,中国石化胜利油田分公司曹绪龙(见《物理化学学报》2014年第7期,1297~1302)研究了阴阳离子表面活性剂混合体系对原油的乳化及增黏行为,对油水体积比、浓度、温度、pH值、离子强度对乳化增黏的影响进行了系统的研究,得到了具有最佳增黏效果的配方体系,与原油黏度相比,实现了80倍左右的黏度上升。国内外研究结果表明,阴阳离子复配表面活性剂具有极高的表界面活性,因而具有非常广阔的应用前景。但由于阳离子季铵盐表面活性剂价格较高,高纯度的阴离子羧酸盐表面活性剂往往需经过复杂的提纯步骤才能得到,从而大大增加了复配表面活性剂的制备成本。采用烷基醇聚醚与卤代羧酸酯在过量碱金属氢氧化物或碱金属醇盐催化下生成聚醚羧酸酯,无需分离直接进行皂化反应得到聚醚羧酸盐,加入所需量的阳离子水或低碳醇水溶混合,体系中的低碳醇作为助剂可以在油水两相分配,改善油相和水相的性质,有利于油水界面张力的而降低和微乳液的形成,生成的无机盐对界面性能有促进作用亦无需去除,可能过量的碱金属氢氧化物还可以中和原油中的酸性物质形成皂进一步提高表面活性剂对原油的增溶能力,提高复合表面活性剂的洗油效率。本发明所述的正是这种在油藏条件下结构稳定的阳离子与阴离子表面活性剂形成的复合型表面活性剂及其低成本制备方法。技术实现要素:本发明所要解决的技术问题之一是现有技术中作为驱油剂体系主要组成的表面活性剂存在对原油增溶能力差、界面活性低的问题,提供一种新的复合型表面活性剂。以此复 合型表面活性剂的水溶液,在0.04~4wt%的浓度范围内能很好乳化原油,增溶参数为2~25,油水界面张力可达10-3~10-4mN/m,从而有效提高了原油驱油效率,具有很好的提高采收率应用前景。本发明所要解决的技术问题之二是提供一种上述技术问题之一所述复合型表面活性剂的低成本制备方法。本发明所要解决的技术问题之三是提供一种解决上述技术问题之一所述复合型表面活性剂的应用。为了解决上述技术问题之一,本发明采用的技术方案如下:一种复合型表面活性剂,以摩尔份数计包括以下组分:(1)0.01~1摩尔的阳离子表面活性剂;(2)1摩尔的阴离子表面活性剂;其中,(1)组分的分子通式为:式(I)中,R1为C4~C32的烷基,R2、R3独立选自(CH2)dOH或(CH2)eCH3中的一种;a=1、b=0,R4选自(CH2)dOH、(CH2)eCH3中的一种,d=2~4中的任一整数,e=0~5中的任一整数;或a=1、b=1,R4选自CH2(CH2)fCH2,f=0~5中的任一整数;Yk-为负电荷数为k的阴离子;(2)组分的分子通式为:R5X[(CH2CH2O)m1(CH3CHCH2O)n(CH2CH2O)m2R6COOM]j,式(II);式(II)中:R5为C8~C30的直链或支链的饱和及不饱和烷基,m1、m2为丙氧基团PO的加合数,m1=0~50、m2=0~50,n为乙氧基团EO的加合数,n=0~100,R6为C1~C5的亚烷基或羟基取代亚烷基,M选自氢、碱金属或者由式NR7(R8)(R9)(R10)所示基团中的至少一种,R7、R8、R9、R10为独立选自H、(CH2)dOH或(CH2)eCH3中的一种,d=2~4、e=0~5中的任一整数;X为杂原子,j为羧酸根的个数,j=1或2。上述技术方案中,所述X优选为氧原子或氮原子。上述技术方案中,所述X优选为氧原子,优选j=1。上述技术方案中,所述X优选为氮原子,优选j=2,所述(2)组分的结构式如式(III) 所示:式(III)中,R11为C8~C30的直链或支链的饱和及不饱和烷基;r1、r2、r3或r4独立选自0~50,但r1和r2、r3和r4不能同时为0;s1和s2独立选自0~100,但s1和s2不能同时为0;R12和R′12独立选自C1~C5的亚烷基或羟基取代亚烷基中的至少一种;Z和Z′独立选自COOM或氢中的任意一种。上述技术方案中,R1优选为C8~C24的烷基,R2、R3优选为甲基、乙基、羟乙基或苄基中的一种,。上述技术方案中,R5和R11优选为C12~C24的烷基。上述技术方案中,R6优选为C1~C3的亚烷基。上述技术方案中,X优选为O。上述技术方案中,优选d=2,e=0~1,f=1、2或4。上述技术方案中,优选m1=0~10,m2=0~10,n=0~20,且m1+m2与n不同时为零;r1+r2=0~10,r3+r4=0~10,s1+s2=0~20,且r1+r2+r3+r4与s1+s2不同时为零。上述技术方案中,所述复合型表面活性剂,以摩尔份数计,优选还包括以下组分:(3)1~20摩尔的短碳链醇;(4)1~10摩尔的盐;其中,短碳链醇选自C1~C8的脂肪醇;盐选自金属卤化物、羟基取代的羧酸盐中至少一种。上述技术方案中,优选短碳链醇为C1~C5的脂肪醇。上述技术方案中,金属卤化物优选为碱金属卤化物,进一步优选为氯化钠、氯化钾、溴化钠、溴化钾中的一种;羟基取代的羧酸盐优选为羟基乙酸钠、羟基乙酸钾中的一种。上述技术方案中,所述阳离子表面活性剂与阴离子表面活性剂的摩尔比优选为(0.05~0.95)∶1;阴离子表面活性剂与短碳链醇与盐的摩尔比优选为1∶(2~15):(1~5)。上述技术方案中,式(1)表示的阳离子表面活性剂的核心在于结构中的阳离子部分,Yk-没有特别限制,只要能够使与式(1)中的阳离子部分构成电中性体系的阴离子均适用本发明。简单阴离子的例子例如,Yk-可以是k=1的无机阴离子(例如氯离子、溴离子或氢氧根离子、磷酸二氢根等)、k=1的有机阴离子(例如醋酸根等一元羧酸根),可以是 k=2的无机阴离子(例如硫酸根、磷酸氢二根等)、k=2的有机阴离子(例如酒石酸根、邻苯二甲酸根、马来酸根);还可以是k>2的多价无机或有机阴离子,例如磷酸根、柠檬酸根。除了上述简单阴离子以外,还包括多聚阴离子(例如三聚磷酸根、多聚磷酸根等)、聚合阴离子(例如聚丙烯酸根)等。但至少从制备方法简便程度考虑,Yk-优选氯离子、溴离子氢氧根或乙酸根离子。在Yk-为氯离子、溴离子或氢氧根离子且a=1、b=0的情形下,式(1)表示的表面活性剂可以从市售渠道获得也可以通过本领域常规技术合成得到;在Yk-氯离子、溴离子或氢氧根离子之外的阳离子表面活性剂,可以通过本领域常规技术合成得到,例如至少也可以通过Yk-为氢氧根离子的阳离子表面活性剂经过相应的酸中和至所需程度得到式(1)所式的阳离子表面活性剂;Yk-为氢氧根离子的阳离子表面活性剂,例如可以通过Yk-氯离子、溴离子的阳离子表面活性剂与氧化银反应得到,再例如还可以通过Yk-氯离子、溴离子的阳离子表面活性剂用强碱性氢氧型阴离子交换树脂处理得到。本发明复合型表面活性剂,还可以包括本领域常用的驱油组分,例如驱油用聚合物,驱油用泡沫剂,驱油用矿物质(例如氯化钠、氯化钾)、碱性物质(例如氢氧化钠、碳酸钠、碳酸氢钠、二乙醇胺和三乙醇胺等小分子有机胺),有机小分子助剂包括短链脂肪醇、低碳链酮、DMSO等。本发明复合型表面活性剂关键有效成分是(1)和(2),本领域技术人员知道,为了便于运输和贮存或现场使用等方面考虑,可以采用各种供应形式,例如不含水的固态形式,或者含水的膏状形式,或者水溶液形式;水溶液形式包括用水配成浓缩液的形式,直接配成现场驱油所需浓度的溶液形式,例如以重量计关键有效成分含量为0.005~0.6wt%的溶液是现场驱油较为适宜的形式;其中,对水没有特殊要求,可以是去离子水,还可以是含无机矿物质的水,而含无机矿物质的水可以是自来水、油田地层水或油田注入水。为解决上述技术问题之二,本发明所采用的技术方案如下:上述技术问题之一所述的复合型表面活性剂的低成本制备方法,包括以下步骤:(a)阳离子表面活性剂的制备:当a=1,b=0时,阳离子表面活性剂为单链季铵盐,可通过市售得到;当a=1,b=1时,阳离子表面活性剂为双链季铵盐,其制备过程为:将脂肪胺与Y01CH2(CH2)fCH2Y02按所需摩尔比在短碳链醇水溶液中混合,升温至回流反应2~100小时,得到所需的阳离子表面活性剂水溶液或短碳链醇水溶液;其中,短碳链醇水溶液的浓度为0~100wt%,短碳链醇选自C1~C5的脂肪醇,Y01、Y02选自氯、溴或碘,f=0~2;(b)阴离子表面活性剂的制备:①在碱性催化剂存在下,烷基醇或烷基胺依次与所需量环氧乙烷、环氧丙烷、环氧乙烷反应得到烷基醇聚醚;②将步骤(b)①得到的产物与Y03R6COOR01以及碱金属氢氧化物或碱金属醇盐以摩尔比1:(1~5):(1~10)混合,搅拌下于反应温度50~120℃反应3~15小时,无需分离,继续加入水进行皂化反应,回流1~10小时后,加入步骤(a)得到的阳离子表面活性剂水溶液或短碳链醇水溶液,升温至40~100℃搅拌1~5小时,得到所需的复合型表面活性剂;其中,Y03选自氯、溴或碘,R6选自C1~C5的亚烷基或羟基取代亚烷基中的至少一种,R01选自C1~C8的烷基。所述制备方法反应方程式如下:上述技术方案中,步骤(b)①所述的反应温度优选为120~160℃,压力优选为0.30~0.60MPa表压,碱性催化剂优选为氢氧化钾或无水碳酸钾中的至少一种;步骤(b)②所述碱金属氢氧化物优选为氢氧化钾或氢氧化钠中的至少一种,烷基醇或烷基胺聚醚与Y03R6COOR01以及碱金属氢氧化物或碱金属醇盐的摩尔比优选为1:(1~3):(2~6),Y03优选自氯或溴中的一种,R6优选自C1~C3的亚烷基,R01优选为C1~C4的烷基,j优选为1。只要进行了步骤(b)的反应,本领域技术人员不需要付出创造性劳动就能够分离、纯化得到所述复合表面活性剂的各种产品形式。例如,为了得到式(2)所示阴离子表面活性剂当M为由式NR7(R8)(R9)(R10)所示基团时的产品,可进一步进行包括步骤(c)的反应:(c)在步骤(b)得到的反应混合物中加入酸调节水相的pH=1~3,用与所需的式NR7(R8)(R9)(R10)所示基团相应的碱中和即可。上述技术方案中所述所需的式NR7(R8)(R9)(R10)所示基团相应的碱,例如与NR7(R8)(R9)(R10)所述基团相应的碱选自氨、乙醇胺、二乙醇胺、三乙醇胺、三乙胺等。Y03R01Z01的例子有但不限于氯乙酸酯(例如氯乙酸乙酯)、溴乙酸酯(例如溴乙酸乙酯)等。为了解决上述技术问题之三,本发明采取的技术方案如下:一种上述技术方案中任一所述的复合型表面活性剂在油田驱油中的应用。上述技术方案中,所述复合型表面活性剂可以根据现有技术加以应用,可以单独使用,也可以与油田常用助剂复配使用;作为优选方案:所述应用优选高温高盐油藏的地层盐水的总矿化度20000~35000mg/L,其中Ca2+为500~1500mg/L、Mg2+为100~500mg/L、HCO3-为5~40mg/L;原油黏度为5~15mPa.s;地层温度为75~90℃。本发明制备的阴离子与阳离子表面活性剂形成的阴阳体系表面活性剂,由于阴离子与阳离子表面活性剂复配后,即可呈现出表面活性的增加、临界胶束浓度的下降、增溶效应等优点。这是因为阴离子表面活性剂中的亲水头基呈负电性与阳离子表面活性剂中铵离子正电荷存在强烈的静电作用,促进了两种带不同电荷表面活性剂离子间的缔合,且二者的疏水基碳氢链间还有一定的疏水作用,促使不同表面活性剂分子采取更加紧密的排列方式,因而在溶液中很容易形成胶束,产生比单一表面活性剂更高的表面活性和低的临界胶束浓度,同时阴离子表面活性剂中的非离子聚醚基团的引入既可增加阴阳体系表面活性剂的亲水性,同时因为位阻效应减弱了复配剂之间的强烈相互作用以避免表面活性剂的液晶化、沉淀等现象的发生。因此,该表面活性剂具有优异的乳化原油的能力和界面活性,可解决油田现场使用过程中表面活性剂对原油增溶能力差而无法达到很好的洗油效率,同时超高的界面活性可以保证低浓度表面活性剂仍可保持超低的油水界面张力,从而能够提高驱油效率。另外,本发明采用的复合表面活性剂的低成本制备方法,由于高纯度阴离子和阳离子表面活性剂价格较高,特别是得到高含量阴非离子羧酸盐表面活性剂往往需经过萃取、柱层析等复杂的提纯步骤才能得到,从而大大增加了复配表面活性剂的制备成本。采用烷基醇与卤代羧酸酯在过量碱金属氢氧化物或碱金属醇盐催化下生成聚醚羧酸酯,无需分离直接进行皂化反应得到聚醚羧酸盐,加入所需量的阳离子水或低碳醇水溶混合,体系中的低碳醇可与表面活性剂在界面形成复合膜,同时低碳醇还可分配至油相和水相改善两相性质,从而有利于降低界面张力和形成微乳液,增加驱油体系对原油的增溶能力,生成的无机盐对界面性能亦有促进作用无需去除,可能过量的碱金属氢氧化物还可以中和原油中的酸性物质形成皂进一步提高表面活性剂对原油的增溶能力,提高复合表面活性剂的洗 油效率,实现了表面活性剂的绿色生产。本发明中涉及到复合表面活性剂含量或者浓度的场合,均指含有上述技术方案中分子通式(1)和分子通式(2)组份的总含量或总浓度。采用本发明制备的复合体系表面活性剂,以质量百分比计,用量为0.005~0.3wt%的范围内,可用于地层温度为75~90℃、矿化度为20000~35000毫克/升、Mg2++Ca2+为600~2000毫克/升、HCO3-为5~40mg/L的胜利油田现场水和原油,测定了该表面活性剂水溶液与原油之间的动态界面张力值,可达10-2~10-4mN/m的低界面张力,静态吸附量小于2mg/g,4wt%表面活性剂能很好乳化原油,最大增溶参数为23.5,取得了较好的技术效果。附图说明图1为0.15%和0.025%的S01在不同浓度氯化钠盐水中对胜利油田原油的油水界面张力图。图2为不同浓度S01~S06的6#模拟盐水溶液对胜利油田原油的油水界面张力图。图3为90℃时,0.15%的S01~S06的6#模拟盐水溶液经不同老化时间后对胜利油田原油的油水界面张力图。下面通过实施例对本发明作进一步阐述。具体实施方式【实施例1】(a)双子阳离子季铵盐表面活性剂(18-4-18,2Br-)的制备C18H37(CH2CH2OH)2N+(CH2)4N+(CH2CH2OH)2C18H37.2Br-将十八烷基二羟乙基叔胺357克(1摩尔)与108克(0.5摩尔)1,4-二溴丁烷、30wt%乙醇水溶液1220克混合于配有机械搅拌、温度计和回流冷凝管的5000毫升的四口烧瓶内,加热至回流反应7小时,停止回流。取10克反应液蒸除乙醇,以四苯硼钠标准溶液滴定双子阳离子表面活性剂(18-4-18,2Br-)的含量为98.9%,其余样品不处理,备用。(b)阴离子及复合表面活性剂S01的制备RO(CH2CH2O)2(CHCH3CH2O)8(CH2CH2O)6CH2COOK其中,R的碳链分布为:C145.53%、C1662.93%、C1831.54%。(1)向装有搅拌装置的2L压力反应器中加入248克(1摩尔)混合醇(C14~18)、5.6克氢氧化钾,加热至80~90℃时,开启真空系统,在高真空下脱水1小时,然后用氮气置换3~4次,将体系反应温度调至140℃缓缓通入90.2克(2.05摩尔)环氧乙烷,再于150℃缓缓通入469.8克(8.1摩尔)环氧丙烷,控制压力≤0.60MPa,待环氧丙烷反应结束后再将温度调至140℃缓缓通入266.2克(6.05摩尔)环氧乙烷,控制压力≤0.40MPa。反应结束后,降温至90℃,真空除去低沸物,冷却后中和、脱水,得混合醇(C14~18)聚氧乙烯(2)聚氧丙烯(8)聚氧乙烯(6)醚1050.2克,收率98.7%。(2)于配有机械搅拌、温度计和回流冷凝管的5000毫升的反应瓶内,搅拌下加入步骤(b)(1)合成的混合醇(C14~18)聚氧乙烯(2)聚氧丙烯(8)聚氧乙烯(6)醚532克(0.5摩尔)和61.6克(1.1摩尔)氢氧化钾,缓慢滴入91.9克(0.55摩尔)溴乙酸乙酯,控制反应温度75℃反应5小时,冷却后加入580克水,继续加热至回流反应4小时。冷却至40℃,加入含120.3克(0.13摩尔)步骤(a)合成双子阳离子季铵盐表面活性剂(18-4-18,2Br-)的乙醇水混合物,继续于40℃搅拌4小时,得到所需的复合表面活性剂S01,以质量百分比计,阴阳表面活性剂41.05%,溴化钾3.12%,羟乙酸钾0.36%,乙醇7.19%,水48.28%。【实施例2】(a)同【实施例1】。(b)阴离子及复合表面活性剂S02的制备RO(CH2CH2O)2(CHCH3CH2O)8(CH2CH2O)6CH2COOH.N(C2H5)3其中,R的碳链分布为:C145.53%、C1662.93%、C1831.54%。(2)于配有机械搅拌、温度计和回流冷凝管的5000毫升的反应瓶内,搅拌下加入步骤(b)(1)合成的混合醇(C14~18)聚氧乙烯(2)聚氧丙烯(8)聚氧乙烯(6)醚532克(0.5摩尔)和61.6克(1.1摩尔)氢氧化钾,缓慢滴入91.9克(0.55摩尔)溴乙酸乙酯,控制反应温度90℃反应5小时,冷却后加入580克水,继续加热至回流反应4小时,冷却至30℃加入浓盐酸调节pH=3,加入55.5克(0.55摩尔)的三乙胺中和生成的羧酸。同【实施例1】加入阳离子表面活性剂,得到所需的复合表面活性剂S02,以质量百分比计,阴阳表面活性剂41.57%,混合物无机盐(溴化钾+氯化钾)5.46%,羟乙酸钾0.33%,乙醇6.69%,水45.95%。【实施例3】(a)阳离子表面活性剂为十二烷基二甲基苄基氯化铵,市售商品,含量45%,溶剂为水。(b)阴离子及复合表面活性剂S03的制备RO(CHCH3CH2O)12(CH2CH2O)2CH2COONa其中,R=iso-C13H27。(1)向装有搅拌装置的压力反应器中加入200克(1摩尔)异构十三醇、4克氢氧化钾和2.6克无水碳酸钾,加热至反应温度80~90℃时,开启真空系统,在高真空下脱水1小时,然后用氮气置换3~4次,将体系反应温度调至150℃缓缓通入701.8克(12.1摩尔)环氧丙烷,控制压力≤0.50MPa,待环氧丙烷反应结束后,降温,于130℃缓缓通入88.0克(2.0摩尔)环氧乙烷,控制压力≤0.60MPa。反应结束后,同【实施例1】后处理,得异构十三醇聚氧丙烯(12)聚氧乙烯(2)醚955.5克,收率97.1%。(2)于配有机械搅拌、温度计和回流冷凝管的5000毫升的反应瓶内,搅拌下加入步骤(b)(1)合成的异构十三醇聚氧丙烯(12)聚氧乙烯(2)醚492克(0.5摩尔)和60.0克(1.5摩尔)氢氧化钠,缓慢滴入79.6克(0.65摩尔)氯乙酸乙酯,控制反应温度90℃反应4小时,冷却后加入600克水及200克95%乙醇,继续加热至回流反应5小时。冷却至40℃,加入含85.0克(0.25摩尔)十二烷基二甲基苄基氯化铵的水溶液,继续于40℃搅拌4小时,得到所需的复合表面活性剂S03,以质量百分比计,阴阳表面活性剂38.02%,氯化钠1.81%,羟乙酸钠0.9%,氢氧化钠0.49%,乙醇13.57%,水45.21%。【实施例4】(a)阳离子表面活性剂为二十二烷基三甲基氯化铵(罗地亚公司,含量98.5%)。(b)阴离子及复合表面活性剂S04的制备C22H45O(CH2CH2O)8(CHCH3CH2O)4(CH2CH2O)2CH2COONa(1)向装有搅拌装置的2L压力反应器中加入326克(1摩尔)二十二醇、5克氢氧化钾和5.5克无水碳酸钾,,加热至80~90℃时,开启真空系统,在高真空下脱水1小时,然后用氮气置换3~4次,将体系反应温度调至140℃缓缓通入354.2克(8.05摩尔)环氧乙烷,再于150℃缓缓通入234.9克(4.05摩尔)环氧丙烷,控制压力≤0.60MPa,待环氧丙烷反应结束后再将温度调至140℃缓缓通入88.0克(2.0摩尔)环氧乙烷,控制压力≤0.40MPa。反应结束后,降温至90℃,真空除去低沸物,冷却后中和、脱水,得二十二醇聚氧乙烯(8)聚氧丙烯(4)聚氧乙烯(2)醚979.0克,收率98.1%。(2)于配有机械搅拌、温度计和回流冷凝管的2000毫升的反应瓶内,搅拌下加入步骤(b)(1)合成的二十二醇聚氧乙烯(8)聚氧丙烯(4)聚氧乙烯(2)醚499克(0.5摩尔)和60.0克(1.5摩尔)氢氧化钠,缓慢滴入102.4克(0.75摩尔)氯乙酸异丙酯,控制反应温度100℃反应3小时,冷却后加入300克水及300克95%乙醇,继续加热至回流反应3小时。冷却至40℃,加入20.2克(0.05摩尔)二十二烷基三甲基氯化铵,继续于40℃搅拌5小时,得到所需的复合表面活性剂S04,以质量百分比计,阴阳表面活性剂43.78%,氯化钠2.25%,羟乙酸钠1.98%,混合醇(乙醇+异丙醇)26.18%,水25.81%。【实施例5】(a)阳离子表面活性剂为十八烷基三甲基溴化铵(OTAB,罗地亚公司,含量98.5%)。(b)阴离子及复合表面活性剂S05的制备RO(CH2CH2O)4CH2COOK其中,R的碳链分布为:C145.53%、C1662.93%、C1831.54%。(1)向装有搅拌装置的2L压力反应器中加入248克(1摩尔)混合醇(C14~18)、3.8克氢氧化钾,加热至80~90℃时,开启真空系统,在高真空下脱水1小时,然后用氮气置换3~4次,将体系反应温度调至140℃缓缓通入178.2克(4.05摩尔)环氧乙烷,控制压力≤0.60MPa反应结束后,降温至90℃,真空除去低沸物,冷却后中和、脱水,得混合醇(C14~18)聚氧乙烯(4)醚421.0克,收率99.3%。(2)于配有机械搅拌、温度计和回流冷凝管的2000毫升的反应瓶内,搅拌下加入步骤(b)(1)合成的混合醇(C14~18)聚氧乙烯(4)260克(0.5摩尔)和128.8克(2.3摩尔)氢氧化钾,缓慢滴入150.5克(1.0摩尔)氯乙酸正丁酯,控制反应温度110℃反应5小时,冷却后加入400克水及50克95%乙醇,继续加热至回流反应3小时。冷却至40℃,加入188.2克(0.48摩尔)十八烷基三甲基溴化铵,继续于45℃搅拌3小时,得到所需的复合表面活性剂S05,以质量百分比计,阴阳表面活性剂41.78%,氯化钾3.15%,羟乙酸钾5.38%,氢氧化钾1.51%,混合醇(乙醇+正丁醇)11.01%,水37.17%。【实施例6】(a)双子阳离子季铵盐表面活性剂(10-6-10,2Cl-)的制备C10H21(C2H5)2N+(CH2)6N+(C2H5)2C10H21.2CI-将癸基二乙基叔胺213.0克(1摩尔)与77.5克(0.5摩尔)1,6-二氯己烷、异丙醇600克混合于配有机械搅拌、温度计和回流冷凝管的2000毫升的四口烧瓶内,加热至回流反应60小时,停止回流。取10g反应液蒸除异丙醇,以四苯硼钠标准溶液滴定,双子阳离子表面活性剂(10-6-10,2Cl-)的含量为96.5%,其余样品不处理,备用。(b)阴离子及复配表面活性剂S06的制备C13H27O(CHCH3CH2O)15CH2COONa(1)向装有搅拌装置的2L压力反应器中加入克200克(1摩尔)异构十三醇、4.6克氢氧化钾,加热至80~90℃时,开启真空系统,在高真空下脱水1小时,然后用氮气置换3~4次,将体系反应温度调至150℃缓缓通入875.8克(15.1摩尔)环氧丙烷,控制压力≤0.60MPa反应结束后,降温至90℃,真空除去低沸物,冷却后中和、脱水,得异构十三醇聚氧丙烯(4)醚1036.8克,收率96.9%。(2)于配有机械搅拌、温度计和回流冷凝管的5000毫升的反应瓶内,搅拌下加入步骤(b)(1)合成的异构十三醇聚氧丙烯(4)醚535克(0.5摩尔)和48.0克(1.2摩尔)氢氧化钠,缓慢滴入108.6克(0.6摩尔)溴乙酸正丙酯,控制反应温度90℃反应4小时,冷却后加入700克水及100克95%乙醇,继续加热至回流反应3小时。冷却至40℃,加入含55.2克(0.095摩尔)步骤(a)制备的双子阳离子季铵盐表面活性剂(10-6-10,2Cl-)的异丙醇混合物,继续于45℃搅拌3小时,得到所需的复合表面活性剂S06,以质量百分比计,阴阳表面活性剂38.04%,溴化钠3.06%,羟乙酸钠0.59%,混合醇(乙醇+正丙醇+异丙醇)14.78%,水43.53%。【实施例7】配制不同盐含量的模拟水,组成见表1所示。油水界面张力测定用原油来至胜利油田,经脱水后使用,原油黏度为35mPa.s。油水界面张力(IFT)由美国德克萨斯大学生产的TX500型旋转滴界面张力仪测定。将表面活性剂S01以1#~5#模拟水溶解,测定表面活性剂溶液对原油的油水界面张力,结果见图1所示。配制表面活性剂S01~S06的6#模拟盐水溶液,测定不同浓度表面活性剂溶液对原油的油水界面张力,结果见图2所示。将0.15wt%的S01~S06的6#模拟盐水溶液装入20毫升安碚瓶中,密封后放入90℃的烘箱内,测定不同老化时间后表面活性剂模拟盐水对与原油的油水界面张力,发现老化 后油水界面张力仍可保持10-3~10-4mN/m的超低值,见图3所示。【实施例8】静态吸附试验主要是探索表面活性剂在地层岩心上的吸附损耗量,以探索实施例合成的表面活性剂在提高原油采收率现场应用的可能性。实验过程为:表面活性剂的6#模拟盐水溶液3g与1g含黏土的石英砂混合后,于90℃震荡24h,冷却后离心分离,取上层清液,采用高效液相色谱(HPLC)分析仪测定表面活性剂阴离子和阳离子的浓度,计算表面活性剂的吸附量,单位mg/g,结果见表2所示。其中,含黏土的石英砂组成为:10wt%高岭土+90wt%100~200目石英砂。【实施例9】相态实验可以很好反映出表面活性剂对原油的增溶能力,得到表面活性剂对原油的增溶参数和表面活性剂的最佳盐含量。实验过程为:首先配制4.0wt%S01不同盐含量的水溶液,取2.5mL加入一端封口的5mL移液管中,再加入2.5mL【实施例7】使用的脱水原油(油水体积比=1:1),上端分封口后,记录起始的油水体积,充分混合后,放入不锈钢密封容器中置于90℃烘箱恒温静置,直到各相体积不变为至,记录各相体积,计算表面活性剂对原油的增溶参数,增溶参数最大时的盐度为S01的最佳盐含量。结果见表3所示。S01的最佳盐含量为20000mg/L,增溶参数为23.5。【比较例1】分别配制0.15%【实施例1】、【实施例2】合成的双子阳离子季铵盐表面活性剂(18-4-18,2Br-)(S07)、混合醇(C14~18)聚氧乙烯(2)聚氧丙烯(8)聚氧乙烯(6)醚乙酸钾阴离子表面活性剂(S08)、混合醇(C14~18)聚氧乙烯(2)聚氧丙烯(8)聚氧乙烯(6)醚乙酸三乙胺阴离子表面活性剂(S09)的6#模拟水溶液,同【实施例7】和【实施例8】测定油水界面张力和吸附量,结果见表4所示。【比较例2】分别配制0.15%【实施例4】的二十二烷基三甲基氯化铵(S10)、二十二醇聚氧乙烯(8)聚氧丙烯(4)聚氧乙烯(2)醚乙酸钠阴离子表面活性剂(S11)6#模拟水溶液,同【实施例7】和【实施例8】测定油水界面张力和吸附量,结果见表4所示。【比较例3】同【实施例1】,不同之处在于,与环氧丙烷和环氧乙烷不是先后分步进行反应的,而是混合后一步进行反应,即在110~150℃缓缓通入466.9克(8.05摩尔)环氧丙烷和354.2克(8.05摩尔)环氧乙烷混合物,控制压力≤0.60MPa,其余相同,得到S12,同【实施例7】和【实施例8】进行界面性能测定和吸附量,结果见表4所示。【比较例4】同【实施例3】,不同之处在于,与环氧丙烷和环氧乙烷不是先后分步进行反应的,而是将混合后一步进行反应,即在110~150℃缓缓通入701.8克(12.1摩尔)环氧丙烷和88.0克(2.0摩尔)环氧乙烷混合物,控制压力≤0.60MPa,其余相同,得到S13,同【实施例7】和【实施例8】进行界面性能测定和吸附量,结果见表4所示。【比较例5】同【实施例1】,不同之处在于,(a)步骤中反应结束时,减压蒸除乙醇,得到阳离子表面活性剂产品;(b)步骤中皂化反应结束后,减压蒸除反应产生的乙醇,以20wt%盐酸调节pH=1-2,分去水相,有机相以30%氢氧化钾调节至pH=12-13。将阳离子和阴离子按同【实施例1】比例混合,得到所需的复合表面活性剂S14,同【实施例7】和【实施例8】进行界面性能测定和吸附量,结果见表4所示。表1表2表面活性剂吸附量mg/gS011.63S021.29S031.45S041.28S050.91S061.33表3水NaCl(mg/L)增溶参数二次蒸馏水02.31#50009.22#1000012.73#2000023.5.4#3000017.55#500008.17#800005.38#1000001.19#1500000表4表面活性剂浓度wt%模拟水IFT(mN/m)吸附量(mg/g)S010.156#0.000571.63S020.156#0.000651.29S070.156#0.085614.12S080.156#0.016520.95S090.156#0.017530.72S030.156#0.002651.45S040.156#0.000981.28S100.156#0.203333.77S110.156#0.024520.73S120.156#0.007411.79S130.156#0.008441.53S140.156#0.000851.74当前第1页1 2 3