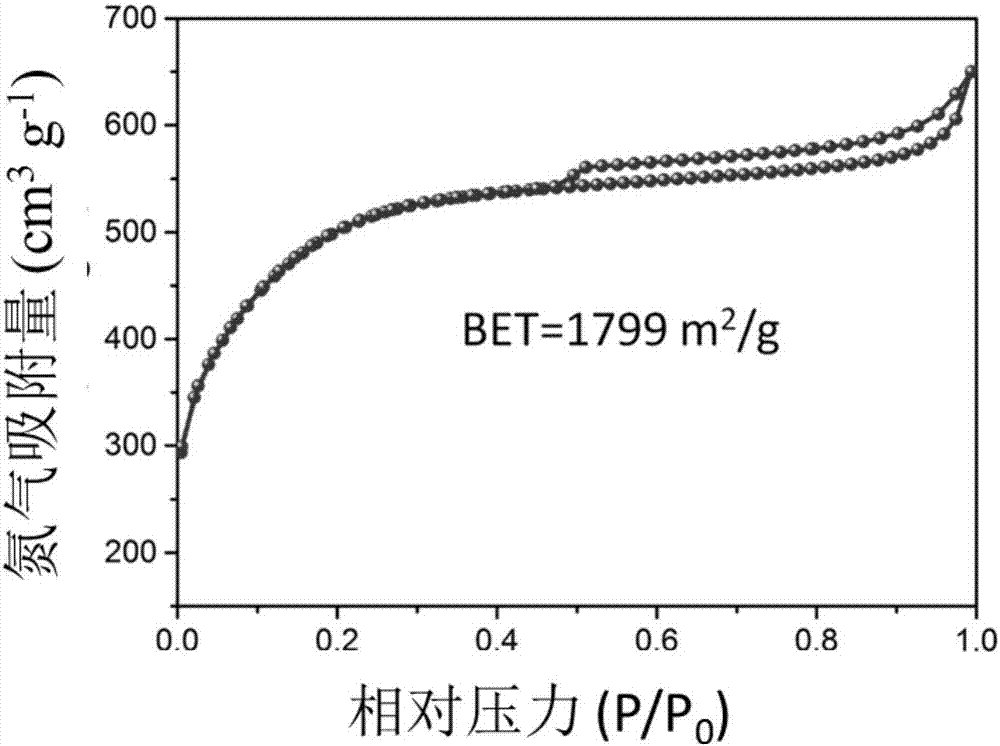
本发明属于石墨烯材料制备领域,更具体地,涉及一种超高比表面积硫氮共掺杂多孔石墨烯的制备方法及产品。
背景技术:在诸多炭材料中,石墨烯由于其特殊的结构和性质成为目前人们研究的热点。石墨烯是由碳六元环组成的二维周期性结构,这种特殊的结构使其具有许多奇特的性质,如室温量子霍尔效应、铁磁性、超导性和巨磁阻效应等。此外,石墨烯还具有优异的热学性能、电学性能、力学性能以及很高的化学稳定性和热力学稳定性,使其在纳米器件、电池/超级电容器、复合材料以及储氢材料、催化剂等领域表现出潜在的应用前景。然而,由于石墨烯没有能带隙,使得其电导性不能像传统的半导体一样完全被控制,而且石墨烯表面光滑且呈惰性,不利于与其他材料的复合,从而在一定程度上阻碍了石墨烯的广泛应用。近年来,研究者发现对石墨烯进行化学掺杂,能够有效地调变其结构和性能,进而实现石墨烯及其相关材料更为丰富的功能和广阔的应用。N、S等元素因能有效打开石墨烯的能带间隙,可调整其导电类型(通过掺杂实现p型和n型半导体之间的转换),改变其电子结构,从而提高其自由载流子密度,增加其导电性和稳定性。传统主要以气相沉积法(CVD)制备N、S掺杂及其S和N共掺杂石墨烯,但其制备过程非常繁琐,不仅需要金属催化剂和硅片等模板,还需要复杂的真空体系,大规模生产成本高昂,难以实现其商业化。除此之外,直接高温煅烧含N、S等高分子及其聚合物前驱体(三聚氰胺、氨水等)和石墨烯/氧化石墨烯的混合物,以及将石墨烯基衍生物在含杂原子气体(NH3,H2S,HCN)等氛围下进行热处理,也可得到单原子掺杂或双原子掺杂石墨烯。但这两种方法制备的石墨烯比表面积普遍不高<900m2/g,且制备过程较为复杂,需要先制备氧化石墨烯再进行混合,或需要复杂的有机气体环境,这都不利于其推广,且聚合物前驱体和有机气体多有毒有害,严重威胁人体健康。另,CN201510201085.4公开了一种动物骨基类石墨烯锂离子电池负极材料及其制备方法,其采用动物骨作为原材料,通过碳化、活化和石墨化,结合一定温度下的热处理制得石墨烯,该方法需高温活化,并且活化后需高温转化为石墨烯,制备工艺复杂,成本高,获得的石墨烯为普通的无掺杂的,且呈层状结构的石墨烯。因此,发明一种新的条件温和简单的制备高比表面积掺杂石墨烯材料方法,特别是制备较为复杂的硫氮双原子掺杂,非常具有实际价值。
技术实现要素:针对现有技术的以上缺陷或改进需求,本发明提供了一种超高比表面积硫氮共掺杂多孔石墨烯的制备方法及产品,其中利用角蛋白的特殊链状及环状结构,将生物质角蛋白直接转化为超高比表面积的硫氮共掺杂多孔石墨烯,所得石墨烯的氮含量可高达5.0at.%以上,硫含量达1.0at.%以上,比表面积高达1500m2/g以上,并且呈现出多孔的泡沫状石墨烯结构,其使用的原材料来源广泛,价格低廉,将其制备为石墨烯,不仅提升其应用价值,还有效解决了这些废物丢弃所带来的环境问题,具有制备简单、环保、成本低等优点。为实现上述目的,按照本发明的一个方面,提出了一种超高比表面积硫氮共掺杂多孔石墨烯的制备方法,该方法包括如下步骤:1)将含有角蛋白的生物质材料洗净晾干,至于管式炉惰性气氛中碳化获得所需样品,该生物质材料同时作为固体碳源、氮源和硫源,其中,碳化的具体工艺被设定为温度200~300℃,保温时间1~5h,升温速率1~2℃·min-1。2)将步骤1)中制得的样品置于真空手套箱碱性溶液中进行减压吸附,然后进行烘干,获得所需样品;3)将步骤2)中烘干的样品至于惰性气氛的管式炉中,初步升温至200~350℃,并保温0.5~3h,然后再升温至600~900℃,保温0.5~2h,以进行活化处理,然后自然冷却;4)将步骤3)所得的样品磨碎后酸洗,抽滤,并加水洗至中性;5)将步骤4)所得的样品置于真空干燥箱中干燥,得到超高比表面积硫氮共掺杂的多孔石墨烯。作为进一步优选的,所述步骤1)中采用的惰性气氛为氩气或氮气。作为进一步优选的,所述步骤2)中所用的碱性溶液为0.5~1.0mol·L-1的KOH或NaOH溶液。作为进一步优选的,所述步骤2)中真空手套箱所保持的气压为0~50pa,减压吸附时间为1~6h。作为进一步优选的,所述步骤2)中烘干的温度为80℃~100℃,烘干的时间为10h~12h。作为进一步优选的,所述步骤3)中惰性气氛为氩气或氮气,步骤3)中全程的升温速率为3~7℃·min-1。作为进一步优选的,所述步骤4)中酸洗为浸渍于60~90℃的酸溶液中酸洗4~10h,酸溶液具体为0.2~0.6mol·L-1的H2SO4、HCl或HNO3。作为进一步优选的,所述步骤5)中真空干燥在5Pa~50Pa条件下进行,干燥温度为60℃~90℃,干燥时间为10h~12h。作为进一步优选的,所述含有丰富角蛋白的生物质材料为动物毛发、蹄甲或角,优选为猪毛、牛毛、羊毛、鸡毛、鸭毛、鹅毛、猪蹄甲、牛蹄甲、羊蹄甲、牛角或羊角。按照本发明的另一方面,提供了一种由所述方法制备的超高比表面积硫氮共掺杂多孔石墨烯,该硫氮共掺杂多孔石墨烯呈多孔泡沫状结构,其比表面积大于1500m2/g,氮元素含量达到5.0at.%以上,硫元素含量达到1.0at.%以上。总体而言,通过本发明所构思的以上技术方案与现有技术相比,主要具备以下的技术优点:1.本发明选用含有丰富角蛋白的生物质例如动物毛发、蹄甲等作为原材料,将其作为唯一前驱体,同时作为固体碳源、氮源和硫源,直接制备具有高比表面积的硫氮共掺杂多孔石墨烯,该原材料来源广泛、环保友好、成本低,实现了动物毛发、蹄甲的再利用,减少了环境污染,不仅为制备杂原子掺杂多孔石墨烯提供了一种新途径,提升了生物质材料的应用价值,还对优化环境有一定促进意义。相比传统方法选用的前驱体,本发明选用的前驱体单一,无需传统多种材料混合,大大节约原料,降低石墨烯制备成本,且原材料无毒无害,有益于大规模生产。2.本发明对各个步骤的工艺及参数均进行了研究与设定,通过不断的研究试验获得最佳的工艺参数,通过各个工艺的相互配合,所制得的硫氮共掺杂多孔石墨烯具有超高比表面积,可达1500m2/g以上,是传统方法制备出的石墨烯比表面积的两倍甚至数倍;并且石墨烯中杂原子掺杂甚为高效,其中氮元素含量达到5.0at.%以上,最高可达8.0at.%以上,硫元素含量达1.0at.%以上,远高于用传统方法掺杂所得,此外,制备出的石墨烯具有传统制备方法难于得到的石墨烯泡状形貌,具有该形貌的石墨烯具有优异的介孔结构,能够有效的促进三相界面反应物质传输。3.本发明在制备中选用减压吸附混合工艺,相比传统搅拌等混合方法,更为高效,混合更为均匀;高温处理过程中,无需特殊的真空环境和复杂的有机气体环境,工艺简单,操作成本低。4.本发明所选用生物质毛发等制备石墨烯,只需低温碳化和900℃及其以下温度活化即可直接转化为石墨烯,并直接在活化步骤中即可转化为石墨烯,制备工艺更为简单,更、节约能量,降低制备成本。附图说明图1(a)是本发明实施例1所得的超高比表面积硫氮共掺杂多孔石墨烯的透射电镜(TEM)图;图1(b)是本发明实施例1所得的超高比表面积硫氮共掺杂多孔石墨烯的高倍透射电镜(HR-TEM)图;图2是本发明实施例1所得的超高比表面积硫氮共掺杂多孔石墨烯的氮气吸脱附图;图3是本发明实施例1所得的超高比表面积硫氮共掺杂多孔石墨烯的拉曼(Raman)图;图4是本发明实施例1所得的超高比表面积硫氮共掺杂多孔石墨烯的X射线光电子能谱(XPS)图。具体实施方式为了使本发明的目的、技术方案及优点更加清楚明白,以下结合附图及实施例,对本发明进行进一步详细说明。应当理解,此处所描述的具体实施例仅仅用以解释本发明,并不用于限定本发明。此外,下面所描述的本发明各个实施方式中所涉及到的技术特征只要彼此之间未构成冲突就可以相互组合。本发明提供了一种将生物质角蛋白转化为超高比表面积硫氮共掺杂石墨烯的方法。生物中的动物毛发、蹄甲、角等含有丰富的角蛋白,角蛋白含有丰富的硫、氮和碳等元素。本发明利用生物质的特点,选用常见的动物指甲、角、毛发等为原材料,以其同时作为固体碳、氮、硫原料,首先初步碳化处理,再通过减压吸附混合KOH或NaOH碱性溶液,在管式炉中低温进一步去水处理和高温活化处理,然后酸洗真空干燥得到石墨烯。利用角蛋白的特殊链状及环状结构,将这种天然的生物质角蛋白直接转化为硫氮共掺杂石墨烯。由于在高温活化过程中,角蛋白这种特殊的链状及其环状分子,易于受K、Na等协同作用重排,重新连接形成石墨烯结构,又因金属钾离子及产生的H2O、H2、CO、CO2等气体在高温活化过程中在材料中不定向穿梭,可形成大量的孔洞,极大地增大了石墨烯的表面积。因此,以生物质角蛋白为前驱体,可通过设定的实验方案将其转化为高比表面积硫氮共掺杂的多孔石墨烯。本发明的一种制备超高比表面积硫氮共掺杂多孔石墨烯的方法,具体包括如下步骤:1)将含有丰富角蛋白的生物质材料例如动物毛发、蹄甲或角,优选为猪毛、牛毛、羊毛、鸡毛、鸭毛、鹅毛、猪蹄甲、牛蹄甲、羊蹄甲、牛角或羊角,洗净晾干,然后至于管式炉惰性气氛中初步碳化获得所需样品,该生物质材料同时作为固体碳源、氮源和硫源。其中,采用的惰性气氛为氩气或氮气,初步碳化温度为200℃~300℃,保温时间为1h~5h,升温速率为1℃·min-1~2℃·min-1。在此过程中,采用慢速的升温制度,有利于对原材料进行预膨胀,去除原料中的结晶水,为后续混合活性物质提供足够的孔道及间隙。2)将步骤1)中制得的样品置于真空手套箱碱性溶液中,减压吸附若干小时,然后至于普通干燥箱中烘干。减压吸附有利于溶液进入材料的深层孔道,利于活化;并在干燥箱去除溶剂。其中,所用的碱性溶液为0.5mol·L-1~1.0mol·L-1的KOH或NaOH溶液;真空手套箱所保持的气压为0~50pa,减压吸附时间为1h~6h;干燥箱的烘干温度为80℃~100℃,烘干时间为10h~12h。3)将步骤2)中烘干的样品至于惰性气氛的管式炉中,初步升温至一定温度并保温,再升温至活化温度保温一段时间,以进行活化处理,然后自然冷却。在惰性气氛(氩气或氮气)处理的前段部分主要是为了进一步去除材料中的结晶水,后续的处理主要是对样品进行有效的活化。其中,惰性气氛为氩气或氮气,初步升温并保持的温度为200℃~350℃,保温时间为0.5h~3h;活化处理的活化温度为600℃~900℃,保温时间为0.5h~2h;全程升温速率为3℃·min-1~7℃·min-1。4)将步骤3)所得的样品磨碎后酸洗,抽滤,并加水洗至中性。其中,酸洗具体为浸渍于60℃~90℃的酸溶液中酸洗4h~10h,酸溶液具体为0.2mol·L-1~0.6mol·L-1的H2SO4、HCl或HNO3。抽滤仪器采用循环水泵,压强为10Pa左右。并反复用去离子水冲洗3-5次,去除里面的杂质及可溶物质。通过上述过程可有效去除样品中的碱金属(K和Na)化合物以及可溶性杂质,得到较高纯度的样品。5)将步骤4)所得的样品置于真空干燥箱中干燥,得到超高比表面积硫氮共掺杂的多孔石墨烯。其中,真空干燥在5Pa~50Pa条件下进行,干燥温度为60℃~90℃,干燥时间为10h~12h。当然,本发明的硫氮共掺杂高比表面积多孔石墨烯的制备方法,不仅仅适用于以上所列的动物毛发和蹄甲等,而是适用于所有含有角蛋白的材料。以下为本发明的具体实施例。实施例11)将猪毛洗净晾干,至于管式炉氩气气氛中,升温至300℃初步碳化,保温时间为2h,升温速率为1℃·min-1;2)将步骤1)中制得的样品置于真空手套箱0.5mol·L-1KOH中,减压吸附2h,气压设置为10pa,并至于普通干燥箱中80℃烘干12h;3)将步骤2)中样品至于管式炉中,保持氩气气氛,升温至350℃,保温0.5h,再升温至800℃,保温1h,升温速率为5℃·min-1,再自然冷却;4)将步骤3)所得产物磨碎后浸渍于0.5mol·L-1的H2SO4溶液中80℃恒温酸洗8h后,抽滤,并加水洗至中性;5)将步骤4)所得样品置于真空干燥箱中(压力为5pa,温度为60℃)干燥12h得到超高比表面积的硫氮共掺杂多孔石墨烯。所得的硫氮共掺杂多孔石墨烯的结构如图1(a)、1(b)所示,其中图1(a)为所得石墨烯的透射电镜(TEM)图,可以看到石墨烯泡状结构及微孔结构。图1(b)为所得石墨烯的高倍透射电镜(HR-TEM)图,石墨烯堆叠状及其泡状结构清晰可见。所得硫氮共掺杂多孔石墨烯的比表面积如图2所示,高达1799m2/g。图3为所得石墨烯的拉曼光谱(Raman)图,在2655cm-1处出现了石墨烯2D峰,表明有石墨烯结构的存在。所得硫氮共掺杂多孔石墨烯的组分结果如图4所示,从图中可以看出该石墨烯主要含有C、N、O、N四种元素,其中N元素的含量为8.25at.%,硫元素的含量为1.29at.%。实施例21)将鸡毛洗净晾干,至于管式炉氩气气氛中,升温至250℃初步碳化,保温时间为3h,升温速率为2℃·min-1;2)将步骤1)中的制得的样品置于手套箱0.7mol·L-1NaOH中,减压吸附1h,气压设置为5pa,并至于普通干燥箱中90℃烘干11h;3)将步骤2)中样品至于管式炉中,保持氩气气氛,升温至200℃,保温1h,再升温至700℃,保温1h,升温速率为3℃·min-1,再自然冷却;4)将步骤3)所得产物磨碎后浸渍于0.3mol·L-1的HCl溶液中90℃恒温酸洗5h后,抽滤,并加水洗至中性;5)将步骤4)所得样品置于真空干燥箱中(压力为40pa,温度为70℃)干燥11h得到超高比表面积硫氮共掺杂多孔石墨烯。所得硫氮共掺杂多孔石墨烯的比表面积为1622m2/g,氮元素的含量为6.93at.%,硫元素的含量为1.67at.%。实施例31)将鸭毛洗净晾干,至于管式炉氩气气氛中,升温至200℃初步碳化,保温时间为4h,升温速率为1.5℃·min-1;2)将步骤1)中的制得的样品置于手套箱0.8mol·L-1KOH中,减压吸附3h,气压设置为20pa,并至于普通干燥箱中100℃烘干10h;3)将步骤2)中样品至于管式炉中,保持氩气气氛,升温至300℃,保温1h,再升温至600℃,保温0.5h,升温速率为4℃·min-1,再自然冷却;4)将步骤3)所得产物磨碎后浸渍于0.6mol·L-1的盐酸溶液中90℃恒温酸洗10h后,抽滤,并加水洗至中性;5)将步骤4)所得样品置于真空干燥箱中(压力为25pa,温度为90℃)干燥10h得到超高比表面积的硫氮共掺杂多孔石墨烯。所得硫氮共掺杂多孔石墨烯的比表面积为1708m2/g,氮元素的含量为6.65at.%,硫元素的含量为1.42at.%。实施例41)将鹅毛洗净晾干,至于管式炉氩气气氛中,升温至275℃初步碳化,保温时间为3h,升温速率为1.7℃·min-1;2)将步骤1)中的制得的样品置于手套箱0.4mol·L-1KOH中,减压吸附1h,气压设置为10pa,并至于普通干燥箱70℃中烘干11.5h;3)将步骤2)中样品至于管式炉中,保持氮气气氛,升温至300℃,保温1.5h,再升温至900℃,保温1h,升温速率为6℃·min-1,再自然冷却;4)将步骤3)所得产物磨碎后浸渍于0.5mol·L-1的HNO3溶液中70℃恒温酸洗11h后,抽滤,并加水洗至中性;5)将步骤4)所得样品置于真空干燥箱中(压力为15pa,温度为80℃)干燥10.5h得到超高比表面积硫氮共掺杂多孔石墨烯。所得硫氮共掺杂多孔石墨烯的比表面积为1502m2/g,氮元素的含量为5.43at.%,硫元素的含量为1.04at.%。实施例51)将牛毛洗净晾干,至于管式炉氩气气氛中,升温至300℃初步碳化,保温时间为3h,升温速率为1℃·min-1;2)将步骤1)中的制得的样品置于手套箱0.9mol·L-1NaOH中,减压吸附4h,气压设置为40pa,并至于普通干燥箱中100℃烘干10h;3)将步骤2)中样品至于管式炉中,保持氩气气氛,升温至350℃,保温0.5h,再升温至700℃,保温2h,升温速率为5℃·min-1,再自然冷却;4)将步骤3)所得产物磨碎后浸渍于0.6mol·L-1的H2SO4溶液中60℃恒温酸洗8h后,抽滤,并加水洗至中性;5)将步骤4)所得样品置于真空干燥箱中(压力为5pa,温度为90℃)干燥10h得到超高比表面积硫氮共掺杂多孔石墨烯。所得硫氮共掺杂多孔石墨烯的比表面积为1709m2/g,氮元素的含量为6.65at.%,硫元素的含量为1.09at.%。实施例61)将羊毛洗净晾干,至于管式炉氩气气氛中,升温至300℃初步碳化,保温时间为1h,升温速率为2℃·min-1;2)将步骤1)中的制得的样品置于手套箱0.6mol·L-1KOH中,减压吸附4h,气压设置为5pa,并至于普通干燥箱中90℃烘干11h;3)将步骤2)中样品至于管式炉中,保持氮气气氛,升温至300℃,保温2h,再升温至800℃,保温1.2h,升温速率为3℃·min-1,再自然冷却;4)将步骤3)所得产物磨碎后浸渍于0.5mol·L-1的HCl溶液中90℃恒温酸洗6h后,抽滤,并加水洗至中性;5)将步骤4)所得样品置于真空干燥箱中(压力为10pa,温度为90℃)干燥10h得到超高比表面积硫氮共掺杂石墨烯。所得硫氮共掺杂石墨烯的比表面积为1584m2/g,氮元素的含量为5.87at.%,硫元素的含量为1.19at.%。实施例71)将牛蹄甲洗净晾干,至于管式炉氩气气氛中,升温至300℃初步碳化,保温时间为3h,升温速率为1.2℃·min-1;2)将步骤1)中的制得的样品置于手套箱1.0mol·L-1KOH中,减压吸附4h,气压设置为3pa,并至于普通干燥箱中85℃烘干11.5h;3)将步骤2)中样品至于管式炉中,保持氮气气氛,升温至280℃,保温2h,再升温至800℃,保温2h,升温速率为6℃·min-1,再自然冷却;4)将步骤3)所得产物磨碎后浸渍于0.3mol·L-1的H2SO4溶液中90℃恒温酸洗12h后,抽滤,并加水洗至中性;5)将步骤4)所得样品置于真空干燥箱中(压力为5pa,温度为85℃)干燥10.5h得到超高比表面积硫氮共掺杂多孔石墨烯。所得硫氮共掺杂多孔石墨烯的比表面积为1726m2/g,氮元素的含量为5.25at.%,硫元素的含量为1.26at.%。实施例81)将羊角洗净晾干,至于管式炉氩气气氛中,升温至300℃初步碳化,保温时间为3h,升温速率为1.8℃·min-1;2)将步骤1)中的制得的样品置于手套箱1.0mol·L-1NaOH中,减压吸附3h,气压设置为10pa,并至于普通干燥箱中88℃烘干11.6h;3)将步骤2)中样品至于管式炉中,保持氩气气氛,升温至300℃,保温3h,再升温至900℃,保温2h,升温速率为3℃·min-1,再自然冷却;4)将步骤3)所得产物磨碎后浸渍于0.5mol·L-1的HCl酸溶液中80℃恒温酸洗4h后,抽滤,并加水洗至中性;5)将步骤4)所得样品置于真空干燥箱中(压力为5pa,温度为90℃)干燥10h得到超高比表面积硫氮共掺杂多孔石墨烯。所得硫氮共掺杂多孔石墨烯的比表面积为1656m2/g,氮元素的含量为6.30at.%,硫元素的含量为1.06at.%。本领域的技术人员容易理解,以上所述仅为本发明的较佳实施例而已,并不用以限制本发明,凡在本发明的精神和原则之内所作的任何修改、等同替换和改进等,均应包含在本发明的保护范围之内。