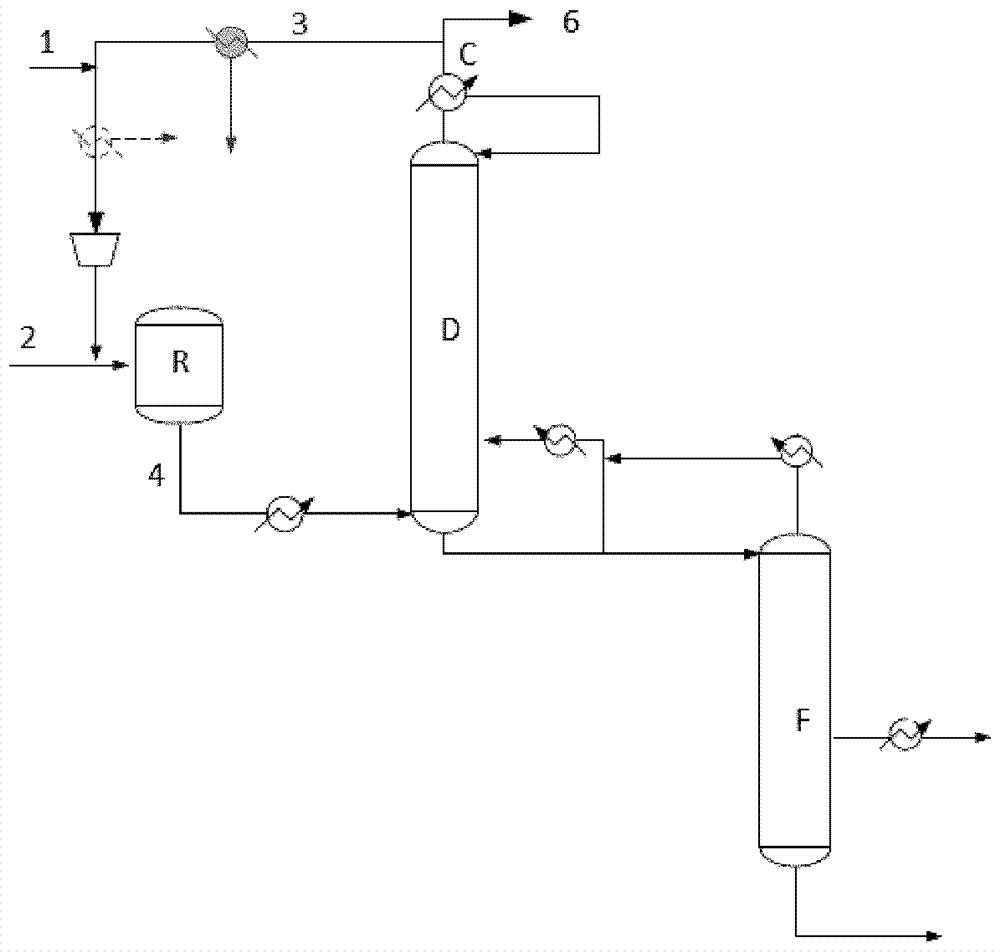
本发明涉及(甲基)丙烯酸的制备。本发明的主题更特别地是在(甲基)丙烯酸的制备方法中实施在再循环的气体流出物中和/或在空气进料中包含的水的冷凝步骤,所述方法包括使包含(甲基)丙烯酸的反应混合物纯化的工艺,该工艺不使用共沸溶剂并基于使用两个蒸馏塔。根据本发明的方法允许减少在纯化期间的(甲基)丙烯酸的损失,并且总体上提高该方法的效率。技术背景和技术问题在工业大规模上使用的丙烯酸的合成方法在氧存在下进行丙烯的催化氧化反应。这种反应通常在气相中,最通常地在两个步骤中进行:第一步在富集丙烯醛的混合物中进行丙烯的基本上定量的氧化反应,然后在第二步中,使丙烯醛选择性氧化为丙烯酸。从第二步得到的气体混合物除了丙烯酸之外还包含:-由第一反应步骤得到的未反应的杂质(丙烯、丙烷);-在第一步中未转化的或在第二步中形成的在通常使用的温度和压力条件下不可冷凝的轻质化合物:氮、未转化的氧、在该方法中通过最终氧化少量形成的或通过循环在回路中流通的一氧化碳和二氧化物;-在第一步中未转化的或在第二步中形成的可冷凝的轻质化合物:水、未转化的丙烯醛、轻醛如甲醛和乙醛、甲酸、乙酸或丙酸;-重质化合物:糠醛、苯甲醛、马来酸和酸酐、苯甲酸、2-丁烯酸、苯酚、原白头翁素。在这种方法中获得的气体混合物的复杂性要求进行一系列操作,以回收在这种气体流出物中包含的丙烯酸并将其转化为与其最终用途,例如丙烯酸酯的合成或丙烯酸和/或丙烯酸酯的聚合物的制备相适应的丙烯酸等级。最近出现了一种新型丙烯酸的回收/纯化技术,其涉及减少数量的纯化步骤并且不需要任何外部有机溶剂。基于这种“不使用溶剂”的技术的专利ep2066613描述了一种不使用外部水和共沸溶剂的回收丙烯酸的方法,该方法仅使用两个用于纯化冷却的气体反应混合物的塔:a)脱水塔,和b)用脱水塔的底部料流的一部分进料的精制塔(或纯化塔)。根据这种方法,使冷却的气体反应料流在第一塔中经受脱水。在塔顶被蒸馏出的气体料流被送至冷凝器中,其中轻质化合物部分地进行冷凝并以回流形式被送回脱水塔,以吸收丙烯酸,气体流出物至少部分地被送到反应中,和剩余物被焚烧。将脱水塔的底部料流进料到第二塔,其允许以液体或蒸气形式通过从侧面取出来分离符合工业级的纯化丙烯酸料流。所获得的工业级丙烯酸通常具有大于98.5重量%的纯度并且含有小于0.5重量%的水。在这种精制塔中,使包含水和轻质副产物的顶部馏出物冷凝,然后再循环至第一塔的底部,并且在底部除去包含富集重质副产物的丙烯酸的料流,以便任选地用于制备丙烯酸酯。在这种方法中,一部分料流(来自脱水塔的底部或来自精制塔的顶部)有利地被送回到脱水塔的加热装置/再沸器和/或用于冷却气体反应混合物,这允许优化该方法的能量需求。尽管在文献ep2066613中描述的纯化方法提供的优点,仍然存在与其实施相关的缺点,特别是在不同步骤期间丙烯酸的可能损失方面。特别地,丙烯酸可以在脱水塔的顶部被夹带出。根据在位于顶部的冷凝器的操作温度的液体/蒸汽平衡,在出口处的气体流出物可含有不可忽略量的丙烯酸。丙烯酸在被焚烧的气体流出物的一部分中直接被损失掉。因此,仍然需要在基于使用脱水塔和精制塔的不使用溶剂的回收/纯化方法中降低丙烯酸的损失,并且特别地降低在脱水塔顶部的丙烯酸的损失。本发明人现已发现,通过控制在这种方法中引入的水的含量,可以降低丙烯酸的损失。主要的水源来自待处理的粗反应混合物,因为其含有在使丙烯催化氧化成丙烯酸的反应期间形成的水。水是在脱水塔顶部蒸馏出的主要“轻质”杂质,并且其在纯化过程中的去除决定了所希望的纯化的丙烯酸(水含量<0.5重量%)的品质。需要在脱水塔顶部以最佳方式除去水,同时使丙烯酸的损失最小化。例如,可以降低在顶部设置的冷凝器的温度,以便改变液体/蒸汽平衡并防止丙烯酸夹带在气体流出物中。然而,这仅在取决于被引入脱水塔中的水的含量的某一限度内是可能的。除了丙烯酸的合成过程中固有的水之外,通过其它途径引入水,例如在引入该反应以进行丙烯的氧化的空气料流中存在的水分。此外,将阻聚剂的水溶液引入塔和/或冷凝器中以限制聚合反应,并且如此引入的水可以通过循环和/或回流在该方法中循环。已经发现,通过减少这些补充的水源,可以优化在脱水塔顶部的水的去除,同时使丙烯酸的损失最小化。根据本发明,提出使在进料该反应的空气流中存在的水和/或在被循环至该反应的来自脱水塔的气体流出物中存在的水冷凝。此外,对于本发明人来说明显的是,本发明可以应用于由除丙烯以外的来源制备的丙烯酸,应用于甲基丙烯酸,以及应用于这些衍生自可再生原料的酸,它们能够产生与水的存在相关的相同的纯化问题。技术实现要素:本发明首先涉及(甲基)丙烯酸的制备方法,其至少包括以下步骤:i)在空气存在下,使至少一种(甲基)丙烯酸的前体进行气相氧化反应,以形成包含(甲基)丙烯酸的气体反应混合物;ii)使气体反应混合物冷却;iii)将气体反应混合物在称为脱水塔的第一塔中不使用共沸溶剂进行脱水反应,得到顶部气体料流和底部料流;iv)使在脱水塔顶部蒸馏出的气体料流至少部分地在顶部冷凝器中经受冷凝,将冷凝液以回流形式送回脱水塔以吸收丙烯酸,并且使气体流出物至少部分地返回到氧化反应,并且使其余部分经受热氧化和/或催化氧化;v)使脱水塔的底部料流在称为精制塔的第二塔中至少部分地经受蒸馏,得到顶部料流和底部料流,该底部料流含有重质化合物;vi)通过从精制塔的侧面取出以回收(甲基)丙烯酸料流;所述方法的特征在于,进行施用于以下两个料流中至少一个的水冷凝步骤:用于步骤i)的氧化反应的空气进料或在步骤iv)的顶部冷凝器的出口处的气体流出物,该气体流出物被再循环至氧化反应。在本发明中,术语“(甲基)丙烯酸”是指“丙烯酸”或“甲基丙烯酸”。术语“共沸溶剂”表示具有与水形成共沸混合物的性质的任何有机溶剂。定性副产物化合物的术语“轻质”表示其沸点低于(甲基)丙烯酸的沸点的化合物,类似地,术语“重质”表示其沸点高于(甲基)丙烯酸的沸点的化合物。根据本发明的方法还可以包括旨在继续使在步骤vi)中回收的(甲基)丙烯酸料流纯化的其它步骤。根据本发明的一个实施方案,(甲基)丙烯酸的前体是丙烯醛。根据本发明的一个实施方案,丙烯醛通过丙烯的氧化或通过丙烷的氧化脱氢获得。根据本发明的一个实施方案,(甲基)丙烯酸的前体是甲基丙烯醛。根据本发明的一个实施方案,甲基丙烯醛通过异丁烯和/或叔丁醇的氧化获得。根据本发明的一个实施方案,甲基丙烯醛由丁烷和/或异丁烷的氧化脱氢获得。根据本发明的一个实施方案,(甲基)丙烯酸的前体衍生自甘油,3-羟基丙酸或2-羟基丙酸(乳酸)。根据本发明的一个优选实施方案,(甲基)丙烯酸是丙烯酸,丙烯酸的前体是通过丙烯的催化氧化获得的丙烯醛。气体反应混合物包含根据两步氧化方法获得的衍生自丙烯的丙烯酸。根据某些特定实施方案,本发明还具有一个或优选更多个以下列出的有利特征:-水的冷凝步骤借助于用于两个料流的单个冷凝器或借助于用于两个料流中的每一个的冷凝器进行实施;-水的冷凝步骤在从15℃至在脱水塔顶部的冷凝器的温度的温度下进行;-用于该循环的气体流出物的水冷凝步骤优选在40℃-60℃之间,更优选在45℃-55℃之间的温度下进行;-用于空气进料的水冷凝步骤优选在15℃-25℃之间的温度下进行;-冷凝的水部分地用于制备阻聚剂水溶液,该水溶液被引入到脱水塔和/或精馏塔中或它们相关的冷凝器中;-冷凝的水部分地进行净化并送至废水处理,或进行热氧化处理。根据本发明的方法允许减少在反应和脱水塔之间的水回路的形成,冷凝水有利地用于制备对于该方法的良好运行所需的阻聚剂水溶液。因此限制了用于制备阻聚剂溶液的外部水的引入,并且可能存在于冷凝水中的丙烯酸被直接再循环到净化管线中,而不是被送回到其中它可以最终被氧化成一氧化碳或二氧化碳的反应器中。外部水的不存在允许通过降低其温度来调节脱水塔的顶部冷凝器的操作条件,因此丙烯酸的损失得到限制。此外,由于在氧化反应器中较低的含水量和较低的有机杂质含量,可以改善(甲基)丙烯酸的前体的氧化催化剂的性能及其寿命。根据本发明的方法还可以包括其它步骤或其它特征,如果它们不负面地影响由本发明提供的效果的话。附图说明通过参照附图1至5,阅读下面的详细描述,本发明的其它特征和优点将更加清楚,其中所述附图表示:-图1:适合于实施根据本发明的方法的装置;-图2:现有技术的流程图;-图3:描述本发明的第一种实施方案的流程图;-图4:描述本发明的第二种实施方案的流程图;-图5:描述本发明的第三种实施方案的流程图。具体实施方式本发明基于将至少一个冷凝器集成到(甲基)丙烯酸的制备方法中,该方法包括现有技术的不使用溶剂的回收/纯化工艺。在图1中示出了反应器r,其产生包含通过(甲基)丙烯酸的前体2使用空气1的气相氧化而获得的(甲基)丙烯酸的气体反应混合物4。根据一个实施方案,反应器r是一组2个串联的反应器或包括至少2个串联的反应区,第一个反应器或第一个反应区用于合成(甲基)丙烯酸的前体。包含通常在0.3至2之间的水/(甲基)丙烯酸重量比的气体反应混合物可以在被送至称为“脱水塔d”的第一塔之前预先被冷却。脱水塔在顶部包括顶部冷凝器c,在其中轻质化合物和水部分冷凝并以回流形式送回脱水塔以吸收丙烯酸。将包含不可冷凝的轻质化合物和水的气体流出物至少部分地送回该反应(料流3),并将剩余物(料流6)送至净化装置、热氧化器和/或催化氧化剂,或被焚烧。根据一个实施方案,脱水塔所有顶部料流被送至顶部冷凝器。脱水塔d至少部分地作为蒸馏塔,通常在大气压或略高于大气压,最高至1.5×105pa运行。有利地,在脱水塔的上部中的温度为至少40℃,优选为在40℃-80℃之间。在脱水塔的底部料流的温度优选不超过120℃。没有共沸溶剂被添加到脱水塔中。脱水塔产生底部料流,该底部料流主要包含具有重质副产物的(甲基)丙烯酸和通常小于10%,优选小于7%的重量含量的水。将脱水塔的底部料流至少部分地送入第二个蒸馏塔(称为精制塔f或纯化塔)的顶部。脱水塔和精制塔可以具有各种构造,例如为无规或规整(structuré)填料塔或板式塔的类型。在纯化塔中的温度和压力不是关键的,并且可以根据现有技术已知的蒸馏方法进行确定。然而,优选地,纯化塔在低于大气压的压力下运行,这允许在相对低的温度下运行,从而防止存在的不饱和产物的聚合,并且使重质副产物的形成最小化。有利地,纯化塔在5kpa至约60kpa的压力下运行,顶部料流的温度有利地在40℃至约90℃之间,底部料流的温度在60℃至120℃之间。精制塔产生包含水和轻质副产物的顶部馏出物,其被冷凝然后再循环到第一塔的底部,和包含富集重质副产物的丙烯酸的底部料流,其在底部被除去以任选地用于制备丙烯酸酯。从精制塔f的侧面取出的料流符合工业(甲基)丙烯酸等级。其通常由纯度大于98%,优选大于99%的(甲基)丙烯酸组成。优选地,其含有小于1.5重量%,优选小于0.5重量%,更特别小于0.2重量%的乙酸和小于1重量%,优选小于0.5重量%,更特别是小于0.3重量%的水。该料流还可以通过蒸馏进行纯化,任选与结晶处理相结合。根据本发明的方法,将至少一个冷凝器设置在气体流出物3和/或空气进料1上以至少使在这些流中存在的水冷凝,其中气体流出物3被循环到反应器r。可以使用单个冷凝器或者两个冷凝器(如图1所示)。冷冻水或冷水用于冷凝该气体。水的温度根据冷凝温度可以为约8℃至约45℃。设置在空气进料上的冷凝器优选用约8℃的冷却水进行冷却。设置在再循环气体流出物上的冷凝器优选用环境温度(约25℃)的水进行冷却。冷凝器可以具有各种构造,如管束式交换器,螺旋式交换器,翅片管式交换器或液体接触式冷凝器等。水的冷凝温度可以从15℃至脱水塔的顶部冷凝器的温度,该脱水塔的顶部冷凝器的温度通常低于65℃。根据一个实施方案,设置于气体流出物3位置处的冷凝器的温度在40℃至60℃之间,优选在45℃至55℃之间。根据一个实施方案,设置在空气进料1的位置处的冷凝器的温度在15℃至25℃之间。根据一个实施方案,来自空气进料的冷凝水(其不含有机杂质)有利地至少部分地被再循环到水冷却塔。根据一个实施方案,冷凝水部分地用于制备阻聚剂的水溶液,其可以在不同位置被引入装置中。阻聚剂选自抑制(甲基)丙烯酸的聚合反应的化合物。作为可使用的化合物的实例,可以提及吩噻嗪,氢醌,2,2,6,6-四甲基-1-哌啶氧基(tempo)或其衍生物的一种,例如4-羟基tempo,可溶性铜盐,可溶性盐锰盐,单独地或作为混合物。阻聚剂的水溶液以本领域技术人员已知的足够量被加入,以防止或减少在装置中,特别是在脱水塔的顶部料流(在塔顶冷凝器位置)中,或者在精馏塔的顶部料流(在与所述塔连接的冷凝器的位置)中,或者在从精制塔的侧面取出的纯化产物料流(任选地在冷凝后,如果排出的料流为气体形式)中的(甲基)丙烯酸的聚合。根据本发明的方法引起以与现有技术方法相比改进的产率制备(甲基)丙烯酸。这是因为对再循环到反应和/或空气进料的气体流出物使用冷凝器允许,与不包括冷凝步骤(以限制水进入反应器)的方法相比,将丙烯酸的损失降低超过50%。此外,除了降低丙烯酸的损失之外,已可以将顶部冷凝器的温度降低约2至4℃,这在能量方面具有额外的优点。现在将通过以下实施例说明本发明,实施例的目的不是限制由权利要求限定的本发明的范围。实验部分实施例1(参照)参考图2,其表示用于制备丙烯酸(aa)的现有技术的方法,反应器用聚丙烯料流2和空气料流1进行供给。在反应器的出口处,将包含所产生的丙烯酸的气体反应混合物在交换器中冷却之后送至在其上装有顶部冷凝器c的脱水塔d。将阻聚剂水溶液料流5引入顶部冷凝器c的位置。一部分气体流出物3被循环到反应器中,并且一部分气体流出物6被送到焚烧炉。借助于aspen软件的模拟用于表征这种类型装置中的丙烯酸的损失。结果示于下表1中:表1通过反应产生的aa,kg/h11805在冷凝器c的顶部损失的aa,kg/h206在c的顶部的aa损失,%1.74顶部冷凝器c的温度,℃60.9在反应器r入口处的水,%6.58在反应器r出口处的水量,kg/h6660在反应器r出口处的aa,kg/h11871在反应器r出口处的aa/水比1.78实施例2(根据本发明)图3表示本发明的第一种实施方案。相对于图2,将冷凝器/冷却器置于进料空气料流1上。冷凝至15℃的水料流7可以被再循环到冷却塔。aspen模拟结果整理在下表2中。通过去除在供给反应器的空气中存在的水分,观察到,与实施例1的情况相比,在冷凝器顶部的丙烯酸的损失降低了接近50%。表2由反应产生的aa,kg/h11813在冷凝器c的顶部损失的aa,kg/h112在c的顶部的aa损失,%0.95顶部冷凝器c的温度,℃58.8在反应器r入口处的水,%5.05在反应器r出口处的水量,kg/h6002在反应器r出口处的aa,kg/h11853在反应器r出口处的aa/水比1.97实施例3(根据本发明)图4表示本发明的第二种实施方案。相对于图2,将冷凝器/冷却器置于进料空气料流1上,并将冷凝器置于被循环至反应器中的流出物3上。来自空气的水分的冷凝水料流7可以被再循环到冷却塔。冷凝液8从该方法中被去除。根据这种配置,根据表3进行了两次aspen模拟。表3测试1测试2由反应产生的aa,kg/h1181811820在冷凝器c顶部的损失的aa,kg/h7359在c顶部的aa损失,%0.690.58循环的流出物的冷凝器的温度,℃5350来自循环的流出物的冷凝液8,kg/h398.4562.9循环的冷凝液,kg/h00在冷凝液中的aa的损失,kg/h8.39.5顶部冷凝器c的温度,℃57.456.7在反应器r入口处的水,%4.143.75在反应器r出口处的水量,kg/h56025430在反应器r出口处的aa,kg/h1183711833在反应器r出口处的aa/水比2.112.18在该表中,在冷凝器c顶部的aa损失的百分比考虑了在冷凝液8中存在的aa的损失。在这些条件下,即使来自再循环气体流出物的冷凝水料流被去除,aa总损失仍然低于参考实施例1的aa总损失。此外,冷凝器c可以在较低温度下运行。实施例4(根据本发明)图5表示本发明的第三种实施方案。相对于图4,将冷凝液8引入搅拌的容器中,在该容器中引入至少一种阻聚剂,并且在原位如此制备的阻聚剂水溶液5可以在冷凝器c位置处直接被引入。aspen模拟结果整理在下表4中:表4反应产生的aa,kg/h11818在冷凝器c顶部损失的aa,kg/h77在c的顶部的aa损失,%0.65循环流出物的冷凝器的温度,℃53来自循环流出物的冷凝液8,kg/h0循环的冷凝液,kg/h395在冷凝液中的aa的损失,kg/h0顶部冷凝器c的温度,℃57.3在反应器r入口处的水,%4.12在反应器r出口处的水量,kg/h5596在反应器r出口处的aa,kg/h11838在反应器r出口处的aa/水比11818这种实施方案不仅允许降低aa损失,而且不需要任何外部清洁水来制备阻聚剂水溶液。当前第1页12