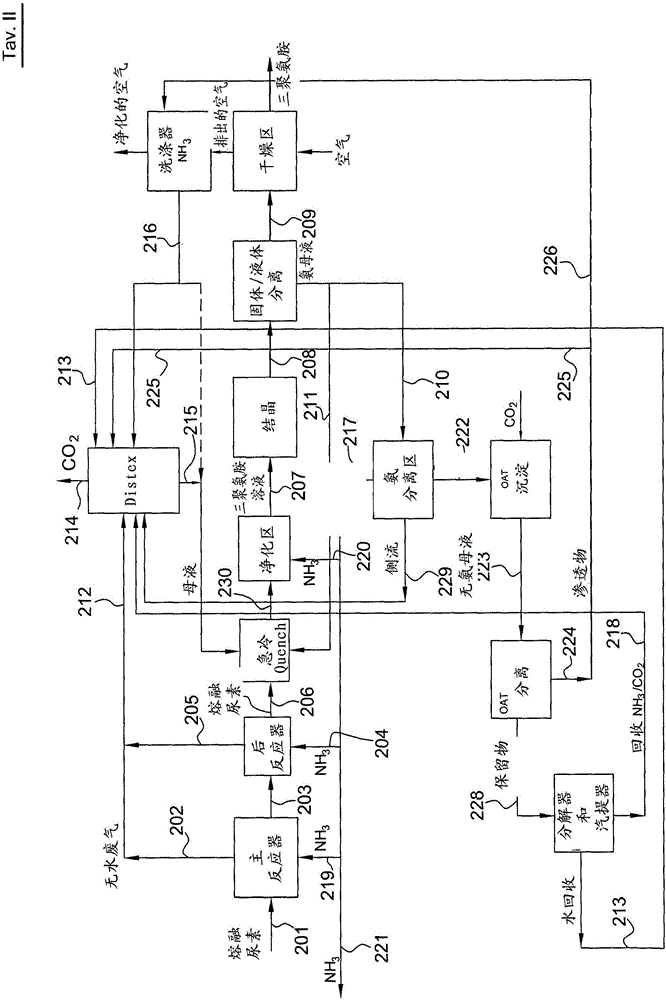
具体的,本发明涉及一种根据基于尿素的高压热解的合成方法,来生产高纯度三聚氰胺的方法,并且同时分离和完全回收在该方法的不同阶段所产生的高纯度NH3和CO2。在工业实践中,由尿素来生产三聚氰胺是在高温,在NH3存在下,在低压在合适的催化剂存在下,以及在高压在不存在催化剂时进行的。在两种情况中,尿素转化成三聚氰胺是根据以下总反应来进行的:6NH2CONH2→(CN)3(NH2)3+6NH3+3CO2(1)尿素三聚氰胺废气除了主产物(三聚氰胺)之外,还形成了NH3和CO2以及与之一起的更少的但非可忽略的量的本领域技术人员公知的副产物,在其中分别是氧-氨基-三嗪(OAT)和缩聚物,三聚氰胺热解和随后反应的中间产物。从总反应(1)的化学计量比,可以推断出供给到三聚氰胺合成方法的50%的摩尔数的尿素理论上被转化成NH3和CO2。因此,在离开合成反应器的流出物中存在着一定量的CO2和NH3(等于至少1.86kg/1kg所生产的三聚氰胺),以及三聚氰胺。归因于NH3的高经济价值,存在在全部三聚氰胺生产方法中回收这种反应副产物的问题。用于生产三聚氰胺的最广泛使用的方法之一是基于尿素的高压热解反应,并且在氨水溶液中回收和净化三聚氰胺。在这种方法中,离开合成反应器的流出物的组成为液相(其含有大部分所生产的三聚氰胺)和气态相(其含有大部分的NH3和CO2副产物)。离开反应器的全部流出物(气体和液体)在下文称作“急冷(Quench)”的具体设备中与来自于下游区域的含有CO2的氨水流接触。含有所生产的全部三聚氰胺的液体流离开该急冷(Quench)的底部,其在除去了所存在的CO2之后,用氨处理来除去缩聚物,反应副产物,将OAT保持在溶液中。来自于以上净化的溶液,通过结晶和随后干燥所分离的固体,获得了高纯度的三聚氰胺,并且滴定浓度高于99.8%。NH3和CO2的水饱和的气态流(湿废气)是从急冷(Quench)顶部萃取的。这种气态流通常再循环到尿素合成设备(尿素设备)来回收其中所含的NH3和CO2,因此通过它们(重新)转化成尿素而使得它们立即重新使用。确保上述气体的回收和再使用的经济便利性的不可或缺的条件是三聚氰胺设备是与尿素设备紧邻布置的。但是,离开急冷(Quench)的湿废气流中水的存在(通常高于20重量%)使得NH3和CO2在尿素设备中的重新使用是费力的,这导致首要的是当尿素设备的规模小于三聚氰胺设备时,三聚氰胺生产的总成本的增加。上述的现有技术的三聚氰胺生产方法在下文中是参考附图1和2来显示的,其显示了所述方法主运行阶段的简化方块图。在图1中,将来自于相邻尿素设备的熔融尿素流101与无水NH3的气态流114一起在135-140℃的温度供给到热解反应器(反应器)。该反应器是连续运行的,并且装备有加热系统,其为反应物混合物提供合成三聚氰胺所必需的热能,将反应环境保持在360-420℃的温度。反应压力保持在高于70bar的值。该反应器是单步反应器,并且该反应物混合物通过在尿素热解过程中所形成的气体保持在高循环。在上述运行条件下,热解反应产生了双相流出物,其组成为含有粗熔融三聚氰胺的液相(其包含减少量的未转化的尿素,和其他反应副产物(在其中,最大量是已经提及的缩聚物和氧-氨基-三嗪(OAT))和气态相(其基本组成为NH3和CO2)。将该双相流出物102送到急冷(Quench)(其位于所述反应器的紧下游),来回收三聚氰胺。在该急冷(Quench)中,双相流102与来自于设备其他区的含有CO2的氨水流103接触,并且它的温度降低到大约160℃。在这些条件下,将所述方法中形成的全部的三聚氰胺,未反应的尿素和杂质送入水溶液或者保持悬浮。将离开Quench的含水流104导向所述方法的随后阶段,而湿废气105(处于大约25bar的压力,基本组成为湿气饱和的NH3和CO2流)再循环到相邻的尿素设备。除了粗三聚氰胺之外,离开Quench的含水流104包含溶解的,相同量的NH3和CO2,其是在所述方法随后的步骤中,依靠水蒸气汽提(CO2-汽提器区)来除去的。CO2的除去对于帮助在随后的净化步骤中达到三聚氰胺的高纯度是必需的。气态流106离开CO2-汽提器的顶部,其与回收流113和124一起被送到吸收塔(NH3-CO2吸收器)。NH3-CO2吸收器允许在单个含水流103(其再循环到Quench)中全部回收上述流。没有CO2(和没有NH3)的含水流107(其含有在溶液中浓度为6-12重量%的三聚氰胺)与不可忽略量的OAT和缩聚物一起离开CO2-汽提器的底部。归因于它们的低溶解度,在含有三聚氰胺的含水流进行随后结晶阶段之前,必须除去该缩聚物。该缩聚物的除去是在净化区中进行的,这里在所加入的氨(流116)存在下将流107加热到大约170℃,直到达到12-15重量%浓度。在上述条件下,缩聚物几乎完全被转化成三聚氰胺。三聚氰胺的氨水流108(基本上不含缩聚物)离开净化区和供给到结晶区,在这里将流108的温度降低到40-50℃,因此允许大部分的三聚氰胺结晶。流108中NH3的存在将OAT保持在溶液中,使得高纯度三聚氰胺晶体沉淀。将含有悬浮的三聚氰胺晶体的流109送到固体/液体分离区,在其中分离了三聚氰胺的湿饼110和结晶母液的流111。流111用氨饱和并且包含全部的OAT,其是离开反应器的那些以及通过三聚氰胺在生产方法随后的步骤中水解所形成的那些二者。在水存在下,在高温下,在进行的方法步骤中,特别有利于OAT的形成。在干燥区中湿饼110最后依靠热空气来干燥,获得了高纯度产物,其三聚氰胺滴定浓度高于99.8%。用于干燥的排出的空气流112通过在NH3洗涤器中水洗来净化其中存在的NH3。将因此净化的空气排入环境中。通过NH3-CO2吸收器将含有所吸收的氨的含水清洗流113再循环到所述方法。将流111(由结晶母液组成,含有浓度为0.8-1.0重量%量级的三聚氰胺)送到氨分离区。在这个区域中,通过蒸馏分离了以下产物:无水NH3流115,其与加入的另外的无水NH3再循环到净化区;含有可能存在于母液111中的CO2的清洗流123;无NH3的含水流117(其基本上仅仅含有三聚氰胺和OAT)。将流117冷却到60-70℃的温度和通过加入CO2中和到pH7,来使得OAT沉淀。流118(其含有处于胶体悬浮的OAT)根据专利申请WO01/46159所述的内容,通过超滤在烛状陶瓷上进行了OAT的分离方法。在OAT超滤区中,OAT是作为保留物(流119)从渗透物相应的流120分离的。后者的流几乎没有OAT,并且再循环到急冷(Quench),来回收其中所含的残留三聚氰胺。保留物流119(几乎含有全部的OAT)在分解器-汽提器区中进行了热处理,在其中OAT,残留三聚氰胺和其中存在的全部其他有机物质几乎完全通过水解转化成NH3和CO2,并且形成了:-净化的含水流(121),其可以排入环境中:-富含NH3和CO2的湿流(122),其再循环到NH3-CO2吸收器。上述方法,即使目前应用于众多的化工厂,其特征在于高蒸气消耗和尿素向三聚氰胺的转化率远低于化学计量比值。此外,该方法受累于气态反应产物NH3和CO2的费力回收,其归因于相当大量的水存在于湿废气的流105中。实际上,再循环到相邻尿素设备的湿废气中存在的水导致了尿素生产成本的增加,其明显是通过三聚氰胺生产设备的管理来维持的。在过去已经面临这个问题,并且尝试寻找从来自于三聚氰胺合成方法的废气和副产物的混合物中分离NH3和CO2的方法,用于获得纯净气体,其可以再循环到尿素设备,可以存储和/或释放到环境中(CO2)。与现有技术(其也已经描述了CO2蒸馏来获得高纯度CO2的气态流(IT1387832,它的方法方案显示在附图2中))已知的内容相反,本申请人现在令人惊讶地发现特别的运行条件允许获得一种方法,用于由尿素来制备三聚氰胺,并且分离和回收高纯度CO2和NH3,其是改进的和优化的,以减少量的水来运行的,并且在能耗方面具有令人惊讶的结果。本发明的目标因此是克服目前的现有技术所揭示的缺点。本发明的一个目标实际上涉及一种由尿素生产三聚氰胺,并且分离和回收高纯度CO2和NH3的方法,包括以下运行步骤:a)在NH3存在下,通过热解熔融尿素流在主反应器中合成三聚氰胺,获得熔融粗三聚氰胺流和含有NH3和CO2的废气流;b)任选地,在气态氨存在下,在后反应器中处理离开主反应器的熔融粗三聚氰胺流,以完成尿素的热解反应,获得基本上不含未转化的尿素和CO2的熔融粗三聚氰胺流,和主要由NH3组成并且含有反应中形成的全部CO2的废气流;c)使来自于步骤a)的废气流,和如果存在时来自于步骤b)的废气流在含水萃取溶剂存在下蒸馏,获得高纯度CO2的气态流和含有CO2的氨水流;d)使来自于步骤c)的氨水流进行汽提以除去仍然存在的CO2;e)通过使获自步骤a)的熔融粗三聚氰胺流和当存在时来自步骤b)的熔融粗三聚氰胺流与来自步骤c)的氨水流接触,冷却和溶解获自步骤a)的熔融粗三聚氰胺流和当存在时来自步骤b)的熔融粗三聚氰胺流,获得含有溶解的三聚氰胺,缩聚物杂质和OAT的氨水溶液;f)通过在NH3存在下保持将缩聚物转化成三聚氰胺,以净化来自于步骤e)的三聚氰胺的氨水溶液;g)使离开步骤f)的净化的水溶液中存在的三聚氰胺结晶,并且使三聚氰胺晶体与所述溶液分离,获得三聚氰胺湿饼和含有仅仅OAT、溶解的三聚氰胺残留物和NH3的结晶母液流;h)蒸馏离开步骤g)的母液,获得高纯度NH3流和无氨的含水流,其含有OAT和三聚氰胺残留物,其随后在方法的专门的下游加工区,例如在分解器/汽提器区中,回收和/或除去;i)用热空气干燥来自于步骤g)的三聚氰胺湿饼,获得具有高纯度的干燥的三聚氰胺晶体和含有氨的排出空气流;所述方法要求用于来自于步骤a)的废气流和如果存在时来自于步骤b)的废气流的萃取蒸馏的步骤c)在含水萃取溶剂存在下,在55-250bar,优选70-170bar的压力下进行。含水萃取溶剂优选是水或者无氨的水溶液,甚至更优选是再循环的无氨的水溶液。含水萃取溶剂的存在量是3-6,优选4-5吨溶剂/1吨所生产的三聚氰胺。此外,萃取蒸馏步骤c)优选在分离装置(蒸馏塔或者Distex)中进行,其由适于经受住所需的运行条件的材料来生产,例如诸如基本组成为镍、铬和钼的组合的合金,或者金属例如锆、钛或者这样的材料的适合的组合。本发明的方法所以由一种生产三聚氰胺的方法组成,其对现有技术进行了增强和优化,其除了允许以相当大的产率增加和降低的成本来生产高纯度三聚氰胺之外,还允许-同时分离和回收在三聚氰胺的生产循环和净化中所产生/所用的高纯度CO2和NH3;-降低水的总用量和将它在三聚氰胺生产方法中完全再循环,和因此消除了液体排出;-CO2的萃取蒸馏在高压进行,其中使用所述压力允许直接蒸馏离开反应器和可能的离开高压三聚氰胺合成方法的后反应器的废气,而无需中间处理来将它们处于如现有技术的方法所述的萃取塔的运行压力(其在低于50bar的压力运行);-CO2的萃取蒸馏,其即使在高压进行,也具有减小的能耗,其可以甚至相对于低压运行时减半。此外,本发明方法的一个基本方面是设计来处理含有CO2和NH3的废气,来获得高纯度CO2和NH3,其中高纯度CO2的气态流在第一步骤中分离,并且高纯度NH3流在随后的步骤中分离。此外,在三聚氰胺的生产和净化循环中所产生的/所用的含有CO2和NH3的废气流(其是根据本发明的方法处理的)可以在同一设备(其中存在萃取性蒸馏塔)中产生,或者它们可以来自于其他三聚氰胺生产设备(通常称作高压或者低压设备,没有装备萃取塔或者Distex)的单个或多个组合。本发明的另一个目标涉及从来自于生产三聚氰胺的设备的废气中分离和回收高纯度CO2和NH3的特别的系统,所述系统包括以下元件:萃取CO2的第一蒸馏塔,其适于用含水萃取溶剂例如水来运行;第二分离塔,其适于从顶部回收离开第一萃取蒸馏塔底部的料流中存在的CO2和NH3;第三分离塔,其适于从顶部回收离开第二塔顶部的料流中存在的NH3,所述元件适于进行从所述废气中分离和回收高纯度CO2和NH3的料流的步骤。所述系统可用于修整现有的生产三聚氰胺的设备的情况中和/或用于集成现有的生产三聚氰胺的设备与生产尿素的设备。本发明系统目标例如可以用于分离和回收在由尿素来生产三聚氰胺的方法中所产生的高纯度CO2和NH3,包括前述运行步骤a)-i)。本发明提出的方法使用简单,但是相对于现有技术已知的方法来说发生了明显改变。附图说明图1是现有技术的三聚氰胺生产方法的图。图2是现有技术的三聚氰胺生产方法的图。图3是本发明的由尿素来合成三聚氰胺的方法的图。本发明的由尿素来合成三聚氰胺的方法以及来自于其的优点可以从下面的说明书而更清楚地理解,其参考了图3,其显示了一种优选的实施方案的主运行步骤的简化的方案。说明书和相关的方法方案应当被认为是本发明的示例,决不代表对于附加权利要求范围的限制。应当首先观察本发明下面的特有特征,即,不再限制尿素设备与三聚氰胺生产单元相邻,因为本发明的方法不再产生含有NH3和CO2的任何废气混合物(湿废气或者无水废气),仅仅归因于这种相邻,含有NH3和CO2的任何废气混合物的回收和传送到尿素设备才是经济上可行的。另外,在本发明方法的萃取蒸馏步骤中具体的压力条件允许获得一种优化的方法,其是以降低量的水来运行的,并且具有在能耗方面令人惊讶的结果。这些具体特征使得本发明的方法相对于迄今所用的和/或所提出的用于由尿素来生产三聚氰胺的全部高压技术是独特的。将熔融尿素流301供给到第一反应器(主反应器),其中高压热解方法在常规条件下进行,即在无水氨(流319)存在下,在360-420℃的温度和高于70bar的压力进行。与图2所示的现有技术的三聚氰胺生产方法相反,热解反应所产生的流出物的两种组分(即,由NH3和CO2组成的无水废气流302和由熔融粗三聚氰胺组成的液体流303)是分别从主反应器,或者从图3未示出的位于下游的合适的相分离器来萃取的,并且分别处理。在图3所示的本发明的实施方案中,将流303送到第二反应步骤(后反应器),在其中在与主反应器相同的温度和压力条件下和在无水氨的连续流(流304)存在下运行,完成了离开主反应器的流303中仍然存在的未反应的尿素的转化,同时完成了导致形成三聚氰胺的中间反应。同时,该后反应器中存在的条件(在其中氨分压远高于主反应器)也导致主反应器中所产生的熔融粗三聚氰胺中的缩聚物和OAT的减少。存在后反应器的另一有益效果是降低了液相(即,熔融粗三聚氰胺流)中存在的CO2的量,这也归因于连续进入的NH3气态流的汽提效应。但是,该方法的步骤b)是任选的。本发明的方法实际上允许生产高纯度三聚氰胺,以及无需后反应器的帮助,来分别回收NH3和CO2。两种分别的流也离开后反应器,都不含水:废气流305(主要由NH3组成)和液体流306(由熔融粗三聚氰胺组成,几乎不含尿素和CO2,含有非常有限量的高沸点副产物例如OAT和缩聚物)。离开后反应器或者来自于图3未示出的位于下游的合适的分离器的废气流305,与离开主反应器的废气流302合并,来在如下所述的特定萃取蒸馏塔(下文称作“Distex”)中处理。另一方面,通过溶解在氨水溶液中,将离开后反应器的熔融粗三聚氰胺流306送到三聚氰胺的回收步骤。这个步骤是在特定设备(下文称作“Quench”)中进行的,在其中熔融粗三聚氰胺流306在110-180℃,优选150-170℃的温度与主要由离开CO2汽提器的氨水流组成的氨水流(其含有显著浓度的NH3,但是几乎没有CO2)(流315a)接触。在这些条件下,缩聚物的初步破坏是在Quench设备中进行的。离开Quench的三聚氰胺溶液然后送到净化区(流330),用于缩聚物的完全破坏。离开Quench的含有三聚氰胺的水溶液330的净化是在本领域已知的压力和浓度条件下进行的,但是处于较低的温度。离开净化区的净化的三聚氰胺的氨水溶液307然后供给到结晶区,在这里类似于图2的现有技术的方法,该溶液的温度降低到40-50℃,获得极纯三聚氰胺晶体的分离。将含有悬浮的三聚氰胺晶体的流308送到固/液分离区,并且分离三聚氰胺的湿饼309和由结晶母液组成的含水流310。从干燥区中回收高纯度的无水结晶三聚氰胺(滴定浓度高于99.8重量%)。含有氨的结晶母液流310部分直接再循环到Quench(流310a)和部分供给到氨分离区(流310b),它的主要功能是回收全部的高纯度NH3。NH3在这个区中的分离是依靠蒸馏进行的,类似于现有技术的三聚氰胺生产方法。气态流312(其来源于两种无水废气流302和305的组合,这二者分别来自于主反应器和后反应器,并且用三聚氰胺蒸气饱和)在特定蒸馏塔(Distex)中,在选自水和无氨的水溶液的含水萃取溶剂存在下进行萃取蒸馏,所述含水萃取溶剂在塔中从顶部向下行进相对于上升的气态流逆流。该含水萃取溶剂优选是来自于分解器/汽提器区、来自于设备下游区域的再循环的无氨的水溶液(流313和325)。将由高纯度CO2组成的气态流314(NH3含量低于10ppm)在塔的运行压力下从Distex的顶部排出,而氨水流315(具有低含量的CO2,含有存在于流312中的三聚氰胺,其因此回收)从Distex的底部排出。将离开Distex的全部含水流315送到CO2汽提塔,用于从底部溶液中完全除去CO2,并且该底部溶液从这里送到Quench作为用于回收离开后反应器的三聚氰胺的溶剂。将来自于NH3洗涤器的流316(其含有氨,其已经作为湿三聚氰胺饼干燥的结果而形成)供给到Quench作为含水溶剂。纯NH3流320也供给到Quench来获得净化步骤所需的NH3浓度。因此,从净化区流向下游的氨水流307包含所述方法产生的全部NH3,即其来源于尿素热解(参见反应(1))和其来源于水解反应(特别是来自于下文所述的分解器/汽提器区)。流310b中所含的氨总量以高纯度(317)通过在氨分离区中蒸馏而分离。含有OAT和在溶液中溶解的三聚氰胺残留物的无氨的水流322也从氨分离区中分离。本发明的方法目标因此还允许在完全回收三聚氰胺生产方法中所产生的全部CO2(处于高纯度)之后,完全回收在三聚氰胺生产区中所产生的全部氨(处于高纯度)。形成流317的处于液态的纯NH3部分地用于所述生产方法的不同点,例如诸如主反应器(流319),后反应器(流304)和净化区(流320),而多余的NH3(其代表了最相关的部分)被传递到设备界区(batterylimitoftheplant)(流321),并且可以转移到尿素设备或者作为高商业价值的副产物来回收,其可以在其他工业方法中用作原材料。将作为氨分离区的底部产物排出的无氨的水流322送到分解器/汽提器区,在其中除了存在的其他有机分子之外,将OAT和残留三聚氰胺依靠高温热解来分解成氨和二氧化碳。将NH3和CO2在同一区域中通过汽提分离作为顶部产物和再循环(流318)到Distex,而将几乎纯净水流从底部回收,并且再循环到Distex作为萃取蒸馏(325)的溶剂或者送到洗涤器以清洗来自于干燥器(流313)或者干燥区的排出的空气。该干燥步骤可以实际上用热空气或者本领域技术人员已知的其他手段来进行。可能存在于流310(结晶母液)中的少量CO2是在氨分离区中以CO2的氨水混合物的形式分离,如现有技术已知的,并且传送(清洗流329)到Distex来回收它们。在生产循环中所形成的全部CO2(通过热解和水解)然后以高纯度下在Distex中作为顶部产物分离,并且在设备界区,在70-170bar的优选压力下可利用(流314)。类似于NH3,CO2也可以转移到尿素设备或者作为原材料回收,用于其他工业方法中。根据本文所示的实施方案,用于由尿素来生产三聚氰胺,并且分离回收高纯度副产物氨和二氧化碳的方法,包括以下基本操作步骤:-将离开三聚氰胺合成反应器的废气流在萃取蒸馏塔中,使用水作为萃取溶剂或者水溶液进行蒸馏,和优选以3-6,优选4-5吨溶剂/吨三聚氰胺的量回收含水流,并且在55-250bar,优选70-170bar的压力下运行,获得高纯度CO2气态流和氨水流,用于回收和净化在所述反应中所生产的三聚氰胺,并且特别地降低了能耗。由结晶下游的固/液分离步骤所形成的氨水流然后蒸馏,获得高纯度氨流和无氨的水流,其含有残留三聚氰胺,OAT和其他少量有机杂质(送去回收或者除去)。在本发明方法的一种优选的实施方案中,所回收的高纯度NH3和CO2流合适地分别供给到尿素设备,相对于包含在废气流中、但是没有分离的这些物质的供料流具有特别的优点。可选择地,上述流之一或者二者适于用作其他工业生产方法中的原材料。本发明所以涉及一种新的循环,以在三聚氰胺生产方法中,通过尿素热解,来获得高纯度NH3和CO2的分离和回收,所述循环包括:-由主反应器和后反应器组成的反应区,其中进行热解,并且尿素高转化成三聚氰胺,并且分离了由NH3、CO2和三聚氰胺蒸气组成的无水废气流;-萃取蒸馏塔(Distex),其连接到所述反应区上,并且从该反应区接收所述废气流,所述Distex优选使用来自于三聚氰胺的回收和净化循环的无氨的水溶液作为萃取溶剂,分离了由高纯度CO2组成的顶部产物和含有NH3和残留三聚氰胺的含水底部流;该高纯度CO2流是在优选的压力70-170bar(即,在与它离开反应器时相同的压力)下蒸馏的,而无需任何中间处理;汽提区,用于从无氨的水溶液中除去残留CO2;-Quench区和净化区,用于依靠来自于所述生产循环,可能加入了NH3的氨水流来回收和净化三聚氰胺;-净化的三聚氰胺的结晶沉淀区,其连接到产物的分离和干燥区;-氨分离区,由结晶母液来通过蒸馏生产高纯度氨,用于所述循环的内部所需,多余的NH3以高纯度传递到界区,来转移到尿素设备或者用于市场销售;-其用于处理离开氨分离区的无氨的母液的区域,由此进行对包含在其中的三聚氰胺的合适的回收,和/或热破坏所存在的全部其他有机物质,并且全部回收所形成的NH3和CO2;来源于这个作业系列的含水流形成了Distex的大部分萃取溶剂需求。本发明的目标,通过高压热解尿素来生产高纯度三聚氰胺的方法允许相对于现有技术已知的方法来获得下面的优点:1)以高纯度和分别地完全回收在三聚氰胺合成反应(反应(1))中所产生的或者在三聚氰胺的回收和净化循环中形成的气态副产物CO2和NH3。相对于现有技术已知的废气(湿的或者无水)再循环到尿素设备的实践,作为本发明目标的CO2和NH3的新回收模式能够解决与现有技术实践运行相关的全部问题。作为传统的废气流再循环的替代选项,将高纯度NH3和CO2分别再循环到尿素设备,其导致了:a)CO2到尿素的各途径转化率(conversionforeachpassage)相当大的增加,和因此以相同的投资获得了增加了生产能力,和降低了尿素的生产成本;b)显著降低了运行尿素设备所必需的能耗例如蒸气和/或电能,另外还相当大地改进了来自于相同尿素设备的能量回收模式;c)供料流到尿素设备的压缩成本的降低,特别是CO2,其是在三聚氰胺设备的界区,在优选的压力70-170bar下可利用的;d)中间处理成本的降低,其将离开三聚氰胺反应器的废气带到压力低于50bar,在此蒸馏塔根据现有技术运行;e)在再循环中所涉及的装置和生产线较少的腐蚀问题;f)尿素合成方法的整体改进的运行可靠性和可利用性;2)本发明的生产三聚氰胺的方法不需要供给另外的NH3和CO2流。该方法要求实际上是通过将在不同的方法步骤副产的和回收的NH3部分地再使用/再循环而集成的和专门满足的;3)通过水解三聚氰胺所形成的OAT减少,这不仅归因于降低了高温运行装置的数目和体积的效果,而且还是作为温度本身降低的结果。该净化实际上可以在比现有技术低了5-10度的温度下进行。除了作为尿素的更高转化率(归因于后反应器的插入)的结果而获得的产率提高之外,这导致了所述方法总产率的进一步增加;4)在生产尿素之外的工业方法中使用NH3和CO2二者的可能性;因为两种化合物是以高纯度和分别回收的,它们可用于不同的用途和具有可能更高的附加值;5)水的总用量减少,并且它完全再循环到三聚氰胺的生产方法,结果是消除了液体排出;6)CO2的萃取蒸馏虽然在高压进行,但是具有降低的能耗;7)本发明的三聚氰胺生产方法可以与在任何已知技术的现有尿素设备中进行的生产尿素的方法相结合,这明显降低了停机时间和用于所述设备现代化和改造所必需的介入性技术改变。下文提供了本发明方法的一种实施例子,用于本发明的说明性和非限定性目的。实施例1在根据本发明所构建的生产高纯度三聚氰胺的设备中,如图3所示,将熔融尿素流301以流速22650kg/h与1500kg/h量的无水氨流319一起送到主反应器。然后将离开主反应器的液体流303送到随后的后反应器,在这里在几乎没有CO2的环境中完成了三聚氰胺的合成反应,这也归因于通过在底部上连续引入的1600kg/h的气态NH3流304的汽提效应。然后从该后反应器中获得液体流出物(流306),其等于7600kg/h的粗三聚氰胺,含有减少量的OAT和缩聚物(分别是0.6和1.0重量%)。两个反应器都是在380℃的温度和80bar的压力下运行的。将由三聚氰胺蒸气饱和的NH3和CO2所组成的气相302和305从所述两个反应器中分离,并且合成单个流312,将其送到萃取蒸馏塔(Distex),用于三聚氰胺回收和高纯度CO2分离。该Distex是在压力75bar下使用的,采用来自于随后的运行阶段的30000kg/h的含水流325作为萃取溶剂。具体的,相对于同等方法(在其中Distex中的蒸馏是在压力35bar进行的),用作本发明方法中的萃取溶剂的含水流的量小于280%。8950kg/h的极纯的和基本上无水的CO2(并且NH3含量低于10ppm)从Distex顶部分离,形成气态流314,其在界区在75bar压力下是可用的。从Distex底部排出的含水流315包含了与流318,325和329一起进入所述方法的全部的氨和三聚氰胺,并且具有极小量的残留CO2。将含水流315送到CO2汽提器来从该含有氨和三聚氰胺的含水流中全部除去CO2。将塔顶部的流(315b,其含有流315全部的CO2和部分的氨)送到氨的分离区;将底部流315a送到Quench,来回收来自于后反应器的粗三聚氰胺(306流)。将离开Quench的全部产物(流330)送到净化区,其在压力25bar和温度165℃运行。将等于9000kg/h量的另外的氨(流320)加入净化区来获得缩聚物向三聚氰胺的完全转化。将净化的三聚氰胺的含水流307(其含有小于100ppm的缩聚物)冷却到40-50℃,并且在结晶区中减压至大气压,在其中获得了三聚氰胺晶体沉淀。三聚氰胺晶体在母液中的悬浮液(流308)然后从结晶器送到离心机滗析器,因此将湿晶体饼与结晶母液分离。该饼然后在特定干燥区中干燥,生产了7500kg/h的无水三聚氰胺,其具有高纯度(滴定浓度高于99.8重量%和湿度低于0.1重量%)。离开离心机滗析器的结晶母液的流310然后送到氨分离区,这里在20bar压力下运行,回收了18800kg/h的极纯氨,并且其部分地用于同一生产三聚氰胺的方法(流304,319和320)和大部分作为设备的副产物在界区可利用(流321)(6700kg/h的液态NH3)。在氨分离区底部所产生的流322由71000kg/h的无氨的母液组成。流322包含了在设备上游区域所产生的全部OAT,并且在结晶条件下用三聚氰胺饱和(大约0.8-1.0重量%)。将流322送到所述设备的最后区(分解器/汽提器)用于通过OAT的高温水解来破坏残留三聚氰胺和其他有机副产物。流322实际上首先加热到280℃,然后送到分解器/汽提器区,在这里全部的有机材料(OAT,三聚氰胺,其他副产物)通过水解被破坏和转化成NH3和CO2,在这些气体在汽提器中分离之后留下几乎纯净的含水流(流313)作为液体残留物,其含有小于100ppm的总固体产物和小于10ppm的游离NH3,将其用于清洗在洗涤器中所排出的空气流。在分解器中形成的气体和在同一区的汽提器顶部所分离的那些(流318)在Distex中进行了萃取蒸馏,来回收CO2和然后回收NH3。将离开分解器的部分的无氨的含水流用作Distex的萃取溶剂。该生产方法的总产率被证实等于0.33kg的三聚氰胺/1kg尿素,其对应于3.02kg尿素/1kg所生产的高纯度三聚氰胺的特定消耗。以下流也获自所述方法:-纯度高于99.9%(基于湿物)和在75bar压力下的CO2流,其量等于0.395kg/1kg所消耗的尿素;-无水和液体NH3流,滴定浓度是99.9%,其量是0.296kg/1kg所消耗的尿素。此外,相对于同等方法(在其中Distex中的蒸馏是在35bar压力下进行的,并且萃取溶剂的量等于85000kg/h),本发明方法的能量平衡如下:实施例2用下面的Distex运行压力来重复实施例1所述的方法:-55bar-170bar。在下表1中,在这些压力所测量的值还与根据WO01/46159的教导在35bar和根据实施例1在75bar下进行的的测试过程中所测量的相应的值进行了比较。表1压力355575170bar吸收到Distex的水流速(流325)85000575003000011250kg/h液体流318流速4200420042004200kg/hDistex所需蒸气的小时流速2300016500990013000kg/hCO2汽提器所需蒸气的小时流速1200011500107004700kg/h上表所示结果显示了相对于根据WO01/46159的教导在35bar进行的Distex,在用Distex在55bar,75bar和170bar进行的方法的情况中,总蒸气消耗的如下减少:55bar=-4000kg/h75bar=-14400kg/h170bar=-17300kg/h此外,在能量平衡中,为了还考虑在较高的压力将溶剂和再循环流引入萃取性蒸馏塔的能耗,测量了表2所示的值。表2表2的内容显示了甚至考虑为了达到萃取蒸馏塔中更高的压力所消耗的能量时,相对于根据WO01/46159的教导在35bar进行的Distex,在用Distex在55bar,75bar和170bar进行的本发明的方法的情况中,也获得了蒸气总消耗的相当大的减少。当前第1页1 2 3