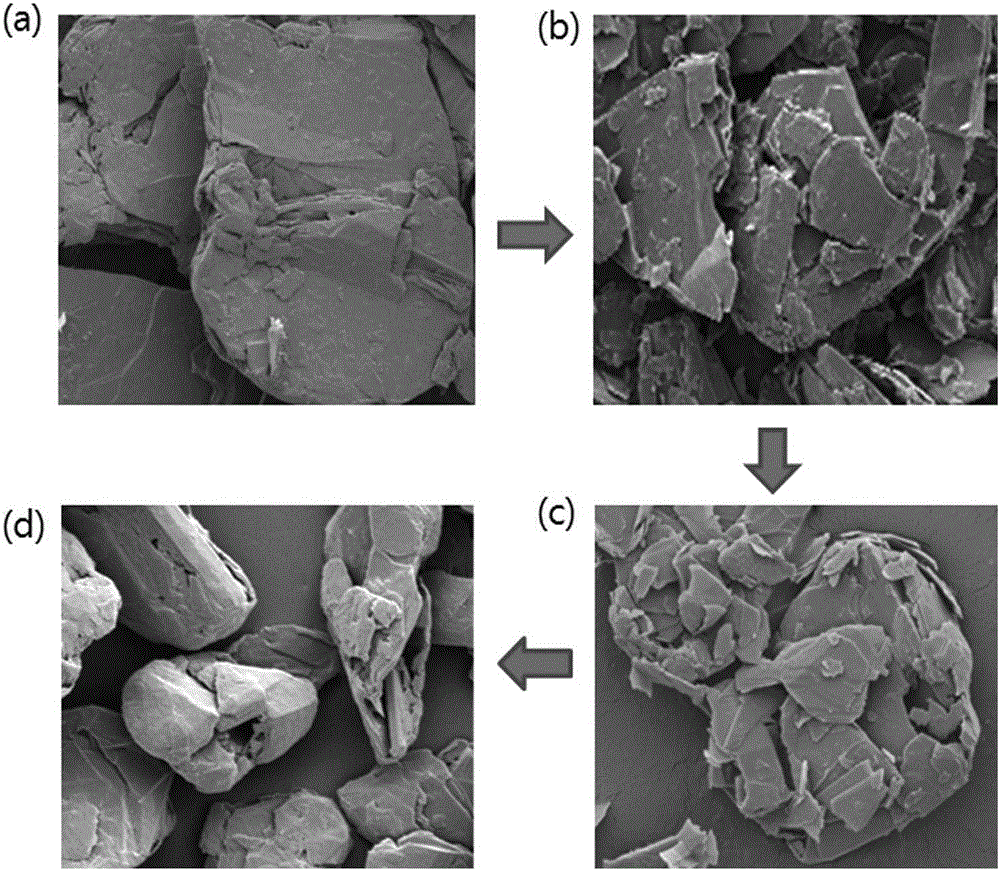
本发明涉及锂二次电池用阴极活性物质的制造方法及由其制造的阴极活性物质,所述锂二次电池用阴极活性物质的制造方法能够改善阴极活性物质的取向性,从而在应用于二次电池时,表现出稳定的循环特性,并且有效减小电极的膨胀率。
背景技术:
:近年来,随着电子设备的小型化,实际情况是需要高容量的二次电池,尤其,与镍镉电池、镍氢电池相比,能量密度高的锂二次电池正受到关注。作为这样的锂二次电池的阴极材料,起初使用了锂金属,然而,目前使用能够防止产生锂枝晶的碳系材料。用作电极活性物质的碳材料大体分为结晶系石墨和非晶系石墨原料。作为结晶系石墨材料,通常可以举出人造石墨、天然石墨和集结(kish)石墨等例子,此外,作为非晶系碳原料,有软碳(softcarbon)、硬碳(hardcarbon)等,所述软碳是在高温下将煤炭系沥青或石油系沥青烧成而得到,所述硬碳是将苯酚树脂等高分子树脂烧成而得倒。当从粒子形状方面观察上述石墨材料时,对于球形石墨的情况而言,由于材料的各向异性低,因此利于维持电压和电流分布的均匀性,相反,在将片状(鳞片状)的石墨用作锂2次电池用阴极材料的情况下,由于材料本身的各向异性,之后在与溶剂或粘合剂混合并进行浆料化的过程中,会因流动性降低而使加工性变差,从而难以形成规定厚度的涂覆层,产生剥离现象等问题。此外,粒子形态的缺点所导致的低密度和比表面积增加,可能会使电池内部的电压和电流分布变得不平衡。因此际情况是,从所使用的各材料的占有率方面考虑,实目前为止仍然最优选球形粒子。以往,利用机械粉碎方法使片状高集结石墨质材料球状化并将球形的粒子主要用作阴极材料。机械粉碎而成的球形的石墨粒子与单轴排列的片状粒子相 比,取向性提高而可期待电极的膨胀率减小。然而,近年来,随着移动IT设备变薄,期待进入内部的电池的厚度膨胀率也进一步降低,因此,实际情况是,与单纯球状化的粒子相比,需要具有更低膨胀率的阴极活性物质。技术实现要素:所要解决的课题本发明为了解决如上所述的问题而提出,其目的在于,提供锂二次电池用阴极活性物质的制造方法和利用上述方法制造的低膨胀性阴极活性物质,在所述锂二次电池用阴极活性物质的制造方法中,由于认识到电池的厚度膨胀率主要来源于阴极,因此相比于以往球状化的碳材料阴极活性物质,将取向指数调整至特定范围,从而在应用于电池时能够表现出电极的低膨胀率特性。解决课题的方法为了实现上述目的,本发明提供一种阴极活性物质的制造方法,其包括:步骤(i),对片状石墨质材料施加机械外力,形成上述石墨质材料的边缘部(edge)的一部分或全部发生折弯或具有变皱的形状的1次粒子;步骤(ii),用非晶碳前体涂覆上述1次粒子;及步骤(iii),对上述步骤(ii)中涂覆的非晶碳前体在其碳化温度以上的温度下进行热处理而造粒。此外,本发明提供一种阴极活性物质的制造方法,其包括:步骤(i),对球状化的石墨粒子施加机械外力,形成在上述粒子内进行结球的片状石墨切片的一部分或全部发生不规则层间剥离(exfoliate)或具有破碎的形状的1次粒子;步骤(ii),用非晶碳前体涂覆上述1次粒子;及步骤(iii),对上述步骤(ii)中涂覆的非晶碳前体在其碳化温度以上的温度下进行热处理而造粒。此外,本发明提供利用上述方法制造的锂二次电池用阴极活性物质。更具体而言,优选上述阴极活性物质包含(a)一种以上的无定形石墨1次粒子、和(b)在上述1次粒子表面的一部分或全部形成的非晶碳层,具有借助于上述非晶碳层使1次粒子造粒而成的2次粒子结构,并且在上述2次粒子结构内包含孔隙。根据本发明的优选的例子,上述阴极活性物质的(002)晶面的X射线衍射强度[I(002)]与(110)晶面的X射线衍射强度[I(110)]之比所表示的取向指数[I(002)/I(110)]可以为50至110的范围。其中,上述阴极活性物质的振实密度可以为0.5至0.8g/cc,平均粒径可以为10至30μm。发明效果在本发明中,通过将片状石墨质材料弄皱而使其具有规定的形状,或者利用球状化的石墨粒子使粒子内片状切片剥离或实施裂开的加工工序,相比于以往球状化的碳材料,能够改善阴极活性物质的取向性。由此,在将上述阴极活性物质应用于电池的情况下,能够确保电池的低膨胀率和长寿命特性,因此能够有效地用作超薄型移动IT设备的电极材料。附图说明图1是分别显示以往平板石墨质材料和本申请实施例1中制造的阴极活性物质的形状的扫描电子显微镜(SEM)照片。图2是显示根据本发明的一个实施例的各制造工序中的阴极活性物质的形状变化的照片。图3是显示根据本发明的另一实施方式的各制造工序中的阴极活性物质的形状变化的照片。图4是通过XRD分析对实施例1~2和比较例1~2中制造的阴极活性物质测定取向指数变化的图表。图5是利用实施例1~2和比较例1~2的电池显示电池的厚度变化率随常温寿命变化的图表。具体实施方式以下,对本发明进行详细说明。电池的膨胀率存在多种原因,但阴极的膨胀率为主要原因。为了减小上述阴极的膨胀率,在本发明中,将导入能够制造取向性更加提高的阴极活性物质粒子的新制造工序。更具体而言,在本发明中,对作为原料的片状石墨质材料或球状化的石墨粒子施加外力而进行加工,并且将外力调节至不使其发生微粉碎或不进行(类似)球状化的范围后施加,从而使具有一定方向的取向(orientation)的晶粒之间产生小的龟裂来起到整体上改变晶粒取向的效果。通过这样的工序,取向性提高的阴极活性物质与以往球状化的粒子相比, 取向指数(crystalorientationratio)低,因此能够在阴极活性物质内完全吸收在充放电时因与锂离子结合而产生的体积膨胀。因此,整体极板的体积不增加,能够极大地减小电池的膨胀率,从而能够稳定地维持包含该阴极活性物质的锂二次电池的长寿命特性。<阴极活性物质的制造方法>以下,对于根据本发明的阴极活性物质的制造方法进行说明。然而,并不限于下述制造方法,可根据需要通过改变各工序的步骤或选择性混用各工序的步骤而进行。作为上述制造方法的优选的一个实施例,通过对片状石墨质材料或球状化的石墨粒子施加机械外力来形成具有特定形状的1次粒子,可在上述1次粒子的表面涂覆非晶碳前体后,将涂覆后的碳前体在被碳化(carbonization)的温度以上的温度下进行热处理并进行造粒化来制造。此时,根据需要,可进一步实施2次热处理工序或分级工序。更具体而言,本发明的阴极活性物质大体可根据2种实施方式来制造。然而,并不特别限于此。制造本发明的阴极活性物质的优选的第一实施方式包括:步骤(i),对片状石墨质材料施加机械外力,形成上述石墨质材料的边缘部的一部分或全部发生折弯或具有变皱的形状的1次粒子(“S10步骤”);步骤(ii),用非晶碳前体涂覆上述1次粒子(“S20步骤”);及步骤(iii),对上述步骤(ii)中涂覆的非晶碳前体在其碳化温度以上的温度下进行热处理而造粒(“S30步骤”)。以下,将上述制造方法分为各个工序步骤进行说明,其内容如下。(1)1次粒子制造步骤(以下,称为“S10步骤”)在上述S10步骤中,通过对片状石墨质材料施加机械外力,并且将外力调节至不使片状石墨质材料发生微粉碎或者进行球形化或类似球形化的范围而形成1次粒子。在本发明中,作为用于制造阴极活性物质的结晶系碳材料的原料,可使用纯度为90%以上的片状(flake)石墨质材料。一般而言,越为结晶性高的石墨,结晶越规则生长,并表现出片状(鳞片状)。此外,最终获得的阴极活性物质的形状反映作为原材料的石墨的形状, 因此优选石墨的形状接近球状,优选使用纵横比(粒子的长轴长度与短轴长度之比)为3以下的石墨。此外,X射线衍射的测定值即d002可以小于0.337nm。作为可使用的石墨质材料的非限制性例子,有市售的片状天然石墨、集结石墨或它们的混合物等。此外,上述片状石墨质材料可使用的平均粒度为10至100μm的范围,优选可以为20至50μm的范围。在石墨质材料的平均粒度处于上述范围的情况下,不仅原料内杂质含量不会过高,而且也可直接发挥1次粒子形成效果。另一方面,在本发明中,对使用片状石墨质材料的情况进行了说明,但使用不是片状的人造石墨等石墨质材料的情况也属于本发明的范畴。这样,在不是片状的石墨质材料的情况下,可利用公知的粉碎装置进行粉碎而制成片状后进行使用。在上述S10步骤中,作为提供机械外力的装置,可无限制地使用本领域公知的混合及粉碎装置。这样的装置利用压缩、冲击、剪切、摩擦的力来对石墨质碳材料的表面进行加工。作为可使用的混合/粉碎装置的非限制性例子,可使用机械混合机、辊磨机(RollMill)、球磨机(BallMill)、碾磨机(Attritionmill)、行星式研磨机(Planetarymill)、振动研磨机(shakermill)、圆盘式粉碎机(diskmill)、成型研磨机(shapemill)、垂直成型研磨机(verticalshapemill)、旋转刀研磨机(rotorblademill)、Nauta研磨机(Nautamill)、Nobilta研磨机(Nobiltamill)、V型混合机(VMixing)、喷射式粉碎机喷射式粉碎机(JetMill)中的任一种。此外,就混合/粉碎时间而言,可根据石墨的种类或量而反复多次投入石墨原料,或者在合适的范围内进行调整以使石墨质原料能够在粉碎机中停留一定时间。例如,线速度可以为10至40m/s的范围,优选可以为30至40m/s。如上所述,如果利用机械装置进行加工工序,则会获得作为原料的石墨质材料(参照图1(a))内的片状石墨切片以多变形状折弯或形成有多个变皱的边缘部的1次粒子(参照图1(b))。此时,上述边缘部的变皱的角度(θ)可以为0<θ<180°的范围,优选可以为0<θ<90°的范围。此时,在1次粒子内部,使具有一定方向的取向(orientation)的晶粒之间存在小的龟裂来整体上改变晶粒的取向。同时,通过存在于内部的微细粒子性杂质所引发的龟裂,能够确保晶粒间的流动性,可一边以不均匀的方向形成微细 气孔,一边造粒这样的微细粒子。(2)被覆非晶碳前体的步骤(以下,称为“S20步骤”)在上述S20步骤中,为了在之前S10步骤中获得的1次粒子的阴极活性物质的电特性,被覆非晶系碳前体。其优选的例子是,向边缘部折弯或变皱的1次粒子中添加非晶系碳前体并均匀混合,然后,通过使用机械搅拌机进行搅拌的工序来实施使非晶系碳前体被覆于1次粒子的表面上的工序。作为上述非晶系碳前体,只要是能够通过烧成进行石墨化的物质,就没有特别限制,可无限制地使用本领域公知的常规物质。例如,有石油系沥青、煤炭系沥青、中间相沥青、煤焦油沥青、热处理沥青、氯乙烯系树脂、乙烯系高分子、芳香族烃、氮化合物、硫化合物、煤炭液化油、沥青烯、原油、石脑油、石油系重油、分解系重油或它们的1种以上的混合物等。就其使用量而言,相对于片状石墨质材料100重量份,可使用2至30重量份,可优选为5至15重量份的范围。如果过量使用非晶系碳原料,则会因形成过厚的被膜层而使电特性降低,如果使用过少,则会因形成过薄的被膜层而导致在充放电过程中被膜发生剥离,从而使寿命效率降低的结果。一般而言,在非晶系碳原料中,优选使用平均直径小的上述片状石墨质材料,例如,粒径10μm以下的粉末形态的上述片状石墨质材料。在上述S20步骤中,涂覆方法可无限制地使用本领域公知的常规的混合方法,为了均匀的混合,可以进行一般的混合(mixing)或使用干式或湿式的机械研磨(milling)方法。例如,可实施利用对流式涂覆(Convective)、旋转式涂覆(Tumbler)、密合型涂覆(Impaction)、剪切型涂覆(HighShear)等涂覆方法来混合和搅拌1次粒子和非晶碳前体。上述涂覆可通过干式工艺、湿式工艺、或组合干式和湿式的混合工艺来进行。此时,可根据1次粒子的成分、含量、非晶碳前体的成分和含量适当调整条件,例如,可在100至2000rpm下搅拌10分钟至100分钟。如果在上述条件下搅拌非晶系碳前体和1次粒子,则会因摩擦和剪切力而产生热,并且会因这样产生的热而使非晶系碳前体发生熔融,从而有助于1 次粒子的均匀被覆。(3)热处理步骤(以下,称为“S30步骤”)在上述S30步骤中,如果非晶系碳前体在1次粒子的表面上固着并稳定,则会通过实施热处理来实施碳化、杂质去除和改善表面性的步骤。上述热处理可在600至1500℃的温度范围下实施30分钟至72小时。此时,如果在上述条件下实施热处理,则能够在非晶系碳前体实现稳定化的同时充分地进行碳化,并且能够完全实现碳材料内的杂质去除。被覆于1次石墨粒子的表面上的非晶系碳前体会随着上述热处理步骤的进行而碳化,同时去除内部的杂质,并且进行硬碳化而使整个被膜层稳定,从而表现出被覆性提高的效果。在上述热处理后,为了提高结晶系石墨材料的结晶性/均一性并提高非晶系碳层的表面性,可在1000℃至3,000℃、优选为1000℃至1500℃的温度下进一步实施30分钟至72小时的2次热处理步骤。在电池的容量和电压平稳性方面考虑,由上述非晶系碳形成的被膜层的厚度处于0.001至1μm的范围是有利的,但不特别限于此。另一方面,图2是显示根据本发明的第一实施方式的阴极活性物质在各制造工序中的形状变化的照片。更具具体而言,通过对作为原料的片状石墨质材料(图2(a))施加外力,形成边缘部发生折弯或变皱的1次粒子(图2(b)),在形成的1次粒子的表面上涂覆非晶碳前体(图2(c)),之后实施热处理并进行造粒化(图2(d)),形成阴极活性物质。在制造本发明的阴极活性物质的优选的第二实施方式中,使用球状化的碳粒子来代替在第一实施方式中用作原料的片状石墨质材料。作为制造上述阴极活性物质的优选的第二实施方式,可包括:步骤(i),对球状化的石墨粒子施加机械外力,形成在上述粒子内进行结球的片状石墨切片的一部分或全部发生不规则层间剥离(exfoliate)或具有破碎的形状的1次粒子(“S11步骤”);步骤(ii),用非晶碳前体涂覆上述1次粒子(“S20步骤”);及步骤(iii),对上述步骤(ii)中涂覆的非晶碳前体在其碳化温度以上的温度下进行热处理而造粒(“S30步骤”)。(1-1)1次粒子制造步骤(以下,称为“S11步骤”)在上述S11步骤中,对球状化的石墨粒子施加机械外力,将外力调节至不使上述球形石墨粒子发生微粉碎的范围而进行加工。这样,在施加节以特定范围调的外力而进行加工的情况下,形成在球状化的石墨粒子内进行结球的片状石墨切片的一部分或全部发生不规则层间剥离(exfoliate)或具有破碎的形状的1次粒子。在本发明中,上述碳粒子可无限制地使用根据本领域公知的常规方法球状化的碳粒子。例如,可使用通过以机械外力对碳材料造粒、球状化而形成的碳粒子。上述球状化的石墨粒子可以是多种片状石墨切片通过结球而球形化的形态。更具体而言,可以是将一种片状碳材料结团而成的石墨粒子、将多种片状碳材料(例如,石墨切片)集合而造粒的石墨粒子中的任一种。特别优选表现出多种片状碳材料以同心圆状造粒而成的形状的石墨粒子。上述球状化的石墨粒子可以是天然石墨、人造石墨、集结(kish)石墨或热解石墨等,也可以为向其中混合软碳、硬碳、石油系焦炭、煤炭系焦炭或它们中的1种以上的物质。石墨的形状优选接近球状,优选使用纵横比(粒子的长轴长度与短轴长度之比)为3以下的石墨。此外,X射线衍射的测定值即d002可以小于0.337nm。上述球状化的石墨粒子是具有能够用作二次电池的阴极材料的平均粒度的球形粒子,例如,其平均粒度被控制在10至40μm的范围,优选在10至30μm的范围。此时,在加工过程中,平均粒度可通过适当选择加工条件而进行调整。在上述S11步骤中,使用提供机械外力的装置加工球状化的石墨粒子,此时,可无限制地使用本领域公知的混合及粉碎装置。例如,可同样地使用上述S10步骤中使用的混合/粉碎装置。此外,混合/粉碎条件也没有特别限制,例如,线速度可以为10至40m/s的范围,优选可以为15至30m/s。如果利用如上所述的机械装置实施加工工序,则会获得作为原料的球状化的石墨粒子内进行结球的片状石墨切片的一部分或全部发生不规则层间剥离(exfoliate)或具有破碎的形状的1次粒子。这样的1次粒子可以是多个外皮层的一部分或全部发生剥离或剥开的卷心菜或洋葱形状的无定形粒子。与上述S10步骤相同,通过在1次粒子内部使具有一定方向的取向(orientation)的晶粒之间存在小的龟裂来起到整体上改变晶粒取向的效果。因此,会进一步提高用于减小阴极的膨胀率的取向性。在上述S11步骤之后,与第一实施方式同样,依次实施S20~S30步骤,从而能够制造阴极活性物质。这样制造的本发明的阴极活性物质可具有如下图3(d)所示的结构。另一方面,图3是显示根据本发明的第二实施方式的阴极活性物质在各制造工序中的形状变化的照片。更具体而言,通过对作为原料的球状化的石墨粒子(图3(a))施加外力而形成1次粒子(图3(b)~图3(c)),在形成的1次粒子的表面上涂覆非晶碳前体,之后实施热处理并进行造粒化(图3(d)),从而形成阴极活性物质。<阴极活性物质>本发明提供利用上述方法制造的锂二次电池用阴极活性物质。更具体而言,上述阴极活性物质包含(a)一种以上的无定形石墨1次粒子;和(b)在上述1次粒子表面的一部分或全部形成的非晶碳层,具有借助于上述非晶碳层使1次粒子部分集合和固着而造粒的2次粒子结构,在上述2次粒子结构内具有包含孔隙的结构。其中,上述无定形1次粒子可具有根据上述2种实施方式的结构。例如,片状石墨切片包含以多边形状折弯或变皱的边缘部,上述边缘部变皱的角度(θ)可以为0<θ<180°的范围,此外,可以是多个外皮层的一部分或全部剥离或剥开的卷心菜或洋葱形状的无定形粒子。本发明的阴极活性物质具有特定范围的取向指数(crystalorientationratio),在锂二次电池的充放电时,阴极活性物质具有自行吸收金属的体积膨胀的特征。由此,能够降低包含该阴极活性物质的电池的厚度膨胀程度,从而能够提高电池的体积膨胀和寿命特性。这样的取向指数显示出阴极内部的结晶结构以一定方向排列,可用X-射线衍射(XRD)进行测定。更具体而言,关于上述阴极活性物质,利用CuKα射线测定的(002)晶面的X射线衍射强度与(110)晶面的X射线衍射强度之比所表示的取向指数[I(002)/I(110)]可以为50至110的范围,优选可以为70至100的范围。此时,XRD测定可以采用本领域公知的常规方法和条件进行测定,由此可测定阴极的取向指数。根据本发明的优选例子,上述阴极活性物质的振实密度可以为0.5至0.8g/cc的范围,平均粒径可以为10至30μm。另一方面,图1是分别显示以往天然石墨和作为本发明的优选的实施例的实施例1中制造的阴极活性物质(天然石墨)的形态的扫描电子显微镜(SEM)照片。此外,图2和图3是分别显示实施例1和2中制造的阴极活性物质在各制造工序中的形状变化的照片。并且,图4是测定实施例1~2中制造的阴极活性物质的取向指数的图表,可确认到具有调整至特定范围的取向指数(crystalorientationratio)。因此,在使用上述阴极活性物质制作电池的情况下,与以往球状化碳粒子相比,取向性提高从而能够提供具有电池的厚度膨胀率减小、高容量和长寿命的优异性能的电池。<阴极>本发明中制造的阴极活性物质可用作二次电池用阴极材料,除此之外,比如,也可用于燃料电池隔板用导电材料、耐火物用石墨或二次电池用阳极的电极材料等。在本发明中,提供上述二次电池用阴极材料及包含其的锂二次电池。此时,作为要件,本发明的阴极材料至少包含上述取向性提高的阴极活性物质。例如,将上述阴极活性物质本身直接用作阴极活性物质,或者将上述阴极活性物质和结合剂混合的阴极合剂、进一步添加溶剂而获得的阴极合剂糊、进一步将阴极合剂糊涂覆于集电体而形成的阴极等也属于本发明的阴极材料的范围。上述阴极可根据本领域公知的常规的方法制造,例如,可根据需要将粘合剂、导电剂、分散剂与电极活性物质混合并搅拌而制造浆料,然后,涂覆(coating)于集电体并压缩,之后进行干燥而制造。此时,分散介质、粘合剂、导电体、集电体等电极材料可使用本领域公知的常规物质,相对于电极活性物质,可适当地使用1~10重量比范围的粘合剂,1~30重量比范围的导电体。作为可使用的导电体的例子,有炭黑、乙炔黑系或者墨西哥湾石油公司(GulfOilCompany)的科琴黑(KetjenBlack)、VulcanXC-72、超级P等。此外,作为上述结合剂的代表性的例子,有聚四氟乙烯(PTFE)、聚偏二氟乙烯(PVdF)或其共聚物、丁苯橡胶(SBR)、纤维素等,作为分散剂的代表性的例子,有异丙醇、N-甲基吡咯烷酮(NMP)、丙酮等。上述金属材料的集电体是导电性高的金属,其作为能够使上述材料的糊容易粘接的金属,只要在电池的电压范围没有反应性就可以任意使用。例如,有铝、铜或不锈钢等的网(mesh)、箔(foil)等。<锂二次电池>并且,本发明提供包含上述阴极的二次电池,优选提供锂二次电池。本发明的锂二次电池使用上述取向性提高的阴极活性物质,除此之外,没有特别限制,可根据本领域公知的常规方法制造。比如,可通过在阳极与阴极之间放入隔膜并投入非水电解质来制造。此时,本发明的锂二次电池包含阴极、阳极、隔膜、电解质作为电池构成要素,其中,除了上述阴极以外,关于阳极、隔膜、电解质和所需的其他添加剂构成要素,以本领域公知的常规的锂二次电池的要素为基准。例如,上述阳极可使用本领域公知的常规的锂二次电池用阳极活性物质,作为其非限制性例子,有LiMxOy(M=Co、Ni、Mn、CoaNibMnc)等锂过渡金属复合氧化物(例如,LiMn2O4等锂锰复合氧化物、LiNiO2等锂镍氧化物、LiCoO2等锂钴氧化物和这些氧化物的锰、镍、钴的一部分被其他常规过渡金属等置换的氧化物、或含有锂的氧化钒等)或硫属化合物(例如,二氧化锰、二硫化钛、二硫化钼等)等。此外,非水系电解质包含本领域通常已知的电解质成分,比如包含电解质盐和电解液溶剂。上述电解质盐可以由如下离子的组合而构成:(i)选自由Li+、Na+、K+组成的组中的阳离子;和(ii)选自由PF6-、BF4-、Cl-、Br-、I-、ClO4-、AsF6-、CH3CO2-、 CF3SO3-、N(CF3SO2)2-、C(CF2SO2)3-组成的组中的阴离子,其中,优选为锂盐。作为锂盐的具体例子,有LiClO4、LiCF3SO3、LiPF6、LiBF4、LiAsF6和LiN(CF3SO2)2等。这些电解质盐可单独使用或组合2种以上而使用。上述电解质溶剂可使用环形碳酸酯、线形碳酸酯、内酯、醚、酯、乙腈、内酰胺、酮。作为上述环形碳酸酯的例子,有碳酸乙烯酯(EC)、碳酸丙烯酯(PC)、碳酸丁烯酯(BC)、氟代碳酸乙烯酯(FEC)等,作为上述线形碳酸酯的例子,有碳酸二乙酯(DEC)、碳酸二甲酯(DMC)、碳酸二丙酯(DPC)、碳酸乙基甲基酯(EMC)和碳酸甲基丙基酯(MPC)等。作为上述内酯的例子,有γ-丁内酯(GBL),作为上述醚的例子,有二丁基醚、四氢呋喃、2-甲基四氢呋喃、1,4-二烷、1,2-二甲氧基乙烷、1,2-二乙氧基乙烷等。作为上述酯的例子,有甲酸甲酯、甲酸乙酯、甲酸丙酯、乙酸甲酯、乙酸乙酯、乙酸丙酯、丙酸甲酯、丙酸乙酯、丙酸丁酯、特戊酸甲酯等。此外,作为上述内酰胺,有N-甲基-2-吡咯烷酮(NMP)等,作为上述酮,有聚甲基乙烯基酮。此外,也可使用上述有机溶剂的卤素衍生物,但不限于此。并且,上述有机溶剂也可使用乙二醇二甲醚(glyme)、二乙二醇二甲醚、三乙二醇二甲醚、四乙二醇二甲醚。这些有机溶剂可单独使用或混合2种以上而使用。上述隔膜可无限制地使用起到切断两电极的内部短路且浸渍电解液的作用的多孔性物质。作为其非限制性的例子,有聚丙烯系、聚乙烯系、聚烯烃系多孔性隔膜或在上述多孔性隔膜上添加有无机物材料的复合多孔性隔膜等。以下,通过实施例对本发明进行具体说明,但下述实施例和实验例仅用于例示本发明的一个形态,本发明的范围不限于下述实施例和实验例。[实施例1]1-1.阴极活性物质制造将板状石墨100g投入旋转的研磨机(mill),以线速度40m/s速度运转6分钟,然后将变皱的粒子和5重量%的沥青在亨舍尔混合机(henschelmixer)中混合20分钟。之后,在氮气气氛的热处理炉中,在1300℃进行1小时的热处理。之后,去除大粒子,然后获得中心粒度为17μm的阴极材料。1-2.阴极制造向根据实施例1制造的阴极活性物质96重量份添加作为粘合剂树脂的纤维素溶液1重量份、丁苯橡胶(SBR)2重量份和作为导电材料的炭黑1重量份并分散,制造阴极用浆料,并且将其涂覆于铜集电体。然后,通过辊轧进行压延制造阴极。1-3.锂二次电池制造将上述阴极与锂金属作为对极,制造钮扣型半电池(Cointypehalfcell)。此时,电解液使用溶解有1.0MLiPF6的碳酸乙烯酯(EC)/碳酸乙基甲基酯(EMC)和碳酸二甲酯(DMC)的混合溶液(EC:EMC:DMC=2/3/1,体积比)。[实施例2]将球状石墨粒子100g投入研磨机(mill),以线速度15m/s的速度与空气碰撞来粉碎粒子,然后与5重量%的沥青在亨舍尔混合机(henschelmixer)中混合20分钟,然后在氮气气氛的处理炉中,在1300℃进行1小时的热处理。之后,去除大粒子,然后获得中心粒度为17μm的实施例2的阴极材料。利用上述阴极材料并根据与实施例1相同的方法分别制造阴极和锂二次电池。[比较例1]将板状石墨100g投入旋转的研磨机(mill),以线速度45m/s的速度运转12分钟后,将球状化粒子和5重量%的沥青在亨舍尔混合机(henschelmixer)中混合20分钟。之后,在氮气气氛的热处理炉中,在1300℃进行1小时的热处理。之后,去除大粒子,然后获得中心粒度为17μm的比较例1的阴极材料。利用上述阴极材料并根据与实施例1相同的方法分别制造阴极和锂二次电池。[比较例2]将板状石墨100g投入旋转的研磨机(mill),以线速度45m/s的速度运转12分钟,然后将球状化粒子和5重量%的沥青在亨舍尔混合机(henschelmixer)中混合20分钟。之后,在氮气气氛的热处理炉中,在3000℃进行24小时的热处理。之后,去除大粒子,然后获得中心粒度为17μm的比较例2的阴极材料。利用上述阴极材料并根据与实施例1相同的方法分别制造阴极和锂二次 电池。[比较例3]将板状石墨100g投入旋转的研磨机(mill),以线速度5m/s的速度运转6分钟,然后将球状化粒子和5重量%沥青在亨舍尔混合机(henschelmixer)中混合20分钟。之后,在氮气气氛的热处理炉中,在1300℃进行1小时的热处理。之后,去除大粒子,然后获得中心粒度为17μm的比较例3的阴极材料。利用上述阴极材料并根据与实施例1相同的方法分别制造阴极和锂二次电池。[实验例1.取向指数测定]对于上述实施例1~2和比较例1~3中制造的阴极活性物质,利用CuKα射线进行X射线衍射测定,从上述X射线衍射图案计算阴极活性物质的(002)面的强度I(002)与(110)面的强度I(110)之比即取向指数(I(002)/I(110))。上述X射线衍射测定根据日本学术振兴会(JSPS)的基准实施,其结果归纳于下述表1。[表1]实施例1实施例2比较例1比较例2比较例3取向指数10296140160190[实验例2.电池的厚度变化率和性能评价]对于上述实施例1~2和比较例1~3中制造的锂二次电池的电池,以1C实施充放电,测定200个循环期间的电池的厚度膨胀率。其结果示于下述图5。实验结果可以看到,在比较例1至3的电池中,在经过50个循环之前,电池的厚度膨胀率就已显著增加(参照图5)。相比于此,可以确认,实施例1和2的锂二次电池即使反复进行200个循环,电池的厚度膨胀率也显著低。由此可知,包含本发明的阴极活性物质的锂二次电池能够在表现出稳定的循环特性的同时使电极的膨胀率显著降低。当前第1页1 2 3