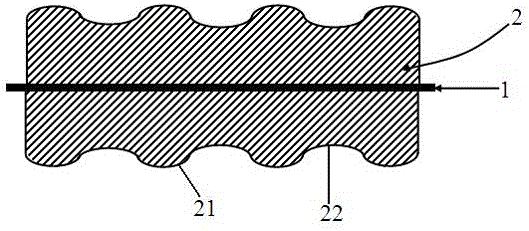
本发明属于锂离子电池技术领域,尤其涉及一种锂离子电池极片及包含该极片的锂离子电池。
背景技术:锂离子电池充放电引起的阳极膨胀积累到一定程度后会产生电芯外观变形,在裸电芯内部形成空隙,导致电解液量不足,从而诱发电池的电化学性能的连锁性恶化,缩短锂离子电池的使用寿命。为了抑制阳极膨胀,可以采用粘结力较强的粘结剂以束缚石墨颗粒在嵌锂后的体积膨胀;或者通过在极片或隔离膜的表面涂覆具有粘接作用的涂层,将阳极极片和隔离膜牢固地粘接在一起,以增强其抵抗变形的能力。此外,还有通过采用高强度的刚性外壳来限制阳极膨胀的方法。上述方法虽然可以从一定程度上缓解阳极膨胀引起的不利影响,但是其关注点为阳极极片,对于锂离子电池卷绕结构的另一重要组成部分阴极极片没有考虑;另外,使用高粘结性粘接剂易导致极片变脆,不利于后续的卷绕工艺;在隔离膜表面增加具有粘接作用的涂层则导致成本增加。现有技术中的极片(包括阴极极片和阳极极片)的断面结构示意图如图1所示,其包括集流体10和涂覆在集流体10表面的活性物质层20,其中,活性物质层20的表面是平整光滑的,将阴极极片、隔离膜和阳极极片卷绕成裸电芯并组装成电池时,阳极极片容易发生膨胀,而与其相对的阴极极片又无法对其进行限制,最终导致整个裸电芯的膨胀。有鉴于此,确有必要提供一种锂离子电池极片及包含该极片的锂离子电池,该极片是基于锂离子电池裸电芯的卷绕结构的特点而设计的具有突起部和凹陷部的极片,这种结构的极片能够抑制阳极膨胀导致的电芯变形及电化学性能劣化,提高电池的循环寿命。
技术实现要素:本发明的目的之一在于:针对现有技术的不足,而提供一种锂离子电池极片,该极片是基于锂离子电池裸电芯的卷绕结构的特点而设计的具有突起部和凹陷部的极片,这种结构的极片能够抑制阳极膨胀导致的电芯变形及电化学性能劣化,提高电池的循环寿命。为了达到上述目的,本发明采用如下技术方案:一种锂离子电池极片,所述极片包括集流体和设置在所述集流体表面的活性物质层,所述活性物质层上设置有若干个凸起部和凹陷部。作为本发明锂离子电池极片的一种改进,所述凸起部和所述凹陷部间隔地分布于所述活性物质层。作为本发明锂离子电池极片的一种改进,所述凸起部和所述凹陷部沿所述活性物质层的宽度方向间隔分布。作为本发明锂离子电池极片的一种改进,相邻两个所述凸起部之间的距离与相邻两个所述凹陷部之间的距离相等。作为本发明锂离子电池极片的一种改进,所述凸起部的高度和所述凹陷部的深度均为所述活性物质层的厚度的1/20~1/50。凸起部的高度和凹陷部的深度(或称之为起伏幅度)太小则不容易在阴极极片和阳极极片之间形成较为紧密的“互锁”结构,无法实现调控阳极极片膨胀所产生的应力的作用;起伏幅度太大则容易形成压实密度过大的区域,导致极片表面层的压实密度差异过大,容易在大电流充充电及低温充电时产生阳极析锂问题,影响电池的安全性能。作为本发明锂离子电池极片的一种改进,所述凸起部的高度和所述凹陷部的深度均为所述活性物质层的厚度的1/20~1/30,这是优选的范围。作为本发明锂离子电池极片的一种改进,所述凸起部的长度和所述凹陷部的长度均为所述活性物质层的宽度的1/5~1/15。凸起部和凹陷部的长度太小,则不利于卷绕时的工序控制,凸起部和凹陷部的长度太长则不利于形成紧密配合的“互锁”结构。作为本发明锂离子电池极片的一种改进,所述凸起部的长度和所述凹陷部的长度均为所述活性物质层的宽度的1/10,这是优选的范围。作为本发明锂离子电池极片的一种改进,所述凸起部和所述凹陷部的横截面的形状均为圆形、椭圆形、长方形或菱形。相对于现有技术,本发明基于锂离子电池裸电芯的卷绕结构特点,通过在极片的活性物质层上设置凸起部和凹陷部,从而形成一种独特的具有“起伏结构”的极片(包括阴极极片和阳极极片),当将该阴极极片和阳极极片与隔离膜卷绕成裸电芯时,阴极极片和阳极极片能够形成“互锁”结构。将该裸电芯组装成电池后,在电池的使用过程中,当阳极极片发生体积膨胀时,由于与其相对的阴极极片基本保持原有形状不变,从而可以限制和诱导阳极极片的膨胀,从而降低阳极膨胀的程度和无规律性。从结构上看,锂离子电池中整条阳极极片的宏观膨胀被化整为零地分解成若干微小的膨胀区域,每个微小的膨胀区域受到最近邻的阴极极片的“起伏结构”的限制,使得其无法从宏观上形成较大的累积作用。因此,本发明的极片可以有效抑制由于阳极膨胀所导致的电池外观变形和后续电池性能恶化的问题,对于提高锂离子电池的品质和使用寿命具有重要的意义。本发明的极片可应用于软包装锂离子电池、硬包装锂离子电池和圆柱型锂离子电池。而且,本发明的极片对于膨胀较为严重的合金阳极的商业化应用具有重要的价值。本发明的另一个目的在于提供一种锂离子电池,包括阴极极片、阳极极片、设置于所述阴极极片和所述阳极极片之间的隔离膜以及电解液,所述阴极极片和所述阳极极片均为本发明所述的锂离子电池极片,并且所述阴极极片的凹陷部与所述阳极极片的凸起部相对设置,所述阴极极片的凸起部与所述阳极极片的凹陷部相对设置。相对于现有技术,本发明通过均具有“起伏结构”的阴极极片和阳极极片的配合使用,充分利用阴极极片表面的“起伏结构”在电化学过程中保持原有形状基本不变的特点,对同样具有表面“起伏结构”的阳极极片的嵌锂膨胀产生牵制、调整和诱导作用。从结构上看,锂离子电池中整条阳极极片的宏观膨胀被化整为零地分解成若干微小的膨胀区域,每个微小的膨胀区域受到最近邻的阴极极片的起伏结构的限制,使得其无法从宏观上形成较大的累积作用。因此,本发明提出的表面互锁结构可以有效抑制由于阳极膨胀所导致的电池外观变形和后续电池性能恶化的问题,对于提高锂离子电池的品质和使用寿命具有重要的意义。此外,本发明的阴极极片和阳极极片上凸起部和凹陷部的设置使得极片上形成了多个宽度较窄的次级通道,在电解液注液过程中,电解液与极片的接触面积增加,有利于电解液通过毛细作用迅速填满阳极极片、阴极极片和隔离膜之间的空隙,从而可以缩短注液后的静置时间,提高注液效率和裸电芯在电解液中的浸润效果,有利于形成均匀、一致的SEI膜,提高电芯容量的一致性。附图说明图1为现有技术中的锂离子电池极片的断面结构示意图。其中10-集流体,20-活性物质层。图2为本发明提供的锂离子电池极片的断面结构示意图。图3为本发明中的阴极极片与阳极极片和隔离膜卷绕成的电芯的断面结构示意图。其中,1-集流体,2-活性物质层,21-凸起部,22-凹陷部,30-阴极极片,40-阳极极片,50-隔离膜。图4为实施例6和对比例2提供的电池在满充和循环测试过程中的厚度变化趋势。图5为实施例6和对比例2提供的电池在循环测试过程中的厚度增加百分比,以满充厚度为基准。具体实施方式为了使本发明的目的、技术方案和有益技术效果更加清晰,以下结合附图和具体实施方式,对本发明作进一步详细说明。应当理解的是,本说明书中所描述的具体实施方式仅仅是为了解释本发明,并不是为了限定本发明。本发明提供了一种锂离子电池极片。实施例1,如图2所示,本实施例提供的一种锂离子电池极片,该极片包括集流体1和设置在集流体1表面的活性物质层2,活性物质层2上设置有若干个凸起部21和凹陷部22。该凸起部21和凹陷部22间隔地分布于活性物质层2的宽度方向上,并且两个相邻的凸起部21之间的距离与两个相邻的凹陷部22之间的距离相等,凸起部21的高度和凹陷部22的深度均为活性物质层2的厚度的1/30,凸起部21的长度和凹陷部22的长度均为活性物质层2的宽度的1/10,凸起部21和凹陷部22的横截面的形状均为圆形。实施例2,与实施例1不同的是:凸起部21的高度和凹陷部22的深度均为活性物质层2的厚度的1/40,凸起部21的长度和凹陷部22的长度均为活性物质层2的宽度的1/7,凸起部21和凹陷部22的横截面的形状均为椭圆形。其余同实施例1,这里不再赘述。实施例3,与实施例1不同的是:凸起部21的高度和凹陷部22的深度均为活性物质层2的厚度的1/50,凸起部21的长度和凹陷部22的长度均为活性物质层2的宽度的1/15,凸起部21和凹陷部22的横截面的形状均为长方形。其余同实施例1,这里不再赘述。实施例4,与实施例1不同的是:凸起部21的高度和凹陷部22的深度均为活性物质层2的厚度的1/20,凸起部21的长度和凹陷部22的长度均为活性物质层2的宽度的1/5,凸起部21和凹陷部22的横截面的形状均为菱形。其余同实施例1,这里不再赘述。实施例5,与实施例1不同的是:凸起部21的高度和凹陷部22的深度均为活性物质层2的厚度的1/25,凸起部21的长度和凹陷部22的长度均为活性物质层2的宽度的1/12,凸起部21和凹陷部22的横截面的形状均为圆形。其余同实施例1,这里不再赘述。本发明锂离子电池的极片采用的是常规的生产和制造方法,不同之处在于碾压工艺:采用表面具有凸起部和凹陷部的碾压辊,对干燥后的极片进行碾压处理,使得经过碾压的极片表面具有相应的凸起部21和凹陷部22。凸起部21和凹陷部22的长度分别由碾压辊表面的凹陷部和凸起部的长度决定,凸起部21的高度和凹陷部22的深度分别由年压辊表面的凹陷部的深度和凸起部的高度决定。对比例1,本对比例提供的锂离子电池的极片的断面结构示意图如图1所示,其包括集流体10和涂覆在集流体10表面的活性物质层20,其中,活性物质层20的表面是平整光滑的。本发明还提供了一种锂离子电池。实施例6,本实施例提供的锂离子电池包括阴极极片30、阳极极片40、设置于阴极极片30和阳极极片40之间的隔离膜50以及电解液,其中,阴极极片30和阳极极片40均为实施例1提供的锂离子电池极片,并且阴极极片30的凹陷部22与阳极极片40的凸起部21相对设置,阴极极片30的凸起部21与阳极极片40的凹陷部22相对设置。将阴极极片30与阳极极片40和隔离膜50卷绕成的电芯的断面结构示意图如图3所示,由于阴极极片30和阳极极片40的结构参数相互匹配,因此,采用该阴极极片30和阳极极片40以及隔离膜50卷绕而形成的电芯中,阴极极片30与阳极极片40紧密地贴合在隔离膜50的两侧。实施例7,与实施例6不同的是:本实施例提供的锂离子电池的阴极极片30和阳极极片40均为实施例2提供的锂离子电池极片。其余同实施例6,这里不再赘述。实施例8,与实施例6不同的是:本实施例提供的锂离子电池的阴极极片30和阳极极片40均为实施例3提供的锂离子电池极片。其余同实施例6,这里不再赘述。实施例9,与实施例6不同的是:本实施例提供的锂离子电池的阴极极片30和阳极极片40均为实施例4提供的锂离子电池极片。其余同实施例6,这里不再赘述。实施例10,与实施例6不同的是:本实施例提供的锂离子电池的阴极极片30和阳极极片40均为实施例5提供的锂离子电池极片。其余同实施例6,这里不再赘述。其中,本发明所说的锂离子电池既可以是软包装锂离子电池,又可以是硬包装锂离子电池和圆柱型锂离子电池。阳极极片40中的阳极活性物质既可以是石墨,也可以是硅合金、锡合金等,或者是石墨和硅合金、锡合金的混合物等。对比例2,与实施例6不同的是:本实施例提供的锂离子电池的阴极极片和阳极极片均为对比例1提供的锂离子电池极片。其余同实施例6,这里不再赘述。将实施例6-10和对比例2提供的电池在低温下(-12oC)满充后,在干燥房中拆解,结果发现:实施例6-10的电池中的阳极极片40的析锂程度与对比例2提供的电池中的阳极极片的析锂程度十分接近,尤其是在实施例6-10的电池中的阳极极片40的凹陷部22,即压实密度相对较大的部分,其析锂程度并没有变严重,这表明本发明提供的锂离子电池的安全性能并没有因为极片结构的改变而受到影响。对实施例6-10和对比例2提供的电池进行电化学容量测试,结果表明实施例的电池的容量与对比例的电池的容量没有明显差异。这表明本发明提供的锂离子电池的容量性能并没有因为极片结构的改变而受到影响。对实施例6和对比例2提供的电池进行电化学容量循环测试,并在每100次循环测试后测量电芯的厚度,结果如图4所示,同时计算电池在容量循环测试过程中的厚度增加百分比(以满充时的电池厚度为基准),所得结果如图5所示。由图4和5可以看出:在不改变阴极极片30和阳极极片40的涂布重量的条件下,实施例6提供的电池的初始厚度要略大于对比例2提供的电池;但是经过200次循环测试后,实施例6提供的电池的厚度小于对比例2提供的电池,且该趋势随着循环测试次数进一步增加越发明显:实施例6提供的电池的厚度在600次循环测试后没有明显增加,而且随着循环测试次数的增加,实施例6提供的电池的厚度增加趋于稳定。经过600次容量循环测试后,实施例6的电池的厚度增加只有5%左右,远低于对比例2提供电池的30%左右的厚度增加。该结果表明:本发明提供的锂离子电池在抑制阳极膨胀方面具有明显的效果,其可以抑制阳极膨胀所产生的不利影响,对于防止电芯变形具有重要的作用。需要说明的是:本发明的实施例中虽然仅给出了凸起部21和凹陷部22间隔地分布于活性物质层2上的例子,但凸起部21和凹陷部22还可以以凸起部21-凸起部21-凹陷部22-凹陷部22-凸起部21之类的分布形式分布在活性物质层2上;本发明的实施例中虽然仅给出了凸起部21和凹陷部22间隔地分布于活性物质层2的宽度方向上的例子,但凸起部21和凹陷部22还可以间隔地分布于活性物质层2的长度方向上;本发明的实施例中虽然仅给出了两个相邻的凸起部21之间的距离与两个相邻的凹陷部22之间的距离相等的例子,但是两个相邻的凸起部21之间的距离与两个相邻的凹陷部22之间的距离也可以不相等。只要保证在将阴极极片30、隔离膜50和阳极极片40卷绕成电芯时,阴极极片30上的凸起部21正对的是阳极极片40上的凹陷部,阴极极片30上的凹陷部22正对的是阳极极片40上的凸起部30即可。还需要说明的是:本发明提供的极片结构可以广泛应用于锂离子电池电极极片的设计与生产,但是不限于锂离子电池电极极片的设计与生产,对于熟知本领域的技术人员而言,本发明同样适用于需要对控制膨胀和由于膨胀而引起的性能恶化的其它相关领域。根据上述说明书的描述和指示,本发明所属领域的技术人员还可以对上述实施方式进行适当的变更和修改。因此,本发明并不局限于上面描述和指示的具体实施方式,对本发明的一些修改和变更也应当纳入本发明的权利要求的保护范围内。此外,尽管本说明书中使用了一些特定的术语,但这些术语只是为了方便说明,并不对本发明构成任何限制。