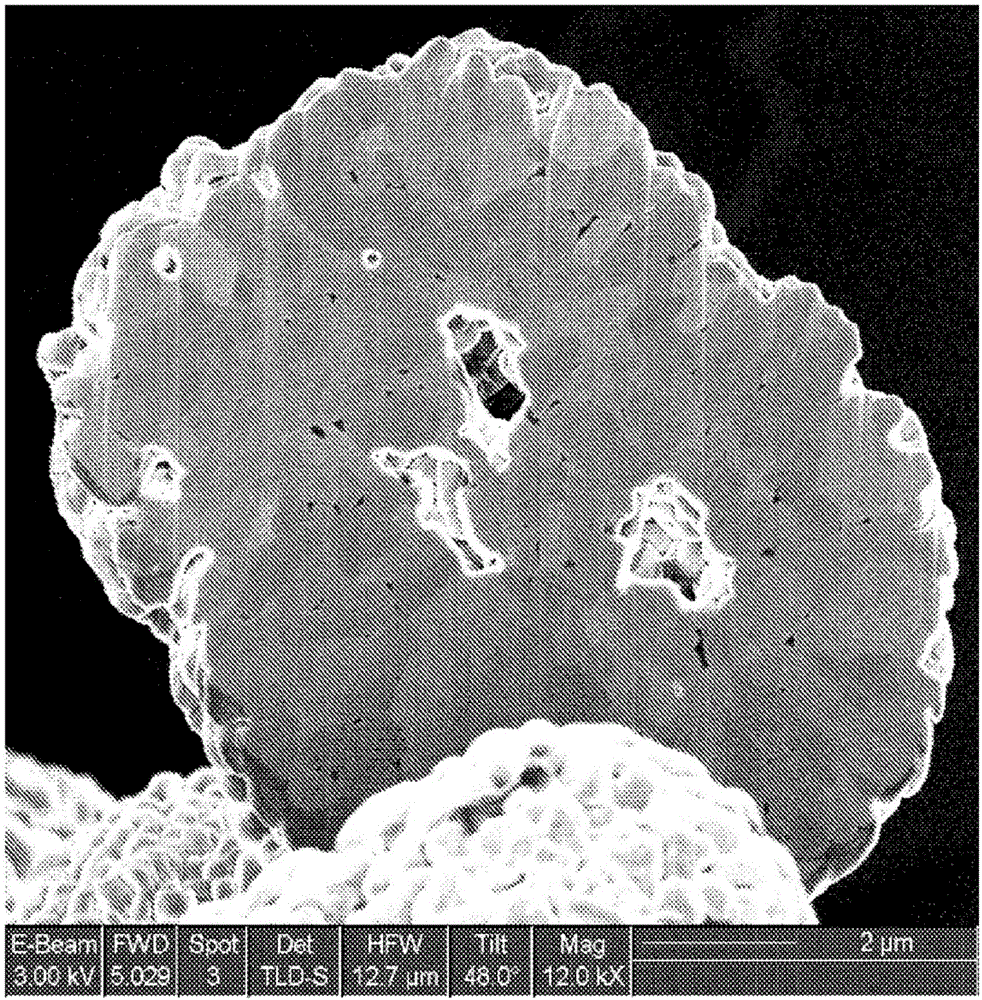
本发明涉及一种制造用于锂离子电池(LIB)的改进的锂金属氧化物(LMO)正极材料的方法以及其制造方法。具体地讲,本发明涉及LMO,其中所述金属由Ni、Mn和Co组成,并且Ni为LMO中所述金属的40摩尔%或更多。
背景技术:
:锂离子电池在过去几十年里被用于便携式电子设备,并且最近用于混合动力车辆或电动车辆。最初,锂离子电池先使用锂钴氧化物正极。因为费用、毒理学问题以及有限的容量,所以已开发或正在开发其它正极材料。已开发或在商业上使用的一类材料为锂金属氧化物(LMO),所述锂金属氧化物(LMO)由镍、锰和钴中两个或更多个组成的,特别是这三种金属都包括在内。这些材料一般展现具有单一菱面体相的层状结构,其中当充电到相对于Li/Li+的约4.2伏特的电压时,实现初期高比电荷容量(一般为155至170mAh/g)。不幸的是,这些材料存在短循环寿命和在某些条件下与氧气逸出相关的会引起火灾的安全问题。Li/Li+表示锂参考电极的氧化还原电位,其按照惯例限定为0伏特。因此,当使用除了Li金属的负极,这些电压将下降以导致此另一个负极与Li金属之间的电位差。说明性地,完全充电的石墨负极具有相对于Li/Li+的约0.1V的电位。因此,当将具有石墨负极的电池的正极充电到相对于Li/Li+的4.25V时,电池电压为约4.15V。循环寿命一般被视为在达到初始比容量的80%的比容量前的循环数(充电-放电)。这些材料的每次循环一般为4.2伏特至2伏特。这些电池也存在一个电池或电池单元与另一个的性能不一致,即使由相同材料制造。这些LMO可包含改善一种或多种性质(例如循环寿命)的掺杂剂或涂料。它们一般以化学计量或基本上以化学计量,例如美国专利号6,964,828、6,168,887、5,858,324、6,368,749、5,393,622和欧洲专利公布号EP1295851、EP0918041、和EP0944125以及日本专利公开号11-307094所述的那些。这些锂金属氧化物通过固态合成制造,其中将颗粒前驱体混合或研磨然后加热到一定温度以形成LMO。这个方法的实例在美国专利号6,333,128、7,211,237和7,592,100中有所描述,但如美国专利号7,592,100(第7栏,第38行至第8栏,第43行)所述,固态合成法因难以制造单相层状材料以及需要使用非常小尺寸的颗粒而是不理想的。锂金属氧化物也通过先在连续搅拌的反应器中沉淀络合物前驱体,随后将络合物前驱体化合物与锂化合物一起加热到一定温度以形成LMO而形成。这些方法的实例在美国专利号7,592,100和6,964,828以及日本专利公开号11-307094中有所描述。也描述了其它方法(例如水热法和溶胶凝胶法)以形成络合物氧化物。这些实例在美国专利号7,482,382和EP0813256中有所描述。因此,LMO倾向于由络合物金属化合物“LMO前驱体”制造,其从连续搅拌的反应器沉淀,然后与含锂化合物混合并充分加热以形成LMO。它们一般以此方式制造以避免简单干混前驱体所遇到的问题,例如化学、一次晶粒/粒径和二次粒径的非均匀性。不幸地是,连续搅拌的反应器需要长反应停留时间以实现所需的二次粒径,改变反应条件防止它们被连续使用(例如,二次粒径随时间生长)以及因在生产规模上制造LMO所需的大型罐导致的大量资本投资。同样,因为沉淀方法的固有限制,所以形成的LMO非常相似,并且它们倾向于形成存在特定地针对具有高Ni含量的组合物而言的低正极密度和低安全性的LMO。因此,需要提供一种LMO和制造LMO的方法,该LMO提供具有高电压、更高能量容量、更大循环能力和改进的安全性的LIB。技术实现要素:申请人发现了一种制造LMO的方法,其实现了能够使LIB具有改进的安全性、更高的可循环性、更高的能量密度和更高的操作电压的LMO。本发明的第一方面是制造由Li、Ni、Mn、Co和氧组成的适用于制造锂离子电池正极的锂金属氧化物粉末的方法,其包括(a)提供前驱体混合物,其包含由Li、Ni、Co和氧组成的颗粒前驱体和不含Ni和Co的Mn颗粒前驱体,其中包含Ni和Co的所述前驱体颗粒具有D50为0.1至0.8微米、、D10为0.05至0.3微米、D90为0.35至1.5微米并且基本上没有大于3微米的颗粒的未聚集一次粒径。(b)聚集所述前驱体混合物以形成由所述颗粒前驱体和所述Mn颗粒前驱体的一次颗粒组成的二次颗粒,所述颗粒前驱体由Li、Ni、Co和氧组成,(c)在含氧氛围中将所述二次颗粒加热到形成所述锂金属氧化物的温度和时间。第一方面的方法令人惊讶地能够形成甚至当Ni含量高时改善安全性,增加循环寿命,并增加由LMO制造的LIB的能量容量的LMO。在不以任何方式限制本发明下,普遍认可这个发现:最终一次粒径与Ni和Co前驱体尺寸相关联以及需要大量大于0.5微米的颗粒能够形成具有先前不可实现的特定一次粒径、一次颗粒化学组成(即,允许更安全的梯度结构)、二次颗粒密度以及二次粒径和分布的LMO。在很大程度上可实现所有这些,而不用折衷LIB的良好倍率容量。本发明的第二方面是由聚集成二次颗粒的一次颗粒组成的锂金属氧化物,该锂金属氧化物由Li、Ni、Mn、Co和氧组成,其中该锂金属氧化物具有整体Mn/Ni比率,并且所述一次颗粒具有使表面Mn/Ni比率大于整体Mn/Ni比率的表面Mn/Ni比率。本发明的第三方面是由聚集成二次颗粒的一次颗粒组成的锂金属氧化物,所述锂金属氧化物由Li、Ni、Mn、Co和氧组成,其中所述二次颗粒具有最多约5%的孔隙率。本发明的第四方面是由聚集成二次颗粒的一次颗粒组成的锂金属氧化物,所述锂金属氧化物由Li、Ni、Mn、Co和氧组成,其中所述二次颗粒具有10至35微米的D50、6至10微米的D10、20至45微米的D90,并且基本上没有大于100微米的颗粒。本发明的LMO被发现能够制造球形二次颗粒,例如通过喷雾干燥形成,其在加热和加热后轻微研磨以分离二次颗粒后保持其结构。在一个优选的实施例中,优选的是,基本上没有小于约5微米当量球形直径的二次颗粒。例如,这避免了破裂的二次颗粒的形成以及单独的一次颗粒的存在,这些被认为例如减少循环寿命。本发明的第五方面是一种正极,其包括一层先前方面的锂金属氧化物和粘附到金属箔的除了锂金属氧化物的锂金属正极材料中任一个的锂金属氧化物。令人惊讶地发现,当使用本发明的LMO时,特别是展现本发明的第三方面和第四方面的特征的那些,可制造高密度正极,允许电池容量的显著增加,而不会有害地影响其它所需电池特征(例如倍率性能)。在一个特定的实施例中,将本发明的第四方面的LMO与更少量的未聚集(即,单独的一次颗粒)的LMO混合。在另一个实施例中,将所述LMO与锂金属正极材料(例如锂金属磷酸盐)混合,此令人惊讶地实现良好的电化学性能以及甚至进一步改进的安全性能。附图说明图1是本发明的锂金属氧化物的二次颗粒的横截面的扫描电子显微照片。图2是本发明的锂金属氧化物的二次颗粒的横截面的扫描电子显微照片。具体实施方式说明性地,锂金属氧化物整体化学由下式表示:LixMyO2其中00.8<x<1.15,y是1,并且金属由Ni、Co和Mn组成。理想地,x是0.85<x<1.1或0.9<x<1.05。令人惊讶地发现,特别地当存在高Ni浓度时(例如,当Ni是0.55或更大时),需要略微不足的Li。应当了解,Li当用于电池时(即,当充电时),Li的量从刚给出的Li下降,并且在充电时,Li增加以接近在上式的量。在一个优选的实施例中,Ni、Mn和Co的量由Ni1-a-bMnaCob表示,其中0.1≤a≤0.9以及0≤b≤0.8。在一个优选的实施例中,a和b是0.1≤a≤0.4和0.1≤b≤0.4以及甚至更优选地0.1≤a≤0.25和0.1≤b≤0.25。在一个优选的实施例中,Ni/(Co+Mn)的比率是0.5至9以及更优选地1至3。应当了解,LMO也可包含少量改善一个或多个性质的掺杂剂,其实例为氟或其它金属。示例性掺杂剂金属包含,但不限于Al、Ti、Mg、Ca、In、Ga、Ge、Si、或其组合。同样,锂金属氧化物在掺杂例如以上掺杂剂金属的氧化物后,也可涂覆有多种涂层以改善一种或多种性质。这些掺杂剂一般以LMO中存在的掺杂剂金属以及Ni、Mn和Co的10%的摩尔量存在。LMO一般展现当以0.1的C速率在3与4.3V或4.5V伏特之间放电时,在通过典型形成方法最初充电到4.3V或4.5V伏特后至少约150至210mAh/g的比容量。1的C速率意指在上述电压之间在1小时内充电或放电,并且C/10是充电或放电等于10小时的速率,并且10C速率等于6分钟。通过X-射线衍射分析的LMO的整体晶体结构基本上展现了单O3相(即,R-3m空间群),如分别在Delmas,C等人,《固态离子(SolidStateIonic)》3/4(1981)165-169和Jarvis,K.A.等人,Chem.Mater.2011,23,3614-3621中所述。再次重申,申请人已发现一种形成LMO的方法,所述LMO具有极佳容量、循环寿命、对于甚至具有高浓度Ni的LMO的安全性。具体地讲,已发现,认为由Ni、Co和Mn组成的LMO的一次颗粒的形成至少部分地受控于Ni和Co前驱体的前驱体尺寸以及在加热时Mn到初始的包含Ni和Co的化合物中的吸收。这允许避免过大的晶粒生长和LMO一次颗粒的硬烧结和二次颗粒之间的硬烧结以及当LMO由其它方法(例如沉淀方法)制造时普遍的更大的二次颗粒的破裂。这些发现目前能够形成具有上述所希望的性质的LMO。为形成LMO,加热前驱体颗粒混合物以形成LMO。前驱体混合物由不含Ni和Co的Mn颗粒前驱体和由Li、Ni、Co和氧组成的颗粒前驱体组成。应当了解,Mn颗粒前驱体可包含少量Ni和Co,例如痕量或整体组合物中所希望的Ni和Co的量的最多约5摩尔%,但是优选地,在Mn颗粒前驱体中基本上不存在Ni或Co。同样,优选的是,Mn颗粒前驱体也不含Li。Mn颗粒前驱体理想地包含氧。说明性的Mn颗粒前驱体包含氢氧化物、氧化物、碳酸盐、上述的水合形式或这些中两个或更多个的组合。优选地,Mn颗粒前驱体是氧化锰(II)、氧化锰(III)、氧化锰(II,III)、碳酸锰或其组合。更优选地,Mn颗粒前驱体是氧化锰(III)氧或碳酸锰。前驱体颗粒混合物也包含由Li、Ni、Co和氧组成的颗粒前驱体。理想地,具有Li的颗粒前驱体不含任何其它金属,痕量除外。具有Ni和Co的任何前驱体也可以针对Mn颗粒前驱体所述的方式包含痕量的Mn和Li。在一个优选的实施例中,前驱体颗粒混合物由Ni颗粒前驱体、Co颗粒前驱体和Li颗粒前驱体以及Mn颗粒前驱体组成,其中这些颗粒前驱体中的每一个都不包含其它颗粒前驱体中任一个中的金属。在另一个优选的实施例中,前驱体混合物由含Ni和Co的颗粒前驱体、和Li颗粒前驱体以及Mn颗粒前驱体组成,其中这些颗粒前驱体中的每一个都不包含其它颗粒前驱体中任一个中的金属。由Li、Ni、Co和氧组成的前驱体可包括氢氧化物、氧化物、碳酸盐、上述的水合形式或这些中两个或更多个的组合。说明性的适宜前驱体包括,例如,碳酸锂、氢氧化镍、碱式碳酸镍四水合物、氢氧化钴、和氢氧化镍钴[NiCo(OH)2]。由Ni和Co组成的颗粒前驱体需要具有一次粒径和尺寸分布,其通过中值尺寸(D50)、D10、D90和最大尺寸限制给出。尺寸是以体积计的当量球形直径,其可通过显微技术测量,但是优选地,利用在低固体负载下固体在液体中的分散液,通过激光光散射方法测量。D10是其中10%的颗粒具有更小尺寸的尺寸,D50是其中50%的颗粒具有更小尺寸的尺寸,并且D90是其中90%的颗粒具有以体积计的更小尺寸的尺寸。已发现,必须具有含有Ni和Co的颗粒前驱体以形成具有高度填充的二次颗粒(具有低孔隙率的聚集的一次颗粒)的LMO,同时仍实现其它所需结果。具有Ni和Co的前驱体颗粒的D50一般为约0.1至0.8微米,D10为0.05至0.3微米,并且D90为0.35至1.5微米,基本上没有颗粒大于约3微米、约2.5微米或甚至约2微米(也称为D100)。在不限制下,普遍认为,关键的是具有显著量的尺寸大于0.5微米的颗粒以实现例如二次颗粒的以上改进的填充并实现在颗粒表面具有更大Mn的梯度结构。优选地,D90为0.45、0.5或0.55至1.4、1.2或1微米。但是,如果过多颗粒大于约2微米,电化学性能看起来受影响或加工的容易性受影响。即使Mn颗粒前驱体看起来对最终LMO一次粒径没有显著影响,其一般必须为不能太大的尺寸,这样形成LMO所需的加热温度和时间太长而不实际或未能形成所需的LMO。一般来讲,D50为约0.2至约1.5微米,D10为约0.05至约1微米,D90为约0.4至约5微米,并且D100为约1至约10微米。优选地,D10为0.01至0.8、0.5、0.2或0.1,D50为0.2至1.3、1.1、1、0.8、0.5或0.4,D90为0.45、0.5或0.55至4、3或1,并且D100为9、7、5、3或2。在一个优选的实施例中,前驱体混合物的所有颗粒具有针对具有Ni和Co的前驱体颗粒给出的上述一次粒径和尺寸分布。颗粒前驱体的粒径和尺寸分布可通过任意适宜方法形成,但是一般需要至少一些粉碎例如已知的研磨技术。例如,研磨可包括干磨、湿磨、喷射研磨以及其任意组合。研磨可对每个前驱体颗粒分开进行并随后通过已知的掺混方法以适当比例掺混。可使用研磨设备,例如球磨机、卧式和立式介质研磨机、振动磨机和超微磨碎机。研磨可在连续研磨步骤中进行以实现所期的粒径和尺寸分布。在一个优选的实施例中,同时研磨所有的前驱体颗粒材料。研磨优选地在液体中进行。液体可为具有低粘度(例如,小于约100厘泊)的任意种并可通过例如喷雾干燥的技术轻易地去除。液体可为有机液体例如酮、烷烃、醚、醇、酯等。优选地,液体为极性溶剂例如醇(例如,乙醇、丁醇、丙醇和甲醇)或水。优选地,液体为水。当在液体中研磨时,由Ni和Co组成的颗粒前驱体一般至多部分地溶于液体中。优选地,溶解度的量为可溶于液体中的以重量计的至多约5%,更优选地,至多约2%以及最优选地,至多约1%。当在液体中研磨时,对于任意其它前驱体材料的溶解度的期望也是一样的。在一个优选的实施例中,在每种颗粒前驱体存在下,研磨在水中进行。在此特定的实施例中,当所有颗粒前驱体同时在水中研磨时,发现使用具有多个酸性基团的有机分子是有利的。使用这些令人惊讶地允许研磨例如在水中具有高达50重量%的固体负载的浆液。有机分子或分散剂可为例如多元酸。示例性多元酸包括聚丙烯酸(一般分子量为2000至100,000)、聚甲基丙烯酸、聚苯乙烯磺酸等。分散剂的量一般为适用于允许在高固体负载(例如,大于约40重量%或45重量%固体负载)下研磨成小粒径同时仍具有低粘度并且不胶凝(即,小于约10,000厘泊,但是优选地小于约5000或甚至2000厘泊)的任意量。一般来讲,分散剂的量尽可能地少并且一般来讲以浆液的总重计的至多约5%、3%、2%或1%至至少约0.01%。使用研磨时的特定研磨机、介质、时间和特定参数可为任意适宜值,例如陶瓷领域中已知的那些。一般来讲,介质可为可购得的那些中的任一种,包括例如,碳化物介质(SiC、具有或不具有Co的WC、具有或不具有Co的混合的金属碳化物)、ZrO2、Al2O3和其组合。一种优选的介质是氧化钇稳定的氧化锆。一旦提供前驱体混合物,将颗粒聚集以形成二次颗粒。如上所述,将前驱体混合物掺混以形成混合物或干磨或单独地在液体中然后合并或同时进行。如果前驱体混合物以干燥形式提供,例如,可通过例如在HosokawaMicronLtd.的市售设备中机械融合的方法来聚集成二次颗粒。优选地,将每个颗粒前驱体分散到液体中以形成浆液然后通过例如喷雾干燥、冷冻干燥、超临界干燥等技术干燥。优选地,通过前驱体混合物的水性浆液的喷雾干燥进行聚集。当从液体进行喷雾干燥时,优选地是,固体负载是至少10重量%,更优选地至少20重量%,甚至更优选地至少30重量%,以及最优选地至少40重量%固体负载到任意可实现量而不会胶凝或液体太粘稠而不会被轻易地泵送到喷雾干燥器(例如,大于500,000厘泊)。当特别地通过喷雾干燥形成二次颗粒时,已发现,当前驱体颗粒具有上述尺寸时,可认识到在加热时形成LMO时的二次颗粒基本上不含一次颗粒。换句话说,已发现,二次颗粒当受热时未能破裂,因此允许形成具有低表面积,宽尺寸分布,但仍保持良好充电和放电倍率容量的LMO。理想的二次粒径和尺寸分布(以微米为单位的体积当量球形直径)是当二次颗粒具有10至35微米的D50,6至10微米的D10,20至45微米的D90以及基本上没有小于约5微米的颗粒时。优选地,D50是12或15至约30微米,D90是约25至约40微米。粒径和尺寸分布可通过例如显微技术、筛分技术、或光散射技术的已知技术确定。在二次颗粒形成后,将它们在含氧氛围中加热到一定温度。特定的最终温度或最大温度可根据所需的化学组成(即,Ni、Mn和Co的量)而变化。一般来讲,最大温度为约890℃至约970℃。优选地,温度为930℃至960℃。颗粒在最大温度下的保持时间一般为至少约5分钟至约10小时,但是优选地,时间为15分钟或30分钟至7.5小时或5小时。已发现,更多时间倾向于产生更大的一次晶粒以及有时产生过大的晶粒生长,但是较低温度不能形成所需的二次颗粒微结构(例如,低孔隙率二次颗粒)。加热可在加热期间保持更低温度(即,保持更低中间温度)。可进行这些,例如以确保混合物温度的均匀性,不需要组分的去除(例如,有机材料或将前驱体分解成氧化物)或适用于制造最终锂金属氧化物的所需中间相的形成。一般来讲,该中间温度为约250℃至850℃。中间温度的至少一个理想地为至少400℃、500℃或600℃至至多约800℃、750℃或700℃。在这些温度下的时间类似于针对以上最高或最终温度所述的那些。加热可具有实际的但产生所需锂金属氧化物的任意加热或冷却速率。一般来讲,加热速率为至少0.1℃/min至250℃/min。更常见地,速率为约1℃/min或5℃/min至50℃/min或20℃/min。加热在含氧氛围中进行,但是令人惊讶地发现,主要由氧或纯氧组成的氛围不理想并倾向于形成更少的所期锂金属氧化物。含氧氛围优选地具有至少约0.1至0.3或0.25大气压(atm)的氧分压。即使氛围可为动态的(例如,流动的),氛围理想地为静态的。在一个优选的实施例中,氛围可以动态方式达到较低中间温度然后以静态方式达到最高温度。同样,氧分压可在加热期间降低。该方法能够形成包含高浓度的Ni并具有大幅度提升的安全性能的锂金属氧化物,这被认为是因为新发现的形成具有呈梯度结构的一次颗粒的该锂金属氧化物的能力。具体地讲,发明人发现了由聚集成二次颗粒的一次颗粒组成的锂金属氧化物,所述锂金属氧化物由Li、Ni、Mn、Co和氧组成,其中所述锂金属氧化物具有整体Mn/Ni比率,并且所述一次颗粒具有使表面Mn/Ni比率大于整体Mn/Ni比率的表面Mn/Ni比率。整体Mn/Ni比率是LiMO2的所需组成并可通过用以确定元素组成的整体分析技术确定。一次颗粒的表面Mn/Ni比率通过X-射线光电子光谱法(XPS)确定。表面Mn/Ni比率是粉末样品的表面比率的平均值并不是随后取平均的单独一次颗粒的梯度组成的测量值。以下进一步描述XPS技术。理想的是,表面Mn/Ni比率比整体Mn/Ni比率大至少1%、2%或甚至5%至至多约20%。如所述,当锂金属氧化物的Ni含量大时,理想的是,表面Mn/Ni比率更大,因为令人惊讶地改善安全性。例如,理想的是,具有使Ni/(Mn+Co)摩尔比为0.5至3(当制造锂金属氧化物时的整体化学或所期化学)的Mn/Ni比率。更理想的是,所述Ni/(Mn+Co)摩尔比是0.75至2。锂金属氧化物的一次粒径被发现与含Ni和Co的前驱体颗粒尺寸相关联。因此,展现所述表面Mn/Ni比率的锂金属氧化物具有类似于以上针对这些前驱体所述的尺寸的尺寸,允许在加热期间出现一些晶粒生长。一般来讲,一次粒径在上述Ni和Co颗粒前驱体尺寸的20%、10%或5%内或基本上相同。在不限制下,特别是具有所述表面Mn/Ni比率的更大一次颗粒的该尺寸被认为导致即使具有高Ni浓度的该锂金属氧化物的改进的安全性同时不明显地降低其他所需的性能特征。又在不限制下,梯度被认为因为Ni和Co氧化物颗粒相的初期形成,其随后必须使Mn分散到更大颗粒中,产生了梯度。也发现了,锂金属氧化物可通过使一次颗粒聚集成二次颗粒的本发明方法形成,所述锂金属氧化物由Li、Ni、Mn、Co和氧组成,其中所述二次颗粒具有至多约5%的孔隙率。优选地,孔隙率为至多约4、3或甚至2%。因为该方法使用Ni和Co颗粒前驱体的上述粒径并结合最终锂金属氧化物尺寸与其相关联的这个发现以及当如上述加热时,形成具有低孔隙率而没有过大晶粒生长的二次颗粒。即使二次颗粒具有低孔隙率,锂金属氧化物仍可展现良好的比容和良好的倍率容量。具有低孔隙率二次颗粒的锂金属氧化物可,但不必具有上述的表面Mn/Ni比率。但是,理想的是,该颗粒具有该比率以及针对具有上述Mn/Ni比率的锂金属氧化物所述的其它每一个属性。在一个优选的实施例中,发现了,当使用上述方法时,锂金属氧化物可形成加热时不破裂的二次颗粒。当锂金属氧化物具有该二次粒径时,可形成具有改进的循环寿命的锂金属氧化物。该二次尺寸和形状实质上与上述的喷雾干燥的二次颗粒给出的相同。令人惊讶地,该方法考虑到这些的密切相关,因为锂金属氧化物二次颗粒本身具有良好的机械完整性,但是实质上不烧结在一起并因此容易分裂(锂金属氧化物的最终粉碎)而当进行时不会使二次颗粒本身破裂。一般来讲,具有以上二次粒径的锂金属氧化物具有约0.75m2/g或优选地至多约0.6、0.5或0.4m2/g至至少约0.1m2/g的表面积。同样,所述锂金属氧化物展现所述锂金属氧化物的理论密度的至少约40%的振实密度,当在以下进一步所述的金属箔上形成正极层时,这是高度令人希望的。一般来讲,振实密度令人希望地为至少约1.15。优选地,振实密度为至少约1.5、1.75、2或甚至2.1g/cc。具有表面Mn/Ni比率或低孔隙率二次颗粒的上述锂金属氧化物也优选地具有刚才描述的二次粒径。通过本发明方法制造的LMO或本发明的任意LMO可通过利用传统粘合剂和方法将LMO粘附到金属箔而形成正极。说明性地,本发明的锂金属氧化物可单独使用或与另一种电池正极材料一起使用,该另一种电池正极材料例如本领域已知的那些(例如,锂金属磷酸盐、镍钴铝氧化物或由镍和锰组成的其它氧化物)。在一个特定的实施例中,本发明的锂金属氧化物中的任一种,但是特定地具有上述二次粒径者与基本上由游离一次颗粒组成且没有二次颗粒并且一次粒径与尺寸分布基本上与针对文中所述的一次颗粒所述相同的锂金属氧化物混合。在另一个实施例中,本发明的LMO与另一种锂金属正极材料混合,另一种锂金属正极材料例如本领域中已知的那些以及具体而言锂铝钴氧化物或锂金属磷酸盐。令人惊讶地发现,具有含高Ni含量(例如,Ni以LMO中除了锂外的金属的50摩尔%的量存在)的LMO的锂离子电池可与锂金属磷酸盐混合,而电化学性能没有显著降低并甚至进一步改善安全性。锂金属磷酸盐理想地是金属由过渡金属组成并可进一步由碱金属组成的锂金属磷酸盐。理想地,金属可为Mn、Co、Fe,这些掺杂了少量碱金属(例如Mg)。理想地,过渡金属主要是Mn(例如,大于除了Li的金属的50摩尔%)。这些优选的锂金属磷酸盐的实例在以引用方式并入本文的发明人ShrikantKhot的共同待审申请PCT/US13/029597中有所描述。使LMO在溶剂中混合以允许形成均匀混合物。溶剂可为任意适宜溶剂,例如本领域中已知的那些并一般为具有低含水量(例如,500ppm或更少以及优选地小于100、50、10或甚至1ppm)的极性和非极性有机溶剂。有用溶剂的实例包括例如n-甲基吡咯烷酮(NMP)和丙酮的有机溶剂以及例如水和JinChong等人,JournalofPowerSources196(2011)第7707至7714页中所述的那些的极性溶剂。固体(例如,锂金属氧化物)的量可为任意有效量。一般来讲,量为溶剂的10体积%至90体积%并且可为至少20%或30%至至多80%或70%。一般来讲,混合在任意剪切下进行,可使用例如具有或不具有挡板的简易桨式混合器或高剪切混合器(例如,胶体磨)。通常,剪切速率为至多约5000sec-1并通常为约1sec-1至约1000sec-1。可使用用于将浆液浇注到箔上的其它已知添加剂,例如适宜的分散剂、润滑剂、粘合剂和水清除剂。将混合进行一段时间以充分地分散锂金属氧化物和锂金属磷酸盐以实现所期结果。一般来讲,时间可为几分钟至可行的任意时间,例如几天或几小时。然后,将混合物涂覆到用以制造电池中电极的金属箔上,例如铝、镀碳的铝、蚀刻铝、镍、铜、金、银、铂、和上述合金或其组合并包括Hsien-ChangWu等人,JournalofPowerSources197(2012)第301至304页中所述的那些。浆液的涂覆可通过任意有效技术进行,例如该领域中已知的那些。一般来讲,所用方法是在所期间隙下刮刀浇注。然后,去除溶剂以形成正极。去除可为任意适宜方法,例如在加热下或不在加热下,在静态或流动空气或例如干燥空气、惰性氛围(氮气或例如稀有气体的惰性气体)或真空的其它适宜氛围中蒸发。如果使用加热,温度为用于所用特定溶剂的任意温度并且可为30℃至500℃,但优选地50至150℃。时间可为任意适宜时间,例如几分钟至几天或几小时。加热可为任意有用加热,例如电阻、对流、微波、感应或任意已知的加热方法。在一个实施例中,在溶剂被去除后,使正极进一步进行压制。在许多情况中,此压制在本领域中被称为压延以进一步增加金属箔上正极涂层的密度。一般来讲,压延通过将正极通过具有设定间隙的辊压进行以实现具有均匀厚度的正极。可在变化间隙或相同间隙下,将正极通过辊压多次,这取决于涂覆行为。通常,压力为至多约250MPa并且理想地至多约180、170或160MPa至可为至少约10MPa的某个低压。在优选的实施例中,使用本发明的锂金属氧化物(二次粒径和通过如上所述的方法可达到的任意其它属性),金属箔上的涂层具有约3或3.5g/cc至约4g/cc的密度。由具有本发明LMO中任一个的正极组成的LIB可具有任意适宜设计。除了正极,该电池一般包括负极、置于负极与正极之间的多孔分离器、和与负极和正极接触的电解质溶液。电解质溶液包括溶剂和锂盐。例如,适宜的负极材料包括含碳材料,例如天然或人造石墨、碳化沥青、碳纤维、石墨化中间相微球体、炉黑、乙炔黑、和多种其它石墨化材料。适宜的含碳负极及其制造方法在例如美国专利号7,169,511中有所描述。其它适宜的负极材料包括锂金属、锂合金、其它锂化合物例如钛酸锂和金属氧化物例如TiO2、SnO2和SiO2,以及例如Si、Sn、或Sb的材料。负极可利用一种或多种适宜负极材料制造。分离器通常为非导电材料。其在操作条件下不应与电解质溶液或电解质溶液中任意组分反应或溶于电解质溶液中但是必须允许负极与正极之间的锂离子传输。聚合分离器通常是适宜的。用于形成分离器的适宜聚合物的实例包括聚乙烯、聚丙烯、聚丁烯-1、聚-3-甲基戊烯、乙烯-丙烯共聚物、聚四氟乙烯、聚苯乙烯、聚甲基丙烯酸甲酯、聚二甲基硅氧烷、聚醚砜等。电池电解质溶液具有至少0.1摩尔/升(0.1M),优选地至少0.5摩尔/升(0.5M),更优选地至少0.75摩尔/升(0.75M),优选地高达3摩尔/升(3.0M),以及更优选地高达1.5摩尔/升(1.5M)的锂盐浓度。锂盐可为适用于电池使用的任意锂盐,包括例如LiAsF6、LiPF6、LiPF4(C2O4)、LiPF2(C2O4)2、LiBF4、LiB(C2O4)2、LiBF2(C2O4)、LiClO4、LiBrO4、LiIO4、LiB(C6H5)4、LiCH3SO3、LiN(SO2C2F5)2、和LiCF3SO3的锂盐。电池电解质溶液中的溶剂可为或包括,例如环状碳酸亚烷基酯,比如碳酸亚乙酯;碳酸二烷基酯,比如碳酸二乙酯、碳酸二甲酯或碳酸甲基乙基酯、多种烷基醚;多种环状酯;多种单腈;二腈,比如戊二腈;对称或不对称砜,以及其衍生物;多种环丁砜,具有多达12个碳原子的多种有机酯和醚酯等。分析技术LMO的振实密度通过将约20克LMO放入带刻度的量筒中并利用购自LoganInstrumentsCorporation,Somerset,NJ的TAP-2s振实密度检测器轻敲2000次来确定。利用Coulter粒径分析仪(CoulterLS230,BeckmanCoulterInc.,Brea,CA)测量粒径和尺寸分布(以体积计的当量球形直径),确定一次颗粒的粒径和尺寸分布。为进行试验,将研磨后的2滴颗粒前驱体的水性浆液加入10ml去离子水中并超声处理30秒。然后,利用粒径分析仪分析粒径。通过XPS利用在14kV和10mA下操作的具有单色AlKαX-射线源的“KratosAXIS165,S/N315-91898/2”确定Mn/Ni比率。为确定Mn/Ni比率,对至少两个样品进行测试。将测试的每个样品放在具有直径7mm以及深3mm的样品空腔的铝样品容器中。分析面积是550(x)x180(y)微米。通过对Mn和Ni2p峰进行积分确定Mn/Ni比率。即使NiLMMAuger线与Co2p3/2和Mn2p3/2峰之间存在潜在的干扰,因为远小于测量值的标准偏差而并不相关。通过电感耦合等离子体原子发射光谱法(ICP-AES)确定LMO的整体化学。先通过将0.10g部分称入50mL聚丙烯试验试管中使LMO溶解。添加4mL50%(v/v)盐酸和100μL浓氢氟酸并在加热模块上在约85℃下加热30分钟。然后添加2.0mL浓硝酸并另加热5分钟。然后,将试管从加热模块移走并利用去离子水稀释。利用ICP-AES在PerkinElmer7300DV电感耦合等离子体光学发射光谱仪上利用5μg/mLEu内标分析制备的溶液。使20Ah堆叠电池单元进行针穿透试验以评价其安全性。在电池单元进行初期形成循环后,在1C速率(20A)下,将测试的包含所关注的特定LMO的电池单元充电到截止电压(例如,4.2V、4.15V、4.1V、4.05V、4V等),然后,将电压保持恒定,直到电流在室温下降到0.05C以下。然后,利用针在80mm/sec的穿透速度下穿透20Ah电池单元并记录任意电池单元燃烧。充电的正极的氧逸出通过在硬币半电池单元中相对于锂金属将正极充电到4.3V,然后在充有氩气的手套箱中拆卸电池单元来测量。利用碳酸二甲酯溶剂冲洗电极以去除电解质并在真空下在25℃下干燥12小时。使干燥的电极在氩气中在10℃/分钟下在质谱中加热,利用氧量标准化为市售LMO来进行逸出气体分析(氧气)(见表2,对比实例5“100%”)。如针穿透结果所示,氧逸出被认为是由LMO制造的电池的安全性的良好指标。比表面积根据布鲁诺-埃梅特-特勒理论通过氮吸附确定。二次颗粒的孔隙率通过离子(Ga)截断二次颗粒并在扫描电子显微镜中成像截面来确定。利用图像分析软件(ImageJ)确定孔面积和LMO的面积以确定孔隙率。在基本上以如下相同方式制造的硬币电池单元和20Ah电池单元上确定电化学性能。如果另一种锂金属正极材料也用于制造正极,不管是否与LMO混合,也可被制成电池单元以按照如下相同方式确定电化学性能。将每个实例和对比实例的LMO或锂金属正极材料与SUPERPTM碳黑(TimcalAmericasInc.Westlake,OH)、和聚偏二氟乙烯(PVdF)(Arkemainc.,KingofPrussia,PA)粘合剂以94:2.5::3.5的LRMO:SuperP::PVdF的重量比混合。通过将正极材料、导电材料、和粘合剂悬浮在溶剂N-甲基-2-吡咯烷酮(NMP)中,然后在真空快速混合器(ThinkyUSA,LagunaHills,CA)中均质化来制备浆液。在中等真空下消泡前,NMP与固体比率为约1.6:1。利用刮刀将浆液涂覆到电池级铝箔上至约50微米的厚度并在130℃下在干燥对流烘箱中干燥30分钟。铝箔厚15微米。在干燥环境(露点低于或等于-40℃)中制造电池单元。使电极在辊压机上压制到约30微米,得到所示的活性材料密度。电池单元具有约10mg/cm2的测量负载量。电解质为具有1.0MLiPF6的碳酸亚乙酯/碳酸二乙酯(EC:EMC,1:3体积比)。硬币电池单元的负极为购自ChemetallFooteCorporation,NewProvidence,NJ的200微米厚的高纯度锂箔。分离器为市售的涂覆分离器。20Ah电池单元的负极是市售石墨,(从贝瑞特电子有限公司(BTRNewEnergyMaterialsInc.),深圳,中国获得的AGP-2粉末)。对于20Ah电池而言,负极/正极容量比是1.1至1.2。使电池在MACCORSeries4000电池试验台(MACCOR,Tulsa,OK)上循环。通过在C/10下充电到4.3V(利用LiNi0.5Mn0.3Co0.2O2的实例)或4.5V(LiNi0.6Mn0.2Co0.2O2),然后保持恒压,直到电流降到C/20来活化电池单元。在0.1的C速率下确定电池的初始容量然后以随后顺序在0.1、0.5、1、2、5、10的C速率下,也确定倍率容量。实例表1中显示了用以制造LMO的原材料。所用水为去离子水。实例1-8和比对实例1-5:将实例1-8和对比实例1-5的LMO制成LiNi0.5Mn0.3Co0.2O2的整体化学。这些实例都以制造该NMC所必要的相同比例使用相同原材料,除了以1.1的量使用过量Li。所用的颗粒前驱体是Li2CO3、Ni(OH)2、Mn2O3和Co3O4。特定Ni(OH)2和Co3O4如表1所示并可互换使用。将所有的颗粒前驱体以约50重量%的固体负载同时在水中混合。除了水,2重量%的聚丙烯酸也用以混合所有前驱体。在装载了0.2至0.3mm直径的钇稳定的氧化锆介质(SigmundLindner,Germany.型号ZY优质)的Micromedia珠磨机(MM-P1,BuhlerInc.Mahwah,NJ)中研磨混合物。使磨机在4KW/小时的功率下运行并研磨足以实现表2中所示的一次粒径的时间。浆液具有在22℃下利用采用了#3RV锭子的Brookfield粘度计(型号DV-II+)(Brookfield,Massachusetts,USA)测量的约1600至2000厘泊的粘度。通过喷雾干燥在MOBILEMINORTM2000型号H喷雾干燥器(GEANiro,Denmark)中以约2.4至2.8Kg/小时的喷雾器的馈送速率在20%2SCFM的氮流量和1巴压力下聚集浆液。进口温度为约140℃,并且出口温度为约60至65℃。喷雾干燥的聚集的前驱体具有13.4微米的D50二次粒径。使喷雾干燥的聚集的前驱体(50g)在静态空气氛围中在0.19立方英尺BlueM炉中加热。使喷雾干燥的聚集的前驱体浸泡约5小时然后保持表2所示的温度和时间。但是,将实例6在10立方英尺U2炉中煅烧,采用相同方案,除了以10小时缓至到保持温度。在保持最终温度后,在约10小时内将形成的LMO冷却到室温。对比实例5是由DaejungEnergyMaterialsCo.Ltd.,Jeonbuk,Korea以商品名L4L-3D12市售的LMO,其基本上具有与实例1-8和对比实例1-4相同的化学。对比实例5通过沉淀方法形成以形成含Ni、Co、和Mn的前驱体化合物,然后将其与锂前驱体混合并加热以形成LMO。从表2可知,当如在对比实例2-4中存在过多大前驱体颗粒(D90过大)时,可看出制造有用LMO的能力会变得困难。也就是,当尝试制造在商业上实际被加工成高振实密度给出的致密正极的LMO时,电化学(EC)性能受影响。相反,实例7和8显示了当D90明显低于对比实例2-4时,即使D100接近相同,制造实用并改进的LMO的能力通过更高的振实密度和EC性能显示。同样,当D100接近1微米并且D90仍大于0.5微米时,形成易加工的具有极佳EC性能的LMO。同样,当比较实例1和8时,明显的是,前驱体的粒径对实现一次颗粒的高Mn/Ni表面组成的能力有影响,这被视为与以下进一步描述的改善的安全性相关联。当比较实例1-3时,也可看到时间对Mn/Ni比率的影响。当比较对比实例1和实例4时,也可看到温度的影响。将对比实例1加热到高温,二次颗粒烧结在一起达到二次颗粒不可分开而不明显使二次颗粒本身破裂的程度。实例5和6为进一步代表性实例,其显示了当含Ni和Co的前驱体具有特定尺寸时制造本发明的LMO的一致性。实施例9、9A、9B和10-13以及对比实例5A和5B实例9的LMO以与实例1相同的方式制造,除了根据下文加热以形成LMO。使LMO在6小时内在静态空气氛围中加热到600℃并在600℃下保持4小时,在3小时内加热到920℃,然后在2小时内加热到950℃并在950℃下保持5小时,然后在10小时内冷却到室温。使该LMO在20Ah电池单元中加工(“实例9A”)并通过上述针穿刺试验进行测试。表3中显示了前驱体粒径、振实密度、逸出的氧、和EC性能。同样,将相同LMO与磷酸锂锰铁(LMFP)以7/3的LMO/LMFP重量比混合并且20Ah电池单元以刚才所述的相同方式制造(“实例9B”)。根据下文制造LMFP。将草酸亚铁二水合物和碳酸锰与水以足以产生足以倾倒和泵送的混合物流体的量混合。使用的掺杂剂金属前驱体是乙酸镁和乙酸钴。缓慢地将85重量%磷酸水溶液加入混合物中。在酸添加结束后,添加氢氧化锂并再搅拌所述混合物约多于30分钟。利用氧化锆介质研磨所述混合物直到颗粒降到直径约50nm。在研磨期间,添加乙酸纤维素或其它碳源(即,葡萄糖、乳糖等)以实现表4中所示的碳含量。在170℃下喷雾干燥研磨的混合物以将小颗粒聚集成具有高达约20微米的直径的基本球形二次颗粒。在含<100ppm氧气的氛围下加热喷雾干燥的颗粒。在三小时内将颗粒从室温加热到400℃并在400℃下保持一小时。然后在两小时内将温度升到650℃并在650℃下保持3小时。将加热的颗粒冷却到60℃以下并通过44微米筛网筛分。表4中显示了LMFP特征。以与以上相同的方式,但是使用对比实例5的LMO,将对比实例5A的LMO制成20Ah电池单元。对比实例5B与对比实例5A相同,除了利用对比实例5的LMO和刚描述的LMFP以7/3的LMO/LMFP比率的混合物制造20Ah电池单元。对比实例5A当进行针穿刺试验时在4.05伏特的截止电压下着火。对比实例5B在4.2的截止电压下着火。实例9A和9B没有着火(即,通过试验)。与对比实例5的LMO相比,本发明的LMO的改善的安全性能被认为至少部分地因为采用一次颗粒的Mn/Ni比率,这也被认为与氧逸出有关。以与实例1相同的方式制造实例10-13,除了如表3所示使用不同的前驱体颗粒并且加热以形成LMO是加热到950℃,持续3小时。从表3可明显得到,只要含Ni和Co的前驱体颗粒具有颗粒尺寸,颗粒前驱体就可变化。实例14-17在这些实例中,以与实例1相同的方式制造LMO,除了含Mn的前驱体(即,Mn2O3)与其它前驱体颗粒分开研磨,然后混合以形成具有约45%的固体负载的含所有前驱体颗粒的浆液。Mn前驱体浆液具有45%的固体负载并研磨一段时间以实现表5中所示的颗粒尺寸。也利用8小时的斜坡速率波动到最终温度,将这些实例加热到950℃,保持3小时。研磨和其它步骤基本上与实例1相同。从表5可知,明显的是,Mn前驱体的尺寸可大于含Ni和Co的前驱体但仍产生具有良好EC性能和易加工性但也允许如Mn/Ni表面比率和逸出的氧所示的良好安全性的LMO。此令人惊讶的结果允许具有改进的安全性以及具有极佳循环寿命和良好EC性能的LMO的更稳健的商业制造。实例18-21实例18-21的LMO以与实例1相同的方式并按照下文制造。LMO的整体化学是LiNi0.6Mn0.2Co0.2O2。这些实例中每一个以制造此LMO所必要的相同比例使用相同原材料,除了不使用过量Li(即,Li等于约1)。使用的颗粒前驱体是Li2CO3、Ni(OH)2、Mn2O3和Co3O4。形成LMO的加热方案是在6小时内加热到600℃,在600℃下保持4小时,在5小时加热到930℃,并在930℃下保持5小时然后在约10小时内冷却到室温。表6中显示了LMO的前驱体颗粒尺寸和特征。表6也显示了对比实例6的数据,其为从EcoproCo.Ltd,Cheongwon-gun,Chingcheongbuk-do,Korea以商品名NCM080-10A(NMC622)购买的具有与实例18-21基本上相同化学的LMO。对比实例6通过沉淀方法形成以形成含Ni、Co、和Mn的前驱体化合物,然后其与锂前驱体混合并加热以形成LMO。表6显示了具有更高镍含量的LMO又可通过显著量的超出0.5微米的颗粒形成。即使LMO可利用甚至更小的颗粒(即,基本上都小于0.5微米)形成,但并不理想,因为从数据可知,明显的是,晶粒生长变得更难控制,当在商业规模上制造时,这是不利的(参见更小的BET表面积,即使从更小的更窄分布的颗粒开始)。即使未显示,当实例18-21的LMO在金属箔上形成正极层时被压制时,这些实例的LMO的密度大于对比实例6的LMO的密度的约10至15%。此允许在相同电池体积中明显更高的容量。也发现,通过本发明方法制造的LMO可得到仍具有极佳EC性能的具有高密度的二次颗粒的LMO。这被认为可能部分地因为Ni和Co前驱体的一次粒径分布和实现具有所有前驱体化合物的浆液的高固体负载的能力。图1(实例1的截图)显示了本发明的LMO的二次颗粒相对于沉淀形成的典型LMO(见图2;对比实例6的LMO的截图)的孔隙率的显著差异。实例22-27实例22-27的LMO以与实例18-21相同的方式制造,但是变化了喷雾干燥器条件以实现所示的不同的二次粒径分布。从数据可知,当喷雾干燥以聚集粉末时,优选地是,D10不小于5微米,因为发现当加热时二次颗粒破裂形成LMO。即使可使用的电池可由该LMO制造,与由其中二次颗粒明显完整的LMO制造的电池的循环寿命相比,循环寿命通常明显受影响。表1表2表3表4特征LMFP化学Li1.05Mn0.75Fe0.15Mg0.05Co0.003PO4表面积(m2/g)24D10(μm)3.8D50(μm)8.2D90(μm)13振实密度(g/cc)1.1至0.9球形二次颗粒1.195真实密度(g/cc)3.45碳(重量%)3当前第1页1 2 3