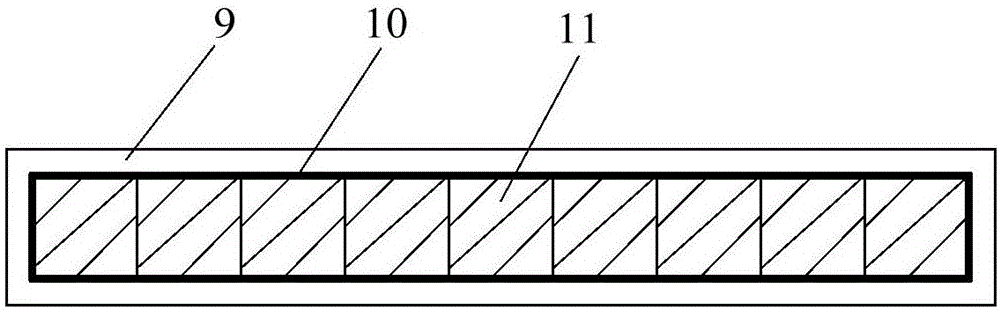
本发明涉及复合材料板材
技术领域:
,特别是一种用于复合材料板材成型的自加热平台。
背景技术:
:复合材料夹层结构由三部分组成,最外层是面板,主要承受弯曲变形引起的正应力,采用高强、高模量的材料制造,如层压的碳纤维或玻璃纤维布等;中间是芯材,为夹层结构提供足够的截面惯性矩,主要承受剪应力,常用蜂窝、泡沫、轻木等材料。面板和芯材之间是胶接层,通过树脂将两者粘接在一起,常用不饱和聚酯、乙烯基树脂、环氧树脂、酚醛树脂等。复合材料夹层结构是一种具有广阔发展前景的材料与结构形式,复合材料夹层结构的应用领域越来越广泛,可涉及军事设施、国防工程、车辆、舰船、建筑、桥梁等领域。在我国,复合材料夹层结构多以蜂窝为芯材,例如申请号为CN201220567532.X,发明名称为一种新型舞台活动板的专利,其公开了一种新型舞台活动板,包括有蜂窝芯材,在所述的蜂窝芯材上、下两面上分别粘贴有面板,所述的面板与蜂窝芯材之间设有粘接层,蜂窝芯材包括有若干个依次紧密连接且截面为正六边形的蜂窝单元体。再例如申请号为CN201420799397.0,发明名称为一种可连续制备蜂窝芯材的模具和装置,具体涉及一种可连续制备蜂窝芯材的模具及装置,并进一步公开了其使用方法。但蜂窝夹层结构的芯材与面板接触面积小,因此其粘结性能相对较弱,造成复合材料板材结构抗压和抗剪切能力差。技术实现要素:本发明要解决的技术问题是针对上述现有技术的不足,而提供一种用于复合材料板材成型的自加热平台。为解决上述技术问题,本发明采用的技术方案是:一种用于复合材料板材成型的自加热平台,包括:长方体框架结构的支撑装置,设置于支撑装置上呈长方形的钢化玻璃模板,设置于支撑装置上位于钢化玻璃模板下方的热辐射灯安装基座,热辐射灯安装基座上设置有多个热辐射灯,多个热辐射灯均与温控装置之间电连接,温控装置与电源连接;通过温控装置可以控制区域内多个热辐射灯的亮、灭,使得复合材料板材受热均匀,并且通过控制区域内多个热辐射灯的亮度及照射时间,可以控制加热温度及时间等因素。支撑装置长方体框架的四周、且位于热辐射灯安装基座与钢化玻璃模板之间围设有四块保温型透明有机玻璃板;设置于支撑装置上、位于钢化玻璃模板的上方罩设有保温透明型的有机玻璃罩,有机玻璃罩与钢化玻璃模板之间为可拆卸式连接,且连接处为活动密封连接;有机玻璃罩外设置有空气增压装置,用于复合材料板材成型过程中边加热边加压。所述支撑装置的支腿底部均设置有支撑活动脚轮。支撑装置长方体框架的上端设置有支撑梁,支撑梁位于钢化玻璃模板的下方,且钢化玻璃模板支撑于支撑梁上。支撑梁与钢化玻璃模板之间设置有橡胶板。热辐射灯安装基座平行于钢化玻璃模板设置在支撑装置上。本发明采用上述方案后具有如下技术效果:本发明所述用于复合材料板材成型的自加热平台,整个装置为全透明设计,通过使用高强度的钢化玻璃模板耐温、透明的特性,既保证钢化玻璃模板在低、中温下的平面度,同时可以观察到树脂的流动状况、复合材料面层与内部金属结构框的贴合程度,以及芯材发泡的过程,可以做到随时发现成型过程中出现的一些问题并及时解决,避免成品出现缺陷后再返工。本发明通过在长方体框架的四周、且位于热辐射灯安装基座与钢化玻璃模板之间围设四块保温型透明有机玻璃板作为保温装置,减少了热量的流失、缩短升温的时间、保证温度的恒定,同时采用透明的材质可以观察到成型时的面层树脂流动、浸润状态。本发明通过设置支撑活动脚轮,便于移动用于纤维复合板成型的自加热平台,同时利用支撑活动脚轮高度调节装置实现整个加热平台的水平调节,摆脱生产场地高低不平的限制。附图说明为了更清楚地说明本发明实施例或现有技术中的技术方案,下面将对实施例或现有技术描述中所需要使用的附图作简单地介绍,显而易见地,下面描述中的附图仅仅是本发明的一些实施例,对于本领域普通技术人员来讲,在不付出创造性劳动的前提下,还可以根据这些附图获得其他的附图。图1显示了本发明的整体结构。图2显示了一种增强型复合材料板材的结构。具体实施方式为使本发明的目的和技术方案更加清楚,下面将结合本发明实施例对本发明的技术方案进行清楚、完整地描述。显然,所描述的实施例是本发明的一部分实施例,而不是全部的实施例。基于所描述的本发明的实施例,本领域普通技术人员在无需创造性劳动的前提下所获得的所有其他实施例,都属于本发明保护的范围。如图2所示,一种增强型复合材料板材结构,由复合材料面层9、金属结构框10和芯材11组成,金属结构框整体呈长方体形,长方体形的金属结构框外表至少包覆一层复合材料面层,金属结构框内部沿其厚度方向平行设置有多个与金属结构框相同材质的加强筋,金属结构框内部填充芯材,芯材为泡沫材质。优选地,所述金属结构框的材质为不锈钢。优选地,本发明增强型复合材料板材结构中芯材为硬质聚氨酯泡沫,复合材料面层可以为无碱玻璃纤维复合材料,也可以为添加型阻燃不饱和聚酯树脂复合材料。不饱和聚酯树脂(UP)为二元醇与不饱和二元酸在高温下缩聚而成,其主链中含有可聚合双键,在引发剂作用下与各类烯类单体共聚,得到体型结构的热固型塑料。但是这类塑料易燃,因此本发明采用将不饱和聚酯树脂添加适量的阻然剂进行处理后形成的添加型阻燃不饱和聚酯树脂。本发明还公开一种结构增强型复合材料板材的制造方法,包括以下步骤:步骤一,制作金属结构框,将金属板材围合形成长方体结构,并在内部沿长方体厚度方向设置多个相同金属材质的加强筋;步骤二,金属结构框内部设置芯材,芯材为硬质聚氨酯泡沫;步骤三,金属结构框外表包覆至少一层复合材料面层,复合材料面层为无碱玻璃纤维或添加型阻燃不饱和聚酯树脂复合材料;步骤四,将内部填充有芯材、外部包覆有复合材料面层的金属结构框放置于复合板成型的自加热平台上,利用该自加热平台对金属结构框进行分阶段加热、加压,使金属结构框内部芯材发泡并填充整个内部空腔;步骤五,待复合材料板材充分固化后取出。进一步地,所述步骤四中分梯度进行加热加压,先加热至80-120摄氏度,加压至50-80MPa,保持2-5min;然后继续加热至180-220摄氏度,加压至100-150MPa,保持2-5min。作为以上所述步骤四中分梯度进行加热加压的一个实施例,先加热至80摄氏度,加压至80MPa,保持5min;然后继续加热至180摄氏度,加压至150MPa,保持5min。作为以上所述步骤四中分梯度进行加热加压的另一个实施例,所述步骤四中分梯度进行加热加压,先加热至120摄氏度,加压至50MPa,保持2min;然后继续加热至220摄氏度,加压至100MPa,保持2min。如图1所示,本发明公开一种用于复合材料板材成型的自加热平台,包括:长方体框架结构的支撑装置1,设置于支撑装置1上呈长方形的钢化玻璃模板2,设置于支撑装置1上位于钢化玻璃模板2下方的热辐射灯安装基座3,热辐射灯安装基座3上设置有多个热辐射灯41,多个热辐射灯41均与温控装置42之间电连接,温控装置42与电源连接;支撑装置1长方体框架的四周、且位于热辐射灯安装基座3与钢化玻璃模板2之间围设有四块保温型透明有机玻璃板;设置于支撑装置1上、位于钢化玻璃模板2的上方罩设有保温透明型的有机玻璃罩5,有机玻璃罩5与钢化玻璃模板2之间为可拆卸式连接,且连接处为活动密封连接;有机玻璃罩5外设置有空气增压装置8,用于复合材料板材成型过程中边加热边加压。优选地,热辐射灯安装基座3平行于钢化玻璃模板2设置在支撑装置1上。因为热辐射灯安装在非封闭的空间中,热辐射灯产生的热量易散失,为了减少热量的流失、缩短升温的时间、保证温度的恒定,所述自加热平台支撑装置1长方体框架的四周、且位于热辐射灯安装基座3与钢化玻璃模板2之间围设有四块保温型透明有机玻璃板,采用透明的材质可以观察到复合材料板材成型时树脂的流动过程,和芯材泡沫的发泡过程,可以及时发现成型过程中出现的一些问题及时解决。为了便于移动用于复合材料板材成型的自加热平台,所述长方体框架的底部均匀设置有多个支撑活动脚轮7。能够通过支撑活动脚轮调节装置高度,可以实现整个加热平台的水平度调节,摆脱生产场地高低不平的限制。为了加强支撑装置对钢化玻璃模板的支撑,所述长方体框架的上端设置有支撑梁,且支撑梁位于钢化玻璃模板的下方,所述支撑梁与钢化玻璃模板之间设置有橡胶板,橡胶板与支撑梁相接触,起到缓冲作用,为了避免因为支撑梁的存在使钢化玻璃模板的一部分不能被热辐射灯照射到,会导致钢化玻璃模板的受热不均,影响复合板成型效果,还可以在支撑梁与钢化玻璃模板之间设置导热板,导热板与钢化玻璃模板相接触,通过设置导热板对该部分钢化玻璃模板起到传热作用,保证整个钢化玻璃模板受热均匀。经过以上所述装置、所述工艺加工得到的本发明所述增强型复合材料板材经过抗拉强度、拉伸模量、线膨胀系数等相关力学性能试验,结果平均值如下所示:测试项目测试结果巴氏硬度/HBA42拉伸强度/MPa135拉伸模量/GPa12.3线膨胀系数(25-55℃)/k-11.81*10-5冲击韧度/kJ/m2184结果表明其保温隔热性能好,抗拉强度高,热膨胀系数低,增强型复合材料板材的尺寸稳定。本
技术领域:
技术人员可以理解,除非另外定义,这里使用的所有术语(包括技术术语和科学术语)具有与本发明所属领域中的普通技术人员的一般理解相同的意义。还应该理解的是,诸如通用字典中定义的那些术语应该被理解为具有与现有技术的上下文中的意义一致的意义,并且除非像这里一样定义,不会用理想化或过于正式的含义来解释。以上述依据本发明的理想实施例为启示,通过上述的说明内容,相关工作人员完全可以在不偏离本项发明技术思想的范围内,进行多样的变更以及修改。本项发明的技术性范围并不局限于说明书上的内容,必须要根据权利要求范围来确定其技术性范围。当前第1页1 2 3